- お役立ち記事
- Factory Audits of Overseas Suppliers: Key Points for Quality and CSR Management in International Procurement
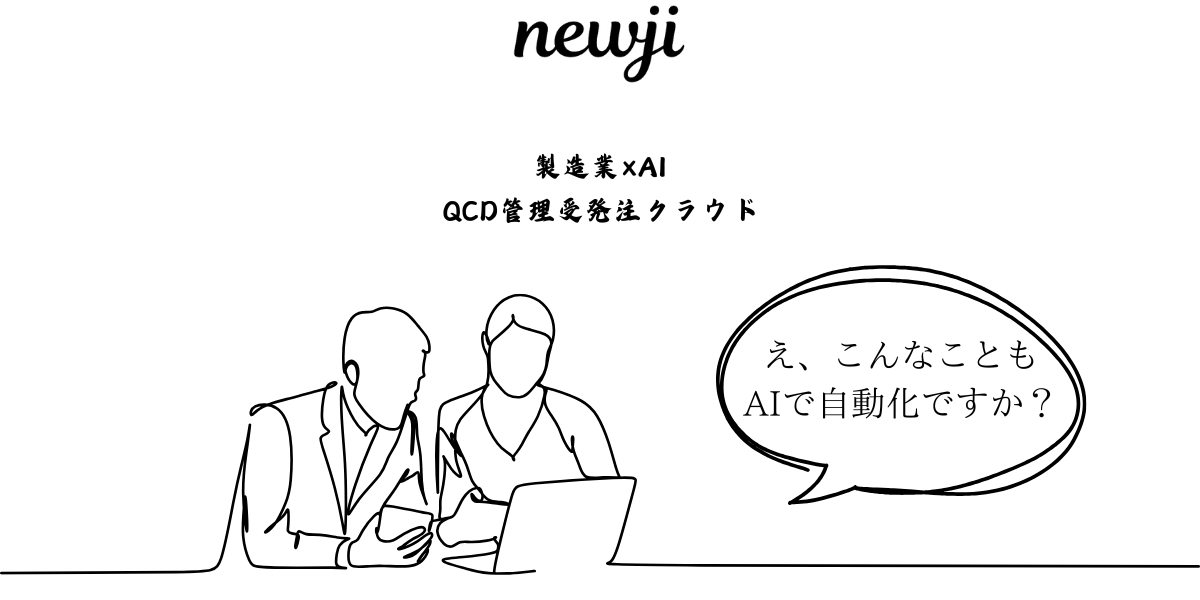
Factory Audits of Overseas Suppliers: Key Points for Quality and CSR Management in International Procurement
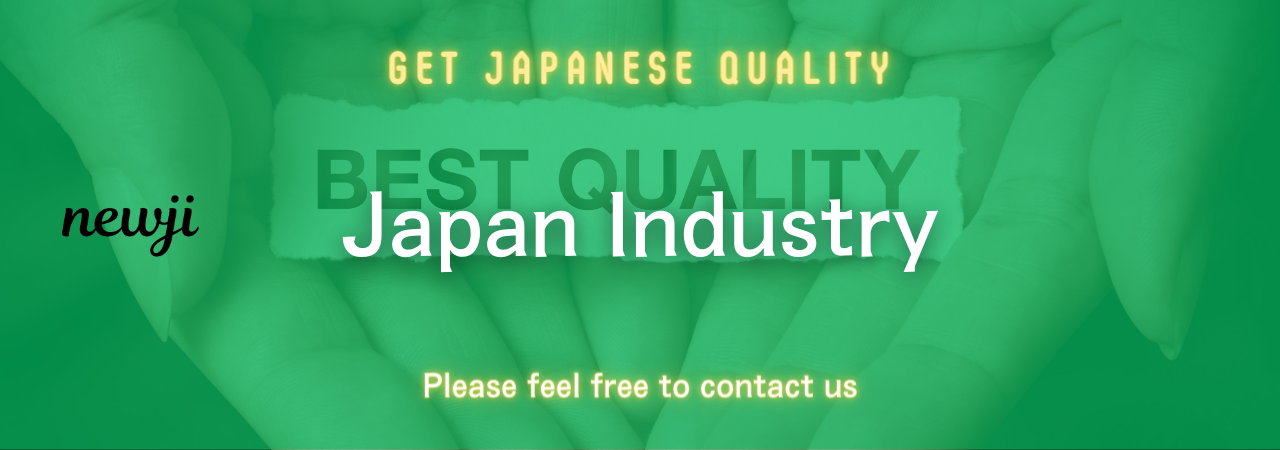
In today’s globalized economy, companies increasingly rely on overseas suppliers for their procurement needs.
While this creates opportunities for cost savings and access to specialized products, it also brings potential risks related to quality and corporate social responsibility (CSR).
A robust factory audit of overseas suppliers is essential to manage these risks effectively.
This article will explore key points to ensure high-quality production and adherence to CSR principles in international procurement.
目次
Understanding Factory Audits
Factory audits are comprehensive evaluations of a manufacturing facility’s processes, systems, and capabilities.
The primary goal is to assess whether the supplier can meet quality, safety, and compliance requirements.
Such audits typically involve site inspections, document reviews, and interviews with management and staff.
Importance of Factory Audits
Factory audits are vital for several reasons:
– **Quality Assurance**: Ensuring that the supplier can produce goods that meet your standards.
– **Risk Mitigation**: Identifying potential problems before they impact your business.
– **Compliance**: Verifying that the factory adheres to legal and regulatory requirements.
– **CSR**: Assessing the social and environmental practices of the supplier.
Quality Management in Factory Audits
Assessing Production Capabilities
One of the first steps in a factory audit is to evaluate the supplier’s production capabilities.
This involves inspecting equipment, machinery, and technology used in manufacturing.
You’ll want to verify if the factory can handle large orders and produce products to your specifications.
An audit should look at the factory’s history of production and any previous quality control issues.
Document Review
Reviewing documents is another crucial part of a factory audit.
Key documents include quality control processes, standard operating procedures, and previous audit reports.
Ensure the supplier has robust quality management systems, like ISO 9001 certification, which indicates a commitment to maintaining high-quality standards.
Employee Training and Competence
A factory’s workforce plays a significant role in maintaining quality.
During an audit, assess the training programs and qualifications of employees.
A skilled, well-trained workforce is more likely to produce high-quality products consistently.
Inspection and Testing
Inspecting the finished products is essential to verify quality compliance.
Check if the factory conducts regular tests and inspections throughout the production process.
Random sampling, mechanical testing, and visual inspections are techniques to ensure products meet specified standards.
CSR Management in Factory Audits
Labor Conditions
CSR is not just about the environment; it also concerns the ethical treatment of workers.
During a factory audit, assess working conditions to ensure they are safe and humane.
Things to check include fair wages, reasonable working hours, and adequate rest periods. Interviews with employees can provide insights into labor conditions and identify potential areas of concern.
Environmental Practices
The environmental impact of a supplier is increasingly important in today’s world.
Auditors should examine the factory’s waste management practices, energy consumption, and emissions.
Check if the factory complies with local environmental laws and has any certifications like ISO 14001 for effective environmental management.
Corporate Governance
Good corporate governance is the cornerstone of CSR practices.
Assess the supplier’s code of conduct, compliance mechanisms, and any CSR initiatives they undertake.
Companies with strong governance are more likely to adhere to ethical standards and legal requirements consistently.
Preparation for Factory Audits
Pre-Audit Checklist
Preparing for a factory audit involves several steps:
– **Identify Key Requirements**: Define what you need to check, focusing on quality and CSR criteria.
– **Assemble a Team**: Form a team of knowledgeable professionals who understand your audit requirements.
– **Documentation**: Gather all necessary documents to streamline the audit process.
– **Schedule the Audit**: Coordinate with the supplier to find a convenient time for the audit, giving them ample notice.
Audit Execution
During the audit, follow these steps:
– **Opening Meeting**: Start with a meeting to outline the audit process and objectives.
– **Site Inspection**: Conduct thorough inspections of production areas, employee facilities, and storage areas.
– **Document Review**: Examine key documents to verify compliance with quality and CSR standards.
– **Interviews**: Speak with management and employees to gather insights and confirm information found during the inspection.
– **Closing Meeting**: Summarize findings and discuss next steps with the supplier, including any required improvements.
Post-Audit Actions
Audit Report
After completing the audit, prepare a comprehensive report detailing your findings.
Highlight areas of compliance and non-compliance, and outline any corrective actions required.
Distribute the report to relevant stakeholders and the supplier for review.
Follow-Up
Following up is crucial to ensure that the supplier implements required improvements.
Plan follow-up audits or inspections to verify that corrective actions have been taken.
Ongoing monitoring helps maintain high standards and builds a solid, long-term relationship with the supplier.
Conclusion
Factory audits of overseas suppliers are essential for managing risks related to quality and CSR in international procurement.
By understanding the critical aspects of quality management and CSR, you can conduct thorough audits that safeguard your business interests and promote ethical practices.
Preparation, execution, and follow-up are key stages that require careful attention to achieve successful outcomes.
With these strategies, you can ensure that your overseas suppliers meet your standards and contribute positively to your supply chain.
資料ダウンロード
QCD調達購買管理クラウド「newji」は、調達購買部門で必要なQCD管理全てを備えた、現場特化型兼クラウド型の今世紀最高の購買管理システムとなります。
ユーザー登録
調達購買業務の効率化だけでなく、システムを導入することで、コスト削減や製品・資材のステータス可視化のほか、属人化していた購買情報の共有化による内部不正防止や統制にも役立ちます。
NEWJI DX
製造業に特化したデジタルトランスフォーメーション(DX)の実現を目指す請負開発型のコンサルティングサービスです。AI、iPaaS、および先端の技術を駆使して、製造プロセスの効率化、業務効率化、チームワーク強化、コスト削減、品質向上を実現します。このサービスは、製造業の課題を深く理解し、それに対する最適なデジタルソリューションを提供することで、企業が持続的な成長とイノベーションを達成できるようサポートします。
オンライン講座
製造業、主に購買・調達部門にお勤めの方々に向けた情報を配信しております。
新任の方やベテランの方、管理職を対象とした幅広いコンテンツをご用意しております。
お問い合わせ
コストダウンが利益に直結する術だと理解していても、なかなか前に進めることができない状況。そんな時は、newjiのコストダウン自動化機能で大きく利益貢献しよう!
(Β版非公開)