- お役立ち記事
- Exploring Dyneema: Revolutionizing Strength in Japanese Manufacturing Techniques
月間76,176名の
製造業ご担当者様が閲覧しています*
*2025年3月31日現在のGoogle Analyticsのデータより
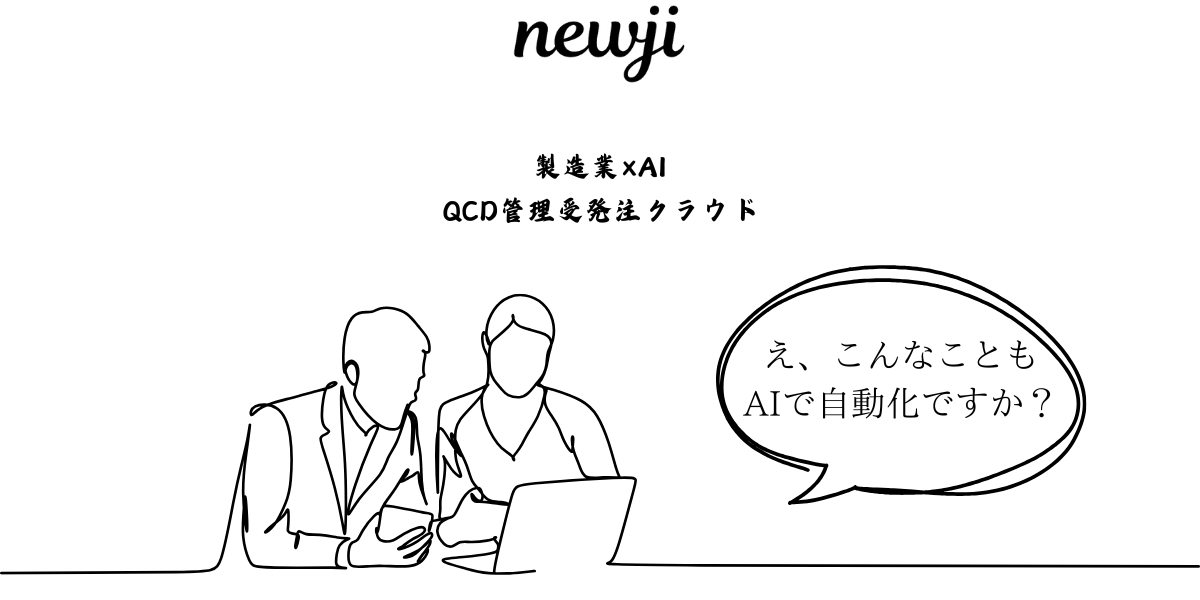
Exploring Dyneema: Revolutionizing Strength in Japanese Manufacturing Techniques
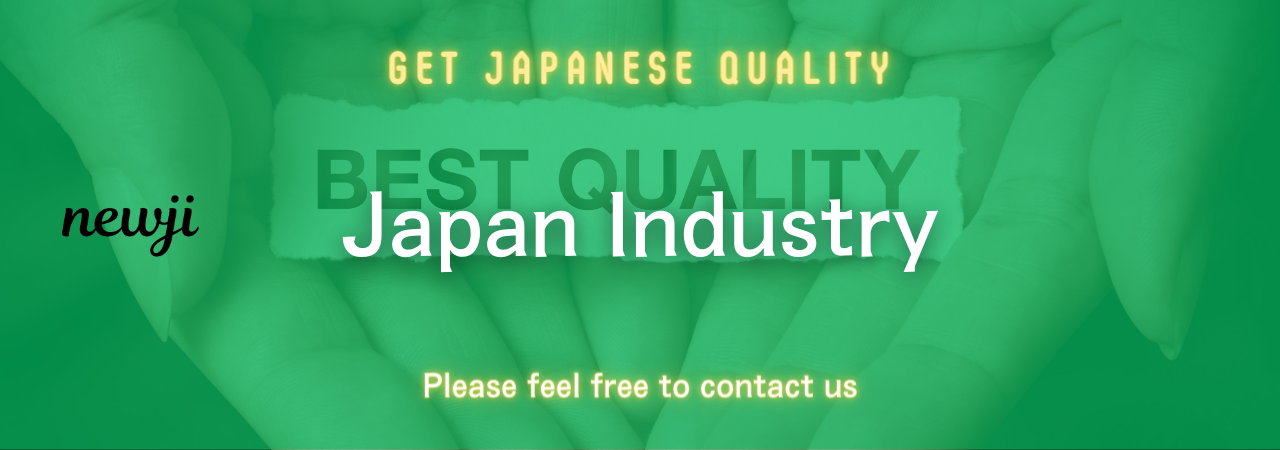
目次
Introduction to Dyneema
Dyneema has emerged as a groundbreaking material in the manufacturing industry, renowned for its exceptional strength and versatility. Often referred to as the world’s strongest fiber, Dyneema is a high-performance polyethylene used in a multitude of applications ranging from aerospace to consumer goods. Its unique properties have revolutionized manufacturing techniques, particularly within Japanese industries known for their precision and innovation.
Understanding Dyneema’s role in modern manufacturing is essential for businesses aiming to enhance product performance and maintain a competitive edge. This article delves into the intricate relationship between Dyneema and Japanese manufacturing practices, exploring the material’s advantages, challenges, and the strategic approaches necessary for successful procurement and integration.
Dyneema in Japanese Manufacturing
Japan has long been a leader in manufacturing excellence, characterized by meticulous attention to detail and a commitment to quality. The integration of Dyneema into Japanese manufacturing processes signifies a fusion of traditional craftsmanship with cutting-edge technology. This synergy has enabled Japanese manufacturers to push the boundaries of product performance and durability.
History of Adoption
The adoption of Dyneema in Japan traces back to the late 20th century when manufacturers began seeking materials that could offer superior performance without compromising on weight or flexibility. Initially utilized in niche applications such as ropes and sails, Dyneema’s potential quickly became apparent across various sectors. Japanese companies, with their emphasis on innovation, were quick to integrate Dyneema into their product lines, setting new standards in industries like automotive, electronics, and consumer goods.
Key Industries Using Dyneema
Several Japanese industries have leveraged Dyneema to enhance their offerings. In the automotive sector, Dyneema is used in seat belts and safety systems, providing unmatched strength and reliability. The electronics industry utilizes Dyneema in cables and connectors, benefiting from the material’s lightweight and high tensile strength properties. Additionally, consumer goods such as backpacks, outdoor gear, and sporting equipment have seen significant improvements in performance and durability due to Dyneema integration.
Advantages of Dyneema in Manufacturing
Dyneema offers a range of benefits that make it an attractive choice for manufacturers seeking to innovate and improve product quality. Its unique properties address several key challenges faced in traditional manufacturing materials.
Superior Strength-to-Weight Ratio
One of Dyneema’s most notable advantages is its exceptional strength-to-weight ratio. It is approximately 15 times stronger than steel and 40% stronger than aramid fibers, yet it is significantly lighter. This characteristic allows manufacturers to design products that are both robust and lightweight, enhancing performance while reducing material costs and energy consumption.
Durability and Longevity
Dyneema’s resistance to abrasion, UV radiation, and various chemicals contributes to the longevity of products. Items manufactured with Dyneema maintain their integrity and performance over extended periods, even in harsh environments. This durability translates to lower maintenance costs and increased customer satisfaction, as products are less likely to fail or degrade over time.
Corrosion Resistance
Unlike metal counterparts, Dyneema does not corrode when exposed to moisture or other corrosive substances. This property is particularly beneficial in applications where products are subjected to outdoor conditions or chemical exposure. Manufacturers can produce items with fewer components susceptible to corrosion, simplifying maintenance and extending product life.
Flexibility in Design
Dyneema’s flexibility allows for innovative design possibilities. It can be molded and shaped without compromising its strength, enabling the creation of complex structures and lightweight assemblies. This flexibility is invaluable in industries such as aerospace and automotive, where intricate designs are often required to meet performance specifications.
Disadvantages of Dyneema
Despite its numerous advantages, Dyneema presents certain challenges that manufacturers must navigate to fully leverage its potential.
Cost Considerations
Dyneema is generally more expensive than traditional materials like steel or standard polyethylene. The high cost can be a barrier for manufacturers, especially in cost-sensitive markets. However, the long-term benefits, such as reduced maintenance and longer product lifespans, often justify the initial investment. Manufacturers must perform cost-benefit analyses to determine the economic viability of incorporating Dyneema into their products.
Processing Challenges
Working with Dyneema requires specialized equipment and expertise. Its high melting point and unique physical properties necessitate precise processing conditions to avoid degradation and maintain material integrity. Manufacturers may need to invest in new machinery or training programs to handle Dyneema effectively, which can add to the overall cost and complexity of production.
Supply Chain Vulnerabilities
Dyneema’s availability is limited to specific suppliers, which can create supply chain vulnerabilities. Dependence on a few key manufacturers increases the risk of disruptions due to geopolitical issues, natural disasters, or other unforeseen events. Diversifying suppliers and establishing robust supply chain strategies are essential to mitigate these risks and ensure a consistent supply of Dyneema.
Supplier Negotiation Techniques for Dyneema
Effective negotiation with Dyneema suppliers is crucial for securing favorable terms and ensuring a reliable supply chain. Japanese suppliers are known for their precision and commitment to quality, making negotiation a strategic process that requires thorough preparation and understanding.
Understanding the Market
Before entering negotiations, it is essential to have a comprehensive understanding of the Dyneema market. This includes being aware of current prices, supply trends, and the competitive landscape. Knowledge of market dynamics enables manufacturers to make informed decisions and identify opportunities for cost savings or value enhancement.
Building Relationships with Japanese Suppliers
Japanese business culture places a strong emphasis on relationships and trust. Building a solid relationship with suppliers can lead to more favorable terms, priority in supply allocation, and collaborative innovation opportunities. Regular communication, visits to supplier facilities, and mutual respect for business practices are key components of successful relationship-building.
Negotiation Strategies
Employing effective negotiation strategies can significantly impact the outcome of supplier discussions. Strategies include:
– **Volume Commitments:** Committing to larger purchase volumes can secure lower prices and priority supply.
– **Long-term Contracts:** Establishing long-term agreements can provide stability for both parties and lead to better pricing and terms.
– **Value-added Services:** Negotiating for additional services, such as customized formulations or expedited shipping, can add value beyond price.
– **Flexibility:** Being flexible with payment terms or delivery schedules can make negotiations more productive and cooperative.
Market Conditions for Dyneema
The Dyneema market is influenced by various factors, including global demand, technological advancements, and economic conditions. Understanding these market conditions is vital for manufacturers to anticipate changes and adapt their procurement strategies accordingly.
Global Demand and Trends
Global demand for Dyneema has been steadily increasing, driven by its adoption in high-performance applications across multiple industries. Trends such as the growth of the aerospace sector, the rise of lightweight consumer electronics, and advancements in renewable energy technologies are significant drivers of Dyneema demand. Manufacturers must stay abreast of these trends to align their product development and procurement strategies with market needs.
Impact of Economic Factors
Economic factors, such as currency fluctuations, trade policies, and raw material costs, directly affect the Dyneema market. For instance, changes in exchange rates can impact the cost of imports, while tariffs and trade restrictions may alter supply dynamics. Manufacturers should monitor economic indicators and engage in strategic planning to mitigate potential adverse effects on their Dyneema procurement.
Future Prospects
The future of Dyneema in manufacturing appears promising, with ongoing research and development aimed at enhancing its properties and expanding its applications. Innovations such as Dyneema Composite Fabrics (DCF) and the integration of Dyneema with other materials are likely to open new avenues for its use. As industries continue to prioritize performance and sustainability, Dyneema is well-positioned to play a pivotal role in the next generation of manufacturing solutions.
Best Practices in Procurement and Purchasing of Dyneema
Implementing best practices in procurement and purchasing is essential for maximizing the benefits of Dyneema while minimizing potential risks. These practices encompass supplier evaluation, quality control, contract management, and strategic sourcing.
Evaluating Suppliers
Thorough supplier evaluation is critical to ensure reliability and quality. Key considerations include:
– **Reputation:** Assessing the supplier’s market standing and track record for reliability.
– **Quality Certifications:** Verifying that suppliers adhere to international quality standards and possess relevant certifications.
– **Capacity:** Ensuring that the supplier can meet demand volumes consistently.
– **Innovation Capacity:** Evaluating the supplier’s ability to support product innovations and customization.
Quality Control Measures
Maintaining high-quality standards is paramount when working with Dyneema. Implementing rigorous quality control measures includes:
– **Incoming Inspections:** Conducting thorough inspections of Dyneema shipments to verify compliance with specifications.
– **Testing Protocols:** Establishing standardized testing procedures to assess material properties such as tensile strength, elongation, and durability.
– **Continuous Improvement:** Collaborating with suppliers to identify and implement quality improvements.
Contract Management
Effective contract management ensures that all parties adhere to agreed-upon terms and conditions. Key aspects include:
– **Clear Specifications:** Defining detailed product specifications, delivery schedules, and performance expectations.
– **Performance Metrics:** Establishing KPIs to monitor supplier performance and compliance.
– **Dispute Resolution:** Outlining mechanisms for resolving conflicts or discrepancies that may arise during the partnership.
Case Studies: Successful Implementation of Dyneema in Japanese Manufacturing
Examining real-world examples of Dyneema integration in Japanese manufacturing provides valuable insights into best practices and the tangible benefits of the material.
Example 1: Automotive Safety Systems
A leading Japanese automotive manufacturer incorporated Dyneema into their seatbelt systems to enhance safety and comfort. By replacing traditional steel belts with Dyneema fibers, the company achieved a significant reduction in seatbelt weight without compromising strength. This innovation not only improved vehicle efficiency by reducing overall weight but also enhanced passenger safety by providing more reliable restraint systems. The successful implementation led to widespread adoption across their vehicle lineup, reinforcing the company’s reputation for safety and innovation.
Example 2: High-Performance Sports Equipment
A Japanese manufacturer of high-performance sporting goods utilized Dyneema in the production of lightweight and durable fishing lines. Traditional fishing lines often suffer from issues such as stretching and susceptibility to environmental degradation. By integrating Dyneema, the manufacturer developed a fishing line that offers superior tensile strength, minimal stretch, and enhanced resistance to UV radiation and chemicals. This advancement resulted in improved fishing performance for consumers and positioned the company as a leader in sports equipment innovation.
Conclusion
Dyneema stands at the forefront of material innovation, offering unparalleled strength, durability, and versatility that align with the high standards of Japanese manufacturing. Its integration into various industries has led to the development of superior products that meet the evolving demands of the global market. While challenges such as cost and supply chain vulnerabilities exist, strategic procurement and effective supplier relationships can mitigate these issues.
Japanese manufacturers’ commitment to quality and innovation provides a robust framework for leveraging Dyneema’s full potential. By adopting best practices in procurement, maintaining rigorous quality control, and staying attuned to market trends, manufacturers can harness the benefits of Dyneema to achieve competitive advantage and drive future growth.
As the landscape of manufacturing continues to evolve, Dyneema is poised to play a pivotal role in shaping the next generation of high-performance products. Embracing this material’s capabilities will enable manufacturers to push the boundaries of what is possible, delivering exceptional value to consumers and stakeholders alike.
資料ダウンロード
QCD管理受発注クラウド「newji」は、受発注部門で必要なQCD管理全てを備えた、現場特化型兼クラウド型の今世紀最高の受発注管理システムとなります。
ユーザー登録
受発注業務の効率化だけでなく、システムを導入することで、コスト削減や製品・資材のステータス可視化のほか、属人化していた受発注情報の共有化による内部不正防止や統制にも役立ちます。
NEWJI DX
製造業に特化したデジタルトランスフォーメーション(DX)の実現を目指す請負開発型のコンサルティングサービスです。AI、iPaaS、および先端の技術を駆使して、製造プロセスの効率化、業務効率化、チームワーク強化、コスト削減、品質向上を実現します。このサービスは、製造業の課題を深く理解し、それに対する最適なデジタルソリューションを提供することで、企業が持続的な成長とイノベーションを達成できるようサポートします。
製造業ニュース解説
製造業、主に購買・調達部門にお勤めの方々に向けた情報を配信しております。
新任の方やベテランの方、管理職を対象とした幅広いコンテンツをご用意しております。
お問い合わせ
コストダウンが利益に直結する術だと理解していても、なかなか前に進めることができない状況。そんな時は、newjiのコストダウン自動化機能で大きく利益貢献しよう!
(β版非公開)