- お役立ち記事
- Example of cost reduction through standardization of parts promoted by purchasing department
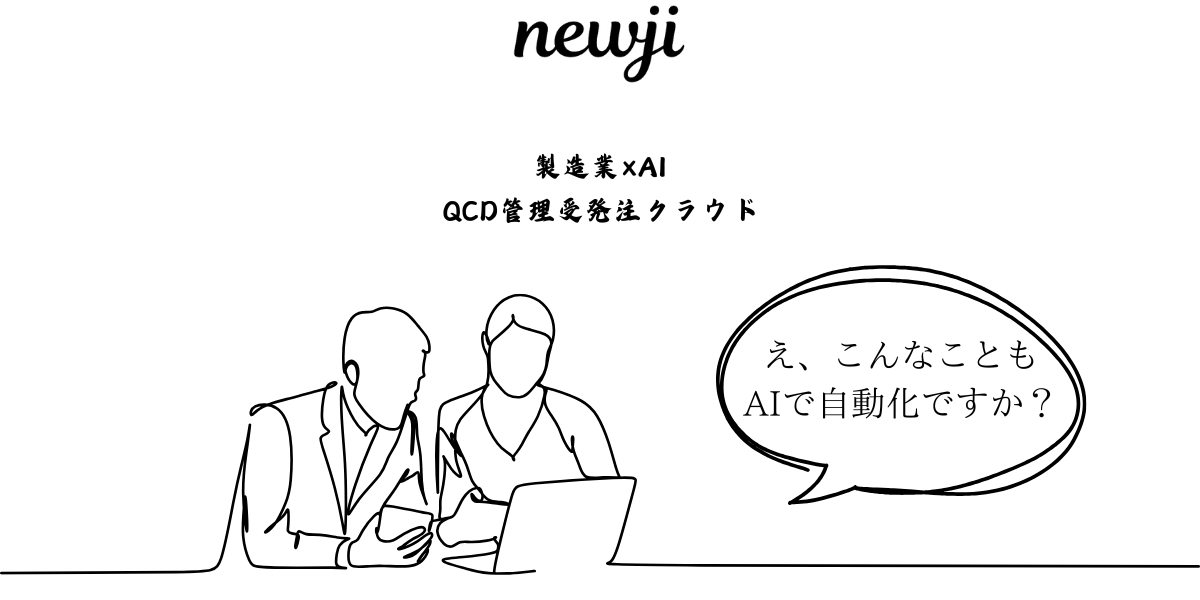
Example of cost reduction through standardization of parts promoted by purchasing department
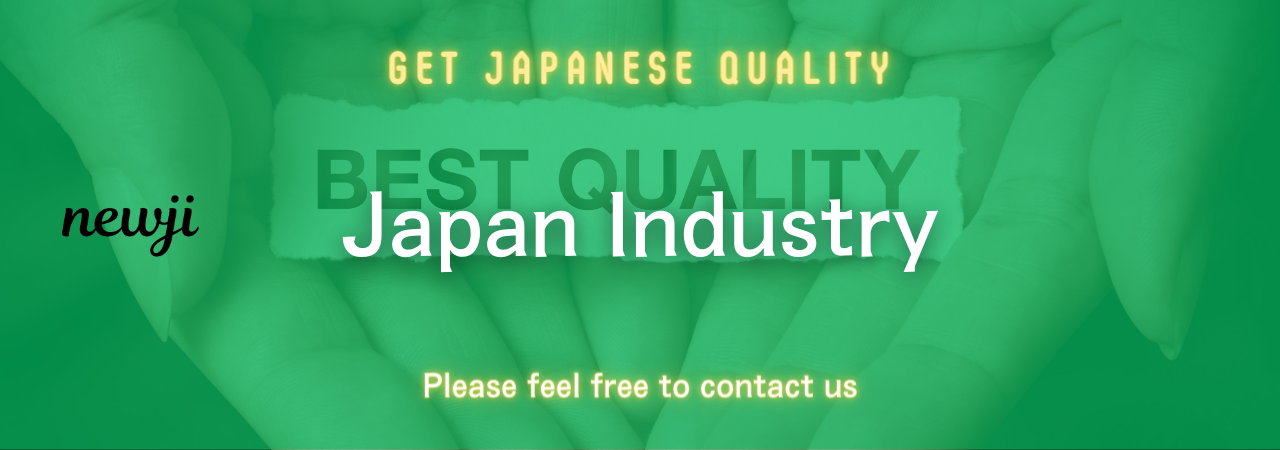
目次
Understanding Part Standardization
Standardization of parts is an essential process in the modern business environment.
It involves creating uniform specifications for certain components used across products or within different operations of a company.
This approach simplifies production, reduces costs, and enhances efficiency.
The purchasing department plays a crucial role in this process, ensuring that parts selected for standardization meet the required quality and performance standards.
Why Standardize Parts?
There are several reasons why companies choose to standardize parts.
Firstly, it reduces costs significantly.
When multiple products within a company use the same parts, it allows for bulk purchasing.
Bulk purchasing often leads to discounts and better negotiation power with suppliers.
Moreover, standardized parts can streamline inventory management by simplifying the process and reducing the number of spare parts that need to be stocked.
Secondly, standardization can improve manufacturing efficiency.
With fewer variations in parts, assembly lines can move faster, and the chances of errors or delays are minimized.
This uniformity also facilitates smoother transitions between product variations or updates.
Lastly, the process aids in maintaining consistent quality.
When consistent parts are used, the final product’s quality becomes more predictable and easier to control.
This consistency is crucial in building brand reputation and customer trust.
The Role of the Purchasing Department
The purchasing department is integral in promoting and implementing parts standardization.
As the bridge between suppliers and the company, the purchasing team must identify opportunities for standardization and work closely with engineers and designers.
They need to ensure that the standardized parts are compatible with various products and application areas.
One of their responsibilities is to choose suppliers who can meet the demand for standardized parts.
This involves evaluating suppliers based on their ability to provide parts that meet quality, cost, and delivery standards.
In addition, the purchasing department is tasked with negotiating contracts that reflect the benefits of standardization, such as lower prices due to volume purchases.
The purchasing department also conducts market analysis to identify trends in components that can be standardized.
This analysis helps in anticipating future needs and fosters strategic planning.
Cost Reduction Through Standardization
Direct Savings
Direct savings from parts standardization are often the most apparent.
By streamlining the parts used across various products, companies can significantly cut their production costs.
This is primarily achieved through bulk purchasing, which lowers the per-unit cost of parts.
The purchasing department can work with suppliers to get discounted rates for buying in large quantities.
The savings gained from these negotiations can be substantial, directly impacting the company’s bottom line.
Operational Benefits
In addition to direct savings, standardization leads to operational benefits that indirectly reduce costs.
For example, with fewer part variations to manage, the logistics of ordering, storing, and using these components become simpler and more efficient.
Inventory costs are minimized as companies need fewer parts in stock.
Thus, the risk of overstocking or understocking particular components is reduced.
Moreover, maintenance and repair operations benefit from standardized parts.
Technicians require less training to service standardized components.
This reduction in training time equates to lower training costs and faster repair times, enhancing productivity and operational uptime.
Quality and Warranty Cost Reductions
Product quality is a vital concern for any company aiming to satisfy and retain customers.
Using standardized parts can lead to better quality control because it reduces variability in the manufacturing process.
Consistent quality leads to fewer defects, which subsequently reduces the costs associated with warranties and returns.
Fewer defects mean less frequent warranty claims and fewer resources spent on repair or replacement of faulty products.
It also helps build a robust reputation for reliability that can translate into increased sales and customer loyalty.
Implementing Standardization
Steps Toward Successful Standardization
Successfully implementing parts standardization requires a clear and strategic approach.
The process often starts with a thorough audit of current parts usage to identify candidates for standardization.
This audit helps determine which components are used across multiple products and have potential for standardization without compromising the product’s functionalities.
Next, a cross-functional team should be assembled, bringing together members from the purchasing, engineering, design, and manufacturing departments.
This team can provide insights into the technical, economic, and operational implications of standardizing particular parts.
Developing clear guidelines and criteria for standardized parts is crucial.
The team should establish what qualities, specifications, and performance levels these parts must meet.
Additionally, setting up monitoring systems to track the performance and cost savings associated with standardized parts will help refine the process over time.
Challenges of Standardization
While the benefits are clear, companies may face challenges during the standardization process.
Resistance to change can be a significant hurdle, whether it comes from internal stakeholders used to working with a variety of parts or suppliers that may be reluctant to adjust to new demands.
Furthermore, the initial transition can involve upfront costs, such as reconfiguring assembly lines or retraining staff.
However, these costs should be viewed as investments that will yield long-term savings and operational benefits.
The Future of Parts Standardization
As technology advances and the global marketplace becomes more competitive, the push for standardization will intensify.
Adopting new technologies like digital twins and Industry 4.0 solutions can further enhance the effectiveness of standardization efforts, making it easier to simulate and predict the impact of standardization on production and costs.
Companies that embrace standardization will likely have a competitive edge, being able to respond faster to market changes, maintain high quality, and reduce costs.
In this evolving landscape, the purchasing department’s role will continue to expand, driving innovation and efficiency across the supply chain through strategic parts standardization.
In conclusion, the example of cost reduction through standardization of parts underscores the vital role the purchasing department plays.
By aligning the efforts of various stakeholders and leveraging the power of volume purchases, companies can maximize the benefits of this approach.
These efforts not only lead to substantial cost savings but also position companies better for future growth and success.
資料ダウンロード
QCD調達購買管理クラウド「newji」は、調達購買部門で必要なQCD管理全てを備えた、現場特化型兼クラウド型の今世紀最高の購買管理システムとなります。
ユーザー登録
調達購買業務の効率化だけでなく、システムを導入することで、コスト削減や製品・資材のステータス可視化のほか、属人化していた購買情報の共有化による内部不正防止や統制にも役立ちます。
NEWJI DX
製造業に特化したデジタルトランスフォーメーション(DX)の実現を目指す請負開発型のコンサルティングサービスです。AI、iPaaS、および先端の技術を駆使して、製造プロセスの効率化、業務効率化、チームワーク強化、コスト削減、品質向上を実現します。このサービスは、製造業の課題を深く理解し、それに対する最適なデジタルソリューションを提供することで、企業が持続的な成長とイノベーションを達成できるようサポートします。
オンライン講座
製造業、主に購買・調達部門にお勤めの方々に向けた情報を配信しております。
新任の方やベテランの方、管理職を対象とした幅広いコンテンツをご用意しております。
お問い合わせ
コストダウンが利益に直結する術だと理解していても、なかなか前に進めることができない状況。そんな時は、newjiのコストダウン自動化機能で大きく利益貢献しよう!
(Β版非公開)