- お役立ち記事
- Failure analysis/accelerated testing technology and its key points to improve reliability of electronic components/mounted boards
月間77,185名の
製造業ご担当者様が閲覧しています*
*2025年2月28日現在のGoogle Analyticsのデータより
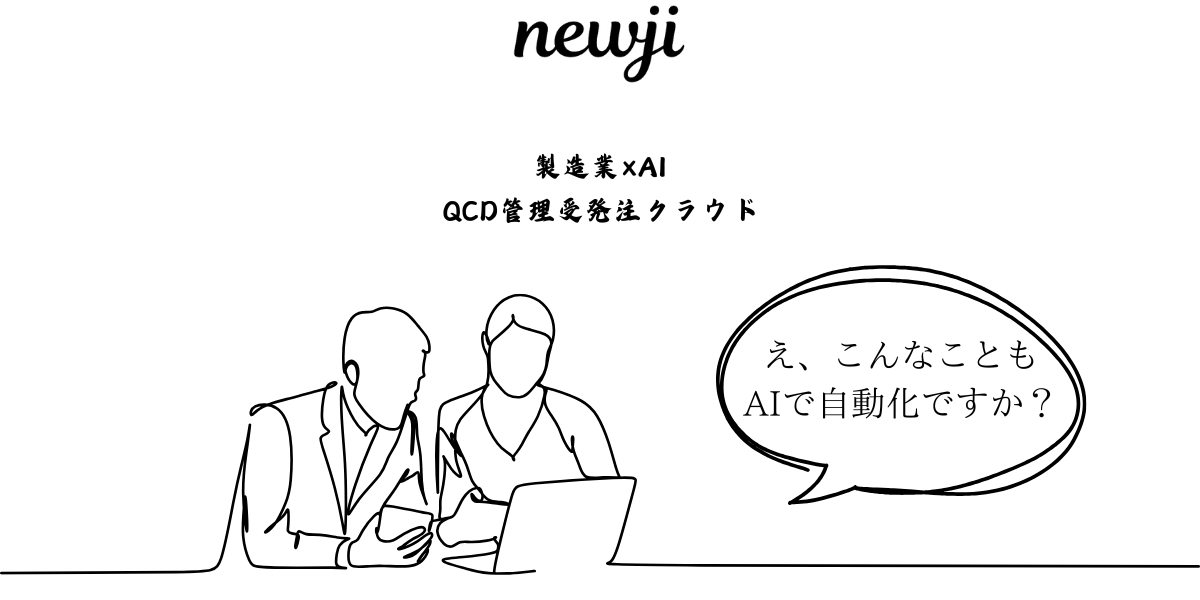
Failure analysis/accelerated testing technology and its key points to improve reliability of electronic components/mounted boards
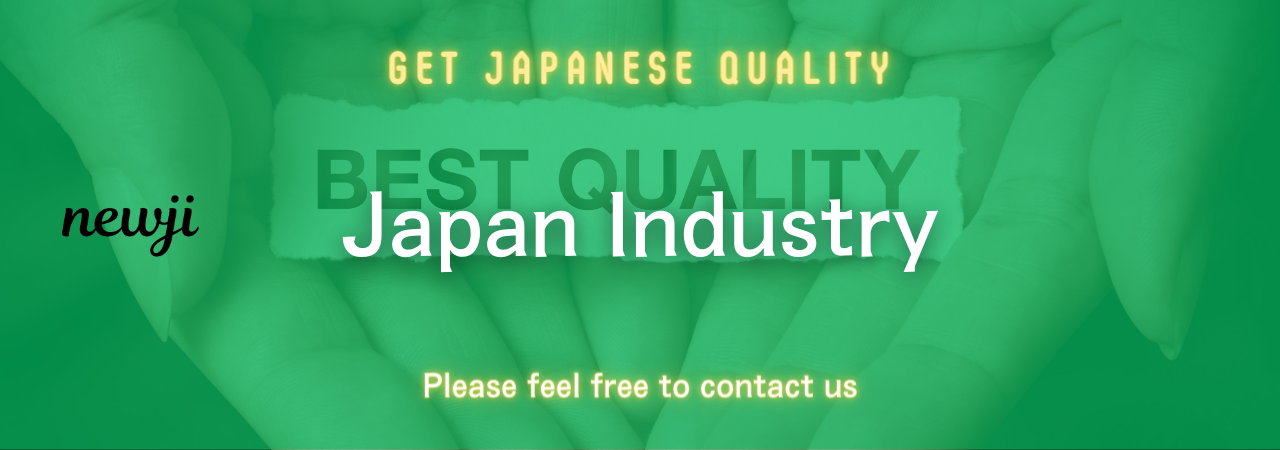
目次
Introduction to Failure Analysis and Accelerated Testing
In today’s rapidly evolving world, electronic components and mounted boards play a crucial role in the functionality and reliability of our devices.
From smartphones to complex industrial machines, these components are integral in ensuring everything runs smoothly.
However, ensuring their reliability over time poses a significant challenge.
This is where failure analysis and accelerated testing technology come into play.
These processes help identify weaknesses and predict potential failures, leading to improved reliability and longevity of electronic components.
What is Failure Analysis?
Failure analysis is the comprehensive process of investigating, examining, and understanding why a product or component has failed.
This investigation often involves detailed observation and testing to determine the root cause of the failure.
By understanding these causes, manufacturers can make informed decisions to improve the design, materials, or processes used in creating electronic components.
Steps in Failure Analysis
1. **Data Collection**: Gathering all relevant information regarding the failed component or system.
This includes environmental conditions, operational history, and previous performance data.
2. **Visual Inspection**: A thorough examination of the component to identify any visible signs of damage or failure, such as cracks, discoloration, or burn marks.
3. **Non-Destructive Testing (NDT)**: Techniques such as X-ray, ultrasound, or thermography are used to examine the internal aspects of the component without causing further damage.
4. **Destructive Testing**: If necessary, the component can be dismantled for a more in-depth examination.
This might involve physical probing, cutting, or grinding.
5. **Chemical Analysis**: Identifies any chemical changes or contaminants that might have led to the failure.
6. **Data Analysis and Conclusion**: Compile all gathered data to identify the failure’s root cause and suggest improvements accordingly.
Understanding Accelerated Testing Technology
Accelerated testing is a method used to speed up the life cycle testing of a component.
It simulates the effects of stress and environmental conditions over an extended time within a shorter period.
This helps in predicting the component’s lifespan and reliability under normal operating conditions.
Types of Accelerated Testing
1. **Temperature Cycling**: Components are subjected to extreme temperatures to test how they expand and contract and to identify potential thermal issues.
2. **Humidity Testing**: Evaluates the component’s ability to withstand moisture, which can lead to corrosion or electrical failures.
3. **Vibration Testing**: Simulates the vibrations experienced during transportation or operation to identify mechanical weaknesses.
4. **Pressure Testing**: Components that must operate under certain pressure levels are tested to ensure they can withstand those conditions without failure.
5. **Electrical Stress Testing**: Components are subjected to electrical stresses, such as over-voltage or surge conditions, to test their robustness.
Key Points to Improve Reliability
Reliability of electronic components and mounted boards can be significantly enhanced by focusing on a few critical points during both the design and testing stages.
Improved Materials and Design
Selecting quality materials that are suited to withstand the application’s specific environmental and operational stresses is essential.
Additionally, a robust design that accounts for these conditions can prevent many potential failures.
Regular Maintenance and Testing
Implementing a routine maintenance schedule can help identify early signs of wear and tear.
Incorporating regular testing, including periodic accelerated tests, ensures that potential issues are caught early before they lead to failure.
Feedback Loop from Failure Analysis
Using the data obtained from failure analysis to continuously improve product design and manufacturing processes is crucial.
This feedback loop allows for iterative improvements, reducing the chances of future failures.
Quality Control and Assurance
Having stringent quality control measures during the production process ensures that each component meets the necessary standards.
This includes regular inspections and testing throughout the manufacturing process to identify defects early on.
Conclusion
Failure analysis and accelerated testing are invaluable tools in enhancing the reliability of electronic components and mounted boards.
These technologies allow manufacturers to identify potential failure modes, understand their causes, and implement effective solutions to prevent future issues.
By focusing on the key points outlined above, companies can improve the longevity and performance of their products, leading to increased customer satisfaction and reduced costs associated with repairs and replacements.
Embracing these methodologies is crucial for staying competitive in the ever-demanding electronics industry.
資料ダウンロード
QCD管理受発注クラウド「newji」は、受発注部門で必要なQCD管理全てを備えた、現場特化型兼クラウド型の今世紀最高の受発注管理システムとなります。
ユーザー登録
受発注業務の効率化だけでなく、システムを導入することで、コスト削減や製品・資材のステータス可視化のほか、属人化していた受発注情報の共有化による内部不正防止や統制にも役立ちます。
NEWJI DX
製造業に特化したデジタルトランスフォーメーション(DX)の実現を目指す請負開発型のコンサルティングサービスです。AI、iPaaS、および先端の技術を駆使して、製造プロセスの効率化、業務効率化、チームワーク強化、コスト削減、品質向上を実現します。このサービスは、製造業の課題を深く理解し、それに対する最適なデジタルソリューションを提供することで、企業が持続的な成長とイノベーションを達成できるようサポートします。
製造業ニュース解説
製造業、主に購買・調達部門にお勤めの方々に向けた情報を配信しております。
新任の方やベテランの方、管理職を対象とした幅広いコンテンツをご用意しております。
お問い合わせ
コストダウンが利益に直結する術だと理解していても、なかなか前に進めることができない状況。そんな時は、newjiのコストダウン自動化機能で大きく利益貢献しよう!
(β版非公開)