- お役立ち記事
- “Exploring Japan’s Manufacturing Evolution: Insights Up to 2023”
“Exploring Japan’s Manufacturing Evolution: Insights Up to 2023”
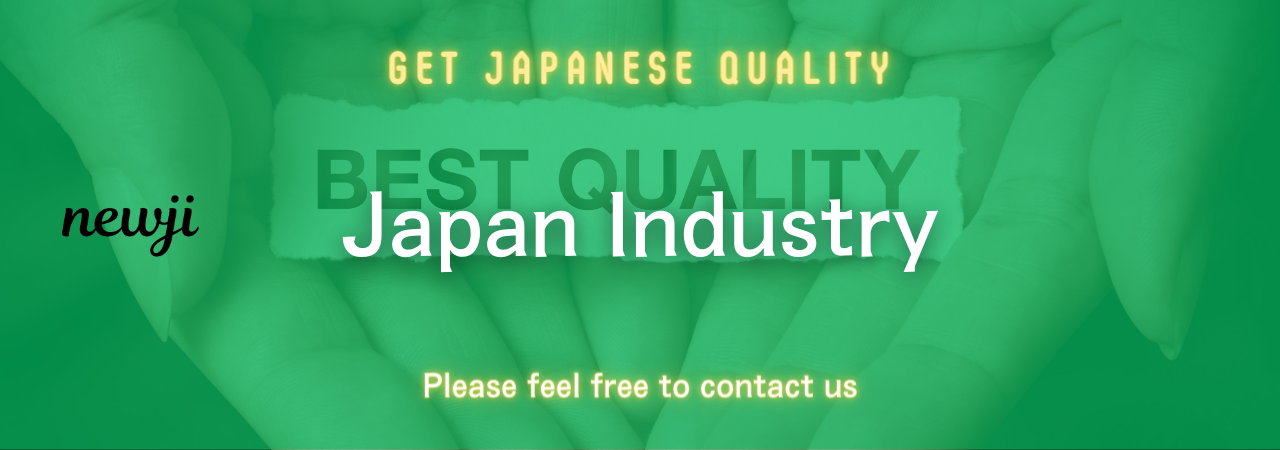
目次
Introduction
Japan’s manufacturing landscape has long held a distinguished position on the global stage, known for its precision, innovation, and efficiency.
By 2023, Japan continues to evolve its manufacturing practices, sustaining a legacy that combines traditional craftsmanship with cutting-edge technologies.
This evolution is not only a testament to Japan’s ability to adapt but also a compelling narrative of growth driven by an unwavering commitment to quality and excellence.
Historical Background of Japanese Manufacturing
Over the decades, Japanese manufacturing has been characterized by an intense focus on process improvements and technological advancements.
From the post-war era’s emphasis on rebuilding and catching up with Western industrial practices, Japan swiftly moved towards innovation-led growth.
The nation introduced methodologies like Kaizen, Just-In-Time (JIT), and the Toyota Production System, which have become globally influential in improving efficiency and minimizing waste.
The Kaizen Approach
Kaizen, meaning ‘continuous improvement,’ is a philosophy ingrained in Japanese manufacturing.
It emphasizes small, incremental changes that collectively lead to significant enhancements in productivity and quality.
This approach has been fundamental to sustaining Japan’s competitive edge, encouraging every employee in a manufacturing facility to contribute ideas for improvement.
Just-In-Time (JIT) Production
JIT is a strategy to optimize inventory levels and streamline production processes.
It reduces waste and improves the efficiency of resource use, aligning production schedules more closely with customer demands.
Japanese companies like Toyota have perfected JIT, allowing them to maintain flexibility and responsiveness in their supply chains.
Advancements in Japanese Manufacturing by 2023
The trajectory of Japanese manufacturing has always been towards integrating modern technologies without losing sight of the foundational principles of quality and efficiency.
Technological Integration and Automation
By 2023, Japan remains at the forefront of integrating Internet of Things (IoT), Artificial Intelligence (AI), and robotics into manufacturing.
Automation has been pivotal in enhancing precision and reducing human errors, thus ensuring consistently high-quality outputs.
Japanese firms are investing heavily in smart factories where interconnected machines and sensors enable real-time data collection and process optimization.
Sustainable Manufacturing Processes
Responding to global environmental concerns, Japanese manufacturers are increasingly focusing on sustainable practices.
Eco-friendly materials and energy-efficient processes are prioritized to minimize environmental impact while meeting international regulations and standards.
Companies are leveraging green technologies to create sustainable production cycles that align with global climate goals.
Digitalization and Data-Driven Decision Making
Digital transformation is another key trend in Japan’s manufacturing evolution.
Manufacturers use data analytics for predictive maintenance, operational efficiency improvements, and lifecycle management.
These insights enable companies to anticipate industry shifts and consumer demands, facilitating better strategic planning and innovation.
Advantages of Partnering with Japanese Manufacturers
Collaborating with Japanese manufacturers presents numerous benefits for international businesses seeking quality and reliability.
High-Quality Standards
Japanese manufacturers have consistently set the bar high in terms of product quality.
Attention to detail and rigorous quality control processes ensure that products meet and often exceed industry standards.
This reputation bolsters consumer trust and enhances brand value for companies sourcing from Japan.
Innovative Capabilities
Japan’s commitment to research and development fuels continuous innovation.
Partnering with Japanese manufacturers enables access to state-of-the-art technologies and processes, granting businesses a competitive edge in their respective markets.
This innovation extends beyond products to include packaging, logistics, and service delivery mechanisms.
Efficient Supply Chain Management
Japan’s emphasis on efficiency translates into well-managed supply chains that minimize disruptions and optimize lead times.
Advanced infrastructure and strategic geographic positioning facilitate smooth logistics and distribution channels, ensuring timely product deliveries.
Challenges and Disadvantages
While there are significant advantages, collaboration with Japanese manufacturers is not without its challenges.
Cultural and Language Barriers
Cultural and linguistic differences can pose communication challenges.
Understanding nuances in Japanese business etiquette and language is crucial for building successful partnerships.
Businesses might require translators or cultural advisors to bridge these gaps and avoid misunderstandings.
High Costs
The pursuit of quality often comes at a higher cost.
Japanese manufacturing does sometimes lead to elevated price points compared to other countries.
However, these costs are often offset by the superior quality and durability of the products, which can reduce long-term expenditures related to returns and customer service issues.
Intellectual Property Concerns
When dealing with innovative manufacturing processes and products, protecting intellectual property (IP) can be a concern.
Companies must ensure robust IP protection measures are in place when engaging with Japanese suppliers to safeguard proprietary information and technologies.
Supplier Negotiation Techniques
Successful negotiation with Japanese suppliers requires an understanding of cultural dynamics and a strategic approach.
Building Relationships
In Japan, business is built on trust and long-term relationships.
Efforts to understand cultural contexts and to invest time in relationship-building activities can significantly enhance negotiations.
Face-to-face meetings, when possible, foster mutual respect and understanding, making future negotiations smoother.
Emphasis on Mutual Benefits
Negotiations should focus on creating win-win scenarios.
Japanese companies value partnerships where both parties benefit and prefer transparent negotiations that promote trust.
Highlighting long-term benefits and shared goals can strengthen bargaining positions.
Patience and Persistence
Japanese negotiation processes can be slower compared to Western standards, characterized by careful consideration and consultation.
Demonstrating patience and an understanding of decision-making hierarchies can lead to fruitful negotiations while avoiding impatience-related missteps.
Current Market Conditions
By 2023, the global market is characterized by changing dynamics that influence Japan’s manufacturing sector.
Trade Policies and Agreements
Trade agreements play a crucial role in shaping market conditions.
Japan’s participation in regional trade pacts such as the Comprehensive and Progressive Agreement for Trans-Pacific Partnership (CPTPP) and bilateral deals enhances its trade access, facilitating external business with Japanese manufacturers.
Impact of Global Supply Chain Shifts
The COVID-19 pandemic has accelerated shifts in global supply chains, prompting companies to reconsider offshoring strategies and increase resilience to disruptions.
Japan’s reputation for reliability makes it an appealing location for companies seeking stable manufacturing partnerships.
Technological and Innovation Trends
Continuous technological advancements define the manufacturing sector’s competitiveness.
Japanese companies that invest in digital transformation, AI, and sustainable technologies are better positioned to respond to global demands and maintain industry leadership.
Best Practices for Engaging with Japanese Manufacturers
To optimize collaborations with Japanese manufacturers, businesses should adopt certain best practices.
Invest in Understanding Japanese Culture
Familiarize yourself with Japanese business culture and etiquette to enhance communication and foster relationships.
Simple gestures, such as bowing and observing silence when appropriate, can convey respect and understanding.
Quality over Cost Considerations
Prioritize quality when considering partnerships with Japanese manufacturers.
While costs might be higher, the long-term benefits and reduced risk of defects and returns justify the investment.
Leverage Local Expertise
Employ local consultants or agents with knowledge of Japanese business practices to bridge cultural and linguistic gaps.
This can facilitate smoother negotiations and ensure all parties are aligned in their business objectives.
Conclusion
Exploring Japan’s manufacturing evolution up to 2023 reveals a dynamic and resilient sector that continues to lead globally through innovation, quality, and efficiency.
While challenges such as cultural barriers and cost considerations exist, the benefits of engaging with Japanese manufacturers are compelling.
By understanding the intricacies of the Japanese market and adopting best practices, international businesses can forge strong, mutually beneficial partnerships that drive growth and innovation.
資料ダウンロード
QCD調達購買管理クラウド「newji」は、調達購買部門で必要なQCD管理全てを備えた、現場特化型兼クラウド型の今世紀最高の購買管理システムとなります。
ユーザー登録
調達購買業務の効率化だけでなく、システムを導入することで、コスト削減や製品・資材のステータス可視化のほか、属人化していた購買情報の共有化による内部不正防止や統制にも役立ちます。
NEWJI DX
製造業に特化したデジタルトランスフォーメーション(DX)の実現を目指す請負開発型のコンサルティングサービスです。AI、iPaaS、および先端の技術を駆使して、製造プロセスの効率化、業務効率化、チームワーク強化、コスト削減、品質向上を実現します。このサービスは、製造業の課題を深く理解し、それに対する最適なデジタルソリューションを提供することで、企業が持続的な成長とイノベーションを達成できるようサポートします。
オンライン講座
製造業、主に購買・調達部門にお勤めの方々に向けた情報を配信しております。
新任の方やベテランの方、管理職を対象とした幅広いコンテンツをご用意しております。
お問い合わせ
コストダウンが利益に直結する術だと理解していても、なかなか前に進めることができない状況。そんな時は、newjiのコストダウン自動化機能で大きく利益貢献しよう!
(Β版非公開)