- お役立ち記事
- Examples of logistics reforms to shorten lead times that purchasing personnel should keep in mind
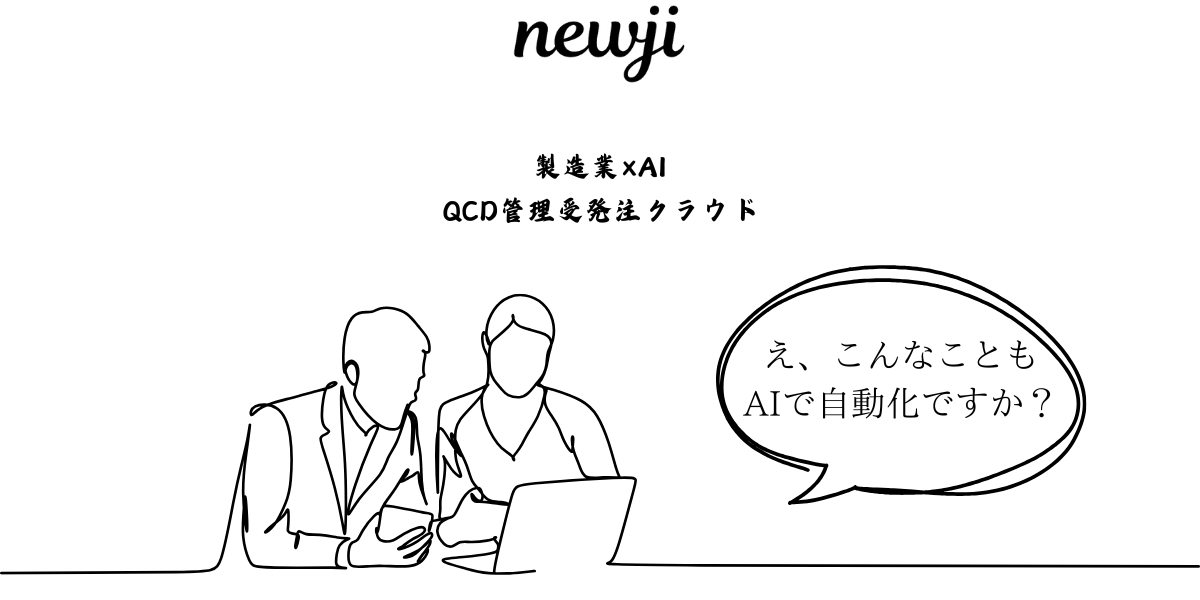
Examples of logistics reforms to shorten lead times that purchasing personnel should keep in mind
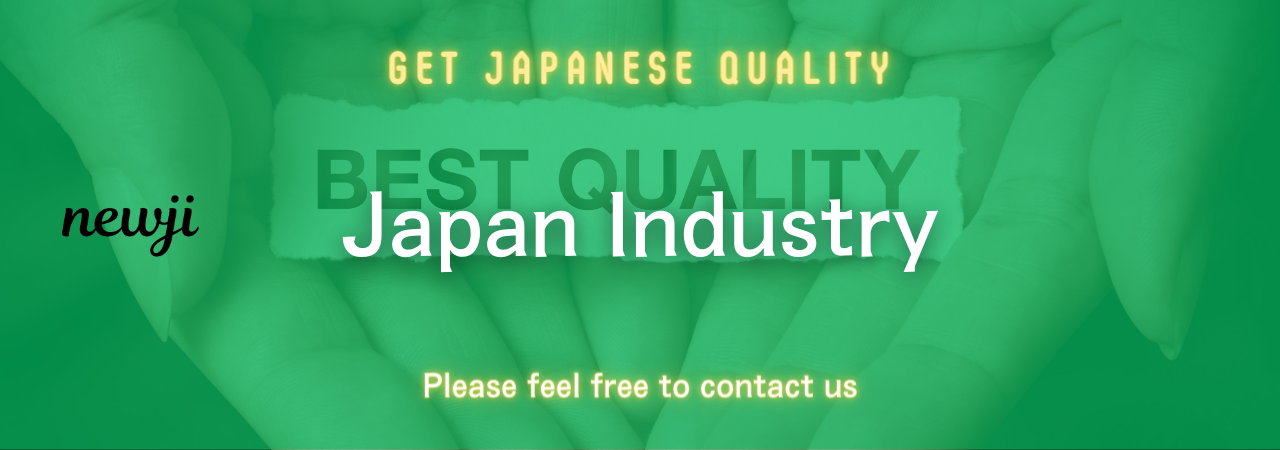
目次
Understanding Lead Times in Logistics
Lead time is a critical factor in the world of logistics and purchasing.
It refers to the amount of time it takes for a product to be delivered from the moment an order is placed until it arrives at the customer’s door.
In the world of purchasing, this is especially important because shorter lead times can result in increased customer satisfaction, reduced inventory costs, and improved competitiveness.
Purchasing personnel need to be well-versed in strategies to reform logistics processes and minimize lead times.
Streamlining Supply Chain Management
One of the most effective ways to shorten lead times is to streamline supply chain management.
This involves closely examining every step in the supply chain to identify bottlenecks and inefficiencies.
By optimizing these processes, companies can reduce the time it takes to move goods from suppliers to customers.
An essential element of supply chain optimization is to enhance communication and collaboration with suppliers.
The quicker and more efficiently you can communicate with suppliers, the faster issues can be resolved and orders processed.
Utilizing advanced technologies such as Electronic Data Interchange (EDI) and automated order systems can significantly speed up the procurement process and reduce lead times.
Implementing Just-In-Time Inventory
Just-In-Time (JIT) inventory is a strategy that aligns raw material orders from suppliers directly with production schedules.
This approach minimizes the need for holding inventory, thus reducing storage costs and the time products spend in warehouses.
In JIT systems, products are manufactured or ordered only as needed, which ensures that excess stock does not build up and that lead times are kept short.
Purchasing personnel should consider adopting JIT practices in collaboration with trusted suppliers.
It requires precise scheduling and a reliable logistics network to ensure that materials arrive exactly when they are needed without causing delays in production.
Enhancing Transportation Efficiency
The transportation phase is a crucial component of the supply chain where significant time savings can be realized.
Leveraging a mix of transportation modes such as road, rail, sea, and air can help in selecting the fastest and most cost-effective delivery routes.
Additionally, optimizing delivery schedules and logistics planning can reduce transit times.
Investing in technologies that improve tracking and route planning can offer real-time insights into delivery progress.
This can help manage delays proactively by finding alternative routes or transportation options to keep deliveries on schedule.
Building Strong Relationships with Suppliers
Building and maintaining strong relationships with suppliers can directly influence lead times.
Good relationships can result in priority treatment when placing orders, quicker responses, and more flexible shipping options.
Ensuring that suppliers understand your lead time objectives and constraints is essential for collaboration.
Regular evaluations of supplier performance and maintaining open lines of communication through regular meetings or business reviews can secure better terms and commitments for shorter lead times.
Utilizing Advanced Technology
The integration of advanced logistics technology is fundamental to reducing lead times.
Automation tools, such as robotics in warehouses and AI-powered analytics, can significantly enhance operational efficiency.
Implementing Warehouse Management Systems (WMS) can streamline warehouse operations by optimizing inventory placement and product picking processes.
Similarly, Transportation Management Systems (TMS) can enhance the efficiency of the movement of goods with better routing and scheduling capabilities.
Moreover, IoT devices and real-time data analytics allow for greater transparency and control over the supply chain, making it possible to predict potential disruptions and take action before they extend lead times.
Adopting Agile Practices
Agile practices, borrowed from the software development realm, promote flexibility and adaptability in logistics operations.
An agile supply chain can quickly respond to changes in demand or supply conditions without increasing lead times.
This involves having flexible contracts with suppliers, responsive logistics strategies, and backup solutions to mitigate potential issues.
Shorter sprints in procurement and continuous feedback loops with stakeholders ensure that any part of the supply chain can quickly adapt to unforeseen changes, thus maintaining short lead times.
Forecasting and Demand Planning
Effective forecasting and demand planning are essential to minimizing lead times.
Accurate demand forecasting allows purchasing teams to plan their procurement activities more effectively, ensuring that the right quantities are ordered and that production is scheduled correctly.
Advanced analytics and demand planning tools can predict trends and potential spikes in demand, allowing for proactivity rather than reactivity.
This approach enables a smoother supply chain flow and reduces the likelihood of stockouts or overstock situations, both of which can lengthen lead times.
Conclusion
Reducing lead times is a multifaceted challenge requiring coordination across various segments of the supply chain.
By implementing reform strategies such as streamlining supply chain processes, adopting just-in-time inventory, enhancing transportation efficiency, and leveraging advanced technology, logistics operations can become more efficient and responsive.
Purchasing personnel must be proactive in adopting these strategies and work towards forging strong relationships with suppliers and utilizing data-driven insights to remain competitive in an increasingly fast-paced market.
Shortened lead times not only boost customer satisfaction but also drive operational efficiency and cost savings.
資料ダウンロード
QCD調達購買管理クラウド「newji」は、調達購買部門で必要なQCD管理全てを備えた、現場特化型兼クラウド型の今世紀最高の購買管理システムとなります。
ユーザー登録
調達購買業務の効率化だけでなく、システムを導入することで、コスト削減や製品・資材のステータス可視化のほか、属人化していた購買情報の共有化による内部不正防止や統制にも役立ちます。
NEWJI DX
製造業に特化したデジタルトランスフォーメーション(DX)の実現を目指す請負開発型のコンサルティングサービスです。AI、iPaaS、および先端の技術を駆使して、製造プロセスの効率化、業務効率化、チームワーク強化、コスト削減、品質向上を実現します。このサービスは、製造業の課題を深く理解し、それに対する最適なデジタルソリューションを提供することで、企業が持続的な成長とイノベーションを達成できるようサポートします。
オンライン講座
製造業、主に購買・調達部門にお勤めの方々に向けた情報を配信しております。
新任の方やベテランの方、管理職を対象とした幅広いコンテンツをご用意しております。
お問い合わせ
コストダウンが利益に直結する術だと理解していても、なかなか前に進めることができない状況。そんな時は、newjiのコストダウン自動化機能で大きく利益貢献しよう!
(Β版非公開)