- お役立ち記事
- Failure Analysis and Reliability Improvement of Semiconductor Light Sources
月間76,176名の
製造業ご担当者様が閲覧しています*
*2025年3月31日現在のGoogle Analyticsのデータより
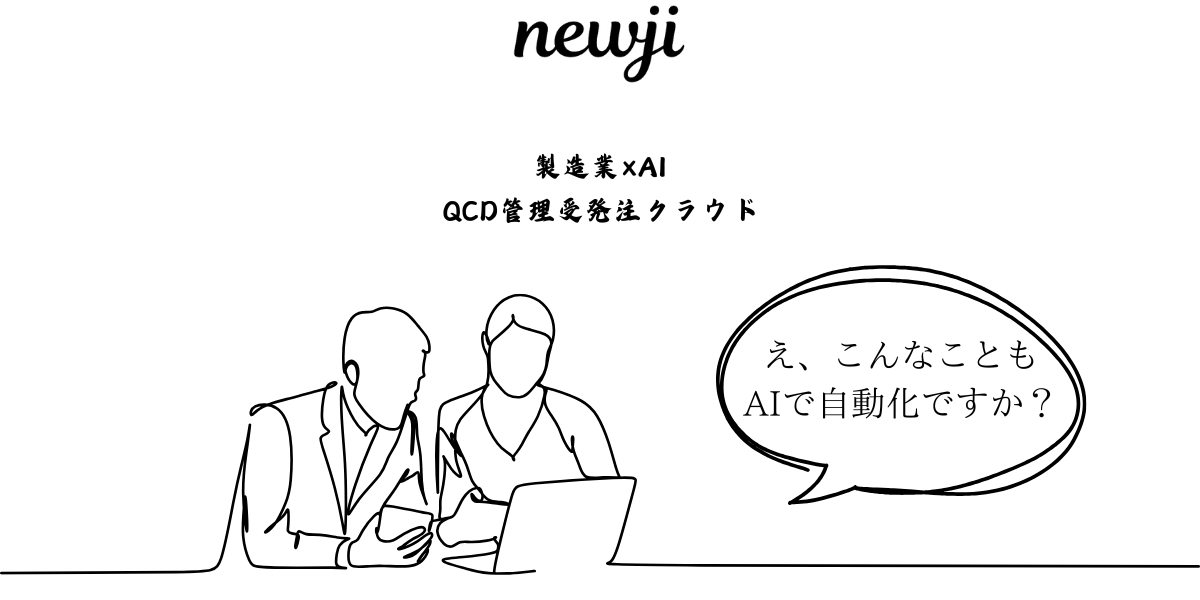
Failure Analysis and Reliability Improvement of Semiconductor Light Sources
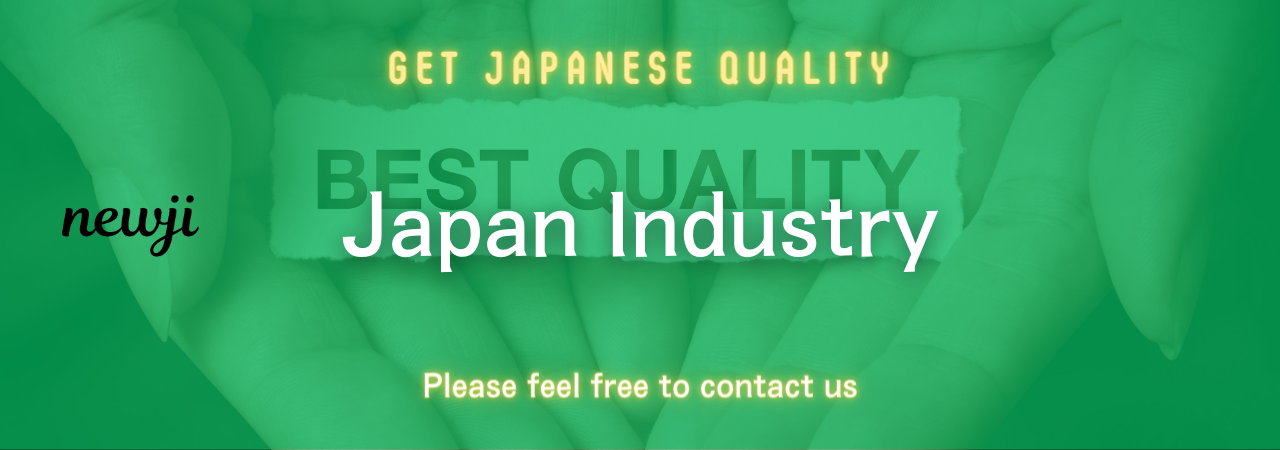
目次
Introduction
Semiconductor light sources are integral to modern technology, powering everything from your smartphone’s display to sophisticated communication systems.
Despite their crucial role, these devices can fail over time, creating a need for robust failure analysis and reliability improvement strategies.
Understanding the failure mechanisms is essential to ensure long-lasting performance and reliability, addressing consumer demands and industry standards alike.
Common Failure Mechanisms
To effectively analyze failures in semiconductor light sources, it’s important to identify common mechanisms that lead to these failures.
Some prevalent causes include thermal degradation, material defects, and electrical stress.
Thermal Degradation
One of the primary reasons for failure in semiconductor light sources is thermal degradation.
Excessive heat can lead to the deterioration of materials, causing performance degradation or complete failure.
This happens because the high operating temperatures can cause interfacial defects, which in turn affect the efficiency and lifespan of the devices.
Material Defects
Material defects present at the time of manufacturing are another significant cause of failure.
These defects can include dislocations, impurities, and incomplete crystallization, all contributing to the eventual breakdown of the semiconductor light source.
While advances in manufacturing processes continue to improve material quality, defects remain a prevalent problem in the industry.
Electrical Stress
Electrical stress, often caused by over-voltage or current surges, can result in the deterioration or failure of semiconductor surfaces and junctions.
This type of stress can create localized hotspots, leading to avalanche breakdown and catastrophic failure of the light source.
Failure Analysis Techniques
To counter these failure mechanisms, various analysis techniques can be employed to detect and understand the causes.
These methods provide critical insights necessary for reliability improvement and include techniques like failure mode and effects analysis (FMEA), accelerated life testing, and scanning electron microscopy (SEM).
Failure Mode and Effects Analysis (FMEA)
FMEA is a systematic, methodical approach used to identify potential failure modes within a design, process, or product.
By analyzing the effects and causes of these failures, manufacturers can prioritize risks and implement strategic measures to mitigate potential issues.
Accelerated Life Testing
Accelerated life testing involves subjecting semiconductor light sources to exaggerated operating conditions.
This approach helps manufacturers quickly identify and study the failure mechanisms, enabling them to predict the service life more accurately.
Scanning Electron Microscopy (SEM)
SEM is a highly effective diagnostic tool offering magnified imaging at the microscopic level.
It enables the visualization of fracture surfaces, defects, and material anomalies, helping engineers understand the root cause of failures more clearly.
Strategies for Reliability Improvement
Enhancing the reliability of semiconductor light sources requires a focused commitment to material improvement, design optimization, and process control.
Material Improvement
The foundation of reliable semiconductor light sources starts with quality materials.
Employing high-purity compounds and refining fabrication processes helps minimize defects, improving the longevity of the light source.
Advancements in materials like GaN (Gallium Nitride) offer better thermal conductivity and efficiency.
Design Optimization
Innovative design practices can significantly enhance the performance and reliability of semiconductor light sources.
Techniques such as heat sinks, optimized die layout, and improved encapsulations help in managing thermal stresses more effectively.
Design improvements in packaging can also contribute significantly to the longevity by reducing stress concentrations.
Process Control
Strict control over the manufacturing process is essential for eliminating discrepancies that lead to failures.
Implementing standardized testing and inspection procedures ensures consistency and identifies defects early in the production line.
Automation and advanced process-monitoring tools can lead to enhanced precision and efficiency in semiconductor light source manufacturing.
Conclusion
As semiconductor light sources continue to evolve, understanding and addressing common failure mechanisms is crucial to their success.
Through comprehensive failure analysis and targeted reliability improvement strategies, manufacturers can meet growing consumer demands for longer-lasting, more reliable products.
By focusing on enhancing materials, optimizing designs, and maintaining strict process controls, the future of semiconductor light sources remains bright and promising.
資料ダウンロード
QCD管理受発注クラウド「newji」は、受発注部門で必要なQCD管理全てを備えた、現場特化型兼クラウド型の今世紀最高の受発注管理システムとなります。
ユーザー登録
受発注業務の効率化だけでなく、システムを導入することで、コスト削減や製品・資材のステータス可視化のほか、属人化していた受発注情報の共有化による内部不正防止や統制にも役立ちます。
NEWJI DX
製造業に特化したデジタルトランスフォーメーション(DX)の実現を目指す請負開発型のコンサルティングサービスです。AI、iPaaS、および先端の技術を駆使して、製造プロセスの効率化、業務効率化、チームワーク強化、コスト削減、品質向上を実現します。このサービスは、製造業の課題を深く理解し、それに対する最適なデジタルソリューションを提供することで、企業が持続的な成長とイノベーションを達成できるようサポートします。
製造業ニュース解説
製造業、主に購買・調達部門にお勤めの方々に向けた情報を配信しております。
新任の方やベテランの方、管理職を対象とした幅広いコンテンツをご用意しております。
お問い合わせ
コストダウンが利益に直結する術だと理解していても、なかなか前に進めることができない状況。そんな時は、newjiのコストダウン自動化機能で大きく利益貢献しよう!
(β版非公開)