- お役立ち記事
- Failure analysis method and reliability test to improve reliability of electronic component mounting boards
月間77,185名の
製造業ご担当者様が閲覧しています*
*2025年2月28日現在のGoogle Analyticsのデータより
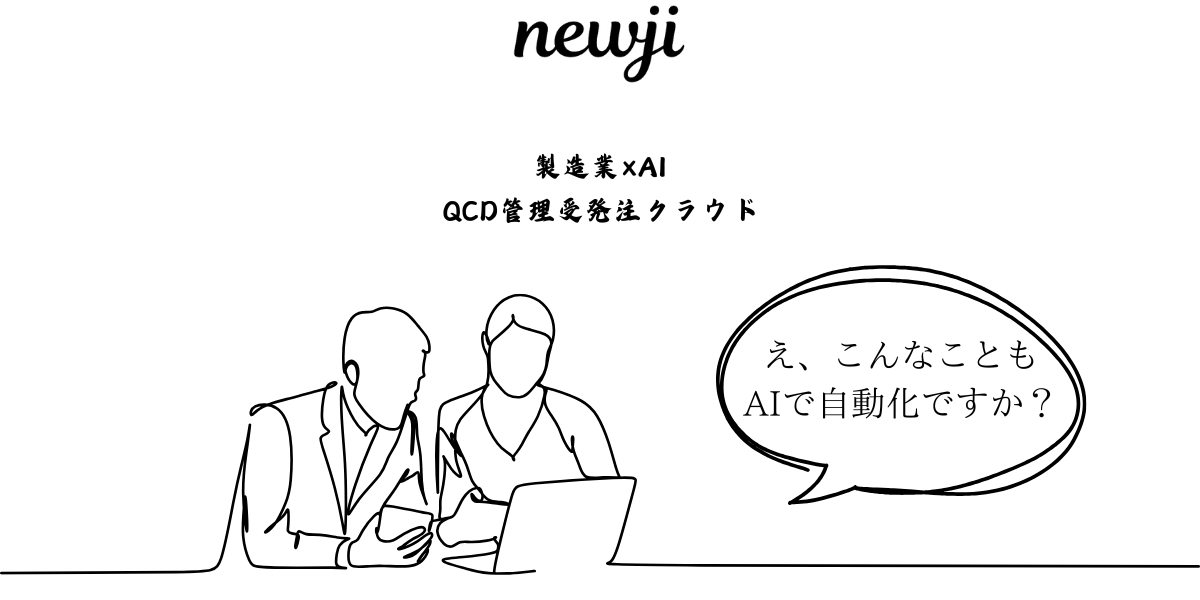
Failure analysis method and reliability test to improve reliability of electronic component mounting boards
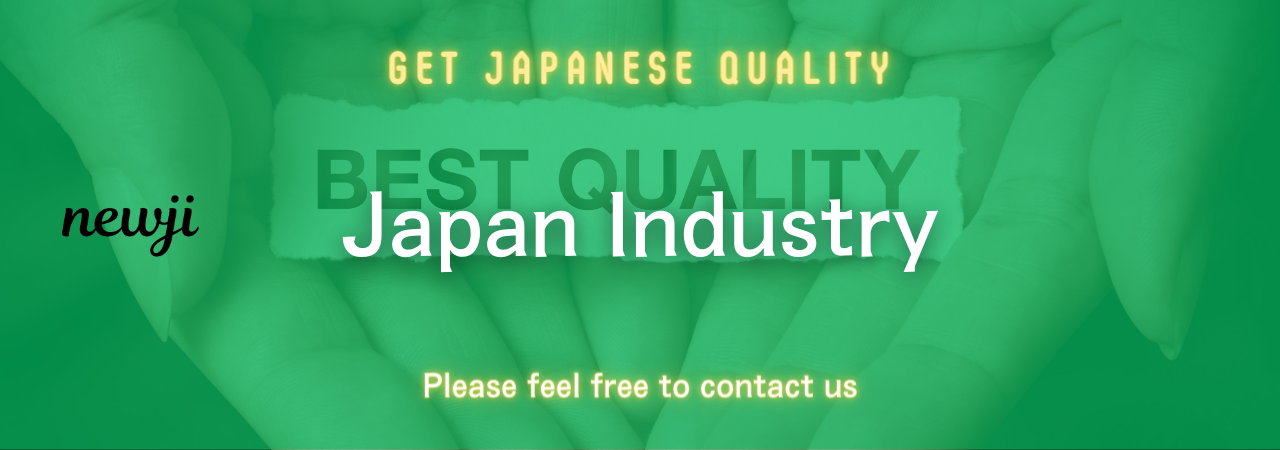
目次
Understanding Failure Analysis in Electronic Component Mounting Boards
Failure analysis is a critical process in enhancing the reliability and performance of electronic component mounting boards.
These boards are integral to numerous electronic devices, meaning their malfunction can lead to significant issues.
The process involves understanding the reasons behind failures and implementing measures to prevent them.
Electronic component mounting boards, often called printed circuit boards (PCBs), serve as the backbone of electronic systems.
They ensure the stable operation of electronic devices by providing both electrical connections and mechanical support.
Given their importance, the need for failure analysis becomes evident in ensuring the longevity and reliability of the devices they support.
Common Causes of Failure in PCBs
Before delving into failure analysis methods, it’s crucial to understand the common causes of failure in PCBs.
Failures can arise from various sources, including:
– **Thermal stress:** High temperatures can lead to thermal expansion, causing the board and its components to crack.
– **Mechanical stress:** Improper handling or mounting can introduce mechanical forces beyond the board’s designed limits.
– **Chemical exposure:** Corrosive environments can deteriorate the material of the PCB.
– **Electromigration:** High current densities can lead to the movement of metal atoms, affecting the circuit’s integrity.
– **Manufacturing defects:** Errors during the production process, such as improper soldering, can lead to future failures.
Understanding these causes is the first step in conducting effective failure analysis and enhancing the reliability of PCBs.
Effective Failure Analysis Methods
There are several methods employed in the failure analysis of electronic component mounting boards.
Each method provides unique insights and helps in diagnosing different types of failures.
Visual Inspection
Visual inspection is often the first step in failure analysis.
It involves a careful examination of the PCB for obvious physical defects.
These can include cracks, discoloration, or soldering issues.
While simple, visual inspection can often pinpoint problems that are immediately apparent to the naked eye.
X-ray Inspection
X-ray inspection provides a non-destructive means to examine the internal structure of a PCB.
This method is particularly useful for detecting issues such as solder joint defects or internal misalignments.
X-ray analysis can reveal connections and alignments not visible through standard visual inspection.
Scanning Electron Microscopy (SEM)
SEM is a more sophisticated analysis method that offers a detailed view at a microscopic level.
It helps in understanding the surface structure and composition of material defects.
SEM can identify surface contaminants or imperfections that lead to failure, which are not visible through simple visual inspections.
Thermal Imaging
Thermal imaging involves analyzing the heat patterns across a PCB.
By identifying hotspots, technicians can pinpoint areas of excessive heat generation that might lead to thermal stress failures.
Thermal imaging is particularly useful for diagnosing overheating issues in real-time use conditions.
Electrical Testing
Electrical testing involves measuring the electrical properties of the PCB to ensure they meet specified parameters.
By testing the continuity, resistance, capacitance, and other electrical characteristics, engineers can identify issues that might impair the board’s electrical performance.
Reliability Testing to Enhance PCB Longevity
Reliability testing goes hand-in-hand with failure analysis, enabling manufacturers to improve the resilience of PCBs under various conditions.
Through simulated environmental tests, the durability and long-term performance of a component are evaluated.
Environmental Stress Screening (ESS)
ESS involves subjecting PCBs to environmental conditions beyond their normal operating conditions.
This includes temperature cycling, vibration testing, and humidity exposure.
ESS helps in identifying potential weak points that might lead to failure when the device is in actual use.
Highly Accelerated Life Testing (HALT)
HALT pushes the product to its operational limits.
By exposing the board to extreme conditions, potential reliability issues can be identified early in the design phase.
HALT testing is crucial in revealing vulnerabilities that typically don’t manifest until after extended periods of use.
Burn-in Testing
Burn-in testing involves operating a PCB under elevated temperature conditions for an extended period.
This test facilitates the early detection of failures and helps to prove the component’s reliability before it leaves the manufacturing facility.
Implementing Improvements from Analysis and Testing
Once analysis and testing are complete, manufacturers need to implement improvements based on the findings.
This can involve redesigning certain board components, adopting new materials, or altering the manufacturing process.
Improving the reliability of electronic component mounting boards ensures that devices meet performance expectations and have longer service lives.
The insights gained from failure analysis and reliability tests are invaluable in maintaining the quality of electronics in an ever-demanding market.
Continuous Improvement
The technology landscape is continually evolving.
As new electronic components emerge, continuous improvement in failure analysis and reliability testing methods becomes essential.
By staying updated with the latest testing techniques and industry standards, companies can better ensure their products’ reliability and success in the marketplace.
By understanding and applying systematic failure analysis and reliability testing, manufacturers can significantly enhance the performance and lifespan of electronic component mounting boards.
This approach not only improves consumer satisfaction but also reduces costs associated with warranty claims and product recalls.
Overall, such practices contribute to the sustained trust and credibility of electronic manufacturers in a competitive industry.
資料ダウンロード
QCD管理受発注クラウド「newji」は、受発注部門で必要なQCD管理全てを備えた、現場特化型兼クラウド型の今世紀最高の受発注管理システムとなります。
ユーザー登録
受発注業務の効率化だけでなく、システムを導入することで、コスト削減や製品・資材のステータス可視化のほか、属人化していた受発注情報の共有化による内部不正防止や統制にも役立ちます。
NEWJI DX
製造業に特化したデジタルトランスフォーメーション(DX)の実現を目指す請負開発型のコンサルティングサービスです。AI、iPaaS、および先端の技術を駆使して、製造プロセスの効率化、業務効率化、チームワーク強化、コスト削減、品質向上を実現します。このサービスは、製造業の課題を深く理解し、それに対する最適なデジタルソリューションを提供することで、企業が持続的な成長とイノベーションを達成できるようサポートします。
製造業ニュース解説
製造業、主に購買・調達部門にお勤めの方々に向けた情報を配信しております。
新任の方やベテランの方、管理職を対象とした幅広いコンテンツをご用意しております。
お問い合わせ
コストダウンが利益に直結する術だと理解していても、なかなか前に進めることができない状況。そんな時は、newjiのコストダウン自動化機能で大きく利益貢献しよう!
(β版非公開)