- お役立ち記事
- Example of optimization of semiconductor manufacturing process using experimental design
月間76,176名の
製造業ご担当者様が閲覧しています*
*2025年3月31日現在のGoogle Analyticsのデータより
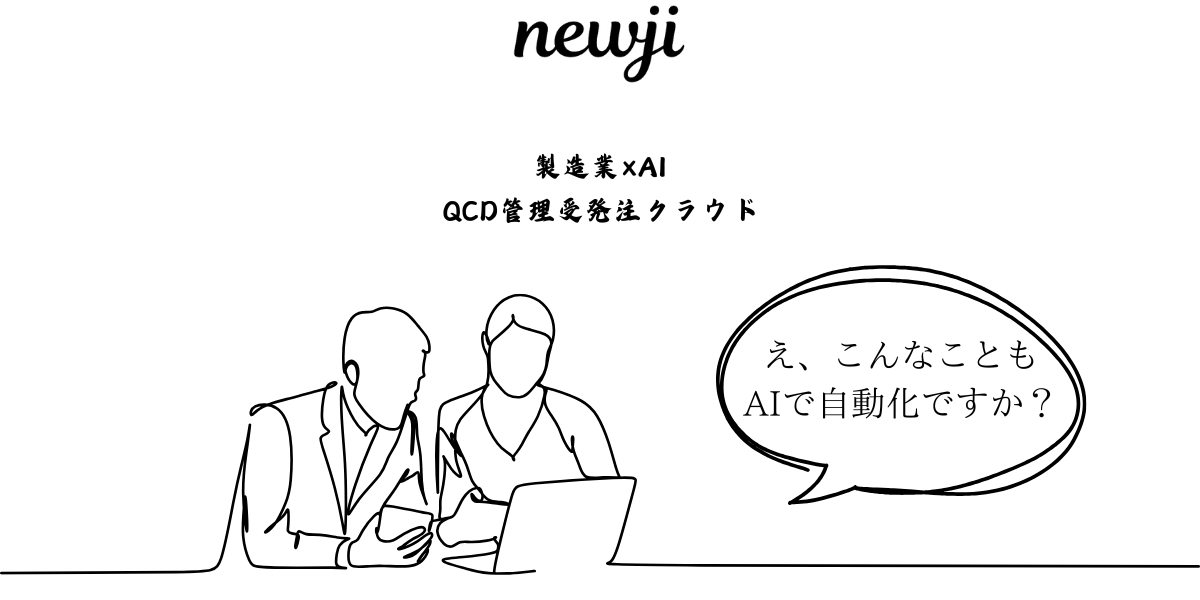
Example of optimization of semiconductor manufacturing process using experimental design
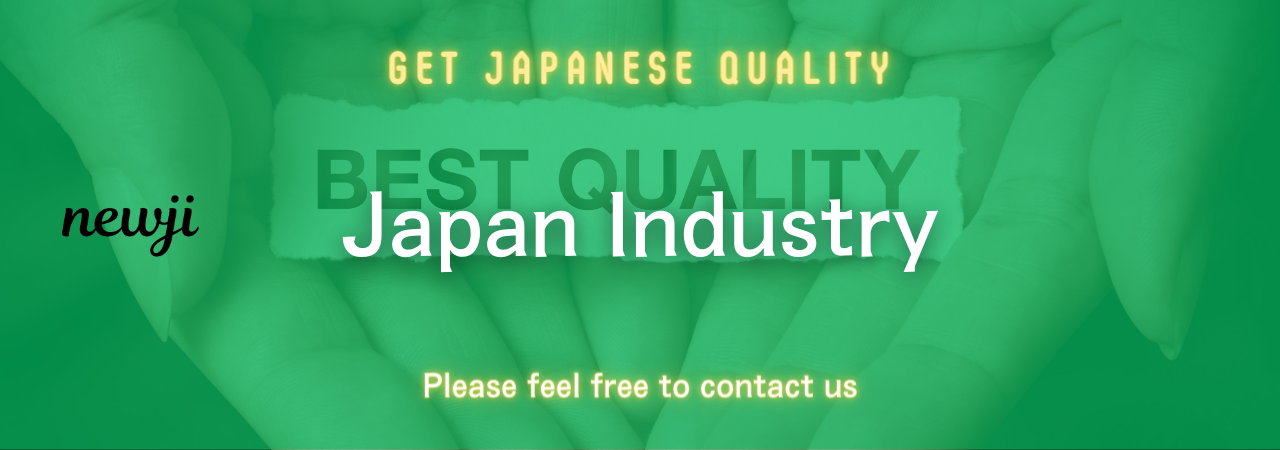
目次
Understanding the Basics of Semiconductor Manufacturing
Semiconductor manufacturing is a complex process that involves the production of tiny semiconductor devices used in electronic circuits and various digital gadgets.
These devices are fabricated using materials like silicon, and the manufacturing process includes several steps such as doping, etching, cleaning, and photolithography.
Due to the complexity and precision required, optimizing the semiconductor manufacturing process is crucial to improving efficiency, yield, and product quality.
Experimentation plays a significant role in discovering the best ways to enhance these processes.
What is Experimental Design?
Experimental design is a structured method used by engineers and scientists to conduct experiments efficiently and systematically.
It involves planning how to conduct an experiment, collecting data, analyzing it, and drawing conclusions.
The purpose of using experimental design in semiconductor manufacturing is to identify the factors or variables that significantly affect the process outcome and to find optimal settings for those factors.
This approach not only minimizes cost and time but also maximizes understanding and process optimization.
Key Elements of Experimental Design in Semiconductor Manufacturing
Before implementing experimental design in semiconductor manufacturing, it’s essential to understand its core components.
Let’s delve into the key elements that form the backbone of this approach.
Identifying Factors
Factors are the variables that can influence the outcome of a semiconductor manufacturing process.
Examples of factors include temperature, time, concentration of reactants, and pressure.
Identifying the right factors is crucial because it allows engineers to understand which variables need to be controlled or adjusted to optimize the process.
Level Setting
Each factor has different levels, which are the possible values or conditions it can take.
In semiconductor manufacturing, level setting often refers to deciding the optimal temperature range or pressure level to achieve the best results.
Choosing the appropriate levels for each factor is crucial to conducting meaningful experiments and obtaining reliable results.
Response Measurement
The response is the output or the result you aim to measure and optimize in the manufacturing process.
In semiconductor manufacturing, responses can include yield, material properties, electrical performance, or product quality.
Accurate measurement of the response is critical because it provides the data needed to analyze the effects of various factors and their settings.
Design of Experiments (DOE) Technique
One of the most powerful tools in experimental design for semiconductor manufacturing is the Design of Experiments (DOE) technique.
DOE is a systematic method that helps engineers determine the effect of multiple factors on a process simultaneously, allowing for comprehensive analysis and optimization.
For example, a full factorial design, which is a type of DOE, evaluates all possible combinations of factors and levels to identify the best settings for the process.
Benefits of Using Experimental Design in Semiconductor Manufacturing
Experimental design offers numerous advantages when applied to semiconductor manufacturing processes.
Understanding these benefits can underscore its importance in optimizing manufacturing outcomes.
Improved Efficiency
By applying experimental design, manufacturers can streamline their processes, reducing the amount of time and resources needed for experimentation.
This efficiency boost is achieved because the methodology allows for evaluating multiple factors simultaneously rather than one at a time.
Enhanced Product Quality
Optimizing the semiconductor manufacturing process through experimental design leads to improved product quality.
By identifying optimal settings for critical factors, manufacturers can produce semiconductors with better performance and reliability.
Reduced Costs
Experimental design helps in reducing costs by minimizing unnecessary trials and errors during the manufacturing process.
With fewer resources spent on ineffective experiments, manufacturers can allocate their budget more efficiently.
Increased Yield
Yield refers to the percentage of acceptable products produced within a manufacturing batch.
Using experimental design helps in maximizing yield by pinpointing conditions that ensure the greatest number of high-quality semiconductors.
Steps in Implementing Experimental Design
To make the most of experimental design in semiconductor manufacturing, it’s essential to follow a structured approach.
Here’s a step-by-step guide to implementing this methodology effectively.
Step 1: Define Objectives
Before commencing any experimental design, clearly defining the goals and objectives is crucial.
Are you looking to improve yield, reduce defects, or enhance certain properties?
Having well-defined objectives will guide the entire experiment process.
Step 2: Select Factors and Levels
Identify the factors that may impact the manufacturing process and determine the levels at which each factor will be tested.
Selecting the right factors and levels will set the foundation for success.
Step 3: Choose the Experimental Design
Select the experimental design that best suits your objectives and constraints.
For comprehensive analysis, a full factorial design may be appropriate, while a fractional factorial design could be used when looking to reduce the number of experimental runs.
Step 4: Conduct Experiments
Perform the experiments according to the chosen design, taking care to maintain consistency and precision in measurements.
Ensure that all data collected is accurate and reliable.
Step 5: Analyze Data
Analyze the data using statistical methods to interpret the effects of different factors and levels on the process outcome.
This analysis will help identify the optimal factor settings needed for improvement.
Step 6: Implement and Monitor
Implement the optimal factor settings identified during the analysis in the actual manufacturing process.
Regularly monitor the results to ensure that improvements are maintained and make adjustments as needed to accommodate any changes or new knowledge gained.
Conclusion
The application of experimental design in semiconductor manufacturing is a powerful strategy for optimizing processes, improving efficiency, reducing costs, and enhancing product quality.
By understanding and applying the principles of experimental design, manufacturers can significantly improve their operations, yielding better products that meet the ever-evolving demands of the technology market.
This structured approach to experimentation not only benefits manufacturers but ultimately enhances the end-user experience with higher-quality semiconductor products.
資料ダウンロード
QCD管理受発注クラウド「newji」は、受発注部門で必要なQCD管理全てを備えた、現場特化型兼クラウド型の今世紀最高の受発注管理システムとなります。
ユーザー登録
受発注業務の効率化だけでなく、システムを導入することで、コスト削減や製品・資材のステータス可視化のほか、属人化していた受発注情報の共有化による内部不正防止や統制にも役立ちます。
NEWJI DX
製造業に特化したデジタルトランスフォーメーション(DX)の実現を目指す請負開発型のコンサルティングサービスです。AI、iPaaS、および先端の技術を駆使して、製造プロセスの効率化、業務効率化、チームワーク強化、コスト削減、品質向上を実現します。このサービスは、製造業の課題を深く理解し、それに対する最適なデジタルソリューションを提供することで、企業が持続的な成長とイノベーションを達成できるようサポートします。
製造業ニュース解説
製造業、主に購買・調達部門にお勤めの方々に向けた情報を配信しております。
新任の方やベテランの方、管理職を対象とした幅広いコンテンツをご用意しております。
お問い合わせ
コストダウンが利益に直結する術だと理解していても、なかなか前に進めることができない状況。そんな時は、newjiのコストダウン自動化機能で大きく利益貢献しよう!
(β版非公開)