- お役立ち記事
- Exploring Japan’s Precision Engineering: The Rise of Drilling Machine OEMs
月間77,185名の
製造業ご担当者様が閲覧しています*
*2025年2月28日現在のGoogle Analyticsのデータより
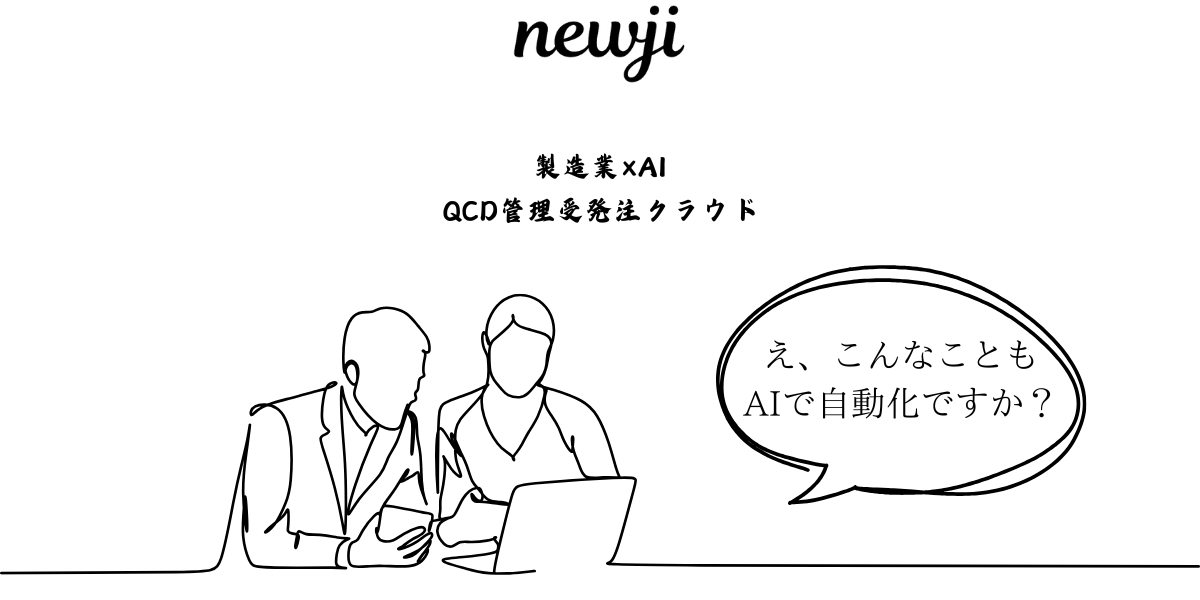
Exploring Japan’s Precision Engineering: The Rise of Drilling Machine OEMs
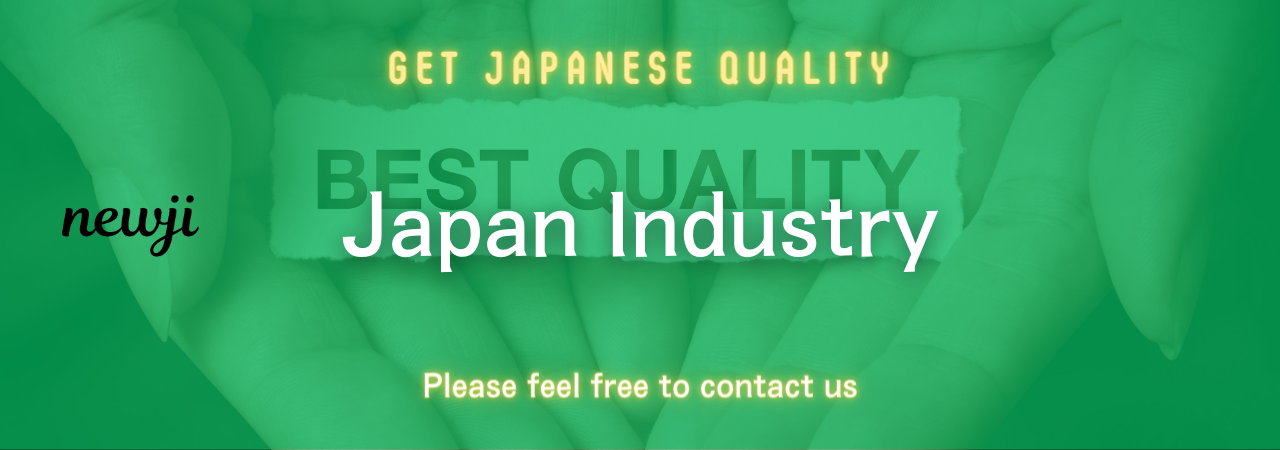
目次
Introduction to Japan’s Precision Engineering
Japan has long been recognized as a global leader in precision engineering, particularly in the manufacturing of drilling machines. The country’s commitment to quality, innovation, and efficiency has positioned its Original Equipment Manufacturers (OEMs) at the forefront of the global market. This article explores the rise of Japan’s drilling machine OEMs, delving into the factors that contribute to their success, the advantages and disadvantages of partnering with Japanese suppliers, effective negotiation techniques, current market conditions, and best practices for procurement and purchasing in this sector.
Understanding the Japanese Drilling Machine OEM Landscape
Japan’s precision engineering sector is characterized by its meticulous attention to detail, advanced technological capabilities, and a strong emphasis on research and development. Japanese drilling machine OEMs produce a wide range of products, from standard models to highly specialized machines tailored to specific industrial needs. These OEMs serve various industries, including automotive, aerospace, electronics, and heavy machinery, demonstrating their versatility and adaptability.
Key Players in the Market
Several Japanese companies have established themselves as leaders in the drilling machine OEM market. Brands like Mitsubishi, DMG Mori, Okuma, and Mazak are renowned for their high-quality equipment and innovative solutions. These companies invest heavily in R&D to stay ahead of technological advancements and maintain their competitive edge.
Technological Advancements Driving the Industry
Japanese OEMs are at the cutting edge of technological innovation in precision engineering. Key advancements include:
– **Automation and Robotics:** Integration of automated systems and robotics enhances precision, reduces human error, and increases production efficiency.
– **CNC Technology:** Computer Numerical Control (CNC) systems allow for highly accurate and repeatable machining processes, essential for complex drilling tasks.
– **Smart Manufacturing:** Implementation of Industry 4.0 principles, including IoT connectivity and data analytics, enables real-time monitoring and optimization of manufacturing processes.
Advantages of Partnering with Japanese Drilling Machine OEMs
Collaborating with Japanese drilling machine OEMs offers numerous benefits for international procurement and purchasing departments. Understanding these advantages can help companies make informed decisions when selecting suppliers.
Unmatched Quality and Reliability
Japanese OEMs are synonymous with high quality and reliability. Rigorous quality control processes ensure that drilling machines meet stringent standards and perform consistently over time. This reliability minimizes downtime and maintenance costs, offering long-term value to purchasers.
Innovative Technology and Customization
Japanese manufacturers excel in innovation, continuously developing new technologies to improve drilling precision and efficiency. Additionally, they offer customization options to meet specific client requirements, allowing for tailored solutions that address unique industrial challenges.
Strong After-Sales Support
Japanese OEMs provide comprehensive after-sales support, including installation, training, maintenance, and technical assistance. This support is crucial for ensuring the smooth operation of drilling machines and maximizing their lifespan.
Efficient Supply Chain Management
Japanese companies are known for their efficient supply chain management practices, which ensure timely delivery of products and spare parts. This efficiency reduces lead times and helps maintain production schedules for buyers.
Challenges and Disadvantages
While there are significant advantages to partnering with Japanese drilling machine OEMs, there are also challenges and potential drawbacks to consider.
Higher Costs
Japanese drilling machines often come with a higher price tag compared to competitors from other regions. The advanced technology and superior quality contribute to these costs, which may be a barrier for some buyers.
Language and Cultural Barriers
Differences in language and business culture can pose challenges in communication and negotiation. Misunderstandings may arise, potentially affecting the procurement process and ongoing relationships.
Longer Lead Times
The high demand for Japanese drilling machines can result in longer lead times for delivery. This delay can impact production schedules, especially for companies operating on tight timelines.
Dependency on Supplier
Relying heavily on a single supplier can create dependency, which may be risky if the supplier faces production issues or changes in business strategy. Diversifying suppliers can mitigate this risk but adds complexity to the procurement process.
Effective Supplier Negotiation Techniques
Negotiating with Japanese drilling machine OEMs requires a strategic approach that respects cultural norms and leverages effective negotiation tactics. Here are some techniques to enhance negotiation outcomes.
Build Long-Term Relationships
Japanese business culture emphasizes long-term relationships and trust. Investing time in building strong, respectful relationships with suppliers can lead to better negotiation outcomes and more favorable terms.
Understand Cultural Nuances
Respect for hierarchy, indirect communication, and patience are key elements of Japanese business culture. Demonstrating cultural awareness and sensitivity can facilitate smoother negotiations and foster mutual respect.
Emphasize Mutual Benefits
Focus on creating win-win scenarios where both parties benefit. Highlight how the partnership can lead to increased sales, technological advancements, or market expansion for the OEM, alongside your own procurement goals.
Be Prepared and Well-Informed
Thoroughly research the OEM’s products, market position, and business practices before entering negotiations. Being well-informed allows you to make compelling arguments and address potential concerns effectively.
Leverage Volume and Long-Term Commitments
Offering commitments for larger volumes or long-term contracts can provide leverage in negotiations. OEMs may be more willing to offer discounts or favorable terms in exchange for consistent and significant orders.
Current Market Conditions
Understanding the current market conditions is essential for effective procurement and purchasing strategies. The drilling machine OEM market in Japan is influenced by various factors that impact supply and demand dynamics.
Global Demand for Precision Engineering
The increasing demand for precision-engineered components in industries such as automotive and electronics drives the need for high-quality drilling machines. Japanese OEMs are well-positioned to capitalize on this demand due to their technological expertise.
Technological Disruption and Innovation
Rapid advancements in automation, robotics, and digital manufacturing require continuous innovation from OEMs. Companies that fail to keep pace with these technological changes may lose their competitive edge.
Supply Chain Challenges
Global supply chain disruptions, such as those caused by the COVID-19 pandemic, have affected the availability and delivery of drilling machines. Japanese OEMs have implemented strategies to enhance supply chain resilience, but challenges remain.
Environmental Regulations and Sustainability
Increasing emphasis on sustainability and environmental regulations influences the design and manufacturing processes of drilling machines. OEMs must adapt to these changes by developing eco-friendly technologies and practices.
Best Practices for Procurement and Purchasing
Adopting best practices in procurement and purchasing can enhance the effectiveness of partnerships with Japanese drilling machine OEMs. Here are some recommended strategies.
Conduct Comprehensive Supplier Evaluation
Evaluate potential suppliers based on criteria such as quality, reliability, technological capabilities, financial stability, and after-sales support. A thorough assessment ensures that you partner with OEMs that align with your business needs and standards.
Establish Clear Communication Channels
Maintain open and transparent communication with suppliers. Clearly articulate your requirements, expectations, and any changes in your needs. Regular communication helps prevent misunderstandings and ensures alignment throughout the procurement process.
Implement Robust Contract Management
Develop detailed contracts that outline terms and conditions, including pricing, delivery schedules, quality standards, and warranties. Effective contract management helps safeguard your interests and provides a framework for addressing any disputes or issues that arise.
Foster Collaborative Relationships
Encourage collaboration and knowledge sharing with your suppliers. Joint initiatives, such as co-development of new technologies or process improvements, can drive innovation and mutual growth.
Utilize Technology and Data Analytics
Leverage technology and data analytics to monitor supplier performance, manage inventory, and optimize procurement processes. Tools such as Supplier Relationship Management (SRM) systems can enhance visibility and control over your supply chain.
Case Studies: Success Stories with Japanese OEMs
Examining real-world examples of successful partnerships with Japanese drilling machine OEMs provides valuable insights into effective procurement strategies.
Automotive Industry Collaboration
A leading automotive manufacturer partnered with a Japanese drilling machine OEM to enhance its production line. By integrating advanced CNC drilling machines, the company achieved higher precision and reduced production time. The collaboration led to the development of customized solutions tailored to the manufacturer’s specific needs, resulting in improved product quality and increased market competitiveness.
Aerospace Manufacturing Partnership
An aerospace components supplier collaborated with a Japanese OEM to implement automated drilling systems. The introduction of robotics and real-time monitoring technologies enabled the supplier to achieve greater efficiency and consistent quality. The partnership also facilitated knowledge transfer, allowing the supplier to adopt best practices in precision engineering and automation.
Future Outlook
The future of Japan’s drilling machine OEMs looks promising, with continued growth driven by technological advancements and expanding global demand. However, OEMs must navigate challenges such as global competition, supply chain disruptions, and the need for sustainable practices.
Embracing Industry 4.0
Japanese OEMs are increasingly adopting Industry 4.0 technologies, including IoT, artificial intelligence, and machine learning, to enhance the capabilities of drilling machines. These technologies enable smarter manufacturing processes, predictive maintenance, and improved operational efficiency.
Expanding Global Presence
To remain competitive, Japanese OEMs are expanding their global footprint through strategic partnerships, acquisitions, and the establishment of overseas manufacturing facilities. This expansion helps mitigate supply chain risks and better serve international markets.
Focus on Sustainability
Sustainable manufacturing practices are becoming a priority for Japanese OEMs. Developing energy-efficient drilling machines, reducing waste, and complying with environmental regulations are essential for long-term success and meeting the evolving demands of customers and regulators.
Conclusion
Japan’s precision engineering prowess has significantly contributed to the rise of its drilling machine OEMs on the global stage. The combination of unwavering quality, innovative technology, and efficient supply chain management makes Japanese OEMs attractive partners for international procurement and purchasing departments.
While there are challenges such as higher costs and cultural barriers, the advantages of partnering with Japanese suppliers often outweigh these drawbacks. By adopting effective negotiation techniques, understanding current market conditions, and implementing best practices, companies can successfully leverage the strengths of Japanese drilling machine OEMs to enhance their manufacturing capabilities and achieve their business objectives.
As the industry continues to evolve, Japanese OEMs are well-positioned to adapt to new technological advancements and market demands, ensuring their continued leadership in precision engineering. For companies seeking reliable, high-quality drilling machine solutions, Japan remains a premier destination for procurement and purchasing excellence.
資料ダウンロード
QCD管理受発注クラウド「newji」は、受発注部門で必要なQCD管理全てを備えた、現場特化型兼クラウド型の今世紀最高の受発注管理システムとなります。
ユーザー登録
受発注業務の効率化だけでなく、システムを導入することで、コスト削減や製品・資材のステータス可視化のほか、属人化していた受発注情報の共有化による内部不正防止や統制にも役立ちます。
NEWJI DX
製造業に特化したデジタルトランスフォーメーション(DX)の実現を目指す請負開発型のコンサルティングサービスです。AI、iPaaS、および先端の技術を駆使して、製造プロセスの効率化、業務効率化、チームワーク強化、コスト削減、品質向上を実現します。このサービスは、製造業の課題を深く理解し、それに対する最適なデジタルソリューションを提供することで、企業が持続的な成長とイノベーションを達成できるようサポートします。
製造業ニュース解説
製造業、主に購買・調達部門にお勤めの方々に向けた情報を配信しております。
新任の方やベテランの方、管理職を対象とした幅広いコンテンツをご用意しております。
お問い合わせ
コストダウンが利益に直結する術だと理解していても、なかなか前に進めることができない状況。そんな時は、newjiのコストダウン自動化機能で大きく利益貢献しよう!
(β版非公開)