- お役立ち記事
- Examples of resolving factory labor shortages through process improvement
Examples of resolving factory labor shortages through process improvement
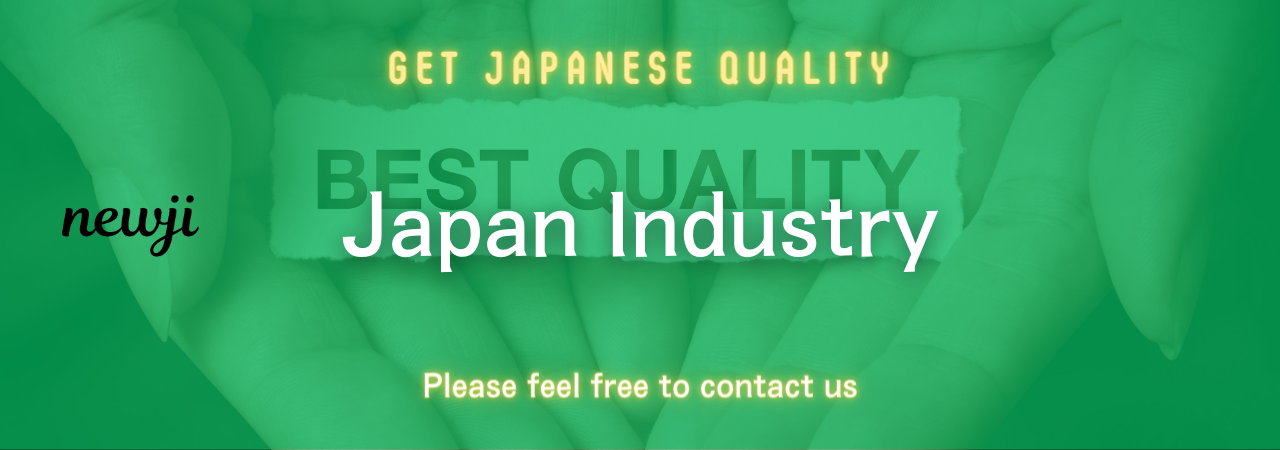
目次
Understanding the Factory Labor Shortage
Factory labor shortages have become a pressing issue in recent times.
As industries expand and demand for manufactured goods increases, factories are struggling to find enough workers to meet production needs.
Several factors contribute to this shortage, including an aging workforce, a lack of new skilled workers entering the field, and the increasing complexity of modern manufacturing processes.
To address these challenges, businesses are turning to process improvements as a solution.
These improvements aim to enhance productivity and efficiency, thereby reducing the dependency on human labor.
Identifying Process Improvement Opportunities
The first step in resolving labor shortages through process improvement is identifying areas within the factory where improvements can be made.
This involves a thorough analysis of the current manufacturing processes to pinpoint bottlenecks or inefficiencies.
By understanding where these issues lie, factories can develop targeted solutions that address specific problems.
The most common areas for process improvements include workflow optimization, machinery upgrades, and employee training.
Workflow Optimization
One effective strategy for improving factory processes is workflow optimization.
This involves reevaluating the layout and flow of work within the factory to ensure that tasks are carried out in the most efficient manner possible.
By rearranging workstations, streamlining task sequences, and eliminating unnecessary steps, factories can significantly increase productivity.
Moreover, better workflow management ensures that workers are not overburdened with physical tasks, which helps in retaining existing staff and attracting new employees.
Machinery and Technology Upgrades
Another key aspect of process improvement is investing in machinery and technology upgrades.
With advancements in tech, factories have access to state-of-the-art equipment that can perform tasks faster and more accurately than human workers.
For example, robotics and automation technologies can take over repetitive and labor-intensive tasks, allowing human workers to focus on more complex and engaging responsibilities.
Upgraded machinery also tends to break down less frequently, reducing downtime and boosting overall production output.
Employee Training and Skill Development
Investing in the skill development of existing employees is a crucial part of improving factory processes.
By providing comprehensive training programs, factories can ensure that their workforce is equipped with the latest skills and knowledge needed to operate new machinery and technologies effectively.
Training also helps in reducing errors and improving the quality of output, thereby increasing overall efficiency.
Real-World Examples of Process Improvement
Numerous factories have successfully addressed labor shortages through process improvements.
One notable example is a large automotive component manufacturer that faced significant workforce challenges.
By implementing automated assembly lines and enhancing their logistics through better inventory management software, they managed to maintain high production levels without hiring additional staff.
Additionally, they introduced flexible work schedules and upskilled their current workforce, enabling them to handle more complex tasks and maintain job satisfaction.
Another example is a clothing manufacturer that turned to lean manufacturing principles to optimize their processes.
They identified redundant steps in their production line and cut them out, leading to a smoother workflow and quicker production times.
Furthermore, they invested in cutting-edge textile machinery, which decreased the manual labor needed in their operations.
These changes not only improved efficiency but also reduced costs, allowing the company to better compete in a tight labor market.
Future of Factory Labor and Process Improvement
The ongoing evolution of technology means that process improvements in factories will continue to evolve.
Future trends point towards increased automation, data-driven decision-making, and the integration of artificial intelligence in manufacturing processes.
These advancements hold the promise of further alleviating labor shortages by reducing the demand for low-skilled labor while increasing the need for skilled workers who can manage and maintain advanced technologies.
It is essential for factories to stay ahead of these trends by continuously assessing their processes and being willing to adopt new technologies.
By doing so, they can ensure that they remain competitive and are able to address labor shortages effectively.
Conclusion
In conclusion, the labor shortages in factories pose a significant challenge to the manufacturing industry.
However, by focusing on process improvements, businesses can significantly mitigate these shortages and enhance productivity.
Through workflow optimization, machinery upgrades, and employee training, factories can operate more efficiently and with fewer human resources.
Real-world examples demonstrate the effectiveness of these strategies, making them a viable solution for factories facing labor challenges.
As technology continues to advance, it’s crucial for businesses to adapt and innovate, ensuring they can navigate the evolving landscape of factory labor demands.
資料ダウンロード
QCD調達購買管理クラウド「newji」は、調達購買部門で必要なQCD管理全てを備えた、現場特化型兼クラウド型の今世紀最高の購買管理システムとなります。
ユーザー登録
調達購買業務の効率化だけでなく、システムを導入することで、コスト削減や製品・資材のステータス可視化のほか、属人化していた購買情報の共有化による内部不正防止や統制にも役立ちます。
NEWJI DX
製造業に特化したデジタルトランスフォーメーション(DX)の実現を目指す請負開発型のコンサルティングサービスです。AI、iPaaS、および先端の技術を駆使して、製造プロセスの効率化、業務効率化、チームワーク強化、コスト削減、品質向上を実現します。このサービスは、製造業の課題を深く理解し、それに対する最適なデジタルソリューションを提供することで、企業が持続的な成長とイノベーションを達成できるようサポートします。
オンライン講座
製造業、主に購買・調達部門にお勤めの方々に向けた情報を配信しております。
新任の方やベテランの方、管理職を対象とした幅広いコンテンツをご用意しております。
お問い合わせ
コストダウンが利益に直結する術だと理解していても、なかなか前に進めることができない状況。そんな時は、newjiのコストダウン自動化機能で大きく利益貢献しよう!
(Β版非公開)