- お役立ち記事
- Explaining the Entire Process of Designing and Manufacturing Printed Circuit Boards
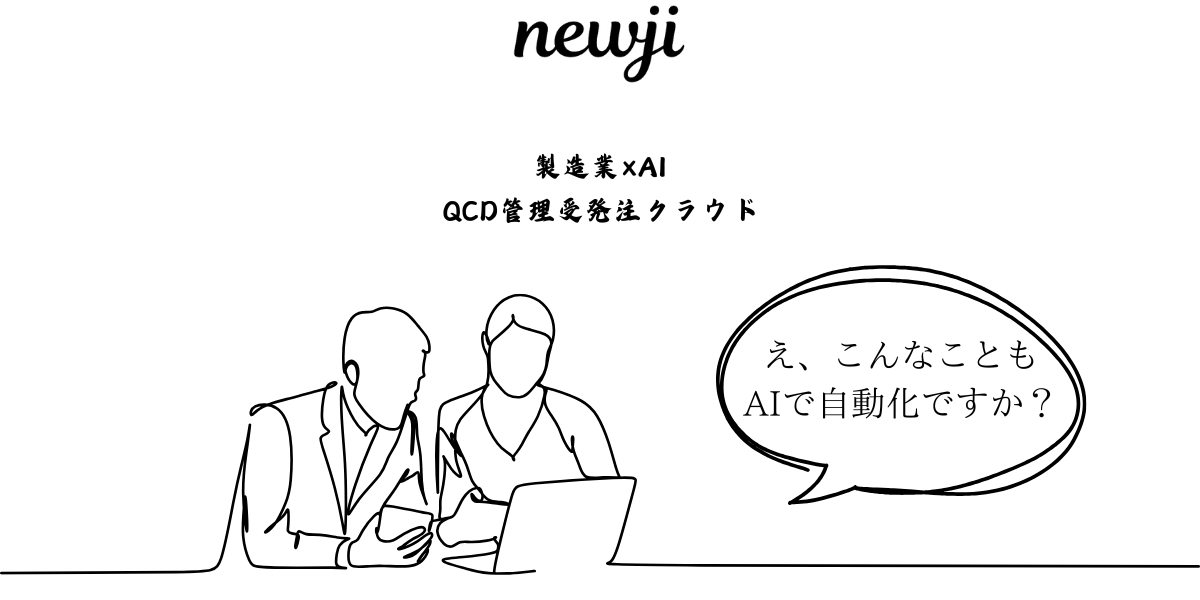
Explaining the Entire Process of Designing and Manufacturing Printed Circuit Boards
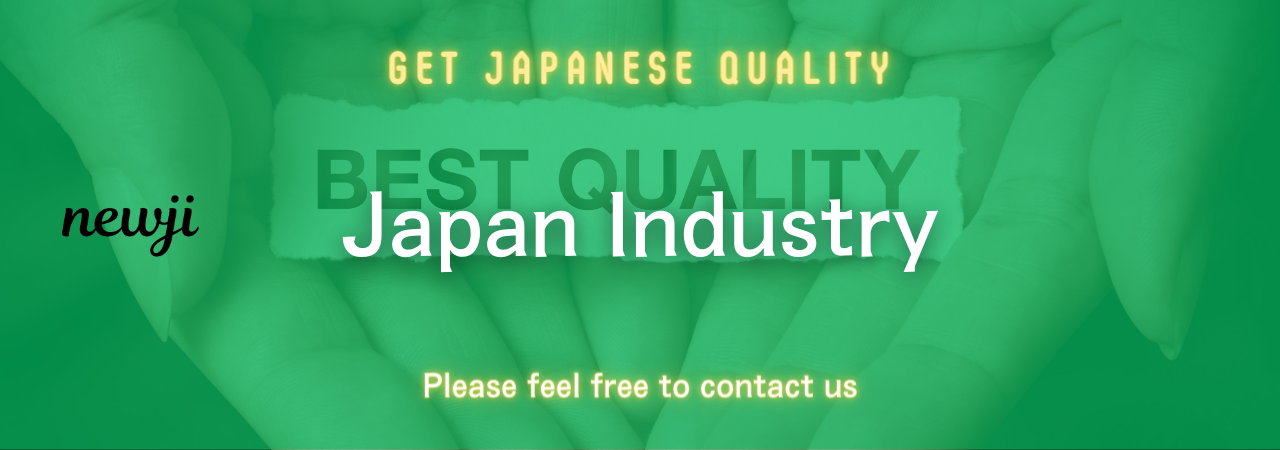
Designing and manufacturing printed circuit boards, or PCBs, involves several meticulous steps that transform an idea into a physical, operational board.
Understanding each stage is crucial for anyone interested in electronics and engineering.
Here’s a detailed guide to the entire process.
目次
Understanding What a PCB Is
Printed circuit boards are the backbone of most electronic devices.
They provide a platform to connect various electronic components, such as resistors, capacitors, and microchips, enabling them to communicate and function together.
PCBs are found in items ranging from simple electronic toys to complex computer systems.
Steps in Designing a PCB
1. Conceptualization and Schematic Design
The first step in designing a PCB is the conceptualization of the circuit.
Engineers and designers must understand the project’s requirements to create an initial schematic.
A schematic represents the circuitry and illustrates how the components will connect.
Software tools, like Eagle or KiCad, are often used at this stage, allowing designers to lay out the circuit logically and ensure all connections are correct.
2. Choosing the Components
Once the schematic is prepared, the next step is to select the electronic components.
Choosing the right components involves considering various factors such as function, size, and availability.
It is crucial to ensure that all the components fit the required specifications for the circuit to function properly.
Component selection impacts the PCB’s performance and reliability.
3. Designing the PCB Layout
The PCB layout design follows, where the schematic is translated into a physical design.
This involves placing the components on the board and routing the electrical connections between them.
Adequate spacing between components must be maintained to avoid short circuits and signal interference.
PCB Manufacturing Process
After the design process, the PCB moves to the manufacturing stage.
This phase involves several steps to turn the digital design into a tangible board.
1. Printing the PCB Design
The first manufacturing step is to print the PCB design onto the board material.
This is typically done using a special printer that transfers the design onto a copper-clad laminate.
The printed design acts as a guide for where the copper needs to remain and where it needs to be removed.
2. Etching
Etching is the process of removing excess copper from the board.
The printed circuit pattern protects the necessary copper while an acid bath or other chemical process removes the unwanted copper.
The result is a PCB with copper traces accurately representing the electrical circuits.
3. Drilling
Once the etching process is complete, the next step is drilling.
Holes are drilled into the board where components will be placed.
These holes are precisely positioned according to the design layout, ensuring components align correctly with the copper traces.
4. Plating and Solder Mask Application
The drilled holes are then plated with copper, allowing connections between different layers of the PCB if it is a multi-layer board.
After plating, a solder mask is applied to the PCB.
The solder mask is a protective layer that prevents solder bridging and protects the copper traces from environmental damage.
Generally, the solder mask is green, but other colors like red, blue, and yellow can also be used.
5. Silkscreen Application
The silkscreen is printed onto the PCB to provide labels and symbols.
It helps identify components, test points, and other important information, making assembly and troubleshooting easier.
This layer is usually white, allowing clear visibility against the solder mask.
6. Surface Finishing
Surface finishing is the final preparation step before assembling the components on the PCB.
This process involves coating the exposed copper areas with a finish that prevents oxidation and aids the soldering process.
Common finishes include HASL (Hot Air Solder Leveling), ENIG (Electroless Nickel Immersion Gold), and OSP (Organic Solderability Preservatives).
Assembling the PCB
After the PCB manufacturing is complete, the next step is to assemble the board with the selected components.
1. Component Placement
The first step in PCB assembly is placing the components onto the board.
This can be done manually for small batches or simple designs, or using automated machines for larger productions.
Automated placement machines, known as pick-and-place machines, accurately place components onto the board based on the design layout.
2. Soldering
Soldering is the process of permanently attaching the components to the PCB.
Several soldering techniques can be used depending on the complexity and requirements of the board.
The most common methods include reflow soldering, wave soldering, and hand soldering.
Reflow soldering is often used for surface-mount components, where solder paste is applied to the board, and the assembly is passed through an oven to melt and solidify the solder.
3. Inspection and Testing
Once the components are soldered, the assembled PCB undergoes inspection and testing to ensure it functions correctly.
Automated Optical Inspection (AOI) systems are commonly used to check for soldering defects, misplaced components, and other assembly issues.
Functional testing is also performed to verify that the PCB operates as intended.
Quality Control and Finalizing the PCB
After assembly and testing, the final step is quality control and implementation.
1. Quality Control
Quality control ensures that the PCB meets all specifications and requirements.
This process involves visual inspection and electrical testing to detect any issues that could impact the PCB’s performance.
High standards and precise tolerances are essential to deliver reliable and functional boards.
2. Final Packaging
Once the PCB passes all quality checks, it is ready for final packaging.
Depending on the end use, the PCB may be delivered as a standalone board or integrated into an electronic device.
Proper packaging protects the PCB from mechanical damage during shipping and handling.
The meticulous process of designing and manufacturing PCBs showcases the importance of precision and attention to detail in electronics.
From initial planning to final quality control, each step ensures the delivery of a functional and reliable product.
Understanding this intricate process can inspire inventors and engineers to explore and innovate within the world of electronics.
資料ダウンロード
QCD調達購買管理クラウド「newji」は、調達購買部門で必要なQCD管理全てを備えた、現場特化型兼クラウド型の今世紀最高の購買管理システムとなります。
ユーザー登録
調達購買業務の効率化だけでなく、システムを導入することで、コスト削減や製品・資材のステータス可視化のほか、属人化していた購買情報の共有化による内部不正防止や統制にも役立ちます。
NEWJI DX
製造業に特化したデジタルトランスフォーメーション(DX)の実現を目指す請負開発型のコンサルティングサービスです。AI、iPaaS、および先端の技術を駆使して、製造プロセスの効率化、業務効率化、チームワーク強化、コスト削減、品質向上を実現します。このサービスは、製造業の課題を深く理解し、それに対する最適なデジタルソリューションを提供することで、企業が持続的な成長とイノベーションを達成できるようサポートします。
オンライン講座
製造業、主に購買・調達部門にお勤めの方々に向けた情報を配信しております。
新任の方やベテランの方、管理職を対象とした幅広いコンテンツをご用意しております。
お問い合わせ
コストダウンが利益に直結する術だと理解していても、なかなか前に進めることができない状況。そんな時は、newjiのコストダウン自動化機能で大きく利益貢献しよう!
(Β版非公開)