- お役立ち記事
- Example of restructuring the purchasing department’s procurement process to reduce the risk of material supply delays
月間76,176名の
製造業ご担当者様が閲覧しています*
*2025年3月31日現在のGoogle Analyticsのデータより
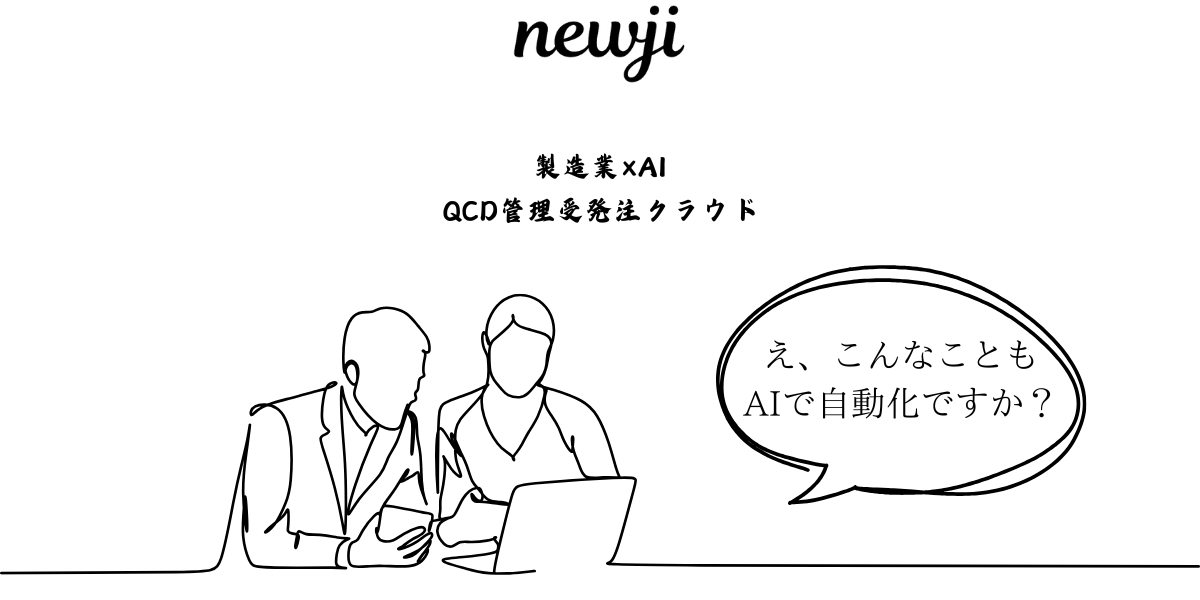
Example of restructuring the purchasing department’s procurement process to reduce the risk of material supply delays
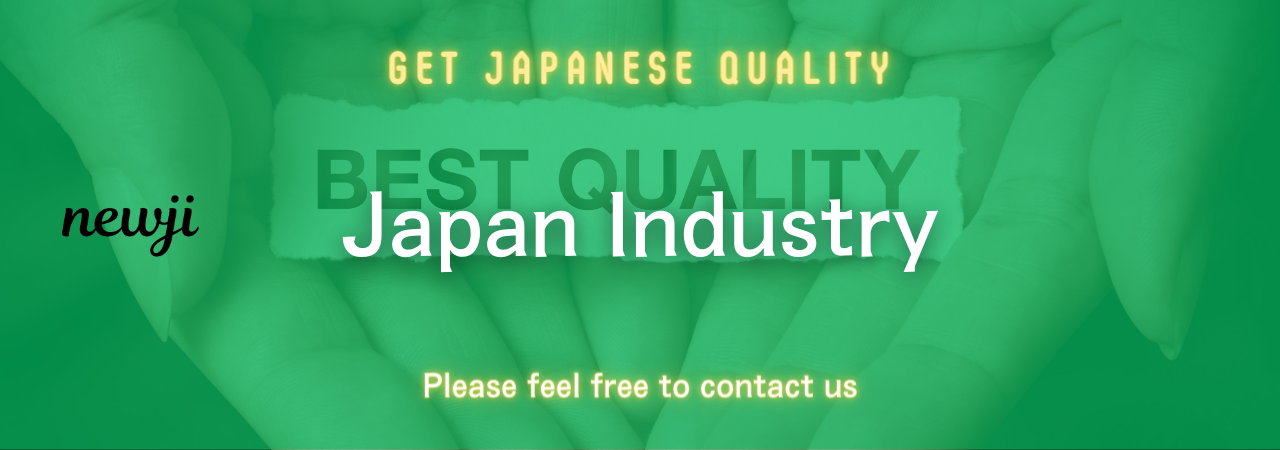
目次
Understanding the Procurement Process
In any organization, the procurement process in the purchasing department plays a vital role in ensuring the smooth operation of services and production.
Procurement involves sourcing and acquiring the goods, services, or materials that an organization needs to operate effectively.
The process encompasses a series of steps: identifying needs, selecting suppliers, negotiating contracts, and acquiring the necessary items at the best possible price.
A streamlined procurement process helps an organization maintain cost control and operational efficiency.
Importance of Reducing Material Supply Delays
One key challenge within the procurement process is the risk of material supply delays.
Delays can significantly disrupt production schedules, lead to costly downtimes, and affect customer satisfaction.
To mitigate these risks, it is essential for the purchasing department to implement strategies designed to anticipate and address potential supply chain disruptions.
Effective risk management in procurement is vital for maintaining business continuity and providing timely products and services to clients.
Restructuring the Procurement Process
Here are some steps an organization can implement to restructure the procurement process and reduce material supply delays:
1. Improving Supplier Selection
A critical aspect of reducing supply delays is choosing the right suppliers.
This goes beyond selecting vendors who offer the lowest prices.
It’s important to evaluate suppliers based on their reliability, delivery performance, financial stability, and quality of materials.
Organizations should consider developing long-term partnerships with multiple suppliers, which offers a cushion in case one vendor encounters difficulties.
Additionally, these partnerships can foster better communication and collaboration, ensuring that both parties work towards common goals.
2. Leveraging Technology
Technology can play a transformative role in enhancing the procurement process.
By using digital tools, organizations can automate routine tasks, track supplier interactions, and gain insights into supply chain dynamics.
Implementing a robust procurement software system allows real-time tracking of orders, inventories, and shipments.
This proactive approach helps identify potential delays early and allows for timely corrective action, significantly reducing the risk of unexpected material shortages.
3. Enhancing Communication Channels
Clear and consistent communication between the purchasing department and suppliers is crucial.
Regular updates and feedback facilitate a mutual understanding of expectations and can preemptively address potential issues.
Establishing an open line of communication ensures both parties have a shared vision, particularly regarding timelines and order specifications.
Ongoing communication can also streamline the resolution of any disputes or misunderstandings that may arise, thereby keeping procurement processes smooth and uninterrupted.
4. Conducting Risk Assessments
Conducting risk assessments of the supply chain is essential.
These assessments should identify potential vulnerabilities in the procurement process, such as reliance on a single supplier or geographical risks.
A thorough risk assessment allows organizations to devise strategic plans, such as sourcing from multiple geographic regions or investigating alternative delivery methods.
Regularly updating risk assessments helps adapt to changes in the supply chain landscape and maintain robust procurement practices.
5. Fostering a Culture of Continuous Improvement
Creating a culture that emphasizes continuous improvement within the purchasing department is fundamental to reducing supply chain risks.
Regularly reviewing and analyzing procurement processes identifies areas for improvement and innovation.
Departments should encourage feedback and new ideas from team members to drive improvements.
Investing in training and developing the skills of purchasing department personnel ensures that they are equipped to handle the evolving challenges of the procurement landscape effectively.
Collaborating for Long-term Success
Procurement is not an isolated function but a collaborative effort that requires coordination with other departments.
By integrating procurement with production, logistics, and quality assurance, organizations can achieve a comprehensive view of their material needs and anticipate potential delays better.
Collaboration encourages departments to share resources and information, which leads to optimizing processes and aligning objectives company-wide.
Monitoring and Review
Once procurement processes have been restructured, it’s important to establish key performance indicators (KPIs) to measure their effectiveness.
Regular performance reviews help assess progress and ensure that procurement goals align with broader organizational objectives.
KPIs such as delivery times, order accuracy, and cost savings provide measurable insights into how well the procurement strategies are working.
Continuous monitoring allows organizations to remain agile and make timely adjustments in strategies to enhance efficiency and reduce the likelihood of material supply delays.
Conclusion
Restructuring the procurement process in the purchasing department is crucial for minimizing the risk of material supply delays.
By focusing on strategic supplier selection, leveraging technology, enhancing communication, conducting risk assessments, and promoting continuous improvement, organizations can create a resilient supply chain.
Collaborative efforts within the organization further solidify this process, helping ensure that production schedules remain uninterrupted and customer satisfaction is maintained.
Through careful planning and proactive management, organizations can position themselves to respond effectively to potential disruptions, thus securing long-term success in an ever-changing business environment.
資料ダウンロード
QCD管理受発注クラウド「newji」は、受発注部門で必要なQCD管理全てを備えた、現場特化型兼クラウド型の今世紀最高の受発注管理システムとなります。
ユーザー登録
受発注業務の効率化だけでなく、システムを導入することで、コスト削減や製品・資材のステータス可視化のほか、属人化していた受発注情報の共有化による内部不正防止や統制にも役立ちます。
NEWJI DX
製造業に特化したデジタルトランスフォーメーション(DX)の実現を目指す請負開発型のコンサルティングサービスです。AI、iPaaS、および先端の技術を駆使して、製造プロセスの効率化、業務効率化、チームワーク強化、コスト削減、品質向上を実現します。このサービスは、製造業の課題を深く理解し、それに対する最適なデジタルソリューションを提供することで、企業が持続的な成長とイノベーションを達成できるようサポートします。
製造業ニュース解説
製造業、主に購買・調達部門にお勤めの方々に向けた情報を配信しております。
新任の方やベテランの方、管理職を対象とした幅広いコンテンツをご用意しております。
お問い合わせ
コストダウンが利益に直結する術だと理解していても、なかなか前に進めることができない状況。そんな時は、newjiのコストダウン自動化機能で大きく利益貢献しよう!
(β版非公開)