- お役立ち記事
- Exploring CIP Molding: The Innovative Japanese Technique in Cold Isostatic Pressing
Exploring CIP Molding: The Innovative Japanese Technique in Cold Isostatic Pressing
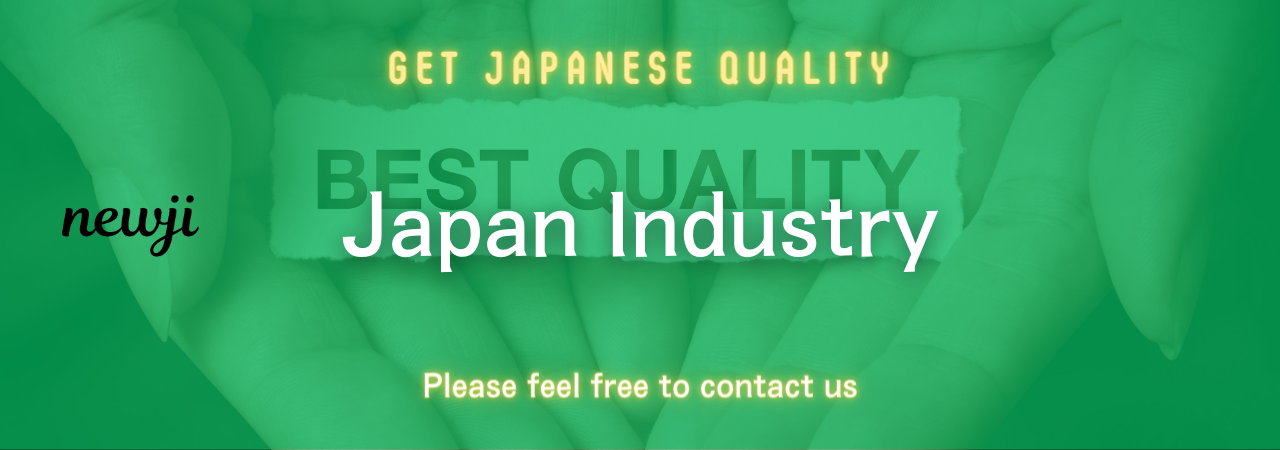
目次
Introduction to CIP Molding
Cold Isostatic Pressing (CIP) molding is an advanced manufacturing technique with significant applications in high-performance component production.
The Japanese have perfected this technique, combining precision, quality, and efficiency.
This article delves into CIP molding, highlighting its capabilities, advantages, and how Japanese innovation has made a substantial impact in this area.
What is Cold Isostatic Pressing (CIP)?
CIP is a process involving the application of uniform pressure to a powder encased in a flexible mold.
This mold is typically submerged in a pressurized fluid, ensuring that pressure is uniformly distributed.
Unlike traditional pressing methods, CIP can produce more consistent and dense materials without compromising structural integrity.
The Components of CIP Molding
CIP involves several key components:
1. **Powder Material**: The choice of powder can vary depending on the application.
Common materials include ceramics, metals, and composites.
2. **Flexible Mold**: This must be durable and capable of withstanding high pressures.
3. **Pressure Vessel and Fluid**: The fluid, usually water or oil, transmits pressure uniformly to all parts of the mold.
Advantages of CIP Molding
When discussing CIP molding, several benefits set this technique apart from conventional methods:
Uniform Density and Structural Integrity
CIP ensures that the material density is uniform throughout.
This uniformity is vital for components where structural integrity can’t be compromised, such as aerospace and medical implants.
Complex Geometries
CIP is ideal for producing complex and intricate shapes which would be difficult to achieve with traditional pressing methods.
The flexibility of the mold allows for a wide range of design possibilities.
Material Efficiency
There is minimal material wastage in the CIP process, which translates into cost savings.
Additionally, the dense compaction reduces porosity, enhancing the final product’s performance.
Scalability
Whether for small-scale prototypes or large production runs, CIP is highly scalable.
Manufacturing companies can easily ramp up production without significant changes in the process.
Challenges and Considerations
While CIP offers numerous advantages, it is not without its challenges.
Initial Investment
The setup for CIP can be costly, involving high capital expenditure for the pressure vessel and other equipment.
Companies must weigh these initial costs against long-term benefits.
Material Limitations
While CIP can work with a variety of materials, not all materials are suitable.
Some materials may react differently to the pressures involved, requiring careful selection and testing.
Process Control
Maintaining consistent pressure and mold integrity is crucial.
Any variations can lead to defects, necessitating stringent process control and monitoring.
Japanese Innovation in CIP Molding
Japanese companies are renowned for their meticulous approach to manufacturing, and CIP molding is no exception.
They have made several advancements that enhance the efficiency and effectiveness of this process.
Precision Engineering
Japanese companies invest heavily in precision engineering.
Their CIP machines are designed to apply pressure with unparalleled accuracy, ensuring that each product meets stringent quality standards.
Material Science
Japanese manufacturers continue to push the boundaries of material science, developing powders that are specifically designed for CIP.
These materials offer superior performance characteristics, making them ideal for high-end applications.
Automation and Integration
To further enhance efficiency, Japanese companies are increasingly incorporating automation in CIP processes.
Automated systems ensure consistent operation, reduce human error, and can seamlessly integrate with other manufacturing processes.
Best Practices in Supplier Negotiations
When engaging with Japanese suppliers for CIP equipment or materials, certain best practices can facilitate successful negotiations.
Understanding Cultural Nuances
Japanese business culture places a high emphasis on respect and relationship-building.
Taking the time to understand and appreciate these nuances can lead to more productive discussions and long-term partnerships.
Clear Communication
Precision and clarity in communication are vital.
Detailed specifications, deadlines, and quality expectations should be clearly articulated to avoid misunderstandings.
Emphasizing Quality
Japanese suppliers pride themselves on quality.
Demonstrating a shared commitment to quality and excellence can resonate well and facilitate better cooperation.
Market Conditions and Trends
The demand for high-performance components is driving the growth of CIP.
Several trends are shaping the market.
Increased Demand for High-Performance Materials
Industries such as aerospace, automotive, and medical are increasingly relying on advanced materials produced through CIP for their superior characteristics.
Technological Advancements
Continuous innovations in CIP technology are expanding its applications, making it feasible for more complex and diverse requirements.
Environmental Concerns
As a more material-efficient process, CIP aligns well with increasing environmental regulations and sustainable manufacturing practices.
Quality Control in CIP Molding
Ensuring the highest quality in CIP molding involves several critical steps.
Material Testing
Before the actual pressing, thorough testing of the powder material is essential.
This includes checking for purity, particle size distribution, and other relevant properties.
Process Monitoring
Continuous monitoring of the pressure and fluid medium during the pressing phase can help detect any anomalies early on.
Post-Processing Inspection
Upon completion, products should undergo rigorous inspection to identify any defects or inconsistencies.
Advanced imaging techniques can be beneficial in detecting hidden flaws.
Conclusion
Cold Isostatic Pressing (CIP) molding, especially as refined by Japanese innovation, represents a pinnacle in advanced manufacturing techniques.
It offers unparalleled benefits in terms of material utilization, structural integrity, and design flexibility.
While it comes with its own set of challenges, systematic approaches and best practices in supplier negotiation, market analysis, and quality control can significantly mitigate these issues.
Embracing CIP can position companies at the forefront of high-performance component manufacturing, ensuring they meet sophisticated market demands with precision and efficiency.
資料ダウンロード
QCD調達購買管理クラウド「newji」は、調達購買部門で必要なQCD管理全てを備えた、現場特化型兼クラウド型の今世紀最高の購買管理システムとなります。
ユーザー登録
調達購買業務の効率化だけでなく、システムを導入することで、コスト削減や製品・資材のステータス可視化のほか、属人化していた購買情報の共有化による内部不正防止や統制にも役立ちます。
NEWJI DX
製造業に特化したデジタルトランスフォーメーション(DX)の実現を目指す請負開発型のコンサルティングサービスです。AI、iPaaS、および先端の技術を駆使して、製造プロセスの効率化、業務効率化、チームワーク強化、コスト削減、品質向上を実現します。このサービスは、製造業の課題を深く理解し、それに対する最適なデジタルソリューションを提供することで、企業が持続的な成長とイノベーションを達成できるようサポートします。
オンライン講座
製造業、主に購買・調達部門にお勤めの方々に向けた情報を配信しております。
新任の方やベテランの方、管理職を対象とした幅広いコンテンツをご用意しております。
お問い合わせ
コストダウンが利益に直結する術だと理解していても、なかなか前に進めることができない状況。そんな時は、newjiのコストダウン自動化機能で大きく利益貢献しよう!
(Β版非公開)