- お役立ち記事
- Exploration and application examples of tube burner cracking sign detection technology
月間77,185名の
製造業ご担当者様が閲覧しています*
*2025年2月28日現在のGoogle Analyticsのデータより
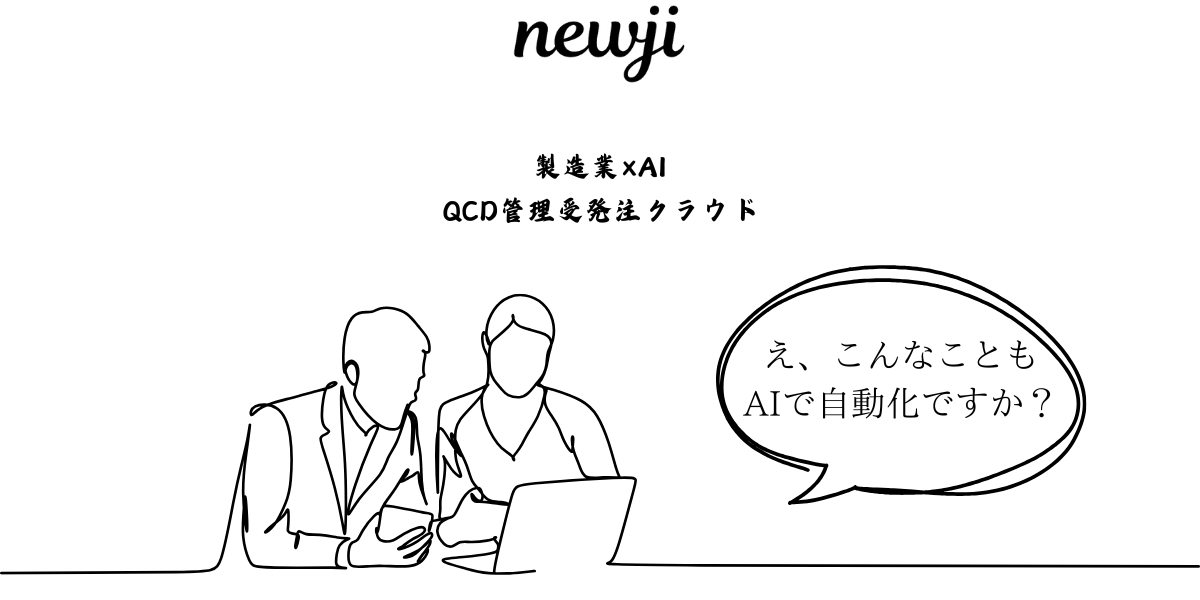
Exploration and application examples of tube burner cracking sign detection technology
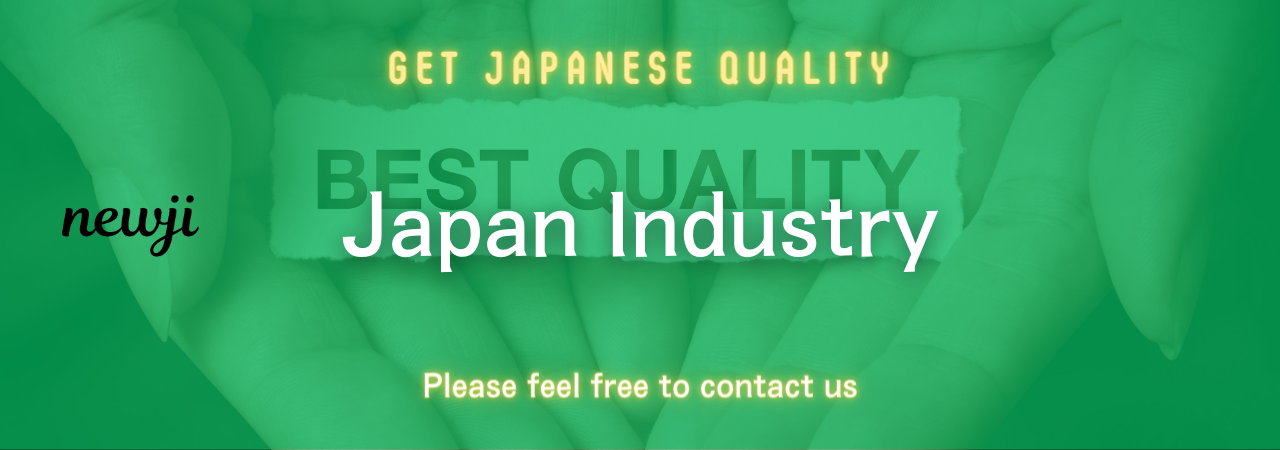
目次
Understanding Tube Burner Cracking
In industrial settings, tube burners play a crucial role in various applications, particularly in heating systems and chemical processing units.
These burners function by combusting fuel to generate heat, which is then utilized for different processes.
However, like any other mechanical component, tube burners are prone to wear and tear over time.
One significant issue that can arise is the cracking of these burners.
Cracking can lead to inefficient operation, increased maintenance costs, and even hazardous situations if not detected early.
What Causes Tube Burner Cracking?
To effectively address the problem of cracking in tube burners, it’s essential to understand the underlying causes.
The most common reasons for cracking include thermal stress, material fatigue, corrosion, and mechanical stress.
1. **Thermal Stress**: As tube burners operate at high temperatures, the constant expansion and contraction can lead to thermal fatigue, eventually causing cracks to form.
2. **Material Fatigue**: Continuous exposure to high temperatures and pressure can cause the burner materials to lose their structural integrity over time, leading to fatigue and subsequent cracking.
3. **Corrosion**: Exposure to corrosive substances and high-temperature environments can significantly damage the burner’s surface, making it more susceptible to cracking.
4. **Mechanical Stress**: Vibration and improper installation or operation can introduce mechanical stresses that contribute to the development of cracks.
Detection Technology for Cracking Signs
Early detection of cracking is pivotal in preventing potential hazards and maintaining operational efficiency.
Several advanced technologies have been developed to identify and monitor cracking signs in tube burners.
Infrared Thermography
Infrared thermography is a non-contact detection method that uses thermal imaging cameras to detect temperature variations on the surface of tube burners.
Cracks often result in uneven heat distribution, which can be captured as thermal anomalies by the camera.
This technology is advantageous because it does not require direct contact with the burners, making it safe and efficient for routine inspections.
Ultrasonic Testing
Ultrasonic testing involves using high-frequency sound waves to detect internal and surface cracks in materials.
This technology is highly effective because it can penetrate deep into the material and provide detailed information about the presence of any discontinuities.
Ultrasonic testing is widely used in industries for its accuracy and reliability, particularly for detecting subsurface cracks that are not visible to the naked eye.
Acoustic Emission Monitoring
Acoustic emission monitoring detects the high-frequency sound waves generated by the sudden release of energy from crack formation and propagation.
These sound waves are recorded by sensors attached to the surface of the burner.
Analyzing patterns in the recorded emissions allows experts to identify crack initiation and growth in real time, enabling prompt maintenance actions.
Practical Applications of Crack Detection Technology
Industries across the globe are increasingly adopting crack detection technologies to safeguard their operations and assets.
These technologies offer numerous practical applications that significantly benefit various sectors.
Enhancing Safety and Reliability
By implementing crack detection systems, industries can significantly enhance the safety and reliability of their operations.
Early identification of cracks reduces the risk of catastrophic failures, safeguarding employees and minimizing downtime.
Optimizing Maintenance Schedules
Predictive maintenance programs can be developed by leveraging crack detection technologies.
By monitoring the health of tube burners in real time, maintenance can be scheduled only when necessary, preventing unnecessary expenses and prolonging equipment life.
Energy Efficiency Improvements
Cracks in tube burners can lead to energy inefficiencies, as they might cause an uneven distribution of heat.
By identifying and rectifying cracking issues early, industries can optimize their energy consumption and improve overall operational efficiency.
Reducing Operational Costs
Addressing cracking issues before they escalate can lead to significant cost savings.
Preventive measures are generally more economical than reactive maintenance, which often involves emergency repairs and production interruptions.
Challenges in Crack Detection
While crack detection technology offers considerable benefits, several challenges must be overcome for optimal implementation.
Cost and Training
The initial investment in advanced crack detection equipment and the training required to use these technologies can be substantial for some industries.
It’s crucial for organizations to weigh the long-term benefits against the upfront costs to make informed decisions.
Data Interpretation
Accurate interpretation of data from detection technologies is essential for effective decision-making.
Skilled analysts are required to ensure that the data collected from these technologies is analyzed correctly, leading to appropriate actions.
Environmental Limitations
Certain detection methods, such as infrared thermography, may have limitations in harsh environments where temperatures fluctuate rapidly or chemicals obscure clear thermal readings.
The Future of Crack Detection in Tube Burners
As technology continues to advance, the future of crack detection in tube burners looks promising.
Integration with IoT
The integration of detection systems with the Internet of Things (IoT) will enable seamless communication between equipment, allowing for predictive maintenance strategies that are data-driven and highly efficient.
Improvements in Sensor Technology
Ongoing research and development efforts are focused on improving sensor technologies to provide more accurate and reliable data, even in challenging industrial environments.
Automated Monitoring Systems
The development of automated monitoring systems will allow industries to streamline their crack detection processes, reducing reliance on manual inspections and ensuring continuous health monitoring of critical equipment.
Through continued innovation and adoption of advanced detection technologies, industries can significantly mitigate the risks associated with tube burner cracking, ensuring safe, reliable, and cost-effective operations.
資料ダウンロード
QCD管理受発注クラウド「newji」は、受発注部門で必要なQCD管理全てを備えた、現場特化型兼クラウド型の今世紀最高の受発注管理システムとなります。
ユーザー登録
受発注業務の効率化だけでなく、システムを導入することで、コスト削減や製品・資材のステータス可視化のほか、属人化していた受発注情報の共有化による内部不正防止や統制にも役立ちます。
NEWJI DX
製造業に特化したデジタルトランスフォーメーション(DX)の実現を目指す請負開発型のコンサルティングサービスです。AI、iPaaS、および先端の技術を駆使して、製造プロセスの効率化、業務効率化、チームワーク強化、コスト削減、品質向上を実現します。このサービスは、製造業の課題を深く理解し、それに対する最適なデジタルソリューションを提供することで、企業が持続的な成長とイノベーションを達成できるようサポートします。
製造業ニュース解説
製造業、主に購買・調達部門にお勤めの方々に向けた情報を配信しております。
新任の方やベテランの方、管理職を対象とした幅広いコンテンツをご用意しております。
お問い合わせ
コストダウンが利益に直結する術だと理解していても、なかなか前に進めることができない状況。そんな時は、newjiのコストダウン自動化機能で大きく利益貢献しよう!
(β版非公開)