- お役立ち記事
- Facility/equipment failure diagnosis methods and remaining life prediction using physical models, and deployment to digital twins
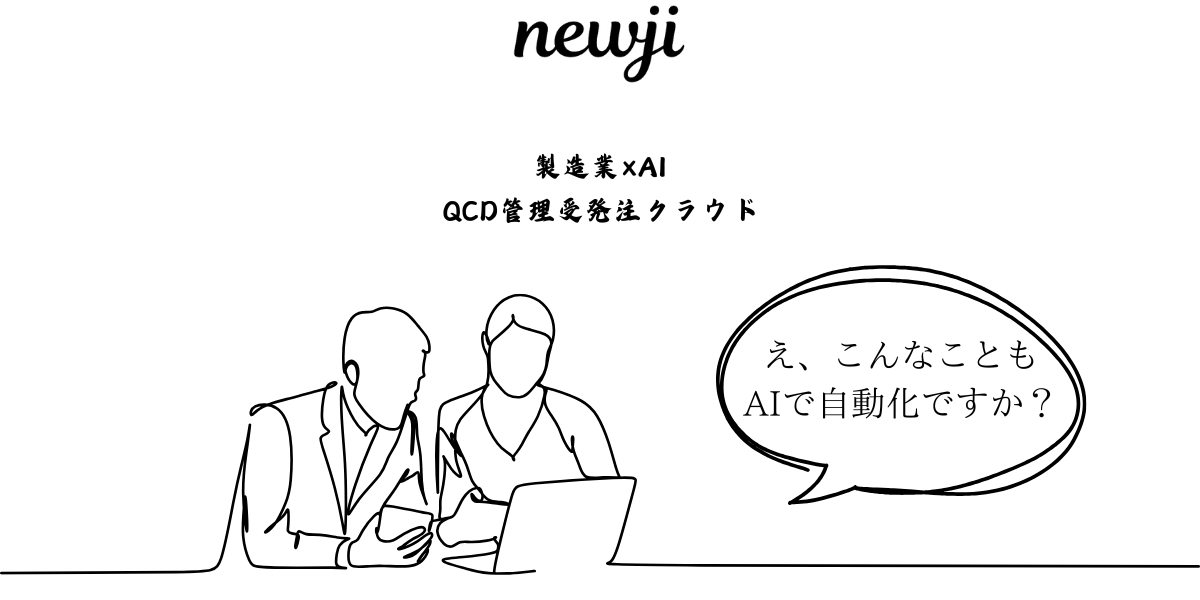
Facility/equipment failure diagnosis methods and remaining life prediction using physical models, and deployment to digital twins
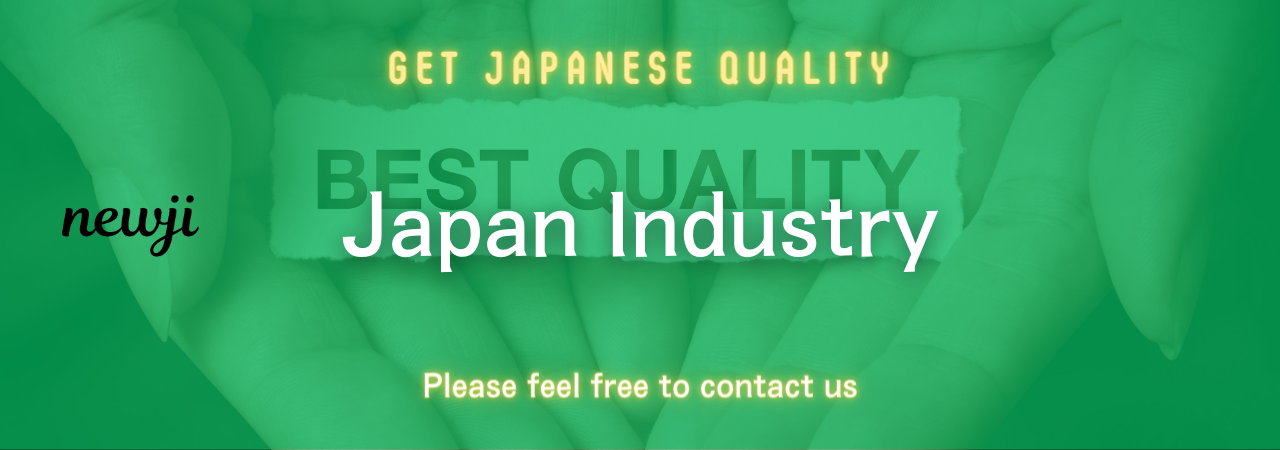
目次
Understanding Facility and Equipment Failure Diagnosis
Facility and equipment failure can be a significant challenge for businesses across various industries.
The ability to diagnose failures accurately and predict the remaining lifespan of equipment is crucial for maintaining efficiency and reducing downtime.
Physical models and digital twins are modern technologies that offer promising solutions to these problems.
The process of diagnosing facility and equipment failures involves identifying the reasons for breakdowns and taking corrective actions.
Traditional methods rely on regular maintenance and inspections, which are often time-consuming and may not always prevent unexpected failures.
The Role of Physical Models in Failure Diagnosis
Physical models play a critical role in simulating the real-world operations of machinery and equipment.
They are mathematical representations that reflect the behavior and dynamics of equipment under different operational conditions.
These models help in understanding the possible causes of failures by analyzing various parameters such as stress, temperature, and load.
By using physical models, engineers can replicate the operational environment of the equipment and conduct virtual tests.
This enables them to predict how and when a piece of equipment might fail.
Consequently, more informed maintenance schedules can be developed, potentially extending the equipment’s lifespan and reducing repair costs.
Predicting Remaining Life with Physical Models
One of the primary benefits of employing physical models is the ability to predict the remaining life of equipment.
This capability is essential for strategic planning and budgeting, as it allows businesses to allocate resources effectively.
The prediction involves using the data generated from the physical models combined with historical performance data.
Advanced algorithms assess patterns and trends to estimate how long the equipment can continue functioning without failures.
This proactive approach ensures that components are replaced before they fail, thus avoiding unexpected down-time and associated costs.
Introducing Digital Twins
Digital twins enhance the capabilities of physical models by creating a virtual replica of an asset or system.
This digital simulation incorporates real-time data from sensors and monitoring devices, providing a comprehensive view of the equipment’s condition and performance.
The concept of digital twins integrates various technologies like the Internet of Things (IoT), artificial intelligence (AI), and machine learning to simulate, predict, and optimize operations.
These technologies help in accurate fault detection and failure prediction by providing a detailed analysis of the system’s current and future states.
Deployment of Digital Twins for Failure Diagnosis
Digital twins are increasingly deployed across industries to address facility and equipment failure diagnosis and prediction.
Their implementation involves the continuous collection of data from sensors attached to equipment, which is then analyzed in real-time.
This real-time analysis allows for the immediate identification of potential issues and the implementation of solutions before actual failures occur.
Furthermore, digital twins enable the visualization of different scenarios, helping decision-makers to choose the best corrective measures.
The deployment of digital twins involves several stages, including the creation of an accurate digital model, real-time synchronization of data, and the use of analytics to interpret data for decision-making.
Organizations can thus maintain optimal operational efficiency and anticipate maintenance needs effectively.
Benefits of Digital Twins in Facility Management
Digital twins offer several benefits to facility management and operations.
Firstly, they improve the accuracy of failure prediction and maintenance planning, ensuring that maintenance tasks are performed only when necessary.
Secondly, digital twins enhance system optimization by constantly analyzing data and providing insights into areas for improvement.
This continuous feedback loop helps in refining processes, reducing energy consumption, and minimizing operational risks.
Additionally, digital twins enable better resource management by providing a clear understanding of the condition and performance of assets.
This information helps managers make informed decisions about equipment investments and replacements.
Synergy of Physical Models and Digital Twins
The combination of physical models and digital twins presents a robust framework for facility and equipment failure diagnosis and prediction.
While physical models focus on replicating the physical characteristics and behavior of equipment, digital twins bring these models to life through real-time data integration.
This synergy allows businesses to not only anticipate failures but also optimize their operations and maintenance strategies.
For instance, a physical model might highlight a potential failure point, while a digital twin could provide real-time data to confirm the prediction and suggest immediate corrective actions.
The continuous feedback from digital twins ensures that the physical models remain relevant and up-to-date, adapting to any changes in environmental conditions or usage patterns.
Future Prospects and Challenges
As technology continues to advance, the future of facility and equipment failure diagnosis looks increasingly promising.
The integration of more sophisticated AI and machine learning algorithms with digital twins could further enhance their predictive capabilities.
However, challenges remain, such as ensuring data security, managing large volumes of data, and requiring significant initial investments.
Despite these challenges, the potential benefits of adopting physical models and digital twins for fault diagnosis and life prediction are substantial.
Businesses looking to stay ahead in their industries should consider implementing these technologies to improve operational efficiency, extend equipment life, and reduce costs.
By harnessing the power of digital transformation, they can achieve a more reliable and sustainable facility management approach.
資料ダウンロード
QCD調達購買管理クラウド「newji」は、調達購買部門で必要なQCD管理全てを備えた、現場特化型兼クラウド型の今世紀最高の購買管理システムとなります。
ユーザー登録
調達購買業務の効率化だけでなく、システムを導入することで、コスト削減や製品・資材のステータス可視化のほか、属人化していた購買情報の共有化による内部不正防止や統制にも役立ちます。
NEWJI DX
製造業に特化したデジタルトランスフォーメーション(DX)の実現を目指す請負開発型のコンサルティングサービスです。AI、iPaaS、および先端の技術を駆使して、製造プロセスの効率化、業務効率化、チームワーク強化、コスト削減、品質向上を実現します。このサービスは、製造業の課題を深く理解し、それに対する最適なデジタルソリューションを提供することで、企業が持続的な成長とイノベーションを達成できるようサポートします。
オンライン講座
製造業、主に購買・調達部門にお勤めの方々に向けた情報を配信しております。
新任の方やベテランの方、管理職を対象とした幅広いコンテンツをご用意しております。
お問い合わせ
コストダウンが利益に直結する術だと理解していても、なかなか前に進めることができない状況。そんな時は、newjiのコストダウン自動化機能で大きく利益貢献しよう!
(Β版非公開)