- お役立ち記事
- Example of implementing a contingency plan in the purchasing department to improve reliability of material supply
月間76,176名の
製造業ご担当者様が閲覧しています*
*2025年3月31日現在のGoogle Analyticsのデータより
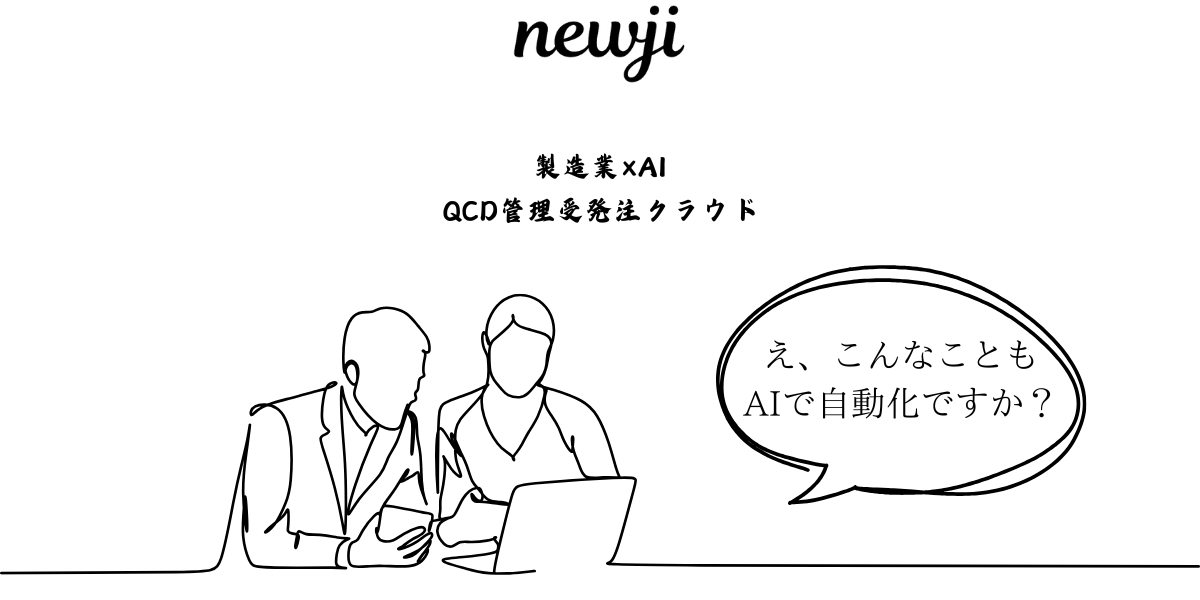
Example of implementing a contingency plan in the purchasing department to improve reliability of material supply
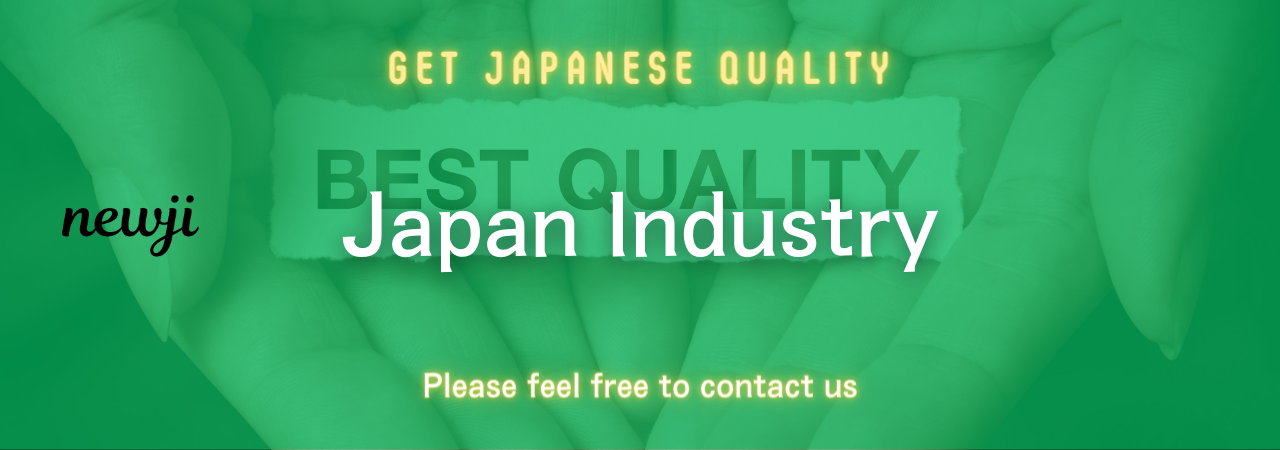
目次
Understanding Contingency Planning
Contingency planning is an essential aspect of any successful business operation, allowing organizations to prepare for unexpected disruptions.
In the purchasing department, this process involves devising strategies to ensure a reliable supply of materials, even when unforeseen challenges arise.
With a well-implemented contingency plan, businesses can maintain their operations without significant interruptions, thus preserving both productivity and profitability.
The Importance of Contingency Plans in Purchasing
In the purchasing department, the reliability of material supply is paramount.
A disruption in the materials pipeline can lead to production delays, increased costs, and ultimately, a loss in customer trust.
To mitigate these risks, companies must develop contingency plans that address potential supply chain disruptions.
These plans ensure continuous supply by identifying alternative sources, establishing stockpiles, and creating efficient communication protocols.
Steps to Implement a Contingency Plan
Implementing a contingency plan in the purchasing department involves several key steps.
By following these steps, businesses can ensure that their supply chain remains resilient, even in times of crisis.
1. Identify Potential Risks
The first step in creating a contingency plan is to identify the potential risks that could disrupt material supply.
This may include natural disasters, supplier bankruptcies, transportation issues, or geopolitical tensions.
By understanding these threats, purchasing departments can prioritize resources and create specific strategies to address them.
2. Assess Supplier Relationships
Next, assessing the reliability and flexibility of current suppliers is crucial.
Building strong, long-term relationships with suppliers can increase a company’s ability to adapt during disruptions.
Purchasing departments should evaluate suppliers’ financial stability, geographic location, and their own contingency plans.
This assessment can help in identifying which suppliers can be relied upon during a crisis.
3. Develop Alternative Supplier Strategies
To ensure material supply remains uninterrupted, it’s important to establish relationships with multiple suppliers.
Having a diversified supplier base reduces dependency on a single source and increases the ability to switch suppliers quickly if necessary.
Purchasing departments should identify secondary suppliers and negotiate agreements that can be activated in an emergency.
4. Establish Inventory Buffers
Maintaining an adequate inventory buffer is another critical aspect of a contingency plan.
By holding additional stock of critical materials, organizations can continue operations during short-term supply disruptions.
While this may increase costs, the insurance it provides against halted production can be invaluable.
5. Implement Technology Solutions
Modern technology offers numerous tools that can enhance supply chain resilience.
Systems like Enterprise Resource Planning (ERP) or supply chain management software can track inventory levels, monitor supplier performance, and provide data analysis for decision-making.
By using these tools, purchasing departments can quickly identify potential issues and adapt their strategies in real-time.
6. Draft and Communicate the Plan
Once the risks, suppliers, and inventory strategies are identified, it’s time to draft the contingency plan.
It should outline specific actions to be taken in various scenarios, including roles and responsibilities of team members.
Clear communication of the plan within the department and with other stakeholders ensures that everyone knows what to do when a disruption occurs.
7. Test and Update Regularly
A contingency plan is only as good as its execution in a real-world scenario.
Regular testing through simulations and drills can help identify weaknesses and areas for improvement.
Moreover, reviewing and updating the plan periodically ensures that it remains relevant and effective as business environments and risks change.
Benefits of a Robust Contingency Plan
Implementing a comprehensive contingency plan in the purchasing department offers several significant benefits, all of which improve the reliability of material supply.
Minimized Disruptions
With a contingency plan in place, companies can swiftly address disruptions, minimizing their impact on operations.
This preparedness ensures that production schedules are maintained, thereby avoiding delays and penalties.
Cost Management
While disruptions can lead to unexpected costs, a contingency plan helps manage these expenses by reducing the likelihood of panic buying and supply shortages.
By having pre-negotiated terms with alternative suppliers, companies can maintain competitive pricing even during a crisis.
Enhanced Supplier Relationships
Strong partnerships with suppliers lead to improved collaboration and trust.
During disruptions, these relationships prove invaluable as suppliers may prioritize clients with whom they have established long-term connections.
Increased Customer Trust
Consumers expect reliability from the companies they choose to do business with.
By maintaining a consistent supply of products, companies reinforce their commitment to quality and reliability, thus enhancing customer trust and loyalty.
Conclusion
In an ever-changing global market, the purchasing department plays a critical role in maintaining a steady flow of materials.
Implementing a robust contingency plan ensures that this function continues to operate smoothly, even amid unforeseen challenges.
By identifying risks, diversifying suppliers, leveraging technology, and regularly testing plans, businesses can make their material supply chain resilient.
This not only safeguards production but also positions companies to thrive in a competitive landscape.
資料ダウンロード
QCD管理受発注クラウド「newji」は、受発注部門で必要なQCD管理全てを備えた、現場特化型兼クラウド型の今世紀最高の受発注管理システムとなります。
ユーザー登録
受発注業務の効率化だけでなく、システムを導入することで、コスト削減や製品・資材のステータス可視化のほか、属人化していた受発注情報の共有化による内部不正防止や統制にも役立ちます。
NEWJI DX
製造業に特化したデジタルトランスフォーメーション(DX)の実現を目指す請負開発型のコンサルティングサービスです。AI、iPaaS、および先端の技術を駆使して、製造プロセスの効率化、業務効率化、チームワーク強化、コスト削減、品質向上を実現します。このサービスは、製造業の課題を深く理解し、それに対する最適なデジタルソリューションを提供することで、企業が持続的な成長とイノベーションを達成できるようサポートします。
製造業ニュース解説
製造業、主に購買・調達部門にお勤めの方々に向けた情報を配信しております。
新任の方やベテランの方、管理職を対象とした幅広いコンテンツをご用意しております。
お問い合わせ
コストダウンが利益に直結する術だと理解していても、なかなか前に進めることができない状況。そんな時は、newjiのコストダウン自動化機能で大きく利益貢献しよう!
(β版非公開)