- お役立ち記事
- Factory improvements before automation implementation
Factory improvements before automation implementation
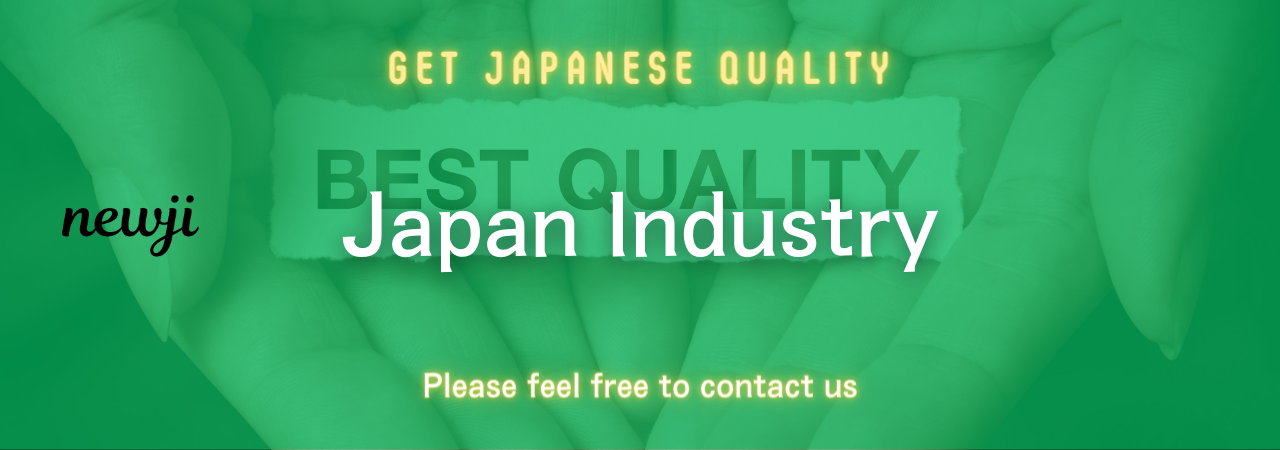
目次
Understanding the Need for Improvements
Before diving headfirst into automation, it’s crucial for any factory to evaluate its current processes and identify areas for improvement.
Enhancing workflow, optimizing space utilization, and refining processes can lead to significant improvements.
These steps not only prepare the factory for smooth automation implementation but also ensure a better return on investment.
Automation, while powerful, can amplify existing inefficiencies if not managed correctly.
Therefore, taking the time to understand and improve current practices is a foundational step.
Evaluating Current Operations
The first step in factory improvement is evaluating current operations thoroughly.
Managers should review all ongoing processes, analyzing bottlenecks, waste, downtime, and areas where delays occur frequently.
Identifying such problems will provide clarity on where changes are necessary.
During this evaluation, it’s important to engage with the workforce.
Employees often have insights into inefficiencies and practical suggestions for improvement.
Holding discussions or conducting surveys can reveal invaluable on-the-ground perspectives that might be overlooked at higher management levels.
Streamlining Processes
Streamlining is a critical precursor to automation.
It involves refining processes to make them as efficient and effective as possible.
One approach is to apply Lean manufacturing principles, which emphasize the importance of minimizing waste and maximizing productivity.
These principles focus on reducing steps in a process that do not add value, thus creating a leaner, more responsive production environment.
Factory layouts should also be evaluated to ensure a seamless flow of materials and products.
Accessible pathways, strategically placed equipment, and organized workspaces contribute significantly to higher productivity levels.
By reconfiguring the layout, manufacturers can reduce time spent on transporting materials or parts within the factory.
Quality Control and Consistency
Another crucial aspect of factory improvement is enhancing quality control mechanisms.
Before automation, it’s imperative to have robust quality checks to ensure consistency in production output.
Improving quality control systems not only prevents costly defects but also provides a stable foundation for automation technologies, which thrive on uniformity and predictability.
Factories should invest in training programs to elevate the skill sets of workers.
Well-trained employees are better equipped to handle quality control effectively, decreasing the likelihood of defects and enhancing product reliability.
Investing in Modern Equipment
Part of preparing for automation involves upgrading old or inefficient equipment.
Older machinery that demands frequent repairs or slows down production should be either refurbished or replaced.
Investing in modern equipment ensures that the factory is not only prepared for automation but is also operating at optimal efficiency currently.
Modern equipment often comes with better energy efficiency, which results in cost savings.
This reduced energy consumption not only impacts the bottom line positively but also aligns with environmental sustainability efforts, creating a more eco-friendly manufacturing approach.
Data Management Systems
Before implementing automation, establishing a strong data management system is crucial.
A well-organized data handling process allows for precise tracking and monitoring of the production process.
Data systems can offer insights into production rates, inventory levels, and maintenance schedules, which are essential for planning and executing automation strategies successfully.
These systems also facilitate better decision-making, allowing managers to base their strategies on real-time, accurate data.
This strategic advantage ensures that once automation is in place, it operates under optimal conditions.
Improving Workplace Safety
A safe working environment is fundamental before introducing automation.
Automation brings enhanced speed and efficiency but can pose risks if safety protocols are not intensified appropriately.
Ensuring that the workforce operates safely around evolving technologies is essential.
Safety improvements might include updating safety gear, installing more accessible emergency stops, or increasing safety signage throughout the factory.
Moreover, regular safety training ensures all employees are aware of potential hazards and know how to address them.
Engaging Employees in Change
Employees should be involved in the transition to automation to ensure a smooth shift.
Providing training and support makes employees feel valued and prepared, which can significantly boost morale and productivity.
Understanding how automation will affect their roles allows employees to adapt more readily to new technologies and processes.
Engaged employees are also more likely to embrace change positively, seeing automation as a tool that will enhance their work rather than as a threat.
This mindset fosters a collaborative environment where innovation and improvement are continuously sought.
The Road Ahead
Improving a factory before implementing automation involves comprehensive evaluation and strategic enhancements across multiple aspects such as operations, equipment, safety, and workforce engagement.
This holistic approach ensures that when automation is finally introduced, it serves to elevate the factory’s productivity, consistency, and profitability.
Taking these preparatory steps guarantees a smoother integration of new technologies, paving the way for a more efficient, reliable, and competitive manufacturing environment.
The road to automation is one of progression and transformation, and these improvements are vital milestones on that journey.
資料ダウンロード
QCD調達購買管理クラウド「newji」は、調達購買部門で必要なQCD管理全てを備えた、現場特化型兼クラウド型の今世紀最高の購買管理システムとなります。
ユーザー登録
調達購買業務の効率化だけでなく、システムを導入することで、コスト削減や製品・資材のステータス可視化のほか、属人化していた購買情報の共有化による内部不正防止や統制にも役立ちます。
NEWJI DX
製造業に特化したデジタルトランスフォーメーション(DX)の実現を目指す請負開発型のコンサルティングサービスです。AI、iPaaS、および先端の技術を駆使して、製造プロセスの効率化、業務効率化、チームワーク強化、コスト削減、品質向上を実現します。このサービスは、製造業の課題を深く理解し、それに対する最適なデジタルソリューションを提供することで、企業が持続的な成長とイノベーションを達成できるようサポートします。
オンライン講座
製造業、主に購買・調達部門にお勤めの方々に向けた情報を配信しております。
新任の方やベテランの方、管理職を対象とした幅広いコンテンツをご用意しております。
お問い合わせ
コストダウンが利益に直結する術だと理解していても、なかなか前に進めることができない状況。そんな時は、newjiのコストダウン自動化機能で大きく利益貢献しよう!
(Β版非公開)