- お役立ち記事
- Exploring the Precision of Japanese Manufacturing Through Cavity Design
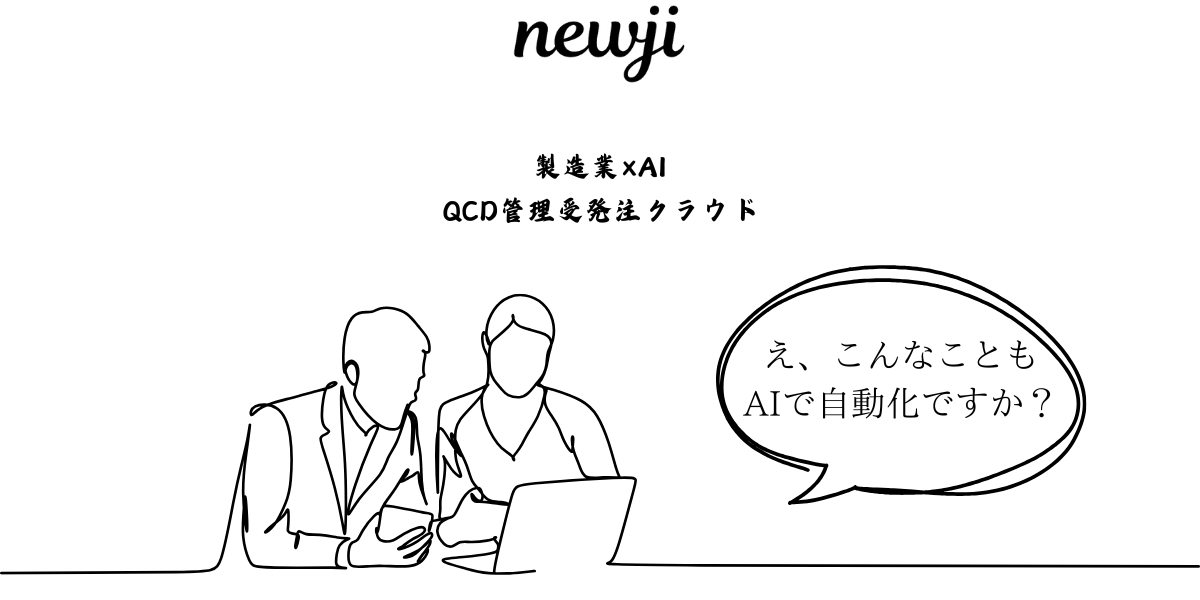
Exploring the Precision of Japanese Manufacturing Through Cavity Design
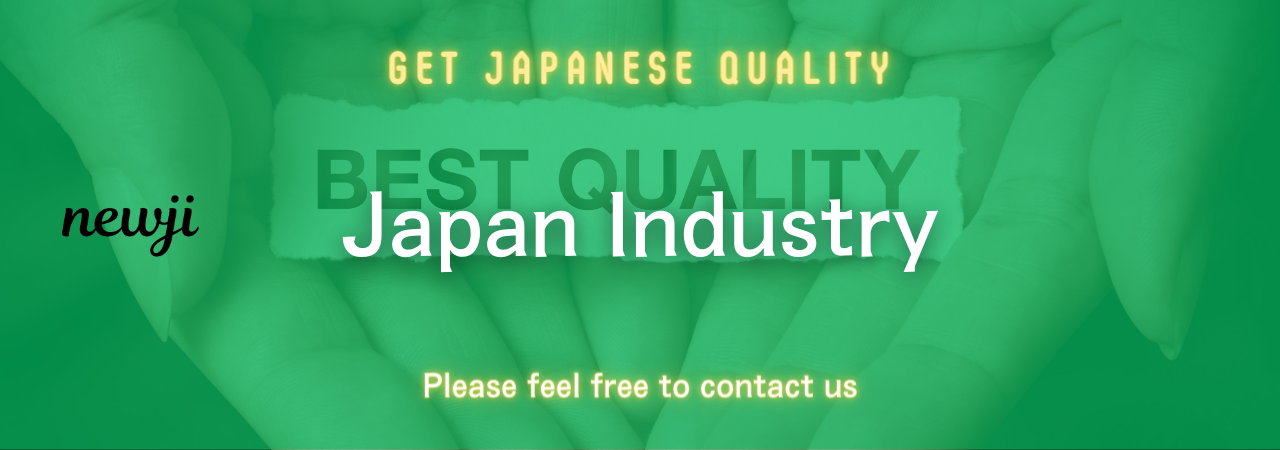
目次
Introduction to Japanese Manufacturing Precision
Japanese manufacturing is renowned globally for its precision, reliability, and innovative approaches to problem-solving.
One of the critical aspects that highlight these features is the meticulous design and execution of cavity design processes.
Cavity design, an integral part of mold-making in industrial manufacturing, is a critical determinant of the overall product quality and production efficiency.
Manufacturers worldwide often look to Japanese techniques for inspiration and benchmarking due to the high standards they maintain.
From automotives to consumer electronics, Japanese manufacturing practices leave an indelible mark on global industries.
This article aims to delve into the rich technical culture of Japanese manufacturing through the lens of cavity design, leveraging practical insights from procurement and purchasing, while exploring supplier negotiation techniques, market conditions, best practices, and the associated advantages and disadvantages.
The Fundamentals of Cavity Design
Cavity design is a cornerstone of injection molding, a process used to produce a vast array of products by injecting molten materials into a mold.
Cavities are essentially the hollow spaces within the mold that dictate the shape and dimensions of the final product.
A well-designed cavity ensures high product quality, repeatability, and efficiency.
Core Principles
The principles of cavity design include understanding the material behavior, precise measurements, and the ability to predict potential issues such as shrinkage and warpage.
Japanese manufacturers use computer-aided design (CAD) and computer-aided engineering (CAE) tools extensively to achieve exceptional precision.
Simulation tools are often employed to predict and mitigate issues, ensuring that the design meets stringent standards even before the mold is manufactured.
Key Materials
Material selection is another critical aspect.
Japanese manufacturers are known for their thorough understanding of materials, from metals to plastics, ensuring that the chosen material aligns perfectly with the intended use and environmental conditions.
Different materials behave differently under heat and pressure; understanding these subtleties is crucial for impeccable cavity design.
Advantages of Japanese Cavity Design
High Precision and Consistency
Japanese manufacturing is synonymous with high precision.
Their cavity designs are no exception.
The use of advanced technologies and stringent quality controls ensures each mold is produced with minimal variations.
This level of precision translates to consistent product quality, enhancing brand reputation and customer satisfaction.
Innovation and Continuous Improvement
The concept of Kaizen, or continuous improvement, is deeply embedded in Japanese manufacturing culture.
This philosophy drives incremental enhancements in processes and products, leading to improved efficiency and reduced waste over time.
Constantly testing and refining cavity designs epitomizes this approach.
Superior Quality Control
Quality control is not an afterthought but an integral part of the manufacturing process in Japan.
Statistical process control (SPC) and other quality management systems ensure that even the slightest deviations are detected and corrected promptly.
This proactive approach minimizes the risk of defects, leading to superior end products.
Enhanced Durability and Longevity
Products made with Japanese cavity design techniques often exhibit remarkable durability and longevity.
This is achieved through meticulous attention to detail, high-grade materials, and rigorous testing.
For industries such as automotive and aerospace where safety and reliability are paramount, this becomes a significant advantage.
Challenges and Disadvantages
While the benefits of Japanese cavity design are manifold, there are some challenges and drawbacks one must consider.
High Initial Costs
The advanced technologies and high-quality materials used in Japanese cavity design can lead to higher initial costs.
For startups or companies with limited budgets, this can be a significant barrier.
However, these costs often pay off in the long term through increased efficiency and reduced waste.
Complexity and Learning Curve
The high precision and advanced techniques in Japanese manufacturing require specialized skills and knowledge.
There can be a steep learning curve for companies and personnel not familiar with these methodologies.
Training and adaptation time must be factored into the implementation plan.
Supply Chain Issues
Relying heavily on Japanese suppliers can sometimes lead to supply chain constraints, especially during global disruptions such as natural disasters or economic downturns.
Diversification and developing a robust supply chain strategy are essential to mitigate these risks.
Supplier Negotiation Techniques
Effective supplier negotiation is crucial in leveraging the high precision of Japanese cavity designs.
Here are some techniques that can help:
Building Long-term Relationships
Japanese business culture places a strong emphasis on long-term relationships.
Approaching negotiations with a focus on building trust and mutual benefit rather than short-term gains can result in more favorable terms and better collaboration.
Understanding Cultural Nuances
Understanding and respecting cultural nuances can significantly impact negotiation outcomes.
Politeness, patience, and an appreciation for detailed discussions are key elements when dealing with Japanese suppliers.
Data-driven Negotiations
Using data and factual information can strengthen your negotiation position.
Japanese suppliers appreciate detailed and well-structured proposals backed by data, which show that you have done your homework and understand the technicalities involved.
Flexibility and Adaptation
While maintaining your non-negotiables, showing flexibility and willingness to adapt can lead to more successful negotiations.
This may include agreeing to phased payments or providing detailed feedback to help improve the process.
Best Practices in Cavity Design
Adopting best practices in cavity design can ensure you get the most out of Japanese manufacturing precision.
Collaborative Design Process
Engaging in a collaborative design process where both the client and the manufacturer work closely can lead to better outcomes.
This includes sharing detailed specifications, conducting joint reviews, and iterative feedback sessions.
Prototyping and Testing
Before committing to full-scale production, prototyping and testing are essential.
Japanese manufacturers often use rapid prototyping techniques to create initial models.
This allows for early identification of potential issues and necessary adjustments.
Regular Audits and Reviews
Regular audits and design reviews ensure ongoing adherence to quality standards.
Spotting deviations early helps in making necessary corrections without significant disruptions.
Embracing Technology
Leveraging cutting-edge technologies such as AI and machine learning can further enhance the cavity design process.
These technologies can predict potential issues with higher accuracy and suggest advanced solutions.
Current Market Conditions
Understanding the current market conditions is essential for making informed decisions.
Technological Advancements
The rapidly evolving technology landscape continues to influence cavity design.
AI, IoT, and advanced robotics have further enhanced precision and efficiency in Japanese manufacturing.
Global Supply Chain Dynamics
The global supply chain has faced unprecedented disruptions, impacting manufacturing processes.
Japanese companies have exhibited resilience by quickly adapting and optimizing their operations to withstand these challenges.
Environmental Sustainability
There is an increasing focus on sustainable manufacturing.
Japanese companies are at the forefront of adopting eco-friendly practices and green technologies in their production processes.
This trend is likely to continue and even expand in the future.
Conclusion: Embracing Japanese Precision
The precision of Japanese manufacturing, especially through meticulous cavity design, offers numerous advantages such as superior quality, durability, and innovation.
However, it also presents some challenges such as high initial costs and supply chain complexities.
Adopting effective supplier negotiation techniques and best practices can unlock the full potential of Japanese manufacturing precision.
As market conditions continue to evolve, staying informed about technological advancements and global dynamics will be key to maintaining a competitive edge.
Embrace the precision of Japanese manufacturing, and you’ll be well on your way to achieving unparalleled quality and efficiency in your production processes.
資料ダウンロード
QCD調達購買管理クラウド「newji」は、調達購買部門で必要なQCD管理全てを備えた、現場特化型兼クラウド型の今世紀最高の購買管理システムとなります。
ユーザー登録
調達購買業務の効率化だけでなく、システムを導入することで、コスト削減や製品・資材のステータス可視化のほか、属人化していた購買情報の共有化による内部不正防止や統制にも役立ちます。
NEWJI DX
製造業に特化したデジタルトランスフォーメーション(DX)の実現を目指す請負開発型のコンサルティングサービスです。AI、iPaaS、および先端の技術を駆使して、製造プロセスの効率化、業務効率化、チームワーク強化、コスト削減、品質向上を実現します。このサービスは、製造業の課題を深く理解し、それに対する最適なデジタルソリューションを提供することで、企業が持続的な成長とイノベーションを達成できるようサポートします。
オンライン講座
製造業、主に購買・調達部門にお勤めの方々に向けた情報を配信しております。
新任の方やベテランの方、管理職を対象とした幅広いコンテンツをご用意しております。
お問い合わせ
コストダウンが利益に直結する術だと理解していても、なかなか前に進めることができない状況。そんな時は、newjiのコストダウン自動化機能で大きく利益貢献しよう!
(Β版非公開)