- お役立ち記事
- FA equipment operation optimization and automation through the introduction of FA equipment DX
FA equipment operation optimization and automation through the introduction of FA equipment DX
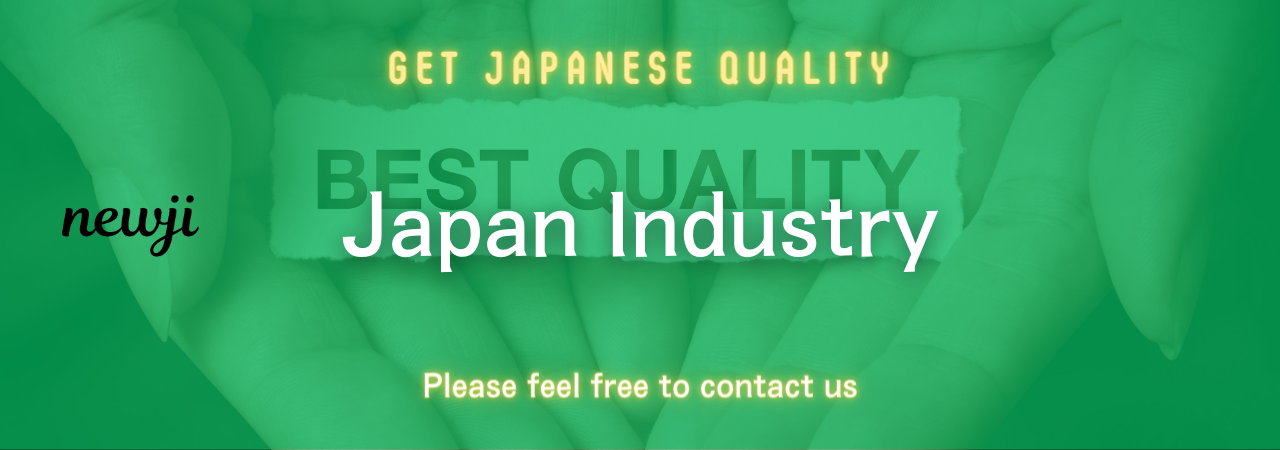
In today’s rapidly evolving industrial landscape, the optimization and automation of Factory Automation (FA) equipment have become paramount. Through the adoption of FA equipment DX (Digital Transformation), factories can significantly enhance efficiency and productivity. This article delves into how integrating DX into FA equipment can lead to streamlined operations and transformative benefits for manufacturing processes.
目次
Understanding FA Equipment DX
What is FA Equipment DX?
FA equipment DX refers to the integration of digital technologies into factory automation systems to improve their performance and efficiency. This involves the utilization of advanced tools like IoT (Internet of Things), AI (Artificial Intelligence), and machine learning to enhance the functionality of existing automation equipment. By doing so, factories can achieve a higher level of operational excellence and adaptability.
The Importance of Digital Transformation
Digital transformation in FA equipment is crucial because it helps factories stay competitive in a global market. With increasing demands for faster production times and higher-quality outputs, traditional methods of factory automation often fall short. By leveraging DX, factories can adopt new strategies for predictive maintenance, real-time data analysis, and enhanced decision-making processes.
Steps to Implement FA Equipment DX
Assess Current Systems
Before embarking on the journey of digital transformation, it is essential to evaluate the current state of your factory automation systems. This assessment should identify areas where digital tools can make the most impact. Look for bottlenecks or inefficiencies in the current workflow that could be improved with the integration of new technologies.
Select Appropriate Technologies
Choosing the right digital tools is crucial for successful implementation. IoT sensors can be used to monitor equipment in real-time, while AI algorithms can predict equipment failures before they happen. Machine learning can optimize scheduling and resource allocation, ensuring that manufacturing processes run smoothly.
Develop a Strategic Plan
A well-structured plan is necessary to guide the digital transformation process. This plan should outline the objectives, timelines, and resources required for the integration of DX into FA equipment. Stakeholders should be involved in the planning process to ensure alignment with overall business goals.
Benefits of FA Equipment DX
Increased Operational Efficiency
One of the most significant benefits of FA equipment DX is the increase in operational efficiency. By automating routine tasks and optimizing workflows, factories can reduce production times and cut down on waste. This not only saves costs but also increases the overall output of the factory.
Enhanced Predictive Maintenance
Digital transformation allows for the implementation of predictive maintenance strategies. With the help of IoT sensors and AI, factories can monitor the health of their equipment in real-time. Predictive maintenance can predict failures before they occur, reducing downtime and extending the lifespan of machinery.
Improved Data Analytics
The integration of digital tools into FA equipment facilitates enhanced data collection and analysis. Real-time data analytics provides valuable insights into the performance of various systems. This data can be used to make informed decisions, optimize processes, and improve product quality.
Scalability and Flexibility
digital transformation makes it easier for factories to scale their operations. Whether it’s increasing production capacity or diversifying the range of products, DX provides the flexibility needed to adapt to changing market demands. This scalability ensures that factories can grow without significant disruptions.
Challenges in Implementing FA Equipment DX
High Initial Investment
One of the biggest challenges of implementing digital transformation in FA equipment is the high initial investment. Purchasing new technologies, upgrading existing systems, and training staff requires substantial financial resources. However, this investment often pays off in the long run through increased efficiency and reduced operational costs.
Data Security Concerns
With the integration of digital tools, data security becomes a critical concern. Factories must ensure that their networks are secure and that sensitive information is protected from cyber threats. This may require additional investment in cybersecurity measures and regular security audits.
Resistance to Change
Implementing FA equipment DX often involves significant changes to existing workflows. Workers may resist these changes due to fear of job displacement or unfamiliarity with new technologies. It’s essential to provide adequate training and communicate the long-term benefits to gain employee buy-in.
Future Trends in FA Equipment DX
Integration of Advanced AI
As AI technology continues to evolve, its integration into FA equipment will bring about even more innovative solutions. Advanced AI can further optimize processes, enhance decision-making capabilities, and provide more accurate predictive maintenance.
Expansion of IoT Networks
The expansion of IoT networks will enable more comprehensive monitoring and control of factory equipment. With more devices interconnected, factories can achieve greater efficiency and responsiveness in their operations.
Adoption of Edge Computing
Edge computing, which processes data closer to the source rather than relying on centralized data centers, is set to play a significant role in FA equipment DX. This approach reduces latency and increases the speed of data processing, leading to faster and more reliable automation systems.
The introduction of FA equipment DX is revolutionizing the industrial sector. By incorporating advanced digital technologies into factory automation systems, manufacturers can enhance efficiency, reduce costs, and stay competitive in a rapidly changing market. Despite challenges such as high initial investment and data security concerns, the benefits of digital transformation far outweigh the drawbacks. With the continuous evolution of AI, IoT, and edge computing, the future of FA equipment DX looks promising, paving the way for smarter and more efficient factories.
資料ダウンロード
QCD調達購買管理クラウド「newji」は、調達購買部門で必要なQCD管理全てを備えた、現場特化型兼クラウド型の今世紀最高の購買管理システムとなります。
ユーザー登録
調達購買業務の効率化だけでなく、システムを導入することで、コスト削減や製品・資材のステータス可視化のほか、属人化していた購買情報の共有化による内部不正防止や統制にも役立ちます。
NEWJI DX
製造業に特化したデジタルトランスフォーメーション(DX)の実現を目指す請負開発型のコンサルティングサービスです。AI、iPaaS、および先端の技術を駆使して、製造プロセスの効率化、業務効率化、チームワーク強化、コスト削減、品質向上を実現します。このサービスは、製造業の課題を深く理解し、それに対する最適なデジタルソリューションを提供することで、企業が持続的な成長とイノベーションを達成できるようサポートします。
オンライン講座
製造業、主に購買・調達部門にお勤めの方々に向けた情報を配信しております。
新任の方やベテランの方、管理職を対象とした幅広いコンテンツをご用意しております。
お問い合わせ
コストダウンが利益に直結する術だと理解していても、なかなか前に進めることができない状況。そんな時は、newjiのコストダウン自動化機能で大きく利益貢献しよう!
(Β版非公開)