- お役立ち記事
- Factory Audits of Overseas Suppliers: Essentials of Quality and CSR Management in Manufacturing’s Global Procurement
月間76,176名の
製造業ご担当者様が閲覧しています*
*2025年3月31日現在のGoogle Analyticsのデータより
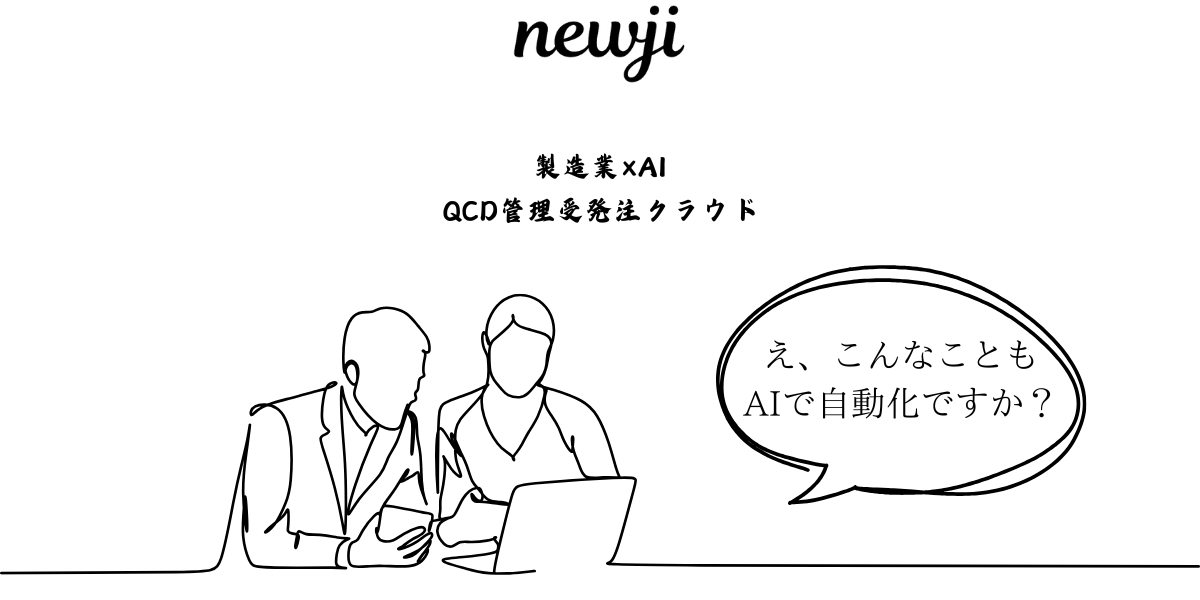
Factory Audits of Overseas Suppliers: Essentials of Quality and CSR Management in Manufacturing’s Global Procurement
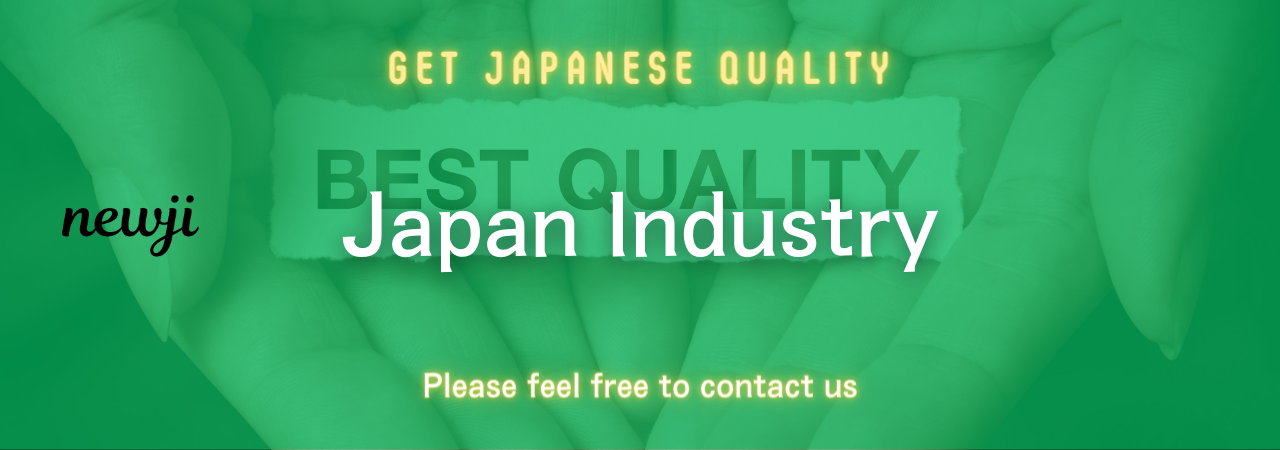
In today’s globalized economy, many companies rely on overseas suppliers to produce goods at competitive prices.
However, ensuring quality and maintaining corporate social responsibility (CSR) standards across borders can be a daunting task.
One effective way to manage these challenges is through factory audits of overseas suppliers.
Here’s what you need to know about conducting successful audits to ensure both quality and social responsibility.
目次
Why Factory Audits Are Crucial
Factory audits play a vital role in global procurement.
They help companies verify that their overseas suppliers are adhering to agreed-upon standards for quality and CSR.
This is essential for maintaining trust with customers, reducing risks, and ensuring compliance with regulations.
A thorough factory audit can reveal issues that might not be apparent through other means, such as virtual inspections or paper checks.
Risk Reduction
One of the biggest advantages of factory audits is the ability to identify and mitigate risks early.
Problems with product quality, labor conditions, and environmental compliance can have serious repercussions.
By catching these issues during an audit, companies can take corrective actions before they escalate into larger problems.
Building Trust
Conducting regular audits helps build trust between companies and their suppliers.
It shows that the company is committed to maintaining high standards and holds its partners accountable.
This can lead to stronger relationships and better long-term collaborations.
Key Components of a Factory Audit
A successful factory audit typically involves several key components.
Each of these areas should be thoroughly reviewed to ensure comprehensive coverage of both quality and CSR requirements.
Quality Management Systems
Quality management systems (QMS) are the backbone of consistent product quality.
During an audit, inspectors should examine the QMS documentation, including procedures for quality control, testing, and corrective actions.
This helps ensure that the supplier has robust processes in place to maintain high quality standards.
Production Processes
Effective production processes are crucial for consistent output.
Auditors should closely observe the manufacturing procedures to ensure they meet the required specifications.
This includes checking the machinery, examining product samples, and assessing the skills of the workforce.
Labor Conditions
Corporate social responsibility includes ensuring that labor conditions adhere to ethical standards.
Auditors should evaluate the working conditions at the factory, including worker safety, wages, and working hours.
Ensuring compliance with local labor laws and international guidelines, such as those from the International Labour Organization (ILO), is essential.
Environmental Compliance
Environmental compliance is another critical aspect of CSR.
Auditors should review the factory’s environmental management practices, including waste disposal, emissions, and resource consumption.
Compliance with local environmental regulations and international standards should be verified to minimize ecological impacts.
Conducting a Factory Audit
Executing a factory audit involves several steps, from planning and preparation to the actual inspection and follow-up actions.
Planning and Preparation
Before the audit, it’s essential to set clear objectives and scope.
This involves identifying the specific standards and criteria that will be assessed.
Auditors should also review previous audit reports and gather relevant information about the supplier.
On-Site Inspection
The on-site inspection is the core of the audit.
Auditors visit the factory to observe operations, review documents, and conduct interviews with staff.
It’s important to maintain open communication with the supplier throughout this process to ensure transparency and cooperation.
Reporting and Follow-Up
After the on-site inspection, auditors compile their findings into a detailed report.
This report should outline any non-conformities and recommend corrective actions.
Companies should follow up with the supplier to ensure that these actions are implemented and verify improvements through subsequent audits.
Challenges and Best Practices
Conducting factory audits of overseas suppliers comes with several challenges, including cultural differences, language barriers, and logistical issues.
However, adopting best practices can help mitigate these challenges.
Building Cultural Sensitivity
Understanding and respecting cultural differences is crucial for successful audits.
Auditors should familiarize themselves with local customs and business practices.
This helps build rapport with the supplier and facilitates smoother communication.
Effective Communication
Clear and effective communication is essential, especially when dealing with language barriers.
Using professional translators and ensuring that all parties understand the audit objectives and criteria can help prevent misunderstandings.
Leveraging Technology
Modern technology can streamline the audit process.
Digital audit tools, cloud-based document management, and real-time communication platforms can enhance efficiency and accuracy.
Virtual audits, while not a complete substitute for on-site inspections, can also be useful for preliminary assessments.
Ongoing Training
Continuous training for auditors is vital for maintaining high standards.
Regularly updating auditors on the latest industry standards, regulatory changes, and best practices ensures they are well-equipped to conduct thorough and effective audits.
In conclusion, factory audits of overseas suppliers are essential for maintaining quality and CSR standards in global procurement.
By understanding the key components of an audit, following a structured approach, and adopting best practices, companies can effectively manage risks, build trust with suppliers, and ensure compliance.
This not only benefits the company but also contributes to broader social and environmental goals.
資料ダウンロード
QCD管理受発注クラウド「newji」は、受発注部門で必要なQCD管理全てを備えた、現場特化型兼クラウド型の今世紀最高の受発注管理システムとなります。
ユーザー登録
受発注業務の効率化だけでなく、システムを導入することで、コスト削減や製品・資材のステータス可視化のほか、属人化していた受発注情報の共有化による内部不正防止や統制にも役立ちます。
NEWJI DX
製造業に特化したデジタルトランスフォーメーション(DX)の実現を目指す請負開発型のコンサルティングサービスです。AI、iPaaS、および先端の技術を駆使して、製造プロセスの効率化、業務効率化、チームワーク強化、コスト削減、品質向上を実現します。このサービスは、製造業の課題を深く理解し、それに対する最適なデジタルソリューションを提供することで、企業が持続的な成長とイノベーションを達成できるようサポートします。
製造業ニュース解説
製造業、主に購買・調達部門にお勤めの方々に向けた情報を配信しております。
新任の方やベテランの方、管理職を対象とした幅広いコンテンツをご用意しております。
お問い合わせ
コストダウンが利益に直結する術だと理解していても、なかなか前に進めることができない状況。そんな時は、newjiのコストダウン自動化機能で大きく利益貢献しよう!
(β版非公開)