- お役立ち記事
- Exploring the Impact of “Three-Phase Common” Technology in Japanese Manufacturing Innovation
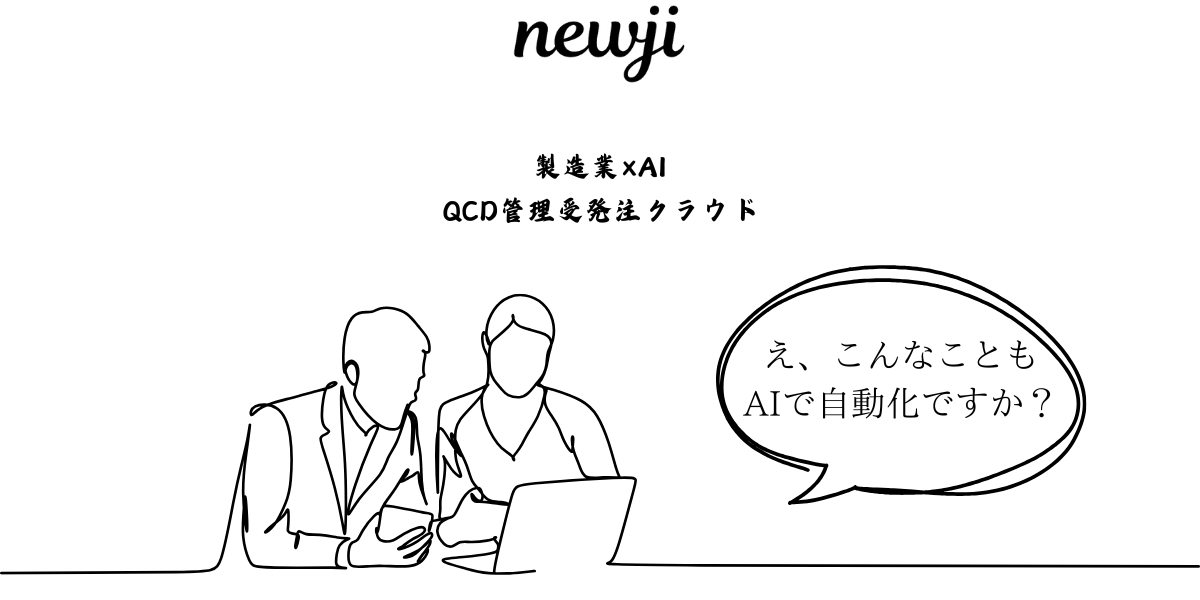
Exploring the Impact of “Three-Phase Common” Technology in Japanese Manufacturing Innovation
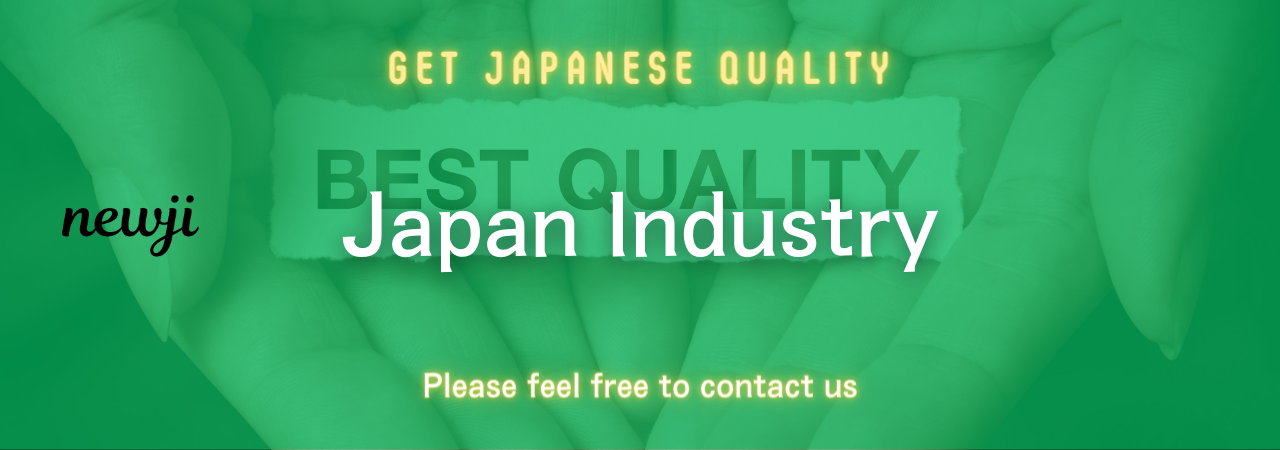
目次
Introduction to Three-Phase Common Technology in Japanese Manufacturing
Three-Phase Common technology has emerged as a pivotal innovation in the Japanese manufacturing sector. This technological advancement integrates three critical phases of manufacturing processes to streamline operations, enhance efficiency, and drive quality improvements. By adopting this approach, Japanese manufacturers can maintain their competitive edge in the global market.
The Components of Three-Phase Common Technology
Phase One: Planning and Design
The first phase focuses on meticulous planning and design. Japanese manufacturers employ advanced software tools and collaborative platforms to ensure that every aspect of the product design aligns with market demands and production capabilities. This phase emphasizes precision, reducing the likelihood of errors that can lead to costly delays or rework.
Phase Two: Production and Implementation
The second phase involves the actual production and implementation of the designed product. Utilizing state-of-the-art machinery and automation technologies, manufacturers can achieve higher productivity levels and maintain consistency in product quality. This phase also incorporates lean manufacturing principles to minimize waste and optimize resource utilization.
Phase Three: Quality Control and Feedback
The final phase centers on rigorous quality control and continuous feedback. Japanese manufacturers implement comprehensive quality assurance protocols to detect and rectify defects promptly. Additionally, feedback loops from customers and production data drive ongoing improvements, fostering a culture of excellence and innovation.
Advantages of Three-Phase Common Technology
Enhanced Efficiency
Integrating the three phases leads to significant improvements in operational efficiency. By aligning planning, production, and quality control, manufacturers can reduce downtime, streamline workflows, and achieve faster turnaround times.
Improved Quality
The emphasis on quality control at every stage ensures that products meet the highest standards. This commitment to quality enhances customer satisfaction and strengthens the brand reputation of Japanese manufacturers in the global market.
Cost Reduction
Three-Phase Common technology facilitates better resource management and waste reduction. By optimizing processes and minimizing errors, manufacturers can lower production costs, making their products more competitive in price-sensitive markets.
Disadvantages and Challenges
High Initial Investment
Implementing Three-Phase Common technology requires significant upfront investment in advanced machinery, software, and training. This financial barrier can be challenging for smaller manufacturers with limited budgets.
Complex Integration
Integrating the three phases seamlessly demands careful coordination and sophisticated management systems. Achieving this integration can be complex, especially for organizations with entrenched processes and legacy systems.
Skill Requirements
The adoption of advanced technologies necessitates a skilled workforce capable of operating and maintaining new systems. Japanese manufacturers must invest in training and development to bridge the skill gap and ensure smooth implementation.
Supplier Negotiation Techniques Utilizing Three-Phase Common Technology
Building Strong Partnerships
Leveraging Three-Phase Common technology, Japanese manufacturers can foster stronger relationships with suppliers. Transparent communication and collaborative planning ensure that suppliers are aligned with production goals and quality standards.
Negotiating Better Terms
With enhanced efficiency and reduced costs, manufacturers are in a better position to negotiate favorable terms with suppliers. Volume discounts, flexible payment terms, and priority delivery schedules become attainable, benefiting both parties.
Ensuring Consistent Quality
By incorporating quality control measures throughout the production process, manufacturers can set clear expectations with suppliers regarding product specifications and standards. This clarity reduces the risk of defects and ensures a consistent supply of high-quality materials.
Market Conditions Impacting Three-Phase Common Technology Adoption
Global Competition
In a highly competitive global market, Japanese manufacturers must continuously innovate to maintain their market position. Three-Phase Common technology provides the necessary framework for sustained innovation and competitiveness.
Technological Advancements
Rapid advancements in technology drive the need for modern manufacturing solutions. Adopting Three-Phase Common technology enables manufacturers to stay ahead of technological trends and leverage new tools for improved productivity.
Economic Factors
Economic fluctuations can influence investment decisions in manufacturing technology. During periods of economic growth, manufacturers are more likely to invest in innovations like Three-Phase Common technology to scale operations and capitalize on market opportunities.
Best Practices for Implementing Three-Phase Common Technology
Comprehensive Training Programs
Investing in training ensures that employees are proficient in using new technologies and understand the integrated processes. Comprehensive training programs minimize resistance to change and facilitate a smoother transition.
Incremental Implementation
Adopting Three-Phase Common technology incrementally allows manufacturers to manage the transition effectively. Phased implementation reduces disruption to ongoing operations and enables continuous assessment and adjustment.
Continuous Improvement
Embracing a mindset of continuous improvement ensures that the benefits of Three-Phase Common technology are sustained over time. Regular reviews, feedback incorporation, and process optimization drive long-term success and innovation.
Case Studies: Success Stories in Japanese Manufacturing
Toyota’s Lean Manufacturing Integration
Toyota has successfully integrated Three-Phase Common technology into its renowned lean manufacturing system. By aligning planning, production, and quality control, Toyota has achieved remarkable efficiency and product quality, setting industry benchmarks.
Panasonic’s Automation Advancements
Panasonic’s adoption of advanced automation technologies within the Three-Phase Common framework has led to significant productivity gains. Their focus on continuous improvement and quality assurance has solidified their reputation for reliable and high-quality products.
Hitachi’s Supplier Collaboration
Hitachi exemplifies effective supplier collaboration through Three-Phase Common technology. By working closely with suppliers during the planning and production phases, Hitachi ensures timely delivery and adherence to strict quality standards, enhancing overall supply chain performance.
Future Trends and Developments
Integration with Industry 4.0
The convergence of Three-Phase Common technology with Industry 4.0 initiatives will further revolutionize Japanese manufacturing. Enhanced connectivity, data analytics, and automation will drive unprecedented levels of efficiency and innovation.
Sustainability Initiatives
Sustainability is becoming increasingly important in manufacturing. Three-Phase Common technology supports sustainable practices by optimizing resource usage, reducing waste, and enabling the production of eco-friendly products.
Artificial Intelligence and Machine Learning
Incorporating artificial intelligence and machine learning into the Three-Phase Common framework will enhance predictive maintenance, quality control, and decision-making processes, driving further advancements in manufacturing performance.
Conclusion
Three-Phase Common technology represents a transformative approach in Japanese manufacturing, integrating planning, production, and quality control to achieve superior efficiency and product quality. While the implementation presents challenges such as high initial investment and complex integration, the benefits it offers in terms of cost reduction, enhanced quality, and improved supplier relationships make it a valuable investment for manufacturers aiming to thrive in the competitive global landscape. By adopting best practices and staying abreast of future trends, Japanese manufacturers can continue to lead the way in manufacturing innovation and excellence.
資料ダウンロード
QCD調達購買管理クラウド「newji」は、調達購買部門で必要なQCD管理全てを備えた、現場特化型兼クラウド型の今世紀最高の購買管理システムとなります。
ユーザー登録
調達購買業務の効率化だけでなく、システムを導入することで、コスト削減や製品・資材のステータス可視化のほか、属人化していた購買情報の共有化による内部不正防止や統制にも役立ちます。
NEWJI DX
製造業に特化したデジタルトランスフォーメーション(DX)の実現を目指す請負開発型のコンサルティングサービスです。AI、iPaaS、および先端の技術を駆使して、製造プロセスの効率化、業務効率化、チームワーク強化、コスト削減、品質向上を実現します。このサービスは、製造業の課題を深く理解し、それに対する最適なデジタルソリューションを提供することで、企業が持続的な成長とイノベーションを達成できるようサポートします。
オンライン講座
製造業、主に購買・調達部門にお勤めの方々に向けた情報を配信しております。
新任の方やベテランの方、管理職を対象とした幅広いコンテンツをご用意しております。
お問い合わせ
コストダウンが利益に直結する術だと理解していても、なかなか前に進めることができない状況。そんな時は、newjiのコストダウン自動化機能で大きく利益貢献しよう!
(Β版非公開)