- お役立ち記事
- Examples of successful multi-site procurement in the manufacturing industry promoted by the purchasing department
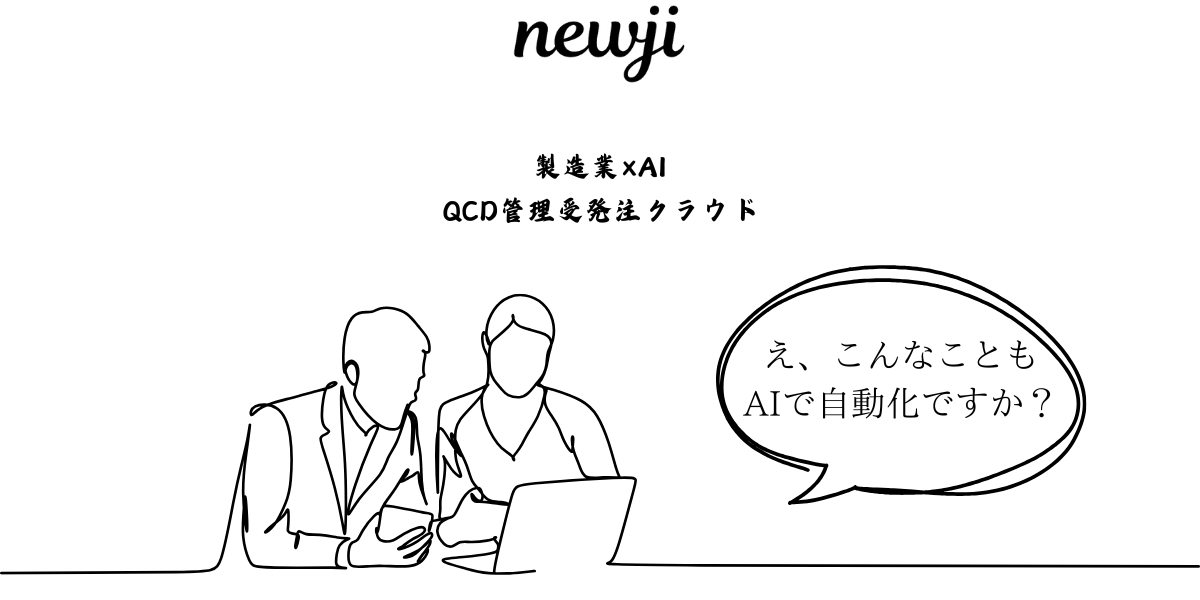
Examples of successful multi-site procurement in the manufacturing industry promoted by the purchasing department
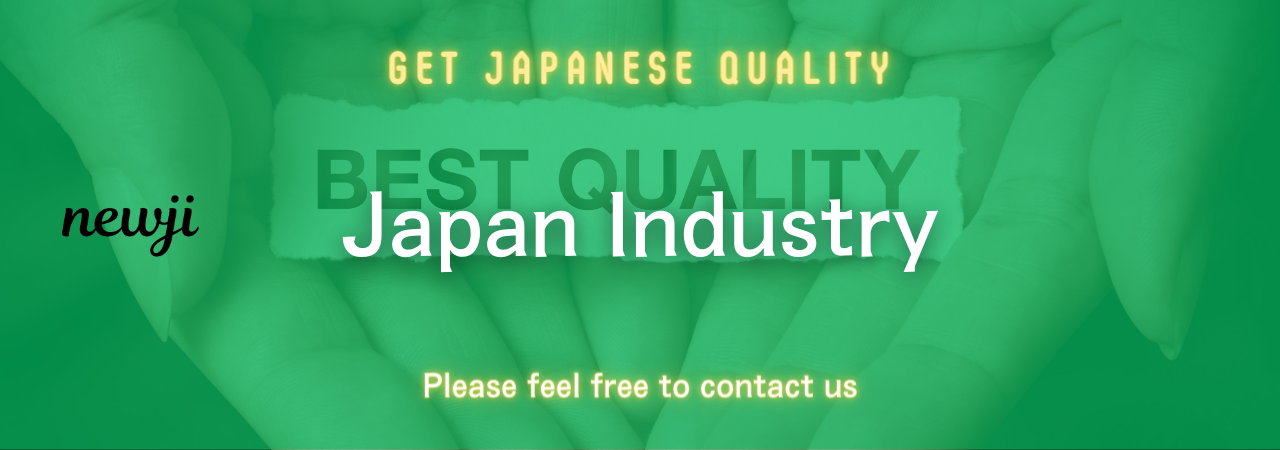
目次
Understanding Multi-Site Procurement
In today’s highly competitive manufacturing industry, efficiency and cost-effectiveness are paramount.
One of the strategic methods driving these objectives is multi-site procurement.
But what exactly does this involve?
Multi-site procurement refers to the practice where a company sources materials, components, or services from multiple locations.
This strategy is particularly effective in achieving cost savings, flexibility, and risk management.
By diversifying the sources of procurement across various sites, companies can enhance their ability to withstand supply chain disruptions and capitalize on regional advantages.
The Role of the Purchasing Department
Within a manufacturing company, the purchasing department plays a critical role in managing multi-site procurement.
They are responsible for identifying potential suppliers, negotiating contracts, and ensuring the timely delivery of materials.
An efficient purchasing department can leverage multi-site procurement to not only cut costs but also improve the overall quality of procurement.
By maintaining a network of reliable suppliers across different geographic locations, the purchasing department can quickly respond to market changes and demand fluctuations.
Additionally, they can negotiate better terms due to increased purchasing power and a broader supplier base.
Case Study 1: Automotive Manufacturer
Let’s take a look at how a major automotive manufacturer successfully implemented multi-site procurement.
Facing rising costs and supply chain disruptions, the company decided to diversify its supply base.
The purchasing department identified potential suppliers in regions where labor and material costs were lower.
By procuring components from multiple sites, they significantly reduced costs and improved their supply chain resilience.
Moreover, the department focused on establishing strong relationships with these suppliers.
Regular communication and transparent negotiations allowed the company to manage logistics efficiently, reducing lead times dramatically.
This approach not only helped the automotive manufacturer reduce expenses but also enhanced its ability to meet production targets on time.
Case Study 2: Electronics Industry
Another successful multi-site procurement example comes from within the electronics industry.
A leading electronics manufacturer was struggling with single-source dependency and increasing supply chain bottlenecks.
To tackle these challenges, the purchasing department reevaluated its supply chain strategy.
They divided their procurement needs across several qualified suppliers in different countries.
This diversification minimized risks associated with political instability and natural disasters.
The purchasing department also incorporated advanced procurement technologies, like AI-driven analytics, to forecast demand accurately and optimize inventory levels.
As a result, the company maintained a steady production flow, improved its supply efficiency, and cut down on factory downtimes.
Benefits of Multi-Site Procurement
The advantages of multi-site procurement are numerous.
First and foremost, diversifying suppliers reduces reliance on a single source, which is critical in mitigating risks and ensuring a stable supply chain.
This enhanced resilience makes companies less vulnerable to local disruptions, such as strikes, natural disasters, or political turmoil.
Secondly, multi-site procurement allows companies to tap into the unique strengths of different regions.
For instance, one site might offer lower labor costs, while another might provide higher-quality materials.
By strategically selecting suppliers, companies can achieve cost savings without compromising on quality.
Moreover, multi-site procurement fosters competition among suppliers.
Suppliers are more likely to offer competitive pricing and innovative solutions when they know companies have alternatives.
In addition, it allows manufacturers to adapt to changing market demands swiftly.
With an array of suppliers at their disposal, companies can quickly scale up or down their production based on current needs.
Challenges of Implementing Multi-Site Procurement
While multi-site procurement offers significant benefits, it is not without its challenges.
Coordinating multiple suppliers requires comprehensive planning and logistics management.
Companies must ensure that communication channels are robust and clear to avoid misunderstandings that could lead to order errors or delays.
Quality control is another potential issue in multi-site procurement.
Maintaining consistent quality standards across different suppliers can be challenging.
Regular audits and quality checks are essential to ensure that all products meet the required standards.
Additionally, varying regulations and trade policies between regions can complicate procurement processes.
Companies need to navigate these regulatory environments carefully to avoid legal issues or unexpected costs.
Conclusion
In conclusion, multi-site procurement is a powerful strategy for manufacturing companies seeking to enhance their efficiency, reduce costs, and improve supply chain resilience.
By leveraging the capabilities of a skilled purchasing department, companies can maximize the benefits of diversifying their sourcing strategies.
While challenges exist, careful planning, clear communication, and strong supplier relationships can overcome these hurdles.
Through successful multi-site procurement, manufacturing companies not only sustain their competitive edge but also prepare themselves robustly against market fluctuations and disruptions.
For any manufacturing company aiming at long-term success, multi-site procurement stands as a cornerstone of their supply chain strategy.
資料ダウンロード
QCD調達購買管理クラウド「newji」は、調達購買部門で必要なQCD管理全てを備えた、現場特化型兼クラウド型の今世紀最高の購買管理システムとなります。
ユーザー登録
調達購買業務の効率化だけでなく、システムを導入することで、コスト削減や製品・資材のステータス可視化のほか、属人化していた購買情報の共有化による内部不正防止や統制にも役立ちます。
NEWJI DX
製造業に特化したデジタルトランスフォーメーション(DX)の実現を目指す請負開発型のコンサルティングサービスです。AI、iPaaS、および先端の技術を駆使して、製造プロセスの効率化、業務効率化、チームワーク強化、コスト削減、品質向上を実現します。このサービスは、製造業の課題を深く理解し、それに対する最適なデジタルソリューションを提供することで、企業が持続的な成長とイノベーションを達成できるようサポートします。
オンライン講座
製造業、主に購買・調達部門にお勤めの方々に向けた情報を配信しております。
新任の方やベテランの方、管理職を対象とした幅広いコンテンツをご用意しております。
お問い合わせ
コストダウンが利益に直結する術だと理解していても、なかなか前に進めることができない状況。そんな時は、newjiのコストダウン自動化機能で大きく利益貢献しよう!
(Β版非公開)