- お役立ち記事
- Examples of innovations in reducing procurement costs in the auto parts manufacturing industry
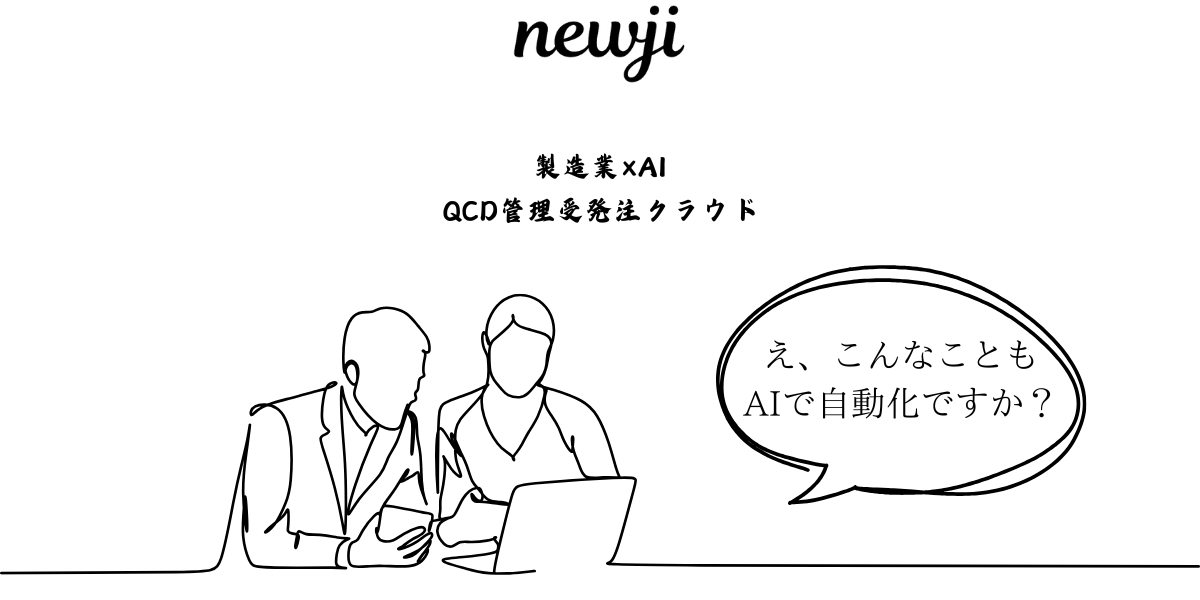
Examples of innovations in reducing procurement costs in the auto parts manufacturing industry
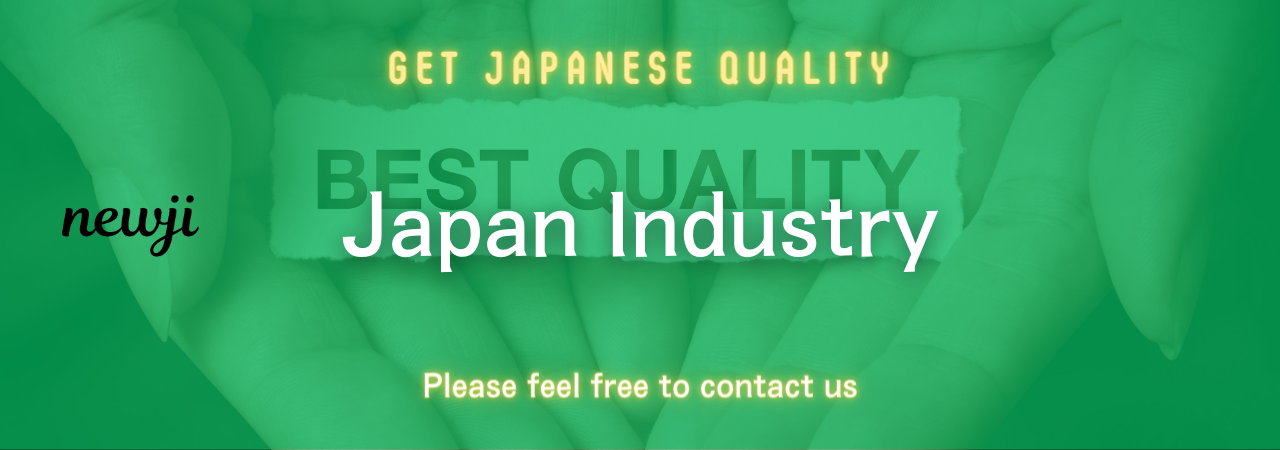
目次
Understanding Procurement Costs in the Auto Parts Industry
Procurement costs are a significant aspect of the auto parts manufacturing industry.
They include the prices of raw materials, logistics, storage, and indirect costs associated with transactions.
Managing these costs effectively is crucial for manufacturers, as it affects the overall profitability of their operations.
By understanding what drives procurement costs, companies can develop strategies to reduce them.
The Importance of Procurement in Auto Parts Manufacturing
Procurement is an essential part of the auto parts manufacturing process.
It involves sourcing the necessary materials and components needed to produce quality products.
With the vast array of auto parts required to build a vehicle, procurement teams must ensure efficient and cost-effective sourcing.
This efficiency directly influences not only the bottom line but also the ability to remain competitive in a fast-paced market.
Innovative Strategies to Reduce Procurement Costs
Manufacturers in the auto parts industry are continuously seeking methods to reduce procurement costs.
Innovative approaches can lead to significant savings and position a company ahead in the competitive landscape.
Leveraging Technology and Automation
One of the most impactful innovations is the integration of technology and automation in the procurement process.
Utilizing advanced procurement software can streamline purchasing activities, reduce human error, and improve accuracy.
Automation tools can handle repetitive tasks such as order placements and tracking, freeing up human resources for more strategic roles.
Supplier Relationship Management
Building strong, long-term relationships with suppliers can also lead to reduced procurement costs.
Open communication channels and regular collaboration with suppliers can foster better negotiations and discounts.
Companies can also benefit from early involvement of suppliers in the design process, leading to cost-effective solutions.
Optimizing Inventory Management
Effective inventory management plays a vital role in reducing procurement costs.
By adopting just-in-time (JIT) inventory practices, manufacturers can minimize holding costs and reduce waste.
JIT involves receiving goods only as they are needed in the production process, thus lowering storage expenses.
Implementing Lean Manufacturing Principles
Lean manufacturing focuses on reducing waste and optimizing processes, which directly impacts procurement costs.
By streamlining operations and identifying inefficiencies, companies can cut down on unnecessary expenditures and improve their bottom line.
Incorporating practices such as continuous improvement and value stream mapping are examples of lean strategies that help in cost reduction.
Exploring Alternative Sourcing Options
Another way manufacturers can reduce procurement costs is by exploring alternative sourcing options.
This involves seeking suppliers in different regions or utilizing alternative materials that provide similar quality at a lower cost.
Global Sourcing Opportunities
The global market provides a wide range of opportunities for cost reduction.
By expanding the search beyond domestic suppliers, companies may find more competitive pricing and improved terms.
However, it’s important to consider factors such as shipping costs, tariffs, and potential risks associated with overseas sourcing.
Using Recycled and Sustainable Materials
As sustainability becomes increasingly significant, manufacturers are looking at recycled and sustainable materials as viable options.
This not only helps in reducing procurement costs but also aligns with corporate social responsibility goals.
Employing recycled materials can sometimes reduce raw material costs and enhance a company’s reputation as environmentally conscious.
Collaboration with Industry Peers
Collaborating with industry peers can also bring about innovative ideas that lead to lower procurement costs.
Through joint ventures and collaborations, companies can share best practices and bulk purchasing strategies, resulting in cost savings for all involved.
Purchasing Consortia
Forming purchasing consortia allows multiple companies to come together to negotiate better prices with suppliers.
By combining their purchasing power, manufacturers can achieve economies of scale, which can significantly lower costs.
These consortiums often have greater leverage to negotiate terms, securing favorable conditions for all members.
Conclusion
In the dynamic auto parts manufacturing industry, reducing procurement costs is essential for maintaining competitiveness and profitability.
By adopting innovative strategies such as leveraging technology, managing relationships with suppliers, optimizing inventories, and exploring alternative sourcing, manufacturers can achieve substantial cost savings.
Collaboration with industry peers also offers unique opportunities to further minimize expenses.
As the industry continues to evolve, staying adaptable and open to new ideas will be key to managing procurement costs effectively.
資料ダウンロード
QCD調達購買管理クラウド「newji」は、調達購買部門で必要なQCD管理全てを備えた、現場特化型兼クラウド型の今世紀最高の購買管理システムとなります。
ユーザー登録
調達購買業務の効率化だけでなく、システムを導入することで、コスト削減や製品・資材のステータス可視化のほか、属人化していた購買情報の共有化による内部不正防止や統制にも役立ちます。
NEWJI DX
製造業に特化したデジタルトランスフォーメーション(DX)の実現を目指す請負開発型のコンサルティングサービスです。AI、iPaaS、および先端の技術を駆使して、製造プロセスの効率化、業務効率化、チームワーク強化、コスト削減、品質向上を実現します。このサービスは、製造業の課題を深く理解し、それに対する最適なデジタルソリューションを提供することで、企業が持続的な成長とイノベーションを達成できるようサポートします。
オンライン講座
製造業、主に購買・調達部門にお勤めの方々に向けた情報を配信しております。
新任の方やベテランの方、管理職を対象とした幅広いコンテンツをご用意しております。
お問い合わせ
コストダウンが利益に直結する術だと理解していても、なかなか前に進めることができない状況。そんな時は、newjiのコストダウン自動化機能で大きく利益貢献しよう!
(Β版非公開)