- お役立ち記事
- Examples of failures in plastic parts prototype production and improvements
月間76,176名の
製造業ご担当者様が閲覧しています*
*2025年3月31日現在のGoogle Analyticsのデータより
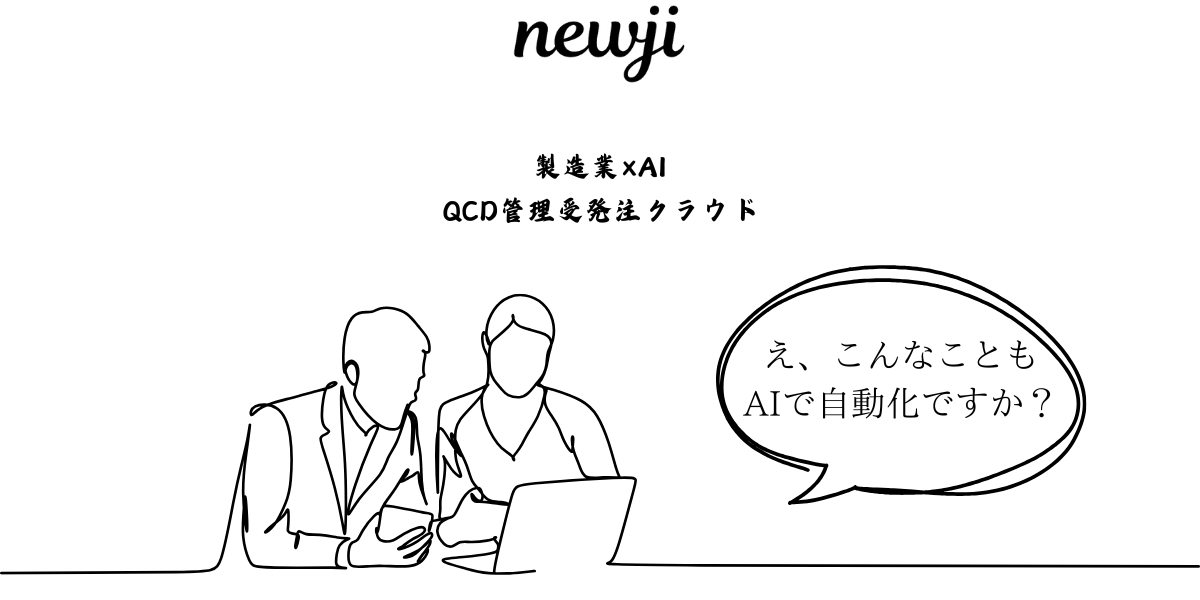
Examples of failures in plastic parts prototype production and improvements
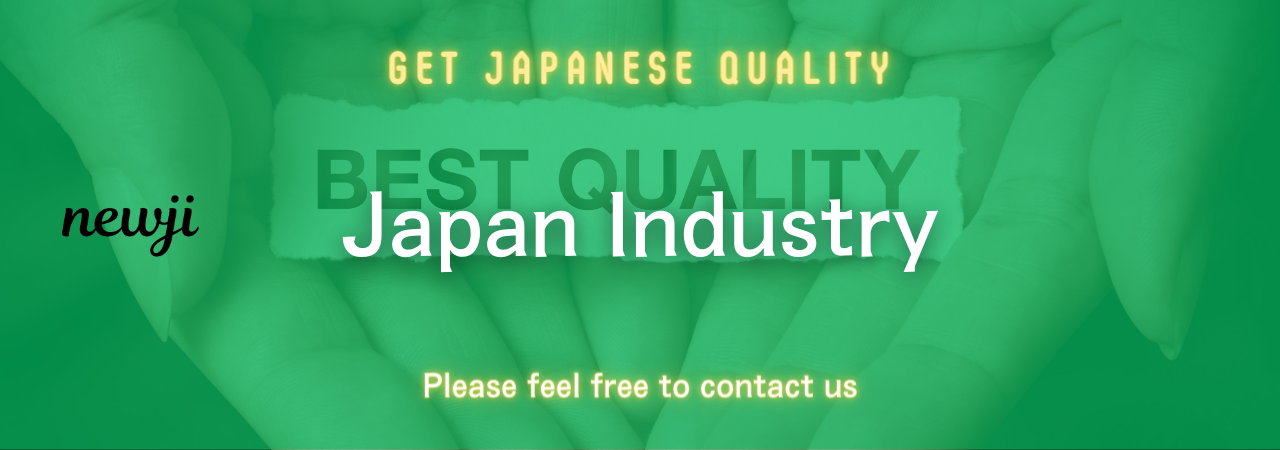
目次
Introduction to Plastic Parts Prototyping
The production of plastic parts prototypes is crucial in the design and development of new products.
Prototyping helps manufacturers test designs, assess functionality, and make necessary adjustments before mass production.
However, the process is not without its challenges.
There are common failures that can arise in the prototyping phase, and learning from these can lead to significant improvements.
In this article, we’ll explore examples of failures in plastic parts prototype production and discuss improvements that can lead to successful outcomes.
Understanding Common Failures
Plastic parts prototyping is complex due to the multitude of variables involved.
Failures often occur due to factors such as material selection, design errors, and manufacturing processes.
Addressing these can reduce costs, save time, and improve product quality.
Material Selection Issues
Choosing the wrong material for a prototype can result in severe functional issues.
Each material has specific properties such as tensile strength, elasticity, and thermal resistance.
Failure to consider these can lead to prototypes that are not representative of the final product.
For instance, a prototype made from a plastic type with insufficient strength might break during testing, misleading developers about its functionality.
Design Errors
Design flaws represent a significant portion of prototype failures.
These errors can include structural weaknesses, poor fit, or oversights in functional elements.
For example, if a component’s geometry does not account for stress points, it could fail under load.
Additionally, design mistakes such as incorrect dimensions can lead to misalignment and assembly problems.
Manufacturing Defects
The manufacturing process itself can introduce defects into prototypes.
Issues such as warping, uneven surface finishes, or incomplete fills can compromise the integrity of the prototype.
These problems are often a result of incorrect mold designs, improper machine settings, or environmental conditions during production.
Improvements in Plastic Parts Prototype Production
Addressing the failures in plastic parts prototyping requires a strategic approach.
Here are some key improvements that can enhance the prototyping process:
Thorough Material Evaluation
An in-depth evaluation of material properties is critical.
Before selecting a material, consider the prototype’s requirements such as strength, flexibility, and resistance to temperature.
Combining data from material datasheets and conducting preliminary tests can help make informed decisions.
By doing so, the chances of functional discrepancies in the prototype are minimized.
Advanced Design Software
Utilizing advanced design software can greatly reduce the occurrence of design errors.
Software with simulation capabilities allows engineers to visualize stress points, thermal effects, and material behavior.
These simulations enable teams to make necessary adjustments early in the design process, reducing the likelihood of design-related failures.
Iterative Design and Testing
Adopting an iterative approach to design and testing can improve prototype accuracy.
Create multiple versions of a prototype to test various aspects and refine designs.
This approach allows for quick identification and correction of any problems, leading to a more robust final design.
Implementing Quality Control Measures
Quality control is essential throughout the prototyping process.
Incorporating measures such as regular inspections and testing can prevent defects from progressing unnoticed.
Regular Inspections
Conduct regular inspections at various stages of the production process.
Visual and dimensional checks are vital to ensure that each prototype meets its design specifications.
These inspections can catch issues early, reducing waste and rework.
Functional Testing
Perform functional tests under real-world conditions to assess the prototype’s performance.
Testing parameters such as load capacity, temperature resistance, and durability can highlight any areas requiring improvement.
Feedback from these tests is invaluable for refining designs and material selections.
Conclusion
The prototyping of plastic parts is an essential step in product development that comes with its own set of challenges.
Understanding common failures such as material selection issues, design errors, and manufacturing defects can lead to more effective prototyping strategies.
Improvements, including thorough material evaluation, advanced design tools, and implementing quality control measures, can drastically reduce these failures.
By adopting these practices, manufacturers can enhance prototype quality, leading to successful product development and market readiness.
資料ダウンロード
QCD管理受発注クラウド「newji」は、受発注部門で必要なQCD管理全てを備えた、現場特化型兼クラウド型の今世紀最高の受発注管理システムとなります。
ユーザー登録
受発注業務の効率化だけでなく、システムを導入することで、コスト削減や製品・資材のステータス可視化のほか、属人化していた受発注情報の共有化による内部不正防止や統制にも役立ちます。
NEWJI DX
製造業に特化したデジタルトランスフォーメーション(DX)の実現を目指す請負開発型のコンサルティングサービスです。AI、iPaaS、および先端の技術を駆使して、製造プロセスの効率化、業務効率化、チームワーク強化、コスト削減、品質向上を実現します。このサービスは、製造業の課題を深く理解し、それに対する最適なデジタルソリューションを提供することで、企業が持続的な成長とイノベーションを達成できるようサポートします。
製造業ニュース解説
製造業、主に購買・調達部門にお勤めの方々に向けた情報を配信しております。
新任の方やベテランの方、管理職を対象とした幅広いコンテンツをご用意しております。
お問い合わせ
コストダウンが利益に直結する術だと理解していても、なかなか前に進めることができない状況。そんな時は、newjiのコストダウン自動化機能で大きく利益貢献しよう!
(β版非公開)