- お役立ち記事
- Exploring the Cutting-Edge of Japanese Manufacturing: Unveiling Aluminum Deep Drawing Technology
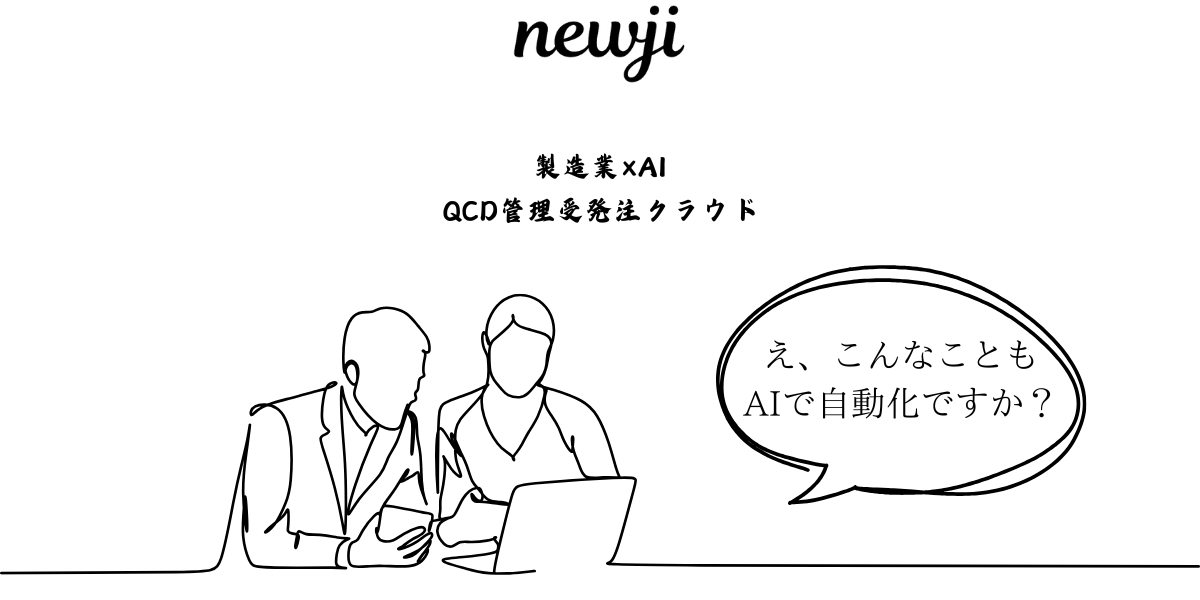
Exploring the Cutting-Edge of Japanese Manufacturing: Unveiling Aluminum Deep Drawing Technology
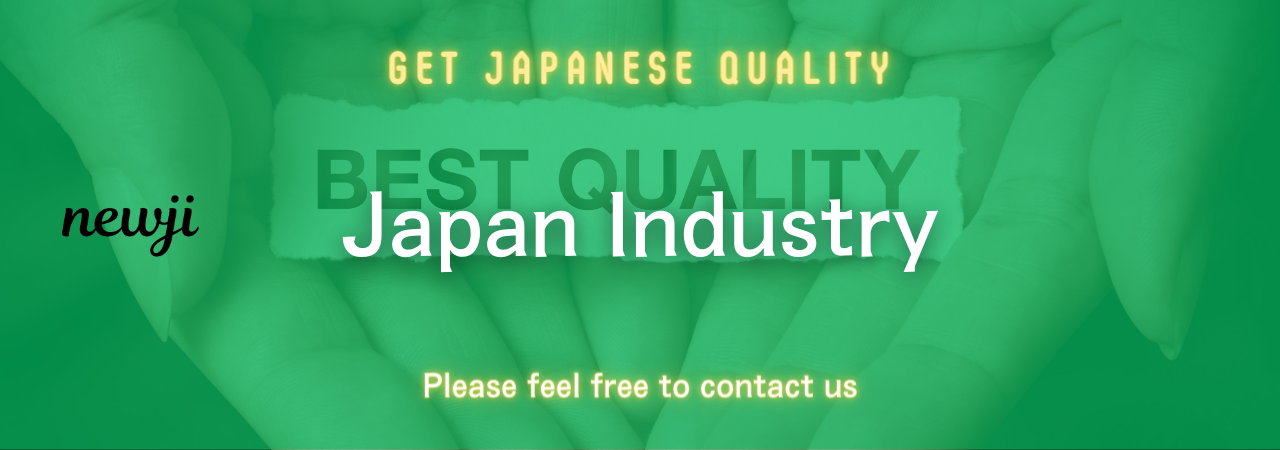
目次
Introduction to Aluminum Deep Drawing Technology
Aluminum deep drawing technology represents a significant advancement in the manufacturing sector, particularly within Japanese industries renowned for their precision and innovation. This manufacturing process involves reshaping flat aluminum sheets into complex three-dimensional forms without compromising the material’s integrity. The efficiency and versatility of deep drawing make it an essential technique for producing components used in automotive, aerospace, electronics, and packaging industries.
The Evolution of Japanese Manufacturing Excellence
Japan’s manufacturing prowess has long been attributed to its commitment to quality, continuous improvement, and technological innovation. The development of aluminum deep drawing technology is a testament to this legacy, showcasing how Japanese manufacturers have leveraged advanced engineering principles to enhance production capabilities. By integrating cutting-edge machinery with meticulous process control, Japanese companies have set benchmarks for precision and reliability in the global market.
Key Advantages of Aluminum Deep Drawing
Enhanced Material Utilization
One of the primary advantages of aluminum deep drawing is the efficient use of raw materials. The process minimizes waste by precisely shaping aluminum sheets into desired forms, reducing excess material that often results from traditional manufacturing methods.
Cost-Effective Production
Aluminum deep drawing offers a cost-effective solution for producing high-volume components. The automation and scalability of the process allow manufacturers to achieve significant economies of scale, lowering the overall production costs per unit.
Superior Surface Finish and Dimensional Accuracy
Japanese manufacturers excel in achieving impeccable surface finishes and tight dimensional tolerances through deep drawing. This precision is critical for applications where aesthetic quality and component fit are paramount, such as in consumer electronics and automotive interiors.
Versatility in Design
The flexibility of aluminum deep drawing enables the creation of complex shapes and intricate designs that would be challenging to achieve with other manufacturing techniques. This versatility expands the range of possible applications, fostering innovation and product differentiation.
Challenges Associated with Aluminum Deep Drawing
Material Limitations
While aluminum is highly malleable, it presents challenges related to strain hardening and material thinning during the deep drawing process. Controlling these factors is essential to maintain the structural integrity of the final product.
High Initial Investment
Implementing aluminum deep drawing technology requires significant upfront investment in specialized machinery and tooling. This expense can be a barrier for smaller manufacturers looking to adopt the technology.
Technical Expertise and Training
Achieving optimal results with deep drawing necessitates a high level of technical expertise. Manufacturers must invest in training skilled personnel who understand the nuances of the process to ensure quality and efficiency.
Procurement and Purchasing in Japanese Manufacturing
Building Strong Supplier Relationships
In the realm of international procurement, establishing robust relationships with Japanese suppliers is crucial. Japanese companies prioritize long-term partnerships based on mutual trust, reliability, and consistent quality delivery.
Negotiation Techniques
Effective negotiation with Japanese suppliers involves understanding cultural nuances and business etiquettes. Key strategies include showing respect, being patient, and demonstrating a commitment to long-term collaboration rather than short-term gains.
Quality Assurance and Control
Japanese manufacturers are renowned for their stringent quality control measures. When procuring aluminum deep-drawn components, it is essential to align with suppliers who adhere to international quality standards and are willing to implement rigorous inspection protocols.
Market Conditions and Trends
Increasing Demand for Lightweight Materials
The global shift towards lightweight materials in industries like automotive and aerospace drives the demand for aluminum deep drawing. Aluminum’s lightweight nature, combined with its strength, makes it an ideal choice for applications aiming to improve fuel efficiency and reduce emissions.
Technological Advancements
Advancements in automation, robotics, and computer-aided design (CAD) have significantly enhanced the capabilities of aluminum deep drawing. These technologies enable more precise manufacturing processes, reducing errors and increasing production speed.
Sustainability and Environmental Impact
Sustainability has become a critical consideration in manufacturing. Aluminum’s recyclability and the efficiency of deep drawing processes align with environmental goals, making it a preferred material for eco-conscious manufacturers.
Best Practices in Aluminum Deep Drawing
Material Selection and Preparation
Choosing the right aluminum alloy is fundamental to the success of the deep drawing process. Factors such as strength, formability, and corrosion resistance must be considered to match the specific application requirements. Proper material preparation, including annealing and surface treatment, further enhances the material’s suitability for deep drawing.
Tooling and Equipment Optimization
Investing in high-quality tooling and machinery is essential for achieving consistent and precise results. Regular maintenance and calibration of equipment ensure optimal performance and prolong the lifespan of tooling components.
Process Monitoring and Control
Implementing real-time monitoring systems allows manufacturers to track critical parameters such as temperature, force, and strain during the deep drawing process. This proactive approach facilitates immediate adjustments, maintaining process stability and preventing defects.
Continuous Improvement and Lean Manufacturing
Adopting continuous improvement methodologies, such as Lean and Kaizen, fosters a culture of ongoing enhancement. By systematically identifying and eliminating waste, manufacturers can streamline operations, reduce costs, and improve overall efficiency.
Supplier Negotiation Techniques
Understanding Supplier Motivations
Successful negotiations begin with a deep understanding of the supplier’s motivations and objectives. Japanese suppliers often prioritize quality, consistency, and long-term partnerships over immediate gains. Tailoring negotiation strategies to align with these priorities can enhance collaboration and mutual benefit.
Transparent Communication
Clear and honest communication is vital in negotiations. Articulating your company’s requirements, expectations, and constraints helps build trust and ensures that both parties are aligned towards common goals.
Flexible Contract Terms
Offering flexibility in contract terms, such as payment schedules, delivery timelines, and order volumes, can make negotiations smoother. Demonstrating willingness to accommodate the supplier’s business needs fosters goodwill and strengthens the partnership.
Leveraging Cultural Insights
Cultural awareness plays a significant role in negotiations with Japanese suppliers. Understanding and respecting Japanese business customs, such as formality, punctuality, and consensus-building, can enhance rapport and facilitate more effective negotiations.
Quality Control in Aluminum Deep Drawing
Implementing Robust Inspection Processes
Ensuring the quality of deep-drawn aluminum components requires comprehensive inspection processes at various stages of production. Techniques such as dimensional measurement, surface finish assessment, and structural integrity testing are essential to verify compliance with specifications.
Collaborative Quality Management
Collaborating closely with suppliers on quality management initiatives can lead to significant improvements. Jointly developing quality standards, conducting regular audits, and sharing best practices foster a culture of excellence and continuous improvement.
Utilizing Advanced Quality Tools
Incorporating advanced quality tools like Statistical Process Control (SPC) and Six Sigma methodologies can enhance quality management. These tools provide data-driven insights, enabling manufacturers to identify and address quality issues proactively.
Logistics and Supply Chain Considerations
Efficient Supply Chain Management
Managing the supply chain effectively is crucial for maintaining the flow of materials required for aluminum deep drawing. This involves coordinating with suppliers, optimizing inventory levels, and ensuring timely delivery of components to meet production schedules.
Risk Mitigation Strategies
Implementing risk mitigation strategies helps address potential disruptions in the supply chain. Diversifying suppliers, maintaining safety stock, and developing contingency plans are essential measures to ensure continuity in production.
Leveraging Technology for Supply Chain Visibility
Adopting technologies such as Enterprise Resource Planning (ERP) systems and supply chain management software enhances visibility and coordination across the supply chain. These tools facilitate real-time tracking of shipments, inventory levels, and production status, enabling more informed decision-making.
Production Management and Efficiency
Optimizing Production Processes
Streamlining production processes through lean manufacturing principles can significantly enhance efficiency. Identifying and eliminating bottlenecks, reducing cycle times, and improving workflow contribute to higher productivity and cost savings.
Automation and Robotics in Deep Drawing
Integrating automation and robotics into the deep drawing process increases precision and repeatability. Automated systems can handle repetitive tasks with greater accuracy, reduce human error, and allow for higher production volumes.
Employee Training and Development
Investing in employee training ensures that the workforce is skilled and knowledgeable about the latest techniques and technologies in aluminum deep drawing. Continuous development programs enhance operational competence and foster a culture of excellence.
Production Engineering Considerations
Design for Manufacturability
Collaborating with design teams to ensure components are designed for manufacturability is essential. Simplifying designs, minimizing tight tolerances, and selecting appropriate materials can facilitate more efficient deep drawing processes.
Tool Design and Maintenance
The design and maintenance of tooling play a critical role in the quality and efficiency of the deep drawing process. Custom-designed tools that match specific application requirements ensure optimal performance and extend the lifespan of tooling components.
Process Innovation and Development
Encouraging innovation in production engineering leads to the development of new techniques and technologies that enhance the deep drawing process. Investing in research and development fosters breakthroughs that can provide a competitive advantage in the market.
Quality Control Strategies
Establishing Quality Standards
Defining clear quality standards is fundamental to ensuring consistent product quality. These standards should align with industry benchmarks and customer expectations, providing a foundation for all quality assurance activities.
Incorporating Statistical Analysis
Using statistical analysis in quality control allows manufacturers to identify trends, detect anomalies, and implement corrective actions proactively. This data-driven approach enhances the ability to maintain high-quality standards consistently.
Continuous Improvement in Quality Processes
Adopting a mindset of continuous improvement encourages ongoing enhancements in quality control processes. Regularly reviewing and refining quality procedures ensures they remain effective and aligned with evolving industry standards and customer requirements.
Factory Efficiency and Automation
Implementing Lean Manufacturing Techniques
Lean manufacturing techniques focus on eliminating waste, optimizing processes, and enhancing overall efficiency. Practices such as Just-In-Time (JIT) production, value stream mapping, and 5S organization contribute to a more streamlined and productive factory environment.
Integrating Advanced Automation Technologies
Advanced automation technologies, including robotics, artificial intelligence, and machine learning, revolutionize factory operations. These technologies enhance production speed, accuracy, and flexibility, allowing manufacturers to meet diverse and dynamic market demands.
Energy Efficiency and Sustainability
Enhancing energy efficiency within the factory contributes to sustainability goals and operational cost reductions. Implementing energy-efficient machines, optimizing production schedules, and utilizing renewable energy sources are effective strategies for achieving these objectives.
Best Practices in Procurement and Purchasing
Strategic Sourcing
Strategic sourcing involves a comprehensive approach to procurement, focusing on long-term supplier relationships, cost optimization, and value creation. By evaluating suppliers based on multiple criteria, manufacturers can select partners that align with their strategic goals and quality standards.
Supplier Evaluation and Selection
A rigorous supplier evaluation process ensures that selected partners meet necessary quality, reliability, and sustainability criteria. This process typically includes assessing supplier certifications, conducting site visits, and reviewing performance history.
Negotiating Favorable Terms
Effective negotiation strategies aim to achieve mutually beneficial agreements. This includes negotiating pricing, payment terms, delivery schedules, and service level agreements that support the manufacturer’s operational needs and financial objectives.
Risk Management in Procurement
Identifying and mitigating risks in procurement is essential for maintaining supply chain stability. Strategies include diversifying suppliers, implementing robust contract terms, and continuously monitoring supplier performance to address potential issues proactively.
Leveraging Technology in Procurement and Purchasing
Adopting Procurement Software Solutions
Utilizing procurement software streamlines purchasing processes, enhances visibility, and improves decision-making. Features such as automated purchase orders, supplier management, and spend analysis contribute to more efficient and effective procurement operations.
Utilizing Data Analytics
Data analytics provides valuable insights into purchasing trends, supplier performance, and cost drivers. Leveraging these insights enables manufacturers to make informed decisions, optimize procurement strategies, and identify opportunities for cost savings.
Implementing E-Procurement Systems
E-procurement systems facilitate the digitalization of purchasing processes, improving efficiency and accuracy. These systems enable seamless communication with suppliers, real-time tracking of orders, and enhanced transparency in procurement activities.
Conclusion
Aluminum deep drawing technology exemplifies the innovation and excellence inherent in Japanese manufacturing. By harnessing advanced techniques, maintaining stringent quality control, and fostering strong supplier relationships, manufacturers can achieve significant advantages in terms of cost, quality, and efficiency. Embracing best practices in procurement and purchasing, coupled with continuous improvement and technological integration, positions companies to capitalize on the benefits of aluminum deep drawing. As the global market continues to evolve, staying abreast of technological advancements and market trends will be crucial for sustaining competitive advantage and driving long-term success in the manufacturing sector.
資料ダウンロード
QCD調達購買管理クラウド「newji」は、調達購買部門で必要なQCD管理全てを備えた、現場特化型兼クラウド型の今世紀最高の購買管理システムとなります。
ユーザー登録
調達購買業務の効率化だけでなく、システムを導入することで、コスト削減や製品・資材のステータス可視化のほか、属人化していた購買情報の共有化による内部不正防止や統制にも役立ちます。
NEWJI DX
製造業に特化したデジタルトランスフォーメーション(DX)の実現を目指す請負開発型のコンサルティングサービスです。AI、iPaaS、および先端の技術を駆使して、製造プロセスの効率化、業務効率化、チームワーク強化、コスト削減、品質向上を実現します。このサービスは、製造業の課題を深く理解し、それに対する最適なデジタルソリューションを提供することで、企業が持続的な成長とイノベーションを達成できるようサポートします。
オンライン講座
製造業、主に購買・調達部門にお勤めの方々に向けた情報を配信しております。
新任の方やベテランの方、管理職を対象とした幅広いコンテンツをご用意しております。
お問い合わせ
コストダウンが利益に直結する術だと理解していても、なかなか前に進めることができない状況。そんな時は、newjiのコストダウン自動化機能で大きく利益貢献しよう!
(Β版非公開)