- お役立ち記事
- Example of using a collaboration platform to support purchasing processes in the manufacturing industry
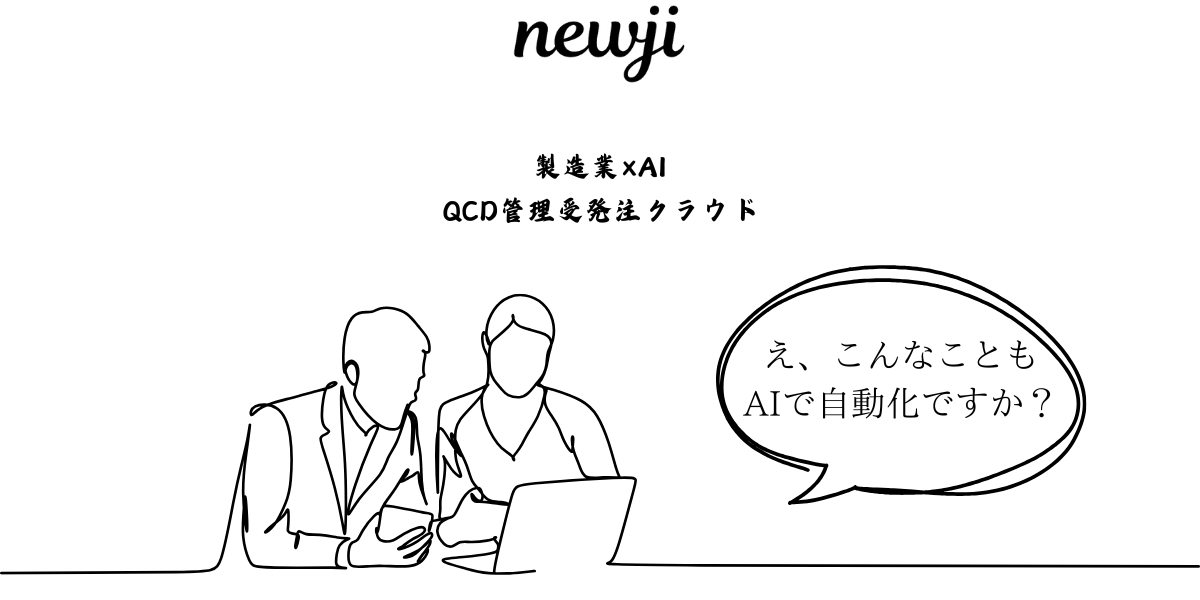
Example of using a collaboration platform to support purchasing processes in the manufacturing industry
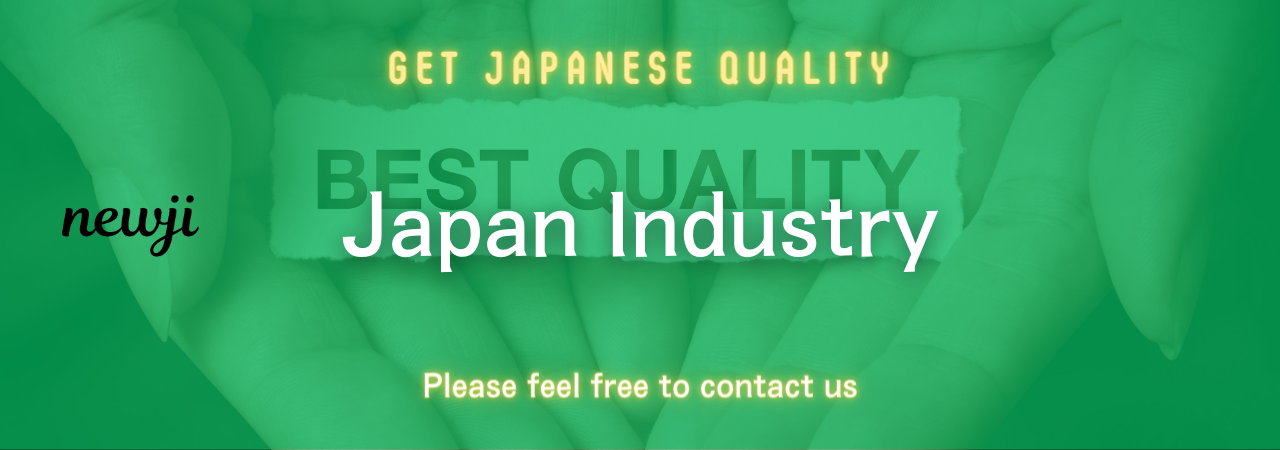
目次
Introduction to Collaboration Platforms in Manufacturing
In today’s fast-paced world, the manufacturing industry constantly seeks ways to streamline processes and enhance efficiency.
One such area where significant improvements can be made is in the purchasing process.
Utilizing a collaboration platform can support and transform the way purchasing operates within manufacturing, leading to increased productivity and cost savings.
Understanding the Purchasing Process in Manufacturing
The purchasing process in manufacturing involves several key steps, from identifying needs and selecting suppliers to negotiating contracts and maintaining records.
This process is crucial to ensure that materials and components are acquired efficiently, cost-effectively, and to the required quality standards.
Key Challenges in the Traditional Purchasing Process
Despite its importance, the traditional purchasing process often faces numerous challenges.
These can include inefficient communication, lack of transparency, difficulties in tracking purchase orders, and fragmented documentation.
Such issues can lead to delays, increased costs, and even production halts if essential materials are not procured on time.
The Role of Collaboration Platforms
Collaboration platforms offer a solution to these challenges by providing a centralized space for teams to communicate, collaborate, and manage tasks seamlessly.
These digital tools integrate various aspects of the purchasing process, promoting transparency, accountability, and more effective decision-making.
Features of Effective Collaboration Platforms
A robust collaboration platform for supporting purchasing processes usually includes features such as:
– Real-time communication tools to ensure quick and effective dialogue between stakeholders.
– Document management systems to organize, share, and access important purchasing documents easily.
– Automated workflows to streamline approval processes and reduce manual errors.
– Analytics tools to track performance and identify areas for improvement.
Benefits of Using Collaboration Platforms
Implementing a collaboration platform can bring numerous benefits to the purchasing processes within the manufacturing industry.
Enhanced Communication
A collaboration platform facilitates real-time communication among team members, departments, and suppliers.
This ensures that everyone is on the same page, reducing misunderstandings and speeding up decision-making processes.
Increased Transparency
By centralizing information and processes, collaboration platforms provide a transparent view of all purchasing activities.
Team members can easily track orders, approvals, and documents, ensuring that nothing is overlooked or lost.
Greater Efficiency
Automated workflows and integrated tools reduce the time spent on repetitive, manual tasks.
This allows purchasing teams to focus on strategic activities, such as analyzing market trends and negotiating better deals with suppliers.
Improved Accountability
With defined roles and responsibilities within the platform, team members are held accountable for their tasks.
This clarity reduces errors and ensures that deadlines are met more consistently.
Case Study: Successful Implementation
Consider the case of a mid-sized manufacturing company that implemented a collaboration platform to overhaul its purchasing processes.
Previously, the company struggled with delayed approvals and frequent miscommunications amongst its purchasing team.
After adopting a collaboration platform, the company saw a marked improvement in several areas:
– Purchase order approval times were reduced by over 40%.
– Communication improved, which led to faster resolution of supplier issues.
– There was a significant decrease in missed orders and lost documents, which had previously been a common problem.
Steps to Implement a Collaboration Platform
Transitioning to a collaboration platform requires careful planning and execution.
Here are steps manufacturing companies can take to ensure a smooth implementation:
Assess Current Processes
Begin by evaluating your current purchasing procedures and identifying areas that require improvement.
This assessment will help tailor the collaboration platform to address specific challenges and bottlenecks.
Choose the Right Platform
Not all collaboration platforms are created equal.
Research and select a platform that aligns with your company’s needs, budget, and existing IT infrastructure.
Train Your Team
Proper training is essential for successful implementation.
Conduct training sessions to familiarize employees with the new platform and its functionalities.
Monitor and Refine
After implementation, continuously monitor the platform’s performance and gather feedback from users.
Use this data to refine and optimize the platform’s usage and address any emerging issues.
Conclusion
The manufacturing industry can significantly benefit from using collaboration platforms to support purchasing processes.
These platforms enhance communication, increase transparency, and improve overall efficiency.
By choosing the right platform and implementing it effectively, manufacturing companies can overcome many traditional challenges and position themselves for future success.
資料ダウンロード
QCD調達購買管理クラウド「newji」は、調達購買部門で必要なQCD管理全てを備えた、現場特化型兼クラウド型の今世紀最高の購買管理システムとなります。
ユーザー登録
調達購買業務の効率化だけでなく、システムを導入することで、コスト削減や製品・資材のステータス可視化のほか、属人化していた購買情報の共有化による内部不正防止や統制にも役立ちます。
NEWJI DX
製造業に特化したデジタルトランスフォーメーション(DX)の実現を目指す請負開発型のコンサルティングサービスです。AI、iPaaS、および先端の技術を駆使して、製造プロセスの効率化、業務効率化、チームワーク強化、コスト削減、品質向上を実現します。このサービスは、製造業の課題を深く理解し、それに対する最適なデジタルソリューションを提供することで、企業が持続的な成長とイノベーションを達成できるようサポートします。
オンライン講座
製造業、主に購買・調達部門にお勤めの方々に向けた情報を配信しております。
新任の方やベテランの方、管理職を対象とした幅広いコンテンツをご用意しております。
お問い合わせ
コストダウンが利益に直結する術だと理解していても、なかなか前に進めることができない状況。そんな時は、newjiのコストダウン自動化機能で大きく利益貢献しよう!
(Β版非公開)