- お役立ち記事
- Example of reviewing purchasing department contract conditions to reduce supply chain risks
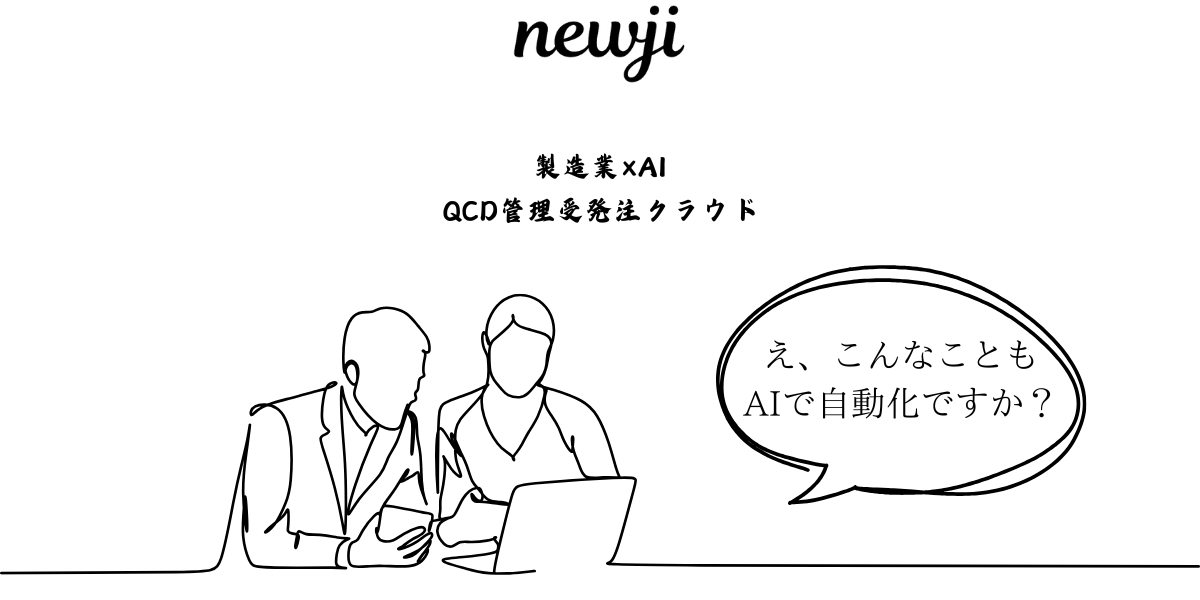
Example of reviewing purchasing department contract conditions to reduce supply chain risks
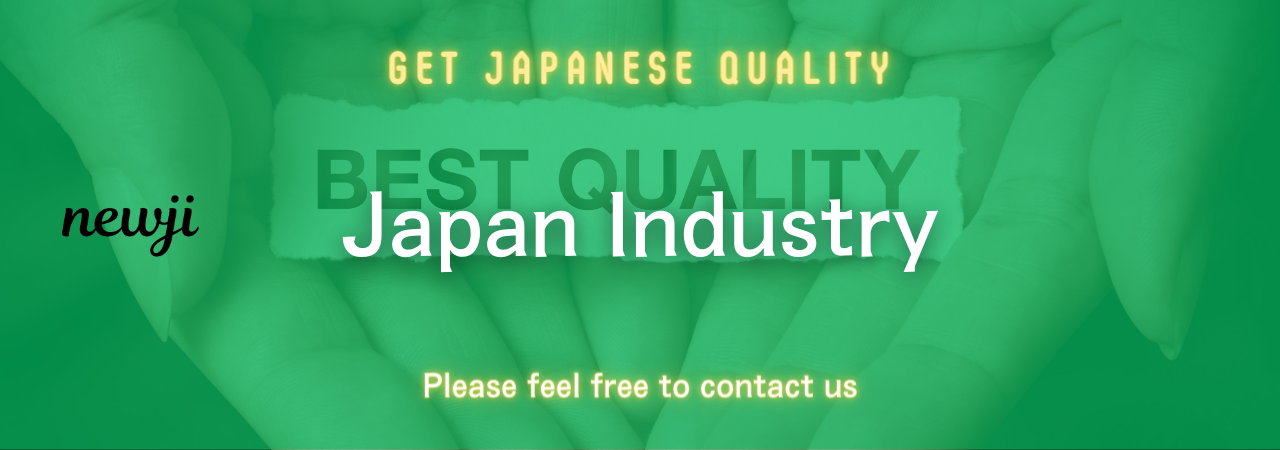
目次
Understanding Supply Chain Risks
In today’s volatile business environment, managing supply chain risks is more crucial than ever.
Supply chain risks can stem from various sources, including natural disasters, political instability, economic fluctuations, and technological failures.
These risks can lead to disruptions that affect the availability of products, increase costs, and ultimately impact the company’s bottom line.
To mitigate these risks, companies need to have a robust risk management strategy in place, and this begins with reviewing and optimizing contract conditions in the purchasing department.
The Role of the Purchasing Department
The purchasing department plays a critical role in the supply chain.
It is responsible for selecting and maintaining relationships with suppliers, negotiating terms, and ensuring the timely delivery of materials required for production.
Because of this, the purchasing department is a key player in identifying and managing supply chain risks.
By carefully reviewing contract conditions, the department can secure terms that offer flexibility and protection against potential disruptions.
Key Contract Conditions to Review
When examining contract conditions, there are several key areas that the purchasing department should focus on to reduce supply chain risks.
1. Force Majeure Clauses
Force majeure clauses are designed to protect parties from unforeseen events that prevent them from fulfilling their contractual obligations.
These can include natural disasters, pandemics, or significant political changes.
It is vital to ensure that the force majeure clause is comprehensive and up-to-date with current risks.
This can help mitigate the impact of events beyond the control of the supplier or the purchasing entity.
2. Price Adjustment Clauses
Price fluctuations in raw materials are a common risk in supply chains.
Having a price adjustment clause in contracts can protect a company from sudden increases or decreases in cost.
This clause should be linked to a reliable index or economic indicator to allow for transparent and fair adjustments.
This ensures that both parties can maintain profitability even in volatile market conditions.
3. Delivery Lead Times and Penalties
Accurate delivery lead times and penalties for delays are critical in maintaining an efficient supply chain.
Contracts should stipulate clear delivery schedules and the consequences of failing to meet these timelines.
This can include financial penalties or the option to secure alternative suppliers.
Effective delivery terms reduce the risk of production downtime and ensure customer demands are met promptly.
4. Quality Assurance Standards
The quality of materials or products is another potential risk factor in supply chains.
Contracts should specify detailed quality assurance standards and testing procedures to ensure that suppliers meet the required specifications.
Regular audits and quality checks can be included in the contract to provide additional assurances.
Building Strong Supplier Relationships
Beyond the specifics of contract conditions, building strong relationships with suppliers is crucial in reducing supply chain risks.
Open communication and collaboration can help identify potential risks early and allow both parties to devise strategies to mitigate them.
Long-term partnerships provide stability and can lead to better terms, more favorable contract conditions, and increased trust.
Supplier Diversification
Relying on a single supplier for critical materials can be risky.
Supplier diversification is an effective strategy to reduce this risk.
By having multiple suppliers, companies can ensure continuity of supply even if one supplier faces a disruption.
The purchasing department should aim to have multiple vetted suppliers for each key component.
Regular Reviews and Audits
Regular contract reviews and supplier audits are essential in identifying emerging risks.
The purchasing department should periodically assess the performance of suppliers against agreed contract terms.
This includes evaluating delivery punctuality, quality of goods, and financial stability of the supplier.
Implementing Technology in Risk Management
Technology can also play a significant role in managing supply chain risks.
Utilizing supply chain management software helps in tracking shipments, monitoring supplier performance, and identifying potential disruptions.
Advanced analytics and artificial intelligence can predict risks by analyzing data trends, enabling proactive rather than reactive management.
Blockchain for Transparency
Blockchain technology provides transparency and traceability in supply chains.
By storing transaction data in a tamper-proof ledger, parties can verify the origin and movement of goods, reducing the risks of fraud or duplication.
This transparency can enhance supplier accountability and streamline contract enforcement.
Developing a Comprehensive Risk Management Strategy
A comprehensive risk management strategy is vital to address potential supply chain disruptions.
This strategy should include risk identification, assessment, and mitigation tactics.
Developing contingency plans and maintaining flexibility in operations can help quickly adapt to unforeseen changes.
Training and Education
Finally, training and educating the purchasing department staff on risk management techniques is essential.
By understanding the intricacies of contract conditions and the complexities of supply chains, staff can make informed decisions that protect the company from risks.
In conclusion, reviewing purchasing department contract conditions is a crucial step in reducing supply chain risks.
By focusing on key contract clauses, building strong supplier relationships, leveraging technology, and implementing a robust risk management strategy, companies can safeguard their operations and ensure long-term success in a dynamic market environment.
資料ダウンロード
QCD調達購買管理クラウド「newji」は、調達購買部門で必要なQCD管理全てを備えた、現場特化型兼クラウド型の今世紀最高の購買管理システムとなります。
ユーザー登録
調達購買業務の効率化だけでなく、システムを導入することで、コスト削減や製品・資材のステータス可視化のほか、属人化していた購買情報の共有化による内部不正防止や統制にも役立ちます。
NEWJI DX
製造業に特化したデジタルトランスフォーメーション(DX)の実現を目指す請負開発型のコンサルティングサービスです。AI、iPaaS、および先端の技術を駆使して、製造プロセスの効率化、業務効率化、チームワーク強化、コスト削減、品質向上を実現します。このサービスは、製造業の課題を深く理解し、それに対する最適なデジタルソリューションを提供することで、企業が持続的な成長とイノベーションを達成できるようサポートします。
オンライン講座
製造業、主に購買・調達部門にお勤めの方々に向けた情報を配信しております。
新任の方やベテランの方、管理職を対象とした幅広いコンテンツをご用意しております。
お問い合わせ
コストダウンが利益に直結する術だと理解していても、なかなか前に進めることができない状況。そんな時は、newjiのコストダウン自動化機能で大きく利益貢献しよう!
(Β版非公開)