- お役立ち記事
- Factory layout design, effective improvement examples, and points for improving productivity
月間76,176名の
製造業ご担当者様が閲覧しています*
*2025年3月31日現在のGoogle Analyticsのデータより
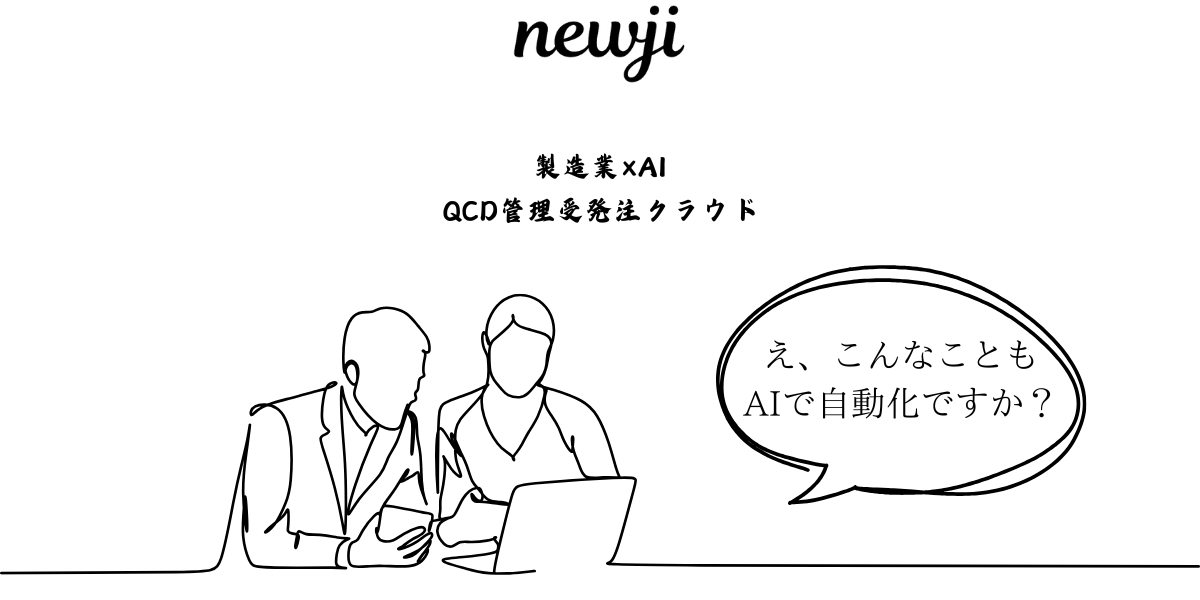
Factory layout design, effective improvement examples, and points for improving productivity
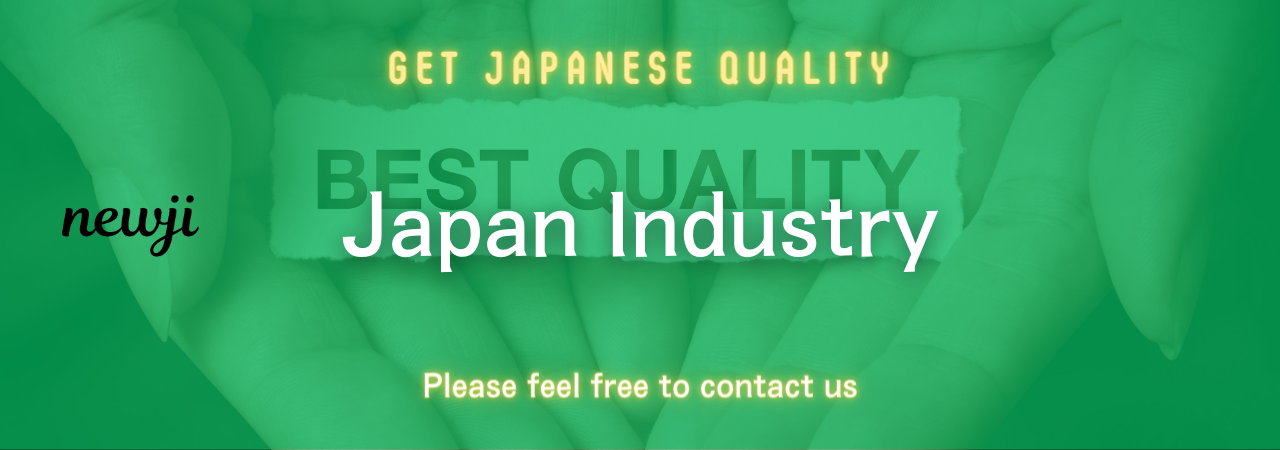
目次
Understanding Factory Layout Design
Factory layout design plays a crucial role in determining the efficiency of production processes.
It refers to the arrangement of machinery, equipment, and workers within a production facility.
A well-designed layout ensures smooth workflow, minimizes production delays, and optimizes space usage.
The primary goal of any factory layout is to enhance productivity by maximizing operational efficiency.
It requires careful consideration of several factors including the flow of materials, the type of production process, and worker safety.
Types of Factory Layouts
Before diving into effective improvement examples, it’s important to understand the various types of factory layouts.
Each type has its own advantages and is suited for different production needs.
1. **Process Layout**: This layout groups similar processes together.
It’s ideal for factories that produce a variety of products in small batches.
Flexibility is its biggest advantage as it allows for easy adjustments in the production process.
However, it can cause delays due to the movement of products between departments.
2. **Product Layout**: In this layout, workstations and equipment are arranged in the sequence of production steps.
It’s most effective for mass production of standardized products.
The main benefit is the reduction of production time, but it requires significant initial investment and lacks flexibility.
3. **Fixed-Position Layout**: Used when the product is too large or heavy to be moved, such as ships or airplanes.
Components are transported to the fixed location instead.
While it allows for a high level of customization, it can result in high costs and complex logistics.
4. **Cellular Layout**: Combines elements of both product and process layouts.
Products are manufactured in groups, or “cells”, that make use of similar operations.
It enhances productivity and product variations but demands a careful selection and arrangement of machinery.
Effective Improvement Examples
When considering improvements in factory layout design, implementing successful examples can significantly boost productivity.
Lean Manufacturing Principles
One of the most effective ways to improve factory layout is by adopting lean manufacturing principles.
Lean manufacturing focuses on minimizing waste and maximizing value for the customer.
– **5S Methodology**: This involves sorting, setting in order, shining, standardizing, and sustaining the workplace.
A clutter-free workspace facilitates easy location of tools, machinery, and materials.
– **Value Stream Mapping**: This technique involves visualizing the entire flow of materials and information in the production process.
Identifying and eliminating bottlenecks can improve efficiency.
Technology Integration
Implementing modern technologies can revolutionize factory layouts and operations.
– **Automation**: Automated systems such as conveyor belts, robotics, and computer-controlled manufacturing reduce human intervention and increase precision, leading to higher productivity.
– **Internet of Things (IoT)**: IoT devices can monitor machinery performance in real-time.
This data helps in predictive maintenance, minimizing downtime, and enhancing the workflow.
Kaizen Approach
Kaizen is a Japanese philosophy that focuses on continuous improvement through small, incremental changes.
Encouraging every employee to contribute ideas for improvement creates a culture of ongoing enhancement.
This not only increases productivity but also improves employee satisfaction and quality of work life.
Points for Improving Productivity
Improving productivity through factory layout design requires addressing several key points.
Ergonomics
Designing workstations tailored to human comfort can have a significant impact on productivity.
Incorporating ergonomic furniture and equipment reduces physical strain on workers.
This can lead to fewer health issues and increased efficiency.
Efficient Material Flow
Optimizing the flow of materials through streamlined processes reduces handling time and transport costs.
Clear pathways and strategic placement of workstations minimize the distance materials travel.
This not only increases speed but also reduces the chance of material damage.
Safety Measures
A safe working environment is crucial for high productivity.
Ensure machinery is properly maintained and safety protocols are in place.
Providing proper signage, protective gear, and regular training helps reduce workplace accidents.
Space Utilization
Efficient use of available space fosters better organization and workflow.
Consider vertical storage solutions to maximize floor space.
Designing flexible layouts allows for quick adjustments to the production line as needed.
Conclusion
Designing an effective factory layout is a continuous journey rather than a one-time task.
By understanding the different types of layouts, implementing successful improvement examples, and focusing on key productivity points, factories can achieve significant enhancement in performance.
Innovation and adaptability in layout design can distinguish successful manufacturers in today’s competitive market.
Always remember that a well-thought-out factory layout is the foundation of manufacturing efficiency and productivity.
資料ダウンロード
QCD管理受発注クラウド「newji」は、受発注部門で必要なQCD管理全てを備えた、現場特化型兼クラウド型の今世紀最高の受発注管理システムとなります。
ユーザー登録
受発注業務の効率化だけでなく、システムを導入することで、コスト削減や製品・資材のステータス可視化のほか、属人化していた受発注情報の共有化による内部不正防止や統制にも役立ちます。
NEWJI DX
製造業に特化したデジタルトランスフォーメーション(DX)の実現を目指す請負開発型のコンサルティングサービスです。AI、iPaaS、および先端の技術を駆使して、製造プロセスの効率化、業務効率化、チームワーク強化、コスト削減、品質向上を実現します。このサービスは、製造業の課題を深く理解し、それに対する最適なデジタルソリューションを提供することで、企業が持続的な成長とイノベーションを達成できるようサポートします。
製造業ニュース解説
製造業、主に購買・調達部門にお勤めの方々に向けた情報を配信しております。
新任の方やベテランの方、管理職を対象とした幅広いコンテンツをご用意しております。
お問い合わせ
コストダウンが利益に直結する術だと理解していても、なかなか前に進めることができない状況。そんな時は、newjiのコストダウン自動化機能で大きく利益貢献しよう!
(β版非公開)