- お役立ち記事
- Exploring the Craftsmanship Behind Japanese Teppanyaki Plate OEM Manufacturing
Exploring the Craftsmanship Behind Japanese Teppanyaki Plate OEM Manufacturing
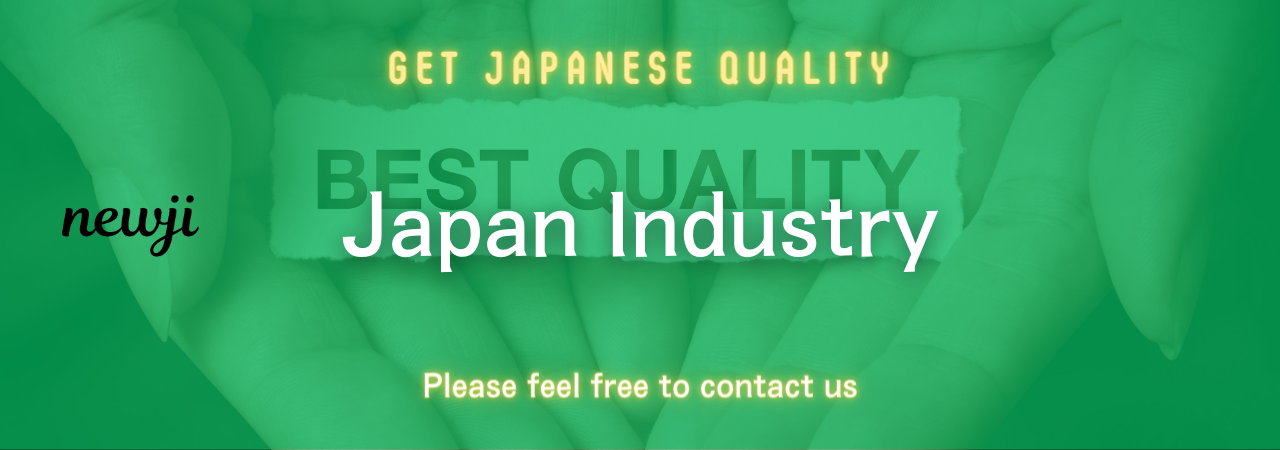
目次
Introduction to Japanese Teppanyaki Plate OEM Manufacturing
Japanese teppanyaki plates are renowned for their exceptional craftsmanship, durability, and aesthetic appeal. OEM (Original Equipment Manufacturer) manufacturing in Japan plays a pivotal role in maintaining these high standards. By collaborating with Japanese OEM manufacturers, companies worldwide can access top-tier products that meet stringent quality requirements. This article delves into the intricacies of Japanese teppanyaki plate OEM manufacturing, exploring the craftsmanship, procurement strategies, supplier negotiation techniques, and best practices essential for successful partnerships.
Advantages of Partnering with Japanese OEM Manufacturers
Unmatched Quality and Craftsmanship
Japanese manufacturers are celebrated for their meticulous attention to detail and commitment to quality. The production processes incorporate traditional techniques combined with modern technology, ensuring that each teppanyaki plate meets the highest standards. This dedication results in products that are not only functional but also aesthetically pleasing, catering to both domestic and international markets.
Advanced Technology and Innovation
Japan is at the forefront of manufacturing innovation. OEM manufacturers leverage state-of-the-art machinery and automation to enhance production efficiency and consistency. This technological prowess enables manufacturers to produce high volumes without compromising on quality, meeting the demands of global markets effectively.
Reliable Supply Chain and Logistics
Japanese OEM manufacturers have well-established supply chains that ensure timely delivery of products. Their logistics infrastructure is designed to handle large orders efficiently, minimizing delays and ensuring that products reach their destinations as scheduled. This reliability is crucial for businesses that depend on timely inventory replenishment.
Strong Reputation and Trust
Partnering with Japanese OEM manufacturers bolsters a company’s reputation. The “Made in Japan” label is synonymous with quality and reliability, enhancing the company’s brand image in competitive markets. This trust factor can be a significant advantage in attracting and retaining customers.
Challenges and Disadvantages
Higher Production Costs
While the quality of Japanese OEM products is superior, it often comes with higher production costs compared to manufacturers in other regions. These costs are attributed to advanced technology, skilled labor, and high-quality materials. Companies must evaluate whether the premium cost aligns with their budget and pricing strategies.
Language and Cultural Barriers
Collaborating with Japanese manufacturers may present language and cultural challenges. Miscommunications can arise due to differences in language, business practices, and work culture. Overcoming these barriers requires effective communication strategies and, in some cases, the assistance of bilingual representatives or translation services.
Lead Times
Japanese OEM manufacturers may have longer lead times, especially during peak seasons or when managing complex orders. Businesses must plan their procurement schedules meticulously to accommodate these lead times, ensuring that inventory levels are adequately maintained to meet market demands.
Procurement and Purchasing Considerations
Understanding Supplier Capabilities
Before engaging with a Japanese OEM manufacturer, it is essential to assess their capabilities. This includes evaluating their production capacity, technological infrastructure, quality control measures, and ability to meet specific design requirements. Detailed assessments help in selecting a partner that aligns with the company’s operational needs and strategic goals.
Cost Analysis and Budgeting
Conducting a comprehensive cost analysis is crucial. This involves not only the production costs but also additional expenses such as shipping, tariffs, and potential wastage. Creating a detailed budget ensures that the procurement process remains financially viable and sustainable in the long term.
Quality Assurance and Standards
Japanese manufacturers adhere to stringent quality standards. It is imperative for companies to understand these standards and how they align with their own quality assurance processes. Establishing clear quality metrics and regular inspections can help maintain consistency and uphold product standards.
Legal and Regulatory Compliance
Navigating the legal and regulatory landscape is essential when procuring from Japanese OEM manufacturers. This includes understanding import/export regulations, intellectual property protections, and compliance with international trade laws. Legal counsel may be necessary to ensure that all agreements and transactions adhere to relevant laws and regulations.
Understanding Market Conditions
Global Demand for Teppanyaki Plates
The global market for teppanyaki plates is influenced by trends in the restaurant industry, especially the popularity of Japanese cuisine. Understanding the demand dynamics, seasonal fluctuations, and emerging markets can help companies make informed procurement decisions and adjust their strategies accordingly.
Competitive Landscape
Analyzing the competitive landscape involves identifying key players, their market share, and their product offerings. This insight helps companies position their products effectively, differentiating them based on quality, design, or other unique selling points derived from the OEM manufacturing process.
Economic Factors
Economic conditions in both the manufacturing region and target markets can impact procurement strategies. Factors such as currency exchange rates, inflation, and economic growth rates influence pricing, costs, and overall profitability. Staying informed about these economic indicators aids in making strategic purchasing decisions.
Supplier Negotiation Techniques
Building Strong Relationships
Establishing a strong, trust-based relationship with Japanese OEM manufacturers is fundamental. Regular communication, site visits, and cultural understanding contribute to a positive partnership. Building rapport helps in negotiating better terms and fosters long-term collaboration.
Effective Communication
Clear and concise communication is vital during negotiations. Companies should articulate their requirements, expectations, and constraints transparently. Active listening and understanding the supplier’s perspective can lead to mutually beneficial agreements.
Leveraging Volume and Long-Term Contracts
Negotiating based on order volume or committing to long-term contracts can provide leverage in securing favorable terms. Manufacturers are more likely to offer discounts or better payment terms when there is assurance of consistent business.
Flexibility and Compromise
Flexibility in negotiations can lead to successful outcomes. Being open to compromises on certain aspects, such as delivery schedules or minor design changes, can help in reaching agreements that satisfy both parties.
Best Practices for Successful OEM Partnerships
Thorough Due Diligence
Conducting comprehensive due diligence before selecting an OEM partner is essential. This includes evaluating the manufacturer’s financial stability, reputation, production capabilities, and previous client feedback. Due diligence minimizes risks and ensures a reliable partnership.
Clear Contractual Agreements
Drafting clear and detailed contractual agreements is crucial. Contracts should outline all aspects of the partnership, including product specifications, pricing, delivery schedules, quality standards, and dispute resolution mechanisms. Well-defined contracts prevent misunderstandings and provide a legal framework for addressing issues.
Regular Performance Reviews
Implementing regular performance reviews helps in monitoring the manufacturer’s adherence to agreed-upon standards. These reviews assess quality, delivery times, and responsiveness, allowing for timely adjustments and continuous improvement.
Collaboration on Product Development
Collaborating with OEM manufacturers on product development can lead to innovative and superior products. Sharing insights, feedback, and market trends fosters a collaborative environment where both parties contribute to enhancing product offerings.
Quality Control and Factory Efficiency
Implementing Robust Quality Control Systems
Japanese OEM manufacturers employ rigorous quality control systems to ensure product excellence. These systems include multiple inspection stages, from raw material evaluation to final product testing. Adopting similar quality control measures enhances product reliability and customer satisfaction.
Enhancing Factory Efficiency
Efficient factory operations are achieved through lean manufacturing principles and continuous improvement practices. Streamlining processes, reducing waste, and optimizing resource utilization lead to higher productivity and cost savings, benefiting both the manufacturer and the procurement partner.
Leveraging Automation
Automation plays a significant role in modern manufacturing. Incorporating automated machinery and processes reduces human error, increases production speed, and maintains consistency. Japanese manufacturers are adept at integrating automation, ensuring high efficiency and scalability in production.
Logistics and Supply Chain Management
Optimizing Supply Chain Processes
Effective supply chain management ensures the smooth flow of materials and products from manufacturers to end-users. This involves coordinating procurement, production, transportation, and distribution processes to minimize delays and reduce costs.
Implementing Just-In-Time Inventory
The just-in-time (JIT) inventory system minimizes inventory holding costs by aligning production schedules closely with demand forecasts. Implementing JIT requires precise coordination with OEM manufacturers to ensure timely delivery of components and finished products.
Risk Management in Supply Chains
Identifying and mitigating risks in supply chains are essential for maintaining stability. This includes managing potential disruptions such as natural disasters, geopolitical issues, and supply shortages. Developing contingency plans and diversifying suppliers can enhance supply chain resilience.
Case Studies and Field Perspectives
Success Story: Enhancing Product Quality through Collaboration
A leading international restaurant chain partnered with a Japanese OEM manufacturer to develop high-quality teppanyaki plates. Through collaborative design sessions and regular quality assessments, the company achieved superior product performance, resulting in increased customer satisfaction and market share.
Overcoming Challenges: Navigating Cultural Barriers
A mid-sized procurement firm faced challenges in communicating design specifications to a Japanese manufacturer due to language differences. By employing bilingual staff and conducting regular virtual meetings, the company successfully streamlined communication, leading to timely and accurate product deliveries.
Innovation through Technology Integration
An electronics company sought to integrate advanced features into their teppanyaki plates. Collaborating with a Japanese OEM manufacturer equipped with cutting-edge technology, they introduced smart plates with temperature control and interactive displays, differentiating their products in a competitive market.
Conclusion
Exploring the craftsmanship behind Japanese teppanyaki plate OEM manufacturing reveals a blend of traditional expertise and modern innovation. Partnering with Japanese OEM manufacturers offers numerous advantages, including superior quality, advanced technology, and a reliable supply chain. However, navigating higher costs, cultural differences, and longer lead times requires strategic planning and effective communication. By understanding market conditions, employing robust procurement strategies, and adhering to best practices, businesses can leverage the benefits of Japanese OEM manufacturing to enhance their product offerings and achieve long-term success.
資料ダウンロード
QCD調達購買管理クラウド「newji」は、調達購買部門で必要なQCD管理全てを備えた、現場特化型兼クラウド型の今世紀最高の購買管理システムとなります。
ユーザー登録
調達購買業務の効率化だけでなく、システムを導入することで、コスト削減や製品・資材のステータス可視化のほか、属人化していた購買情報の共有化による内部不正防止や統制にも役立ちます。
NEWJI DX
製造業に特化したデジタルトランスフォーメーション(DX)の実現を目指す請負開発型のコンサルティングサービスです。AI、iPaaS、および先端の技術を駆使して、製造プロセスの効率化、業務効率化、チームワーク強化、コスト削減、品質向上を実現します。このサービスは、製造業の課題を深く理解し、それに対する最適なデジタルソリューションを提供することで、企業が持続的な成長とイノベーションを達成できるようサポートします。
オンライン講座
製造業、主に購買・調達部門にお勤めの方々に向けた情報を配信しております。
新任の方やベテランの方、管理職を対象とした幅広いコンテンツをご用意しております。
お問い合わせ
コストダウンが利益に直結する術だと理解していても、なかなか前に進めることができない状況。そんな時は、newjiのコストダウン自動化機能で大きく利益貢献しよう!
(Β版非公開)