- お役立ち記事
- Failure occurrence mechanism of solder joints, recurrence prevention/prevention procedures, and countermeasures
Failure occurrence mechanism of solder joints, recurrence prevention/prevention procedures, and countermeasures
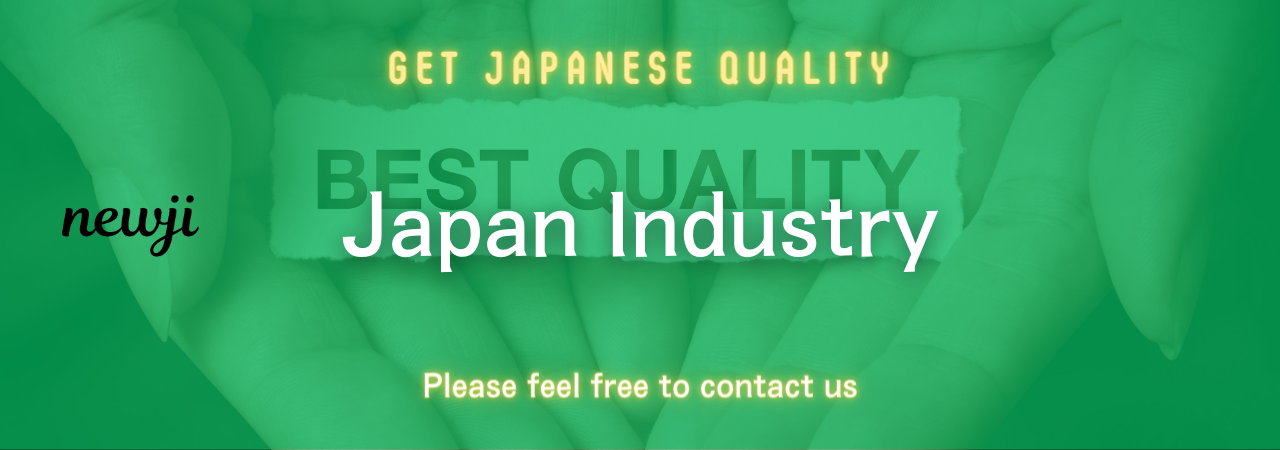
目次
Understanding the Basics of Solder Joints
Solder joints are essential components that connect electronic components to printed circuit boards (PCBs).
They ensure electrical conductivity and mechanical stability.
However, like any other component, solder joints can experience failures.
Understanding the failure mechanisms, as well as ways to prevent and counteract them, is crucial in electronics manufacturing.
Why Do Solder Joints Fail?
Solder joint failures can occur due to various reasons.
One common cause is thermal cycling.
Electronics often undergo temperature changes, which cause expansion and contraction.
This constant change can weaken solder joints over time.
Another reason is mechanical stress.
Physical stress from movements, vibrations, or shocks can lead to fractures in solder joints.
Additionally, environmental factors like humidity and corrosion can degrade solder materials.
Material defects can also be a reason for failure.
If the soldering material was not correctly formulated, it might affect the joint’s integrity.
Similarly, improper soldering during the manufacturing process can leave solder joints vulnerable to failure.
Recognizing Solder Joint Failure Symptoms
Detecting the signs of solder joint failure early can prevent further damage.
Common symptoms include intermittent connectivity issues or complete circuit failure.
If a device functions sporadically or not at all, checking the solder joints should be the first step.
Visual inspections can reveal visible cracks or a dull appearance of the solder, indicating a problem.
Anomalies in device performance, such as unexpected shutoffs or function interruptions, can also suggest bad solder joints.
Ways to Prevent Solder Joint Failures
Preventing solder joint failures begins with selecting the right materials.
High-quality, reliable solder alloys that can withstand the intended environmental conditions will ensure durability.
Design considerations play a vital role too.
Making sure that the layout minimizes stress points and thermal cycles will aid in maintaining joint integrity.
Applying conformal coatings can protect solder joints from environmental factors like moisture or dust.
Lastly, controlling the manufacturing process is crucial.
Using equipment that provides consistent temperatures and ensuring that the solder paste is correctly applied will make a difference.
Furthermore, training for personnel on best soldering practices can mitigate human-error-induced failures.
Preventive Maintenance Strategies
Establishing preventative maintenance routines can extend the life of solder joints.
Regular visual inspections of joints, particularly in high-stress environments, can catch potential issues early.
Implementing a proactive thermal management strategy to regulate device temperatures will undoubtedly reduce thermal cycling stress.
Another effective preventive measure is to apply quality assurance tests.
This includes X-ray inspection and using automatic optical inspection systems to continually monitor the integrity of solder joints.
Effective Procedures for Recurrence Prevention
Once a solder joint failure has been identified and addressed, it’s important to prevent recurrence.
Analyzing the root cause of the failure is the first step.
This might involve reviewing design files, examining the failed joint under a microscope, and considering environmental conditions.
Based on this analysis, you can implement specific changes in materials, design, or processes.
Creating a feedback loop into the manufacturing process will help identify patterns and prevent future issues.
Improving training protocols for assembly line workers and updating them on the latest soldering technologies can bridge knowledge gaps.
It will equip them to handle similar situations better in the future.
Countermeasures for Existing Solder Joint Failures
Addressing existing solder joint failures promptly is critical.
One common countermeasure is reflow soldering, which involves reheating and effectively “resetting” the solder joints.
However, this technique is only viable when the underlying materials and design are deemed sound.
In cases where reflow soldering is insufficient, replacing the entire affected component is necessary.
For severe cases involving multiple failed joints, involving a redesign or consulting with a failure analysis expert might be required to mitigate future occurrences.
Conclusion
The occurrence of solder joint failures is inevitable in the long run, given the dynamic nature of electronics.
However, understanding the mechanisms of failure, along with implementing preventive and corrective measures, significantly reduces their impact.
Design improvements, diligent material selection, and consistent manufacturing practices are the cornerstones of maintaining robust solder joints.
With vigilance, regular maintenance, and training at all levels of manufacturing, solder joint failures will become manageable challenges rather than recurring problems.
This approach ultimately promises enhanced reliability and longevity for electronic devices across the industry.
資料ダウンロード
QCD調達購買管理クラウド「newji」は、調達購買部門で必要なQCD管理全てを備えた、現場特化型兼クラウド型の今世紀最高の購買管理システムとなります。
ユーザー登録
調達購買業務の効率化だけでなく、システムを導入することで、コスト削減や製品・資材のステータス可視化のほか、属人化していた購買情報の共有化による内部不正防止や統制にも役立ちます。
NEWJI DX
製造業に特化したデジタルトランスフォーメーション(DX)の実現を目指す請負開発型のコンサルティングサービスです。AI、iPaaS、および先端の技術を駆使して、製造プロセスの効率化、業務効率化、チームワーク強化、コスト削減、品質向上を実現します。このサービスは、製造業の課題を深く理解し、それに対する最適なデジタルソリューションを提供することで、企業が持続的な成長とイノベーションを達成できるようサポートします。
オンライン講座
製造業、主に購買・調達部門にお勤めの方々に向けた情報を配信しております。
新任の方やベテランの方、管理職を対象とした幅広いコンテンツをご用意しております。
お問い合わせ
コストダウンが利益に直結する術だと理解していても、なかなか前に進めることができない状況。そんな時は、newjiのコストダウン自動化機能で大きく利益貢献しよう!
(Β版非公開)