- お役立ち記事
- Examples of using monitoring tools to improve equipment utilization rate
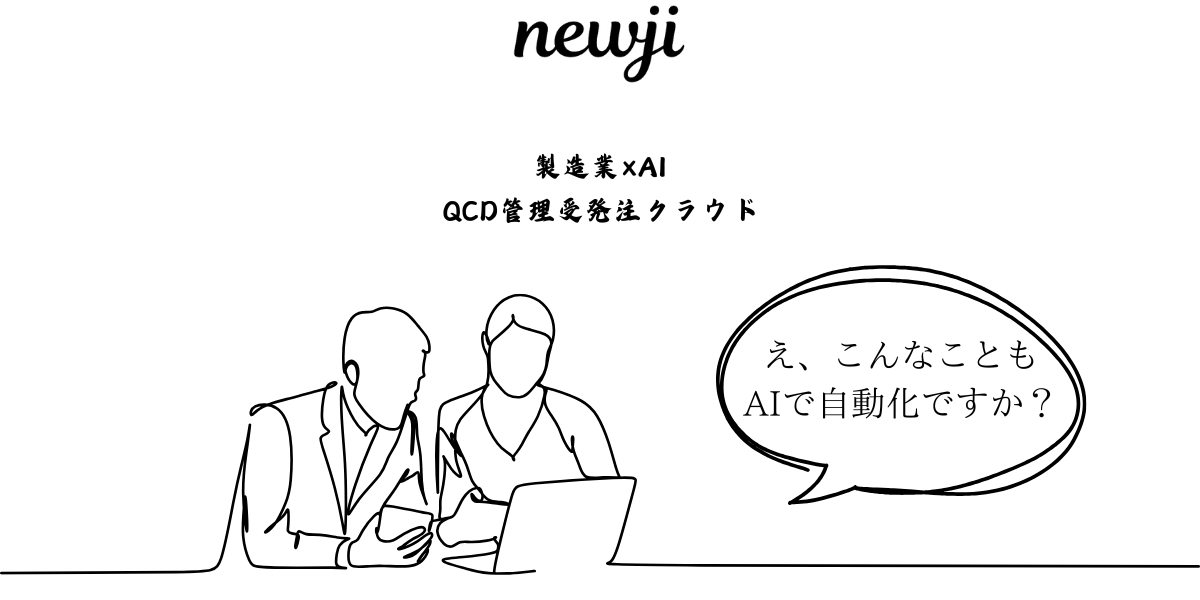
Examples of using monitoring tools to improve equipment utilization rate
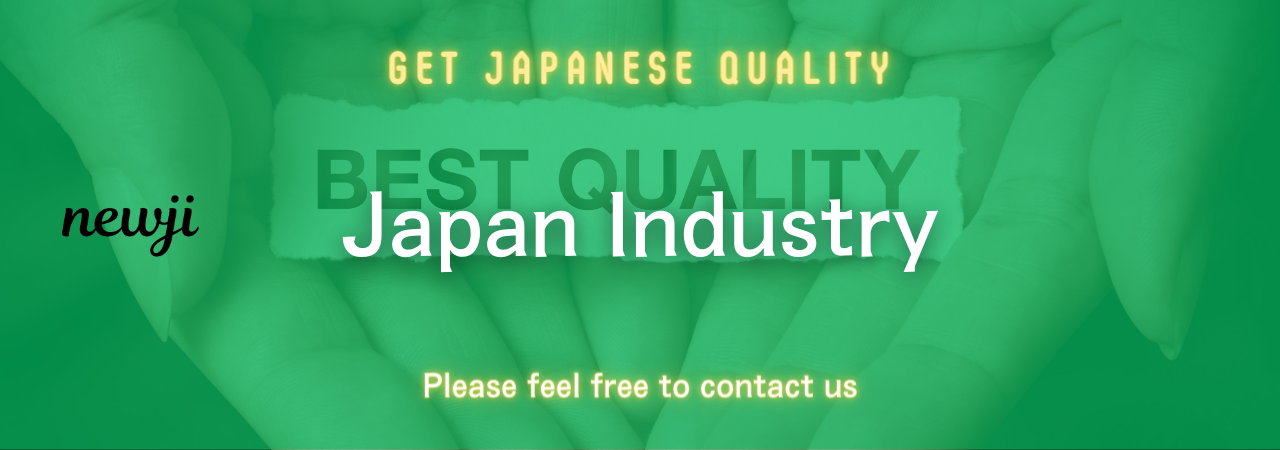
目次
Understanding Equipment Utilization Rate
In today’s competitive industrial landscape, maximizing efficiency is crucial for maintaining profitability and staying ahead of the curve.
One key metric that businesses often track to gauge operational efficiency is the equipment utilization rate.
This rate measures how effectively a company is using its equipment compared to its capacity.
The equipment utilization rate is calculated by dividing the actual operating time by the total available time.
For any business heavily reliant on machinery, maximizing this rate means getting the most output from investments in equipment.
The Role of Monitoring Tools
Monitoring tools have become invaluable in enhancing the equipment utilization rate.
These tools leverage advanced technologies such as IoT, machine learning, and data analytics to provide detailed insights into equipment performance.
By using these technologies, businesses can track a range of metrics, including operational efficiency, maintenance needs, and downtime incidents.
Monitoring tools capture real-time data, which allows managers to make informed decisions quickly.
This real-time detection of inefficiencies leads directly to increased uptime, as issues are identified and resolved before escalating into major problems.
Real-Time Data Collection and Analysis
From the moment equipment is switched on, monitoring tools start collecting data.
This data is then analyzed to provide insights into usage patterns and efficiency levels.
Real-time data collection means that instances of underperformance can be immediately highlighted.
For example, if a machine is running below expected efficiency, alerts can be set up to notify maintenance teams to take corrective actions.
This proactive approach ensures that the equipment is used at its optimal level, thereby improving the utilization rate.
Predictive Maintenance
One of the greatest advantages of using monitoring tools is the capability for predictive maintenance.
These tools help predict when a piece of equipment is likely to fail or perform below par.
Instead of reactive maintenance—fixing what is broken after it fails—companies can perform maintenance activities just before a failure is predicted.
This approach reduces unplanned downtime and extends the lifespan of equipment.
As a consequence, equipment can be kept in operation longer and more predictably, enhancing the overall utilization rate.
Examples of Monitoring Tools
Monitoring solutions come in various forms, designed to suit different industrial needs.
Below are some popular examples:
IoT Sensors
Internet of Things (IoT) sensors are ubiquitous in modern warehouses and manufacturing plants.
These sensors are attached to equipment to collect data on various parameters like temperature, vibration, and operational speed.
IoT sensors enable the continuous monitoring of equipment conditions.
By gathering and analyzing this data, companies can gain insights into how often, and how well, their equipment is used.
Supervisory Control and Data Acquisition (SCADA) Systems
SCADA systems are another effective tool for monitoring industrial processes.
These systems gather real-time data and provide visualization to alert operators to deviations in process conditions.
Using SCADA systems, managers can oversee entire operations down to specific pieces of equipment.
By doing so, they can quickly detect inefficiencies that reduce utilization, such as unusual delays or sub-optimal operating sequences.
Machine Learning-Based Predictive Analytics
Machine learning algorithms can analyze historical data to find patterns that precede equipment failures or drops in performance.
These algorithms grow smarter over time, providing increasingly accurate predictions.
By applying predictive analytics, businesses can implement preventive measures, effectively closing the gap between potential performance and actual output.
Case Studies and Success Stories
Let’s examine a few real-world examples that illustrate how effective monitoring tools can significantly improve equipment utilization rates.
Automotive Manufacturer
A leading automotive manufacturer implemented advanced monitoring tools across its assembly lines.
By relying on IoT sensors and real-time data analytics, the company was able to reduce unplanned downtime by 15%.
This improvement directly increased the utilization rate, allowing the manufacturer to meet its production targets more effectively and at a lower cost.
Food Processing Plant
A food processing plant facing frequent bottlenecks adopted machine learning-based predictive analytics.
Monitoring tools helped predict equipment failures with an 85% accuracy rate.
Maintenance schedules were optimized, leading to a 20% boost in utilization rates by ensuring machinery operated at peak performance with minimal disruptions.
Textile Industry
A textile company integrated SCADA systems into its operations to monitor power consumption and machine health.
Through detailed data insights, the company identified non-essential equipment that was routinely powered, leading to wasted energy and reduced utilization.
Reassessing machine schedules based on the monitoring data, the company improved its equipment utilization rate by 25%, reducing overhead costs and enhancing productivity.
Conclusion
Monitoring tools provide businesses with the data needed to make informed decisions that directly affect equipment utilization rates.
From IoT sensors to advanced predictive analytics, these tools empower managers with insights that improve efficiency and productivity.
By embracing these technologies, companies can extend equipment lifespans, reduce downtime, and maximize their investment value.
With constant advancements in monitoring technology, the potential for improving utilization rates is only set to increase, offering greater opportunities for businesses to optimize their operations.
資料ダウンロード
QCD調達購買管理クラウド「newji」は、調達購買部門で必要なQCD管理全てを備えた、現場特化型兼クラウド型の今世紀最高の購買管理システムとなります。
ユーザー登録
調達購買業務の効率化だけでなく、システムを導入することで、コスト削減や製品・資材のステータス可視化のほか、属人化していた購買情報の共有化による内部不正防止や統制にも役立ちます。
NEWJI DX
製造業に特化したデジタルトランスフォーメーション(DX)の実現を目指す請負開発型のコンサルティングサービスです。AI、iPaaS、および先端の技術を駆使して、製造プロセスの効率化、業務効率化、チームワーク強化、コスト削減、品質向上を実現します。このサービスは、製造業の課題を深く理解し、それに対する最適なデジタルソリューションを提供することで、企業が持続的な成長とイノベーションを達成できるようサポートします。
オンライン講座
製造業、主に購買・調達部門にお勤めの方々に向けた情報を配信しております。
新任の方やベテランの方、管理職を対象とした幅広いコンテンツをご用意しております。
お問い合わせ
コストダウンが利益に直結する術だと理解していても、なかなか前に進めることができない状況。そんな時は、newjiのコストダウン自動化機能で大きく利益貢献しよう!
(Β版非公開)