- お役立ち記事
- Examples of mechanical seal failures, countermeasures, and prevention measures
月間76,176名の
製造業ご担当者様が閲覧しています*
*2025年3月31日現在のGoogle Analyticsのデータより
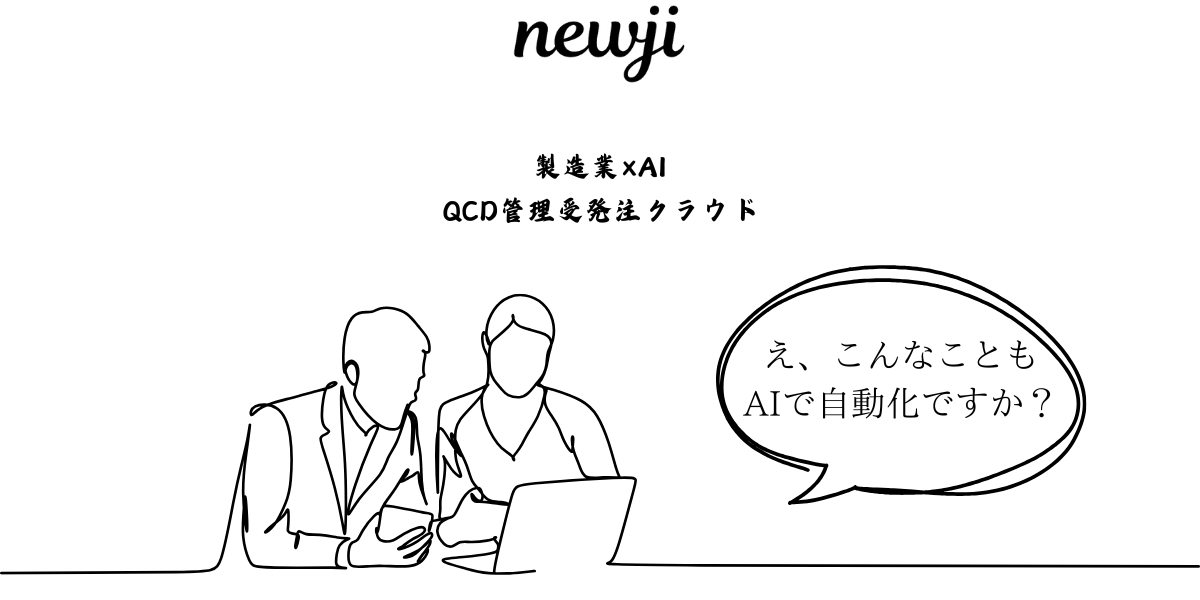
Examples of mechanical seal failures, countermeasures, and prevention measures
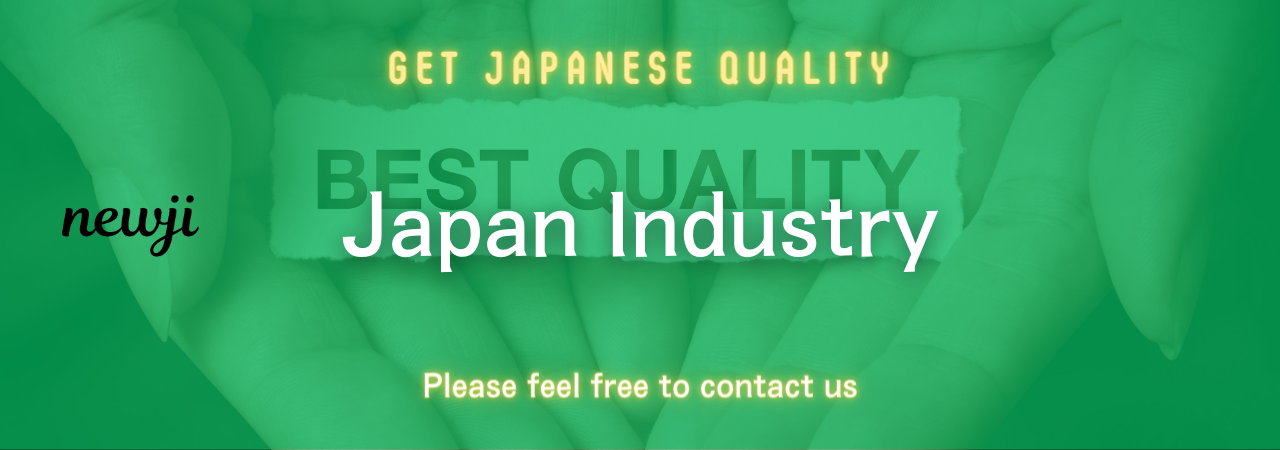
目次
Understanding Mechanical Seal Failures
Mechanical seals are an integral part of various industrial systems, playing a crucial role in preventing fluid leakage between rotating and stationary components.
Despite their importance, mechanical seal failures are not uncommon and can lead to significant downtime and costly repairs.
Recognizing the causes of these failures and implementing effective countermeasures can significantly enhance the longevity and reliability of mechanical systems.
Common Causes of Mechanical Seal Failures
Mechanical seal failures can be attributed to several factors.
Understanding these common causes is the first step in developing solutions to prevent them.
1. **Misalignment:** One of the primary causes of seal failure is misalignment between the rotating and stationary components.
This misalignment can cause uneven wear and tear on the seal, leading to premature failure.
2. **Improper Installation:** Installation errors, such as incorrect placement of the seal, can compromise its integrity.
A mechanical seal must be installed according to the manufacturer’s specifications to function effectively.
3. **Excessive Vibration:** Machines that experience high levels of vibration can cause degradation of the seal material.
Over time, this can result in cracks and breaks, leading to failure.
4. **Inadequate Lubrication:** Mechanical seals require proper lubrication to minimize friction and wear.
Inadequate lubrication or the use of inappropriate lubricants can lead to increased friction, resulting in seal damage.
5. **High Temperatures:** Excessive heat can cause thermal expansion of the seal materials, altering their physical properties.
This can lead to loss of sealing ability and mechanical seal failure.
Countermeasures for Mechanical Seal Failures
To effectively tackle mechanical seal failures, it is important to implement strategic countermeasures targeting the identified causes.
Alignment Checks
Regularly checking and maintaining the alignment of machine components can prevent misalignment-related failures.
Using precision alignment tools and techniques ensures the seals are properly engaged, reducing wear and tear.
Proper Installation Practices
It is crucial to follow the manufacturer’s guidelines during seal installation.
Proper training of maintenance personnel can help prevent installation errors.
Additionally, using the right tools and ensuring a clean environment can enhance the likelihood of a successful seal installation.
Minimizing Vibration
Reducing machine vibration is essential in prolonging the life of mechanical seals.
This can be achieved by balancing rotating parts, installing vibration dampeners, and conducting regular maintenance checks to ensure all components function smoothly.
Ensuring Adequate Lubrication
Select the right lubrication for your mechanical seals and ensure it is applied regularly, as per the maintenance schedule.
Routine checks and timely replacement of lubricants help keep friction in control, preventing seal damage.
Temperature Control
Monitoring and regulating system temperatures can prevent heat-related failures.
Implement cooling systems, such as heat exchangers, and use temperature-resistant materials to maintain suitable operating conditions for the seals.
Prevention Measures for Long-Term Reliability
Prevention measures are essential for ensuring the long-term reliability of mechanical seals.
Integrating a proactive maintenance and monitoring strategy can help prevent potential failures before they occur.
Regular Maintenance Schedule
Establish a regular maintenance schedule to inspect and maintain mechanical seals and their associated components.
Routine inspections help identify issues early, allowing for timely interventions that can prevent sudden failures.
Implementing Condition Monitoring
Advances in technology enable the implementation of condition monitoring systems that provide real-time data on seal health.
Sensors can detect changes in vibration, temperature, and pressure, alerting operators to potential problems before they result in failure.
Training and Support
Provide regular training for maintenance personnel to keep them updated on the latest seal technologies and installation practices.
Enhanced skills in diagnosing and addressing seal issues promptly contribute to overall system reliability.
Utilizing High-Quality Seals
Invest in high-quality mechanical seals designed for the specific requirements of your application.
Opting for seals with enhanced properties, such as higher temperature and chemical resistance, can help withstand challenging operating conditions.
Mechanical seal failures can significantly impact the efficiency and productivity of industrial operations.
Identifying the causes and implementing effective countermeasures, as well as preventive strategies, can help achieve longer service life and reliability.
By investing in regular maintenance, monitoring systems, and quality components, companies can minimize failures and ensure smooth operation of their mechanical systems.
資料ダウンロード
QCD管理受発注クラウド「newji」は、受発注部門で必要なQCD管理全てを備えた、現場特化型兼クラウド型の今世紀最高の受発注管理システムとなります。
ユーザー登録
受発注業務の効率化だけでなく、システムを導入することで、コスト削減や製品・資材のステータス可視化のほか、属人化していた受発注情報の共有化による内部不正防止や統制にも役立ちます。
NEWJI DX
製造業に特化したデジタルトランスフォーメーション(DX)の実現を目指す請負開発型のコンサルティングサービスです。AI、iPaaS、および先端の技術を駆使して、製造プロセスの効率化、業務効率化、チームワーク強化、コスト削減、品質向上を実現します。このサービスは、製造業の課題を深く理解し、それに対する最適なデジタルソリューションを提供することで、企業が持続的な成長とイノベーションを達成できるようサポートします。
製造業ニュース解説
製造業、主に購買・調達部門にお勤めの方々に向けた情報を配信しております。
新任の方やベテランの方、管理職を対象とした幅広いコンテンツをご用意しております。
お問い合わせ
コストダウンが利益に直結する術だと理解していても、なかなか前に進めることができない状況。そんな時は、newjiのコストダウン自動化機能で大きく利益貢献しよう!
(β版非公開)