- お役立ち記事
- Examples of strategic collaboration with logistics partners promoted by the purchasing department
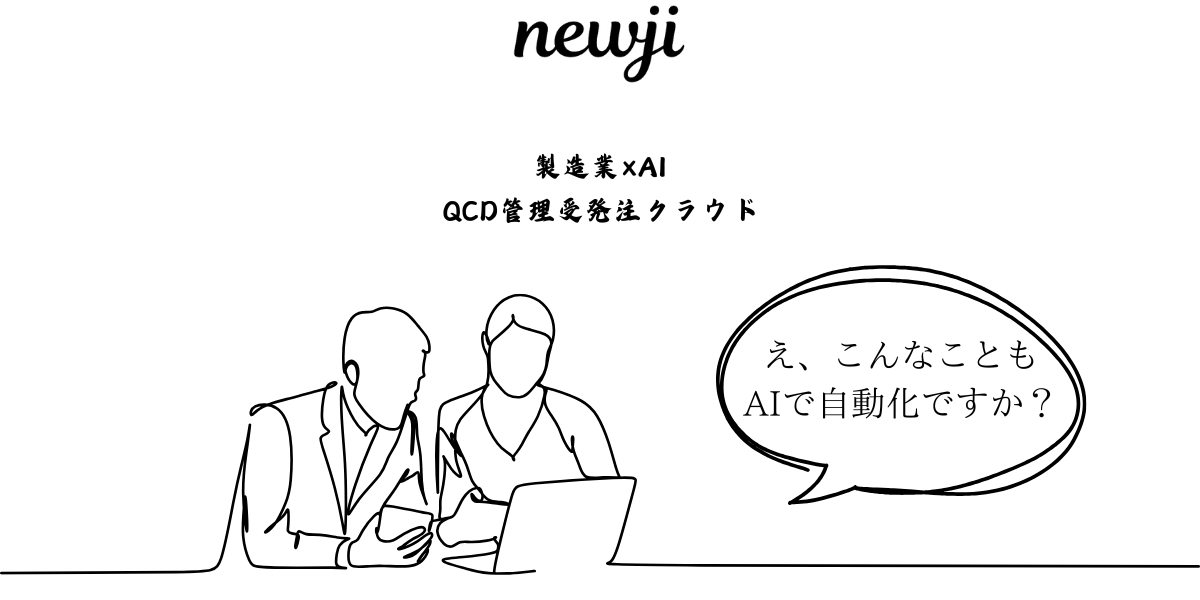
Examples of strategic collaboration with logistics partners promoted by the purchasing department
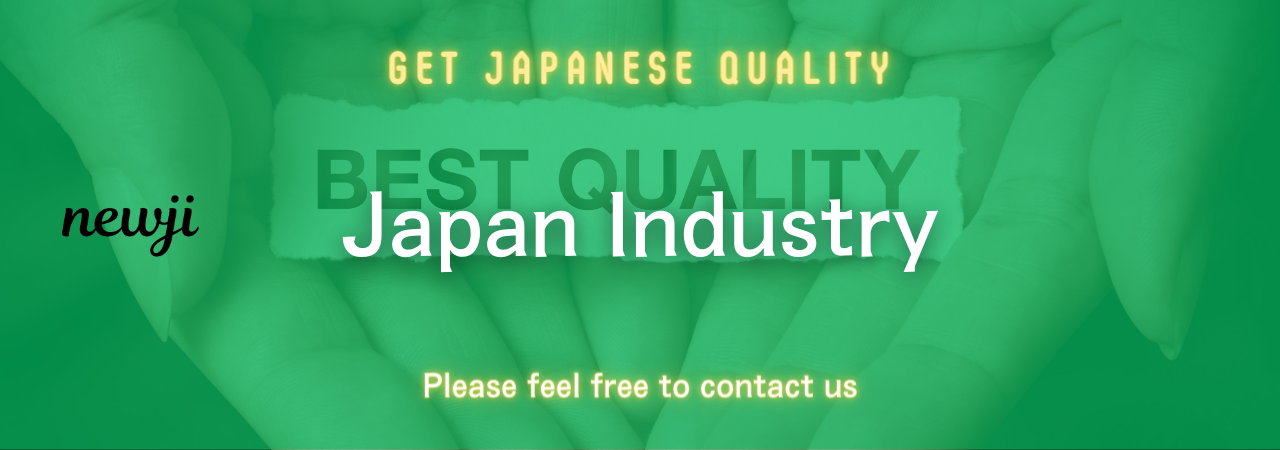
目次
Understanding Strategic Collaboration in Procurement
In today’s fast-paced business environment, companies are constantly seeking ways to enhance their efficiency and streamline operations.
One area ripe for improvement is in the relationship between the purchasing department and logistics partners.
Strategic collaboration with logistics partners is not just a trend; it’s a necessity for companies aiming to optimize their supply chain and reduce costs.
By fostering a collaborative relationship, businesses can ensure smoother operations, timely deliveries, and ultimately, a better bottom line.
In this article, we will explore examples of how strategic partnerships with logistics providers can be effectively implemented by purchasing departments.
The Need for Strategic Collaboration
The purchasing department plays a crucial role in a company’s supply chain.
It is responsible for procuring goods and services that a business needs to operate.
As the bridge between suppliers and other company departments, the purchasing team directly impacts the timeliness and cost-effectiveness of operations.
However, sourcing and procurement do not occur in isolation.
They are deeply intertwined with the logistics of getting goods from suppliers to their final destination.
This makes collaborating with logistics partners strategically essential.
By working closely with logistics providers, purchasing departments can gain insights into shipping trends, potential disruptions, and innovative transportation solutions.
Such collaborations can lead to improved decision-making and more efficient supply chain management.
Enhanced Connectivity through Technology
One powerful way to foster collaboration with logistics partners is through technology integration.
Today, technology solutions such as cloud-based platforms, Internet of Things (IoT), and data analytics enable real-time communication and tracking of shipments.
For instance, a synchronization between the purchasing department’s systems and those of logistics partners can provide instant updates on the status of shipments, inventory levels, and transportation costs.
This transparency facilitates more accurate forecasting and planning.
A clear example is the use of Electronic Data Interchange (EDI) or Application Programming Interfaces (APIs) to exchange procurement and shipping information seamlessly.
These technological tools allow businesses to reduce manual processes, minimize errors, and maintain real-time data flow, significantly improving collaboration efforts.
Joint Planning and Forecasting
Another effective strategy involves joint planning and forecasting between purchasing departments and logistics partners.
By working together to predict future demand, both parties can prepare for potential changes in the market.
Collaboration enables logistics providers to optimize routes and capacities, while purchasing departments can align orders with these capabilities.
For example, a company might plan its inventory deliveries during off-peak times to take advantage of lower shipping costs and reduced congestion, as advised by logistics partners.
Moreover, joint forecasting helps in developing contingency plans for unexpected events, such as supply chain disruptions due to natural disasters or economic shifts.
This helps in mitigating risks and avoiding costly delays.
Cost Optimization through Shared Resources
Strategic collaboration can also lead to shared resources, resulting in cost optimization.
This might include co-loading shipments with other companies using the same logistics provider to reduce transportation costs and carbon emissions.
Logistics partners often have valuable insights into optimizing load capacities and routes, and they can offer solutions for consolidating shipments.
By working together, purchasing departments can leverage these opportunities for cost savings.
Furthermore, partnerships might involve joint investment in infrastructure or technology that yields mutual benefits, such as shared warehouses or transportation hubs.
This not only reduces costs but also enhances service levels through improved logistics efficiency.
Improved Service Quality
Collaboration with logistics partners is fundamental in enhancing service quality.
Maintaining a strong relationship allows purchasing departments to adapt quickly to changing customer needs and expectations.
With better communication and collaboration, companies can ensure that their products are delivered on time and in optimal condition.
Logistics providers can offer insights into packaging improvements or alternative delivery methods that increase customer satisfaction.
A collaborative approach also facilitates quicker resolution of issues that arise during transportation, as both partners are aligned in their objectives and can work towards a swift and effective solution.
Navigating Challenges in Collaboration
Despite the evident benefits, strategic collaboration is not without its challenges.
Different organizational cultures, communication styles, and priorities can pose obstacles to building strong partnerships.
To address these challenges, businesses must focus on building trust and maintaining open communication.
Establishing clear expectations and roles for each partner is critical for seamless operations.
Moreover, setting up regular meetings and performance reviews helps to address issues proactively and ensures that both parties remain aligned in their goals.
By prioritizing collaboration, purchasing departments can foster successful partnerships that drive business growth.
Conclusion
Strategic collaboration between purchasing departments and logistics partners is a key driver of supply chain efficiency and cost-effectiveness.
Through technology integration, joint planning, shared resources, and improved service quality, these partnerships can lead to significant benefits for businesses.
While challenges exist, the positive outcomes far outweigh the initial hurdles.
Embracing strategic collaboration is essential for companies looking to strengthen their supply chain operations and achieve a competitive edge in today’s dynamic market.
資料ダウンロード
QCD調達購買管理クラウド「newji」は、調達購買部門で必要なQCD管理全てを備えた、現場特化型兼クラウド型の今世紀最高の購買管理システムとなります。
ユーザー登録
調達購買業務の効率化だけでなく、システムを導入することで、コスト削減や製品・資材のステータス可視化のほか、属人化していた購買情報の共有化による内部不正防止や統制にも役立ちます。
NEWJI DX
製造業に特化したデジタルトランスフォーメーション(DX)の実現を目指す請負開発型のコンサルティングサービスです。AI、iPaaS、および先端の技術を駆使して、製造プロセスの効率化、業務効率化、チームワーク強化、コスト削減、品質向上を実現します。このサービスは、製造業の課題を深く理解し、それに対する最適なデジタルソリューションを提供することで、企業が持続的な成長とイノベーションを達成できるようサポートします。
オンライン講座
製造業、主に購買・調達部門にお勤めの方々に向けた情報を配信しております。
新任の方やベテランの方、管理職を対象とした幅広いコンテンツをご用意しております。
お問い合わせ
コストダウンが利益に直結する術だと理解していても、なかなか前に進めることができない状況。そんな時は、newjiのコストダウン自動化機能で大きく利益貢献しよう!
(Β版非公開)