- お役立ち記事
- “Exploring Japanese Manufacturing Precision: The Double-Head Grinder Revolution”
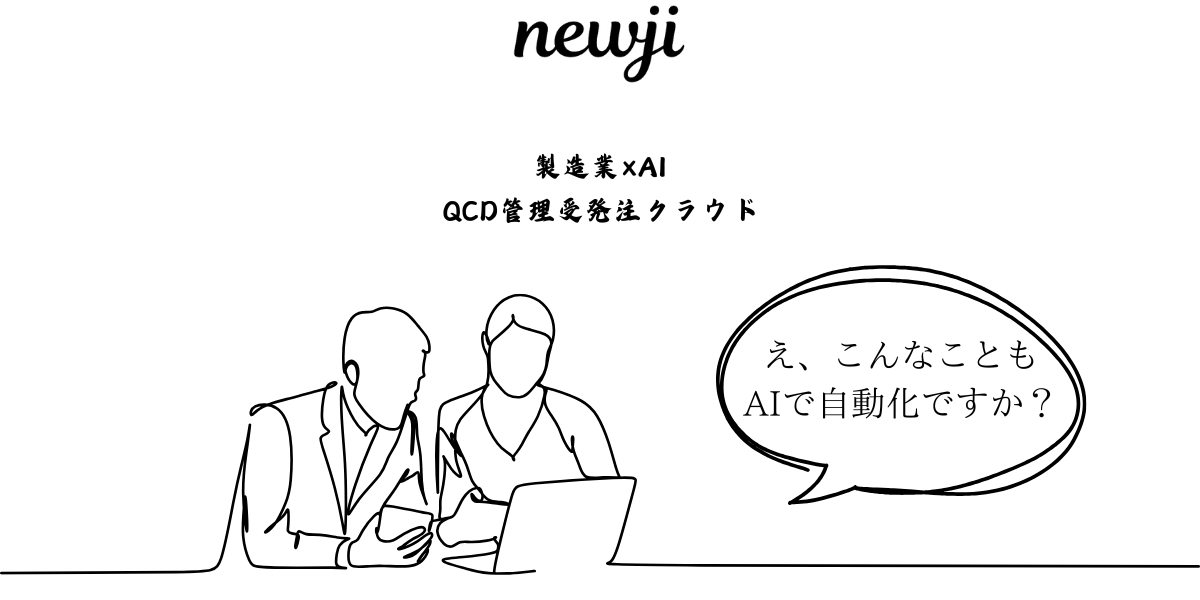
“Exploring Japanese Manufacturing Precision: The Double-Head Grinder Revolution”
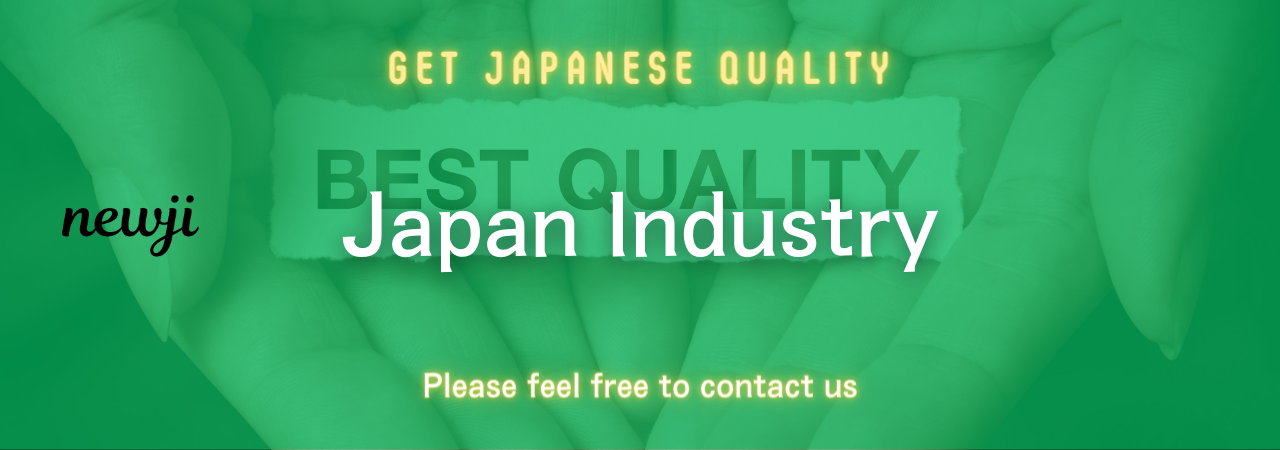
目次
Introduction to Double-Head Grinders in Japanese Manufacturing
Japanese manufacturing has long been renowned for its precision and innovation.
One such advancement is the double-head grinder, a tool that has revolutionized the industry.
This article delves into the intricacies of double-head grinders and their impact on manufacturing processes.
We will explore the advantages and disadvantages, procurement strategies, negotiation techniques, market conditions, and best practices associated with these precision tools.
The Precision of Japanese Manufacturing
Japanese manufacturers have consistently set benchmarks in engineering and production quality.
The emphasis on meticulous craftsmanship ensures that products meet the highest standards.
This commitment to precision is evident in the development and deployment of advanced machinery like double-head grinders.
These tools are integral to achieving the fine tolerances and surface finishes required in modern manufacturing.
Understanding Double-Head Grinders
Double-head grinders feature two grinding wheels positioned to simultaneously work on opposing sides of a workpiece.
This configuration allows for increased efficiency and uniformity in the grinding process.
By handling dual grinding operations, manufacturers can reduce cycle times and enhance productivity.
The synchronized movement ensures consistent precision across the entire workpiece.
Operational Advantages
The primary advantage of double-head grinders is their ability to handle complex grinding tasks with minimal manual intervention.
This leads to higher throughput and reduced labor costs.
Additionally, the dual-action mechanism improves accuracy by maintaining consistent pressure and alignment on both sides of the workpiece.
This results in superior finish quality and dimensional accuracy.
Technological Innovations
Japanese manufacturers have integrated advanced technologies into double-head grinders.
Features such as computerized numerical control (CNC) systems enable precise adjustments and real-time monitoring.
This level of automation not only enhances precision but also allows for customization to meet specific manufacturing requirements.
The incorporation of sensors and feedback systems further optimizes the grinding process, ensuring maximal efficiency and minimal downtime.
Procurement and Purchasing Strategies
When procuring double-head grinders from Japanese suppliers, it is essential to adopt strategic approaches to ensure optimal investment.
Supplier Selection
Selecting the right supplier is critical for acquiring high-quality double-head grinders.
Japanese suppliers are known for their adherence to strict quality control standards and continuous improvement practices.
Evaluating potential suppliers based on their track record, technological capabilities, and customer support services is crucial.
Cost-Benefit Analysis
A comprehensive cost-benefit analysis helps in understanding the long-term value of investing in double-head grinders.
Although the initial investment may be higher compared to single-head models, the increased productivity and precision can lead to significant cost savings over time.
Evaluating factors such as maintenance costs, energy efficiency, and expected lifespan of the equipment is essential in making informed purchasing decisions.
Building Relationships with Japanese Suppliers
Establishing strong relationships with Japanese suppliers can lead to better negotiation outcomes and long-term partnerships.
Understanding cultural nuances and business practices in Japan is vital for effective communication and collaboration.
Building trust through consistent and respectful interactions can pave the way for favorable terms and access to the latest technological advancements.
Supplier Negotiation Techniques
Negotiating with Japanese suppliers requires a tactful and informed approach.
Preparation and Research
Thorough preparation is the cornerstone of successful negotiations.
Researching the supplier’s background, product specifications, and market positioning provides valuable insights that can be leveraged during discussions.
Understanding the supplier’s needs and constraints helps in identifying mutually beneficial solutions.
Emphasizing Long-Term Partnership
Japanese businesses value long-term, stable relationships over short-term gains.
Emphasizing the potential for a lasting partnership can be more effective than pushing for immediate discounts or concessions.
Highlighting mutual benefits and shared goals fosters a collaborative negotiation environment.
Flexibility and Compromise
Demonstrating flexibility and a willingness to compromise on certain terms can facilitate smoother negotiations.
Be prepared to adjust volume commitments, payment terms, or delivery schedules in ways that accommodate both parties’ interests.
This approach not only aids in reaching an agreement but also strengthens the supplier relationship.
Market Conditions and Trends
Staying informed about current market conditions and industry trends is essential for strategic procurement.
Global Supply Chain Dynamics
Global supply chain disruptions can impact the availability and pricing of double-head grinders.
Monitoring geopolitical developments, trade policies, and logistical challenges helps in anticipating and mitigating risks.
Diversifying supplier bases and maintaining contingency plans are prudent strategies to navigate fluctuating market conditions.
Technological Advancements
The manufacturing sector is continually evolving with technological breakthroughs.
Japanese suppliers are at the forefront of integrating smart technologies and automation into grinding machinery.
Staying abreast of these advancements ensures that procurement decisions align with the latest industry standards and innovations.
Economic Factors
Economic indicators such as inflation rates, currency exchange fluctuations, and interest rates influence procurement strategies.
Understanding how these factors affect pricing and supplier viability is crucial for making informed purchasing decisions.
Economic stability in Japan contributes to reliable supply chains and consistent product quality.
Best Practices in Procuring Double-Head Grinders
Adhering to best practices enhances the effectiveness of procurement processes and ensures the acquisition of high-quality equipment.
Clear Specification and Requirements
Clearly defining the technical specifications and operational requirements of double-head grinders is essential.
Providing detailed information on desired features, performance standards, and integration needs facilitates accurate quotations and reliable product performance.
Vendor Evaluation and Auditing
Regularly evaluating and auditing suppliers ensures ongoing compliance with quality and performance standards.
Conducting on-site visits, reviewing certifications, and assessing production capabilities help in maintaining high procurement standards.
This proactive approach mitigates risks associated with supplier reliability and product quality.
Leverage Total Cost of Ownership (TCO)
Considering the total cost of ownership, including maintenance, training, and operational expenses, provides a comprehensive view of the investment.
Evaluating TCO helps in selecting suppliers that offer not only competitive pricing but also long-term value and support.
Implementing Collaborative Planning
Collaborative planning with suppliers enhances alignment and efficiency in the procurement process.
Sharing forecasts, production schedules, and inventory data fosters synchronization and reduces lead times.
This collaborative approach supports a seamless supply chain and optimal equipment utilization.
Advantages of Japanese Double-Head Grinders
Japanese double-head grinders offer numerous advantages that make them a preferred choice in manufacturing environments.
Superior Precision and Quality
The precision engineering of Japanese double-head grinders ensures high accuracy and consistency in grinding operations.
This reliability minimizes defects and enhances the overall quality of the manufactured products.
Enhanced Productivity
The dual-action mechanism of double-head grinders accelerates the grinding process, leading to increased throughput.
Manufacturers can achieve higher production volumes without compromising on quality.
Advanced Technological Features
Incorporation of cutting-edge technologies such as CNC, automation, and smart sensors enhances the functionality and efficiency of double-head grinders.
These features enable real-time monitoring, precise control, and data-driven optimization of grinding operations.
Energy Efficiency
Japanese double-head grinders are designed with energy-efficient components and innovative designs that reduce power consumption.
This not only lowers operational costs but also contributes to environmentally sustainable manufacturing practices.
Potential Disadvantages and Mitigation Strategies
While Japanese double-head grinders offer substantial benefits, there are potential drawbacks that organizations must consider.
Higher Initial Investment
The advanced features and superior quality of Japanese double-head grinders come with a higher upfront cost.
Conducting a detailed cost-benefit analysis and exploring financing options can help mitigate the financial impact.
Complexity of Operation
The sophisticated technology embedded in double-head grinders may require specialized training for operators.
Investing in comprehensive training programs and partnering with suppliers for technical support ensures efficient and effective utilization of the equipment.
Supply Chain Dependencies
Relying on Japanese suppliers may create dependencies that can be problematic during supply chain disruptions.
Diversifying the supplier base and establishing contingency plans can reduce the risk associated with supplier dependence.
Supplier Relationship Management
Effective management of supplier relationships is essential for maximizing the benefits of procuring Japanese double-head grinders.
Regular Communication and Feedback
Maintaining open lines of communication with suppliers fosters trust and collaboration.
Providing regular feedback on product performance and addressing issues promptly enhances supplier responsiveness and product quality.
Continuous Improvement Collaboration
Engaging in continuous improvement initiatives with suppliers drives innovation and efficiency.
Collaborative efforts to optimize grinding processes and adopt new technologies can lead to mutual growth and enhanced competitiveness.
Performance Monitoring and Evaluation
Implementing performance metrics and conducting regular evaluations of supplier performance ensures that procurement goals are met.
Tracking key indicators such as delivery punctuality, quality standards, and responsiveness helps in making informed decisions about supplier partnerships.
Implementing Best Practices in Procurement
Adhering to established best practices in procurement ensures the successful acquisition and integration of double-head grinders into manufacturing operations.
Strategic Sourcing
Adopting a strategic sourcing approach involves analyzing and planning procurement activities to align with organizational goals.
This includes identifying critical suppliers, optimizing supplier networks, and leveraging market intelligence to make informed sourcing decisions.
Risk Management
Identifying and mitigating risks associated with procurement activities protects the organization from potential disruptions.
Developing risk management plans that address supplier reliability, geopolitical factors, and technological changes ensures procurement resilience.
Ethical and Sustainable Procurement
Ensuring that procurement practices adhere to ethical standards and promote sustainability is increasingly important.
Collaborating with suppliers who prioritize environmental responsibility and fair labor practices enhances the organization’s reputation and supports global sustainability efforts.
Case Studies: Success Stories with Japanese Double-Head Grinders
Examining real-world implementations of Japanese double-head grinders provides valuable insights into their impact on manufacturing processes.
Automotive Industry
A leading automotive manufacturer integrated Japanese double-head grinders into their production line for engine component manufacturing.
The dual-action grinding significantly reduced cycle times, allowing for increased production capacity.
The enhanced precision ensured that engine parts met stringent quality standards, resulting in fewer defects and increased overall reliability of the vehicles.
Aerospace Sector
In the aerospace industry, precision is paramount. A major aerospace company adopted double-head grinders to machine turbine blades.
The consistent quality and dimensional accuracy provided by the grinders enabled the production of high-performance components that meet the demanding specifications of the aerospace sector.
This integration also streamlined the manufacturing process, leading to cost savings and improved lead times.
Medical Device Manufacturing
A medical device manufacturer utilized Japanese double-head grinders to produce intricate components with tight tolerances.
The grinders’ advanced features allowed for precise shaping and finishing, ensuring that each component complied with medical standards and performance requirements.
This led to an enhancement in product quality and a reduction in production costs due to decreased material waste and rework.
Training and Skill Development
Proper training and skill development are crucial for maximizing the benefits of double-head grinders.
Operator Training Programs
Implementing comprehensive training programs for operators ensures that staff are proficient in handling and maintaining double-head grinders.
Training should cover operational procedures, safety protocols, and troubleshooting techniques to minimize downtime and optimize productivity.
Certification and Continuous Learning
Encouraging certification programs and continuous learning opportunities fosters a culture of excellence and competency among the workforce.
Staying updated with the latest technological advancements and industry best practices enhances the efficiency and effectiveness of manufacturing operations.
Integration with Lean Manufacturing
Double-head grinders align well with lean manufacturing principles aimed at maximizing value while minimizing waste.
Reducing Waste and Improving Efficiency
By increasing productivity and reducing cycle times, double-head grinders contribute to the elimination of waste in production processes.
Their ability to perform dual operations streamlines workflows and enhances overall manufacturing efficiency.
Just-In-Time Production
The enhanced reliability and performance of double-head grinders support just-in-time production strategies by ensuring timely and consistent output.
This alignment with lean principles helps in maintaining optimal inventory levels and reducing holding costs.
Maintenance and Support
Proper maintenance and support are vital for sustaining the performance and longevity of double-head grinders.
Preventive Maintenance Programs
Establishing preventive maintenance schedules helps in identifying and addressing potential issues before they escalate.
Regular inspections, lubrication, and calibration ensure that the grinders operate smoothly and maintain precision over time.
Technical Support from Suppliers
Partnering with suppliers who provide robust technical support and service agreements enhances the reliability of double-head grinders.
Access to expert assistance and timely repairs minimizes downtime and ensures continuous production flow.
Future Trends in Grinding Technology
The evolution of grinding technology continues to shape the manufacturing landscape.
Automation and Robotics
The integration of automation and robotics in grinding operations is set to increase, offering higher precision and reduced labor costs.
Advanced robotics can handle complex grinding tasks with greater efficiency and consistency, further enhancing production capabilities.
Smart Manufacturing and Industry 4.0
The advent of Industry 4.0 brings smart manufacturing practices that leverage data analytics, Internet of Things (IoT), and artificial intelligence (AI) to optimize grinding processes.
Smart double-head grinders equipped with sensors and connectivity features enable real-time monitoring and predictive maintenance, fostering a more agile and responsive manufacturing environment.
Eco-Friendly Grinding Solutions
Sustainability is becoming a critical focus in manufacturing. Future grinding technologies will prioritize eco-friendly solutions, such as energy-efficient designs and environmentally safe coolant systems.
These advancements will help manufacturers reduce their environmental footprint while maintaining high performance and productivity levels.
Global Impact of Japanese Grinding Innovations
Japanese innovations in grinding technology have a significant impact on the global manufacturing sector.
Standardization and Quality Benchmarks
Japanese manufacturers set global standards for precision and quality, influencing manufacturing practices worldwide.
Their advancements in grinding technology establish benchmarks that drive other manufacturers to adopt similar high standards.
Economic Contributions
The export of advanced grinding machinery contributes to Japan’s economy and supports global manufacturing industries by providing tools that enhance productivity and quality.
Collaborative Global Innovations
Collaboration between Japanese suppliers and international manufacturers fosters global innovation and the sharing of best practices.
These partnerships stimulate advancements that benefit the broader manufacturing community and drive progress across various industries.
Conclusion: Embracing the Double-Head Grinder Revolution
The revolution of double-head grinders in Japanese manufacturing exemplifies the fusion of precision engineering and advanced technology.
These tools offer significant advantages in terms of accuracy, productivity, and operational efficiency, making them invaluable assets in modern manufacturing environments.
However, successful procurement and integration require strategic planning, effective supplier management, and adherence to best practices.
By leveraging the expertise of Japanese suppliers and embracing the technological advancements of double-head grinders, manufacturers can achieve superior quality and maintain a competitive edge in the global market.
As manufacturing continues to evolve with technological advancements and global market dynamics, Japanese double-head grinders will remain a pivotal tool in driving innovation and sustaining excellence.
資料ダウンロード
QCD調達購買管理クラウド「newji」は、調達購買部門で必要なQCD管理全てを備えた、現場特化型兼クラウド型の今世紀最高の購買管理システムとなります。
ユーザー登録
調達購買業務の効率化だけでなく、システムを導入することで、コスト削減や製品・資材のステータス可視化のほか、属人化していた購買情報の共有化による内部不正防止や統制にも役立ちます。
NEWJI DX
製造業に特化したデジタルトランスフォーメーション(DX)の実現を目指す請負開発型のコンサルティングサービスです。AI、iPaaS、および先端の技術を駆使して、製造プロセスの効率化、業務効率化、チームワーク強化、コスト削減、品質向上を実現します。このサービスは、製造業の課題を深く理解し、それに対する最適なデジタルソリューションを提供することで、企業が持続的な成長とイノベーションを達成できるようサポートします。
オンライン講座
製造業、主に購買・調達部門にお勤めの方々に向けた情報を配信しております。
新任の方やベテランの方、管理職を対象とした幅広いコンテンツをご用意しております。
お問い合わせ
コストダウンが利益に直結する術だと理解していても、なかなか前に進めることができない状況。そんな時は、newjiのコストダウン自動化機能で大きく利益貢献しよう!
(Β版非公開)