- お役立ち記事
- Fatigue crack growth prediction and elastic-plastic fracture simulation using FEM
月間76,176名の
製造業ご担当者様が閲覧しています*
*2025年3月31日現在のGoogle Analyticsのデータより
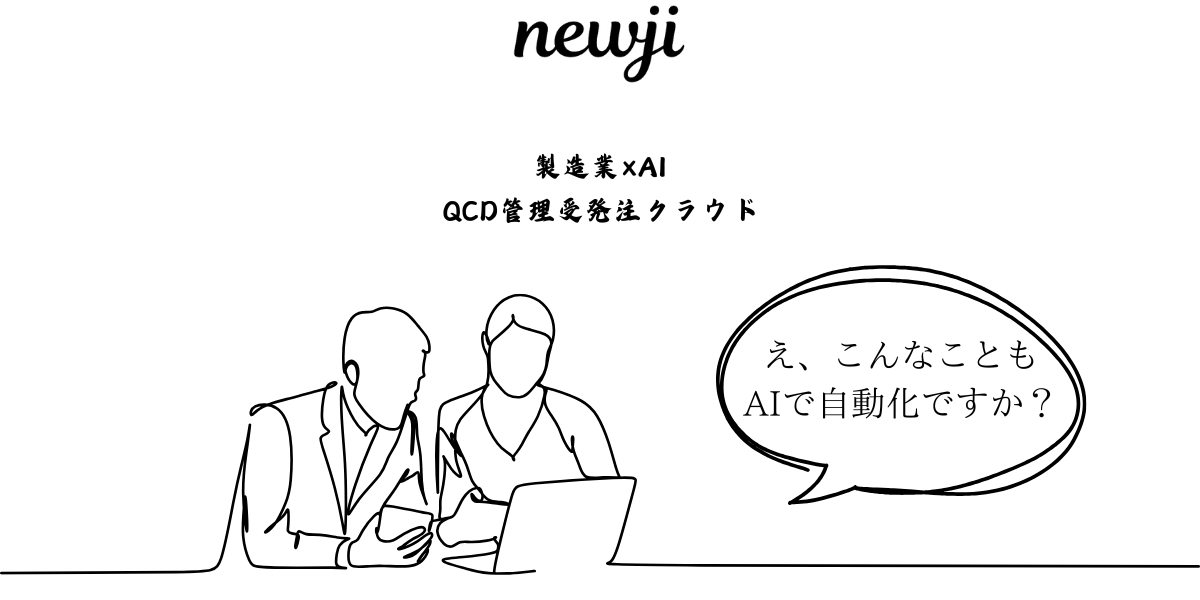
Fatigue crack growth prediction and elastic-plastic fracture simulation using FEM
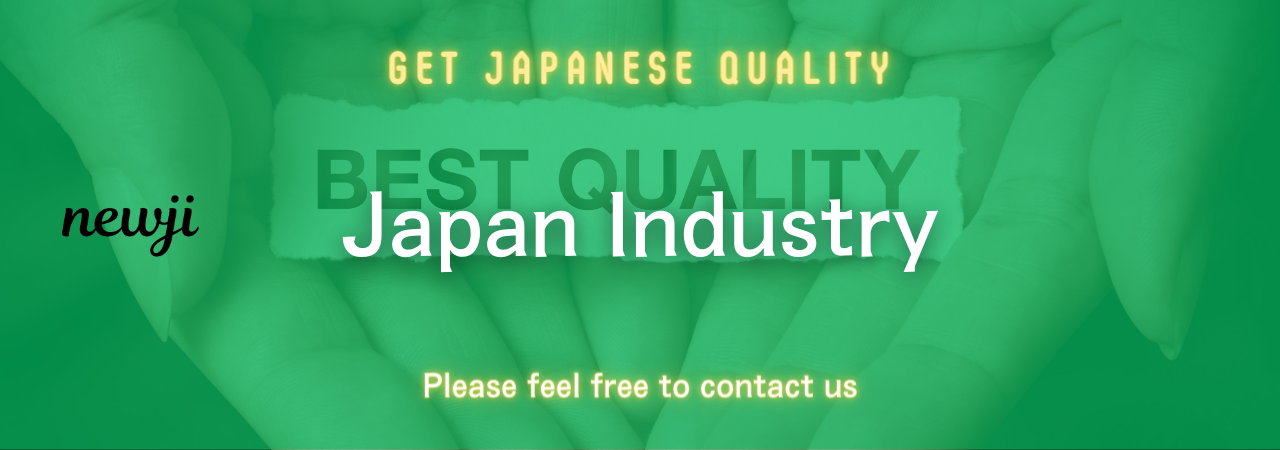
目次
Understanding Fatigue Crack Growth
Fatigue crack growth is an essential concept in material science and engineering, particularly when it comes to the durability and longevity of structures.
When materials are subjected to repeated stress cycles, even if the stress level is well below the yield strength of the material, they can develop fatigue cracks.
These cracks can grow over time and lead to catastrophic failures if not properly managed.
In engineering, predicting and understanding the behavior of these cracks under various conditions is crucial.
This knowledge helps in predicting the lifespan of components and in designing against unexpected breakdowns.
The Role of FEM in Fatigue Analysis
Finite Element Method (FEM) is a numerical technique widely used for performing simulations that involve complex physical phenomena.
One of the key applications of FEM is in the field of fracture mechanics, where it is used to predict fatigue crack growth and simulate elastic-plastic fracture behavior.
By using FEM, engineers can create a computer model of a material and apply forces to see how it behaves under different conditions.
This helps in understanding the progression of fatigue cracks over time and in optimizing the design to increase the material’s lifespan.
Predicting Fatigue Crack Growth
Predicting the growth of fatigue cracks through FEM involves several sophisticated methodologies.
The method uses equations and algorithms to construct a virtual environment, mimicking the real-world behavior of materials under stress.
Modeling the Crack Growth
In FEM, the crack growth is modeled by creating a mesh.
This mesh is essentially a network of elements or grid points that simulate the material’s structure.
As forces are applied, these elements deform and move.
In the case of fatigue, tiny cracks at these weak points can start to grow.
Crack growth modeling can be linear or non-linear, depending on the material and the nature of the applied stresses.
Engineers select the appropriate model to get the most accurate prediction of how a crack might evolve.
Applying the Paris’ Law
One popular model used in fatigue crack growth prediction is the Paris’ Law.
This empirical relationship helps define the rate at which a crack grows as a function of the cyclic load (stress intensity factor range).
The use of Paris’ Law in FEM simulations aids in predicting when a crack will reach a critical size, leading to failure.
This predictive capacity is vital for the maintenance of critical components in safety-sensitive industries like aerospace and automotive.
Elastic-Plastic Fracture Simulation
Apart from predicting fatigue crack growth, FEM is also used to simulate elastic-plastic fracture behavior.
This is important because most engineering materials don’t behave purely elastically; they exhibit both elastic and plastic characteristics when subjected to loads.
Understanding Elastic-Plastic Behavior
Elastic behavior refers to the material’s ability to return to its original shape once the load is removed.
Plastic behavior, on the other hand, involves permanent deformation.
In the real world, materials often show a mix of these behaviors.
Simulating this behavior accurately is crucial for understanding how a material will perform in service and under different loading conditions.
Using FEM for Accurate Simulation
FEM allows engineers to build an accurate representation of elastic-plastic behavior in materials.
This involves defining material properties that describe how it will behave under various stress and strain conditions.
The simulation can then show not just where cracks may form, but how a material might stretch, bend, or deform permanently before a fracture occurs.
This provides engineers with comprehensive data that can be used to refine designs and develop materials with superior performance characteristics.
Benefits of Using FEM in Fracture Mechanics
The use of FEM in fracture mechanics offers a multitude of benefits:
– **Precision:** FEM provides precise simulations and predictions, reducing the chances of unexpected failures.
– **Optimization:** Engineers can test various scenarios and optimize designs virtually before physical prototypes are made.
– **Cost Efficiency:** Conducting virtual tests using FEM is more cost-effective than extensive physical testing.
– **Safety:** By predicting the behavior of materials under operational loads, FEM helps ensure the safety and integrity of structures.
Integrating FEM in Engineering Practice
Incorporating FEM into standard engineering practice requires skilled professionals who can interpret the data and apply it effectively in design and analysis.
With continual advancements in computational power and modeling techniques, FEM’s role in fatigue crack growth prediction and elastic-plastic fracture simulation is expanding.
For engineers, understanding and utilizing FEM is essential for developing materials and structures that meet modern demands for safety, durability, and efficiency.
As technology continues to advance, so too will the capabilities of FEM, opening new possibilities in material science and engineering practice.
In summary, FEM is a powerful tool in the realm of fracture mechanics, enabling engineers to simulate and predict fatigue crack growth and elastic-plastic fracture behavior with precision and accuracy.
This predictive ability not only enhances material performance but also promotes safety across various industries.
資料ダウンロード
QCD管理受発注クラウド「newji」は、受発注部門で必要なQCD管理全てを備えた、現場特化型兼クラウド型の今世紀最高の受発注管理システムとなります。
ユーザー登録
受発注業務の効率化だけでなく、システムを導入することで、コスト削減や製品・資材のステータス可視化のほか、属人化していた受発注情報の共有化による内部不正防止や統制にも役立ちます。
NEWJI DX
製造業に特化したデジタルトランスフォーメーション(DX)の実現を目指す請負開発型のコンサルティングサービスです。AI、iPaaS、および先端の技術を駆使して、製造プロセスの効率化、業務効率化、チームワーク強化、コスト削減、品質向上を実現します。このサービスは、製造業の課題を深く理解し、それに対する最適なデジタルソリューションを提供することで、企業が持続的な成長とイノベーションを達成できるようサポートします。
製造業ニュース解説
製造業、主に購買・調達部門にお勤めの方々に向けた情報を配信しております。
新任の方やベテランの方、管理職を対象とした幅広いコンテンツをご用意しております。
お問い合わせ
コストダウンが利益に直結する術だと理解していても、なかなか前に進めることができない状況。そんな時は、newjiのコストダウン自動化機能で大きく利益貢献しよう!
(β版非公開)