- お役立ち記事
- Examples and Effectiveness of the Seven QC Tools in Quality Control in Manufacturing
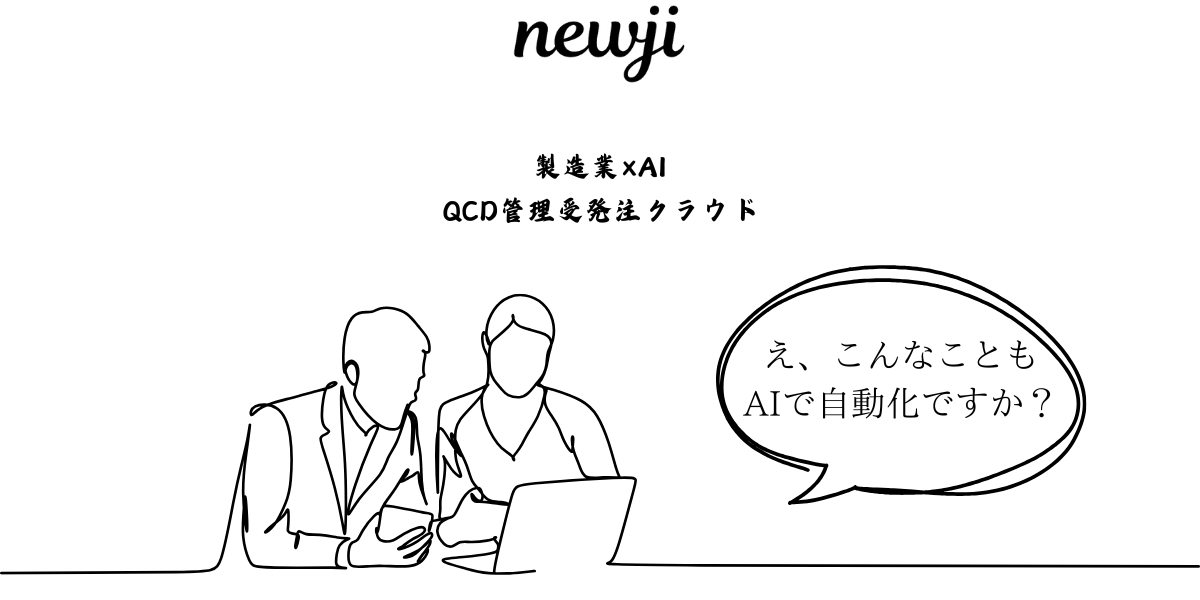
Examples and Effectiveness of the Seven QC Tools in Quality Control in Manufacturing
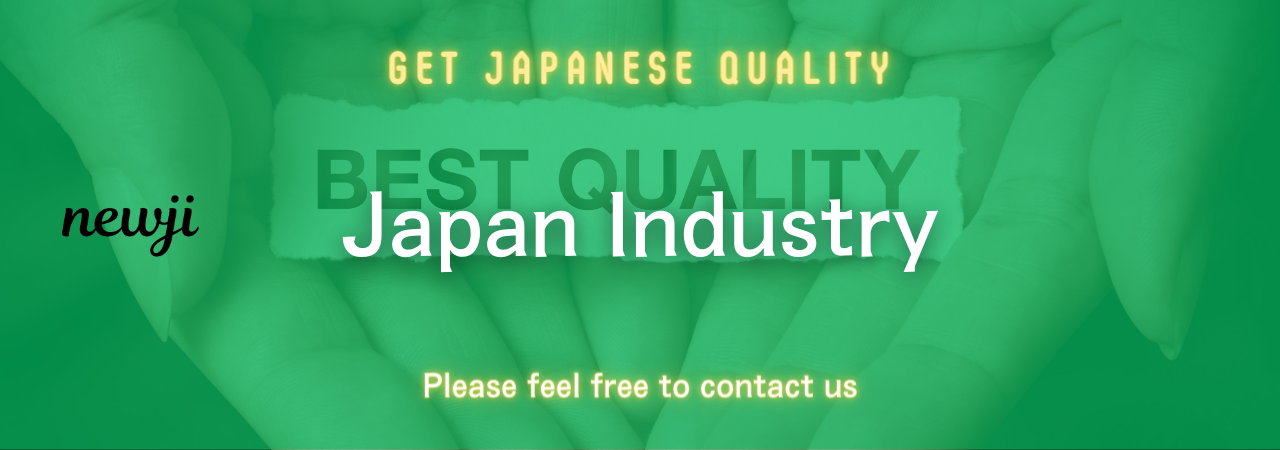
Quality control is crucial for manufacturing. It ensures products meet standards, satisfy customers, and reduce the cost of poor quality. One of the most effective methods for maintaining high-quality standards is by using the Seven QC Tools. This article will explore each tool, provide examples, and discuss its effectiveness.
1. Cause-and-Effect Diagram
Example: Imagine a factory facing a high defect rate in its plastic bottle production line. Engineers use a cause-and-effect diagram to brainstorm and identify potential causes such as machine malfunctions, poor raw materials, and inadequate worker training. This visual aid helps them focus on the most impactful areas for improvement.
Effectiveness: The cause-and-effect diagram, also known as the fishbone diagram or Ishikawa diagram, is highly effective in identifying root causes of problems. It encourages brainstorming and organizes complex issues into manageable categories, simplifying problem-solving.
2. Check Sheet
Example: In a car manufacturing facility, a quality control inspector uses check sheets to record data on defects observed during the inspection of a day’s production. The check sheet categorizes defects into types like scratches, paint issues, and assembly errors.
Effectiveness: Check sheets are simple yet powerful tools for data collection. They help in gathering accurate and real-time data, making it easier to identify patterns and trends. This information can aid in focusing on areas that require immediate attention.
3. Control Chart
Example: A smartphone manufacturer monitors the thickness of screen glass using control charts. Samples are collected in batches, and the thickness is plotted on the chart with upper and lower control limits. Any variation outside these limits signals a potential issue.
Effectiveness: Control charts are essential for monitoring process stability. They help in detecting abnormalities in real-time, allowing for prompt corrective actions. Maintaining processes within control limits ensures consistent product quality.
4. Histogram
Example: A furniture manufacturing plant uses a histogram to display the distribution of the length of wooden planks. The uniform distribution indicates a controlled process, while any skewness or irregularities highlight the need for inspection and correction.
Effectiveness: Histograms offer a visual representation of data distribution, making it easier to understand variability and central tendency. This visualization helps quality control teams quickly identify deviations from desired performance.
5. Pareto Chart
Example: A textile company analyzes defects in fabric production and creates a Pareto chart. The chart reveals that 80% of defects arise from 20% of causes, such as incorrect dyeing and weaving machine issues.
Effectiveness: The Pareto Principle, or the 80/20 rule, underlies the Pareto chart. It is instrumental in prioritizing issues by highlighting the most significant factors. This focus allows teams to allocate resources efficiently and effectively tackle the most impactful problems.
6. Scatter Diagram
Example: A beverage company wants to study the relationship between bottle cap tightness and leakage rates. A scatter diagram plots cap tightness against leakage incidents, revealing a clear correlation.
Effectiveness: Scatter diagrams are helpful for visualizing relationships between two variables. Recognizing such patterns allows quality control teams to make informed decisions regarding process adjustments and improvements.
7. Flowchart
Example: A flowchart in a semiconductor manufacturing process maps out steps from raw material intake to final packaging. Quality control personnel use this to identify bottlenecks and inefficiencies.
Effectiveness: Flowcharts provide a clear and detailed view of a process. They help in understanding each step, identifying redundancies, and streamlining operations. This tool is vital for optimizing processes and ensuring quality throughout the production line.
目次
Integration of the Seven QC Tools
Example: A toy manufacturing company incorporates all seven QC tools to manage quality control. They first use a cause-and-effect diagram to identify potential defect causes, then gather data using check sheets and control charts to monitor process stability. Histograms and Pareto charts help visualize data and prioritize issues. Scatter diagrams analyze relationships between variables, and flowcharts optimize the entire process workflow.
Effectiveness: Using the tools in an integrated manner enhances overall quality control. The combined approach allows for comprehensive problem-solving and continuous improvement, leading to higher product quality and customer satisfaction.
Conclusion
In manufacturing, quality control is the bedrock of success, ensuring products meet stringent standards and customer expectations. The Seven QC Tools are invaluable in this endeavor. The cause-and-effect diagram helps identify root causes, while check sheets and control charts aid in data collection and process monitoring. Histograms and Pareto charts provide visual insights into data distribution and prioritization of issues. Scatter diagrams highlight relationships between variables, and flowcharts streamline processes. Implementing these tools collectively strengthens quality control practices, leading to superior products and improved operational efficiency. By mastering these tools, manufacturing companies can achieve sustainable success and stay competitive in the market.
資料ダウンロード
QCD調達購買管理クラウド「newji」は、調達購買部門で必要なQCD管理全てを備えた、現場特化型兼クラウド型の今世紀最高の購買管理システムとなります。
ユーザー登録
調達購買業務の効率化だけでなく、システムを導入することで、コスト削減や製品・資材のステータス可視化のほか、属人化していた購買情報の共有化による内部不正防止や統制にも役立ちます。
NEWJI DX
製造業に特化したデジタルトランスフォーメーション(DX)の実現を目指す請負開発型のコンサルティングサービスです。AI、iPaaS、および先端の技術を駆使して、製造プロセスの効率化、業務効率化、チームワーク強化、コスト削減、品質向上を実現します。このサービスは、製造業の課題を深く理解し、それに対する最適なデジタルソリューションを提供することで、企業が持続的な成長とイノベーションを達成できるようサポートします。
オンライン講座
製造業、主に購買・調達部門にお勤めの方々に向けた情報を配信しております。
新任の方やベテランの方、管理職を対象とした幅広いコンテンツをご用意しております。
お問い合わせ
コストダウンが利益に直結する術だと理解していても、なかなか前に進めることができない状況。そんな時は、newjiのコストダウン自動化機能で大きく利益貢献しよう!
(Β版非公開)