- お役立ち記事
- Evolution and Applications of Micromolding Technology
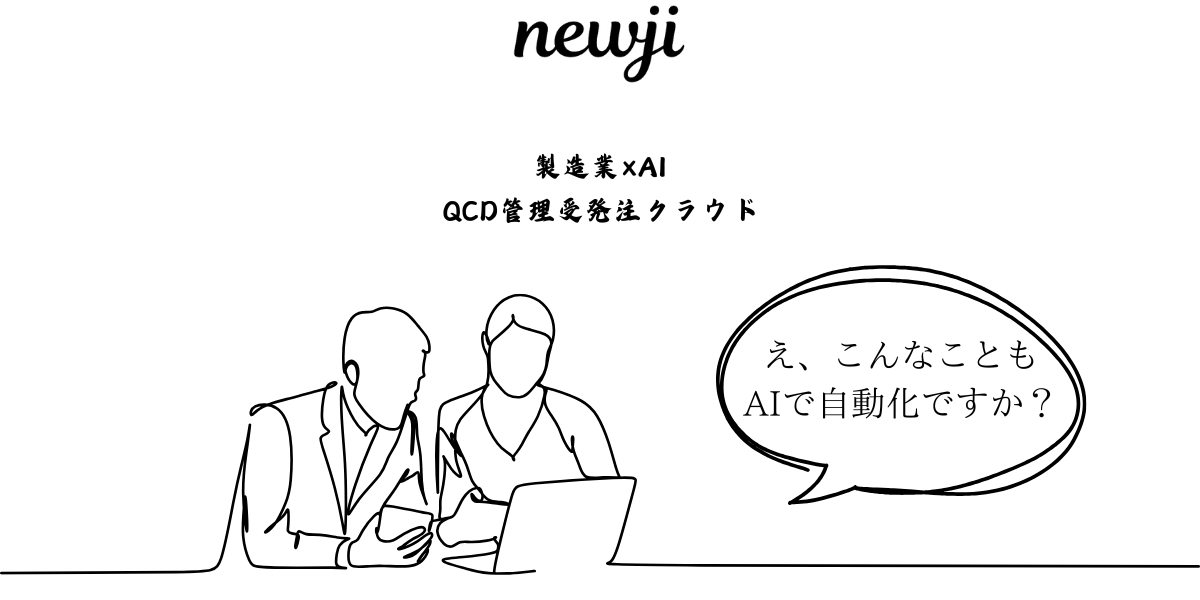
Evolution and Applications of Micromolding Technology
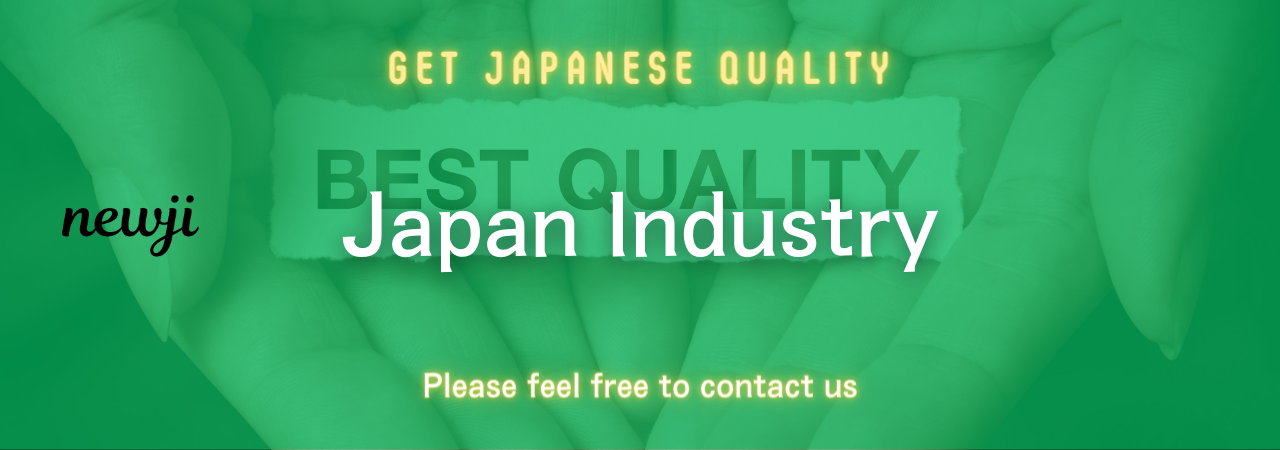
Micromolding technology has transformed how industries approach manufacturing, allowing for the production of very small, detailed parts with high precision. This technology involves the creation of tiny components by injecting molten material into a mold. These components are often used in various industries, including medical devices, electronics, and automotive sectors.
目次
Understanding Micromolding
Micromolding can be defined as the process of making small plastic parts with intricate features. This process is ideal for producing components that require extreme precision and fine details. Because of the small scale and high detail, the molds used in micromolding are crafted with meticulous care and accuracy.
The Evolution of Micromolding
The origins of micromolding can be traced back to traditional injection molding methods. As industries advanced, the need for smaller and more precise parts grew, leading to the development of micromolding techniques. This evolution was marked by the integration of advanced materials, high-precision machinery, and sophisticated software.
Initially, traditional metal molds used in larger-scale manufacturing were adapted for creating smaller parts. However, engineers and scientists soon realized that to achieve the necessary precision, specialized micromolding equipment was required. This led to the development of micro-milling and Electrical Discharge Machining (EDM) technologies, paving the way for more accurate mold fabrication.
Materials Used in Micromolding
One of the critical aspects of micromolding is the selection of appropriate materials. Because the parts produced are minuscule, the material used must offer excellent mechanical properties, durability, and stability.
Common materials used in micromolding include thermoplastics like Polyethylene (PE), Polypropylene (PP), and Polycarbonate (PC). Advanced engineering materials, such as Liquid Crystal Polymers (LCPs) and PEEK (Polyether Ether Ketone), are also frequently used. These materials provide the necessary strength and thermal stability required for specialized applications.
The Micromolding Process
The micromolding process involves several stages, each vital for producing high-quality components. Here’s a detailed look at these stages:
Mold Design and Fabrication
Creating an accurate mold is the first and most significant step in micromolding. The mold design must consider the material properties, component geometry, and production volume. Sophisticated CAD software is employed to design the mold, ensuring every detail is accounted for.
After the design phase, the mold is fabricated using high-precision techniques like micro-milling and EDM. These processes allow for the creation of complex geometries and intricate details.
Material Preparation
The selected material is carefully prepared to prevent contamination and ensure uniformity. For polymers, this often involves drying to remove any moisture content, which can affect the final product’s quality. The material is then melted and injected into the mold.
Injection and Cooling
Once the material is prepared, it is injected into the mold cavity under high pressure. This ensures that the material fills every intricate feature of the mold. The mold is then cooled to solidify the material. This cooling process must be carefully controlled to avoid defects such as warping or shrinkage.
Part Ejection and Finishing
After cooling, the part is ejected from the mold. Due to the tiny size of the parts, specialized techniques are often required for ejection to prevent damage. Post-processing steps, such as deburring and surface finishing, are carried out to ensure the part meets the quality standards.
Applications of Micromolding Technology
Micromolding technology has found extensive applications in various fields due to its ability to produce highly detailed, small-scale components.
Medical Devices
In the medical industry, micromolding is used to manufacture components for devices such as catheters, surgical tools, and diagnostic equipment. The precision and biocompatibility of micromolded parts are vital for ensuring patient safety and the accuracy of medical procedures.
Electronics
The electronics industry relies on micromolding for producing components like connectors, switches, and sensors. With the trend towards miniaturization, the demand for microscale parts continues to grow. Micromolding offers the precision required to create these tiny, complex components.
Automotive Industry
In the automotive sector, micromolding is used to create parts for systems such as fuel injectors, sensors, and connectors. The ability to produce lightweight and high-strength components is crucial for enhancing vehicle performance and efficiency.
Consumer Goods
Micromolding is also prevalent in the consumer goods industry, particularly in the production of components for wearables, hearing aids, and mobile devices. The precision and quality of micromolded parts help to ensure the functionality and reliability of these products.
The Future of Micromolding Technology
As technology continues to advance, the capabilities and applications of micromolding are expected to expand. Innovations in materials, mold fabrication techniques, and process control will likely lead to even greater precision and quality in micromolded parts.
Advanced Materials
The development of new materials with enhanced properties will enable the creation of components that can withstand more extreme conditions. This will open up new possibilities for micromolding in industries such as aerospace and defense.
Automation and Quality Control
The integration of automation and advanced quality control systems will improve the efficiency and consistency of the micromolding process. Real-time monitoring and feedback systems will allow for immediate adjustments, reducing defects and improving overall product quality.
Micro-injection 3D Printing
The combination of micromolding with 3D printing technology is another exciting development on the horizon. This hybrid approach could facilitate the production of highly complex parts with even finer details and customization options.
In conclusion, micromolding technology has significantly advanced from its origins, providing a critical manufacturing solution for a wide range of industries. With ongoing technological developments, its future looks promising, offering new possibilities and applications across various fields.
資料ダウンロード
QCD調達購買管理クラウド「newji」は、調達購買部門で必要なQCD管理全てを備えた、現場特化型兼クラウド型の今世紀最高の購買管理システムとなります。
ユーザー登録
調達購買業務の効率化だけでなく、システムを導入することで、コスト削減や製品・資材のステータス可視化のほか、属人化していた購買情報の共有化による内部不正防止や統制にも役立ちます。
NEWJI DX
製造業に特化したデジタルトランスフォーメーション(DX)の実現を目指す請負開発型のコンサルティングサービスです。AI、iPaaS、および先端の技術を駆使して、製造プロセスの効率化、業務効率化、チームワーク強化、コスト削減、品質向上を実現します。このサービスは、製造業の課題を深く理解し、それに対する最適なデジタルソリューションを提供することで、企業が持続的な成長とイノベーションを達成できるようサポートします。
オンライン講座
製造業、主に購買・調達部門にお勤めの方々に向けた情報を配信しております。
新任の方やベテランの方、管理職を対象とした幅広いコンテンツをご用意しております。
お問い合わせ
コストダウンが利益に直結する術だと理解していても、なかなか前に進めることができない状況。そんな時は、newjiのコストダウン自動化機能で大きく利益貢献しよう!
(Β版非公開)