- お役立ち記事
- Fatigue design and failure analysis technology based on the fundamentals of material mechanics/fracture mechanics and reliability engineering
月間76,176名の
製造業ご担当者様が閲覧しています*
*2025年3月31日現在のGoogle Analyticsのデータより
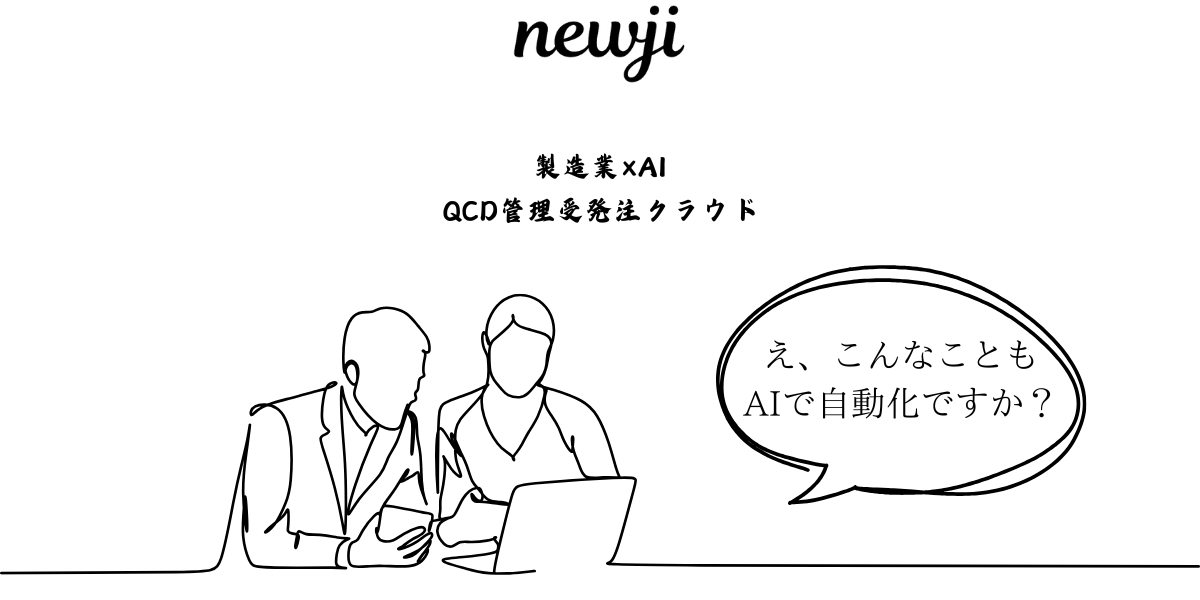
Fatigue design and failure analysis technology based on the fundamentals of material mechanics/fracture mechanics and reliability engineering
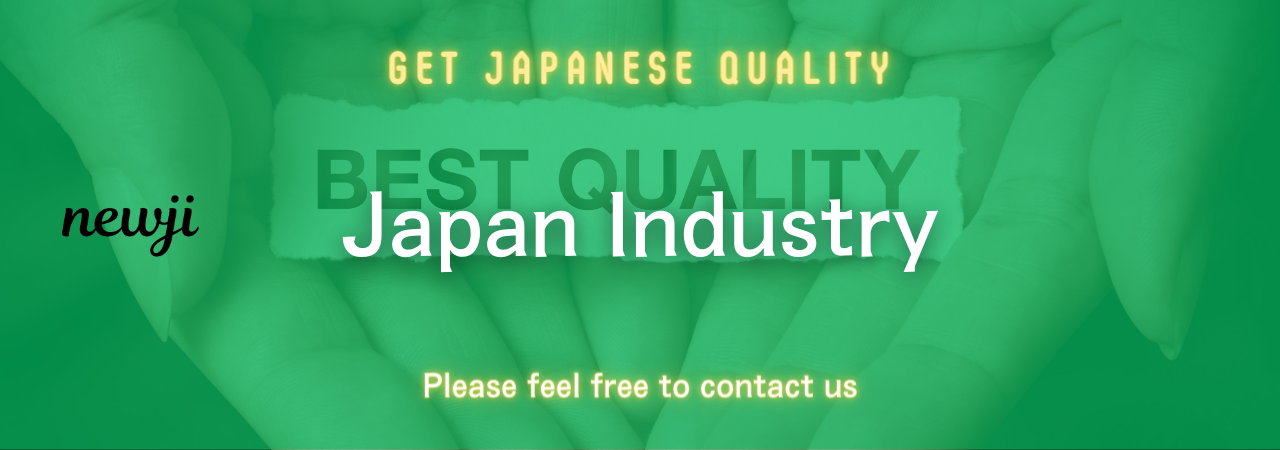
目次
Introduction to Fatigue Design and Failure Analysis
In the world of engineering and material science, understanding how materials behave under stress and fatigue is crucial.
Fatigue design and failure analysis technology is a field that combines the fundamentals of material mechanics, fracture mechanics, and reliability engineering to predict when and how materials will fail.
This ensures that structures and components can be designed to last longer and perform safely over their lifespan.
Understanding Material Mechanics
Material mechanics is the study of how materials respond to various forces and loads.
It focuses on understanding the stress-strain relationship, which is the way a material deforms and strains when a force is applied.
This is the backbone of fatigue design, as it helps engineers predict how materials will behave under repeated stress.
Stress and Strain
Stress is the force applied to a material divided by the area over which the force is distributed.
Strain is the change in shape or size of a material due to this stress.
Understanding these concepts is fundamental to analyzing how materials will react under various conditions.
Fracture Mechanics: Analyzing Cracks and Failures
Fracture mechanics delves into how and why materials crack and eventually fail.
It provides tools and models to predict the growth of cracks in materials under stress, which is critical for avoiding catastrophic failures.
Crack Initiation and Propagation
A key aspect of fracture mechanics is understanding how cracks initiate and propagate.
Small flaws sometimes present in materials can grow over time under repeated stress, leading to failure.
By analyzing these processes, engineers can design materials to resist crack initiation and slow down crack growth.
Reliability Engineering: Ensuring Safety and Longevity
Reliability engineering focuses on ensuring that a system or component performs its intended function without failure over a specified period.
This aspect of fatigue design involves statistical methods to assess and enhance the reliability of materials and structures.
Predictive Modeling
Reliability engineering uses predictive models to estimate the likelihood of failure over time.
These models help engineers design structures that can withstand expected loads and conditions, providing a greater margin of safety.
Integrating Fatigue Design and Failure Analysis
By integrating material mechanics, fracture mechanics, and reliability engineering, fatigue design and failure analysis provide a comprehensive approach to understanding and preventing material failure.
Testing and Simulation
Testing and simulation are key components of this integrated approach.
Engineers use experiments and computer simulations to model how materials will behave under real-world conditions.
This allows for the testing of different scenarios and the optimization of material design for improved performance and reliability.
Applications in Various Industries
Fatigue design and failure analysis are applied across a wide range of industries, from aerospace to automotive to civil engineering.
Aerospace Industry
In the aerospace industry, fatigue analysis ensures that aircraft components can withstand the stresses of flight over countless missions.
Safety is paramount, and rigorous testing is performed to prevent failures that could lead to accidents.
Automotive Industry
The automotive industry uses fatigue design to ensure that vehicle parts endure the stresses of road use without failing prematurely.
This improves vehicle longevity and safety, protecting passengers and reducing maintenance costs.
Civil Engineering
In civil engineering, structures such as bridges and buildings must endure varying loads and environmental conditions.
Fatigue design helps engineers create structures that remain safe and functional over their expected lifetimes.
Conclusion
In conclusion, fatigue design and failure analysis technology is a vital field that combines the fundamentals of material mechanics, fracture mechanics, and reliability engineering.
By understanding how materials behave under stress, predicting crack growth, and ensuring reliability, engineers can design safer and more efficient structures.
This technology not only extends the life of components and structures but also enhances safety across numerous industries, proving its significance in modern engineering.
資料ダウンロード
QCD管理受発注クラウド「newji」は、受発注部門で必要なQCD管理全てを備えた、現場特化型兼クラウド型の今世紀最高の受発注管理システムとなります。
ユーザー登録
受発注業務の効率化だけでなく、システムを導入することで、コスト削減や製品・資材のステータス可視化のほか、属人化していた受発注情報の共有化による内部不正防止や統制にも役立ちます。
NEWJI DX
製造業に特化したデジタルトランスフォーメーション(DX)の実現を目指す請負開発型のコンサルティングサービスです。AI、iPaaS、および先端の技術を駆使して、製造プロセスの効率化、業務効率化、チームワーク強化、コスト削減、品質向上を実現します。このサービスは、製造業の課題を深く理解し、それに対する最適なデジタルソリューションを提供することで、企業が持続的な成長とイノベーションを達成できるようサポートします。
製造業ニュース解説
製造業、主に購買・調達部門にお勤めの方々に向けた情報を配信しております。
新任の方やベテランの方、管理職を対象とした幅広いコンテンツをご用意しております。
お問い合わせ
コストダウンが利益に直結する術だと理解していても、なかなか前に進めることができない状況。そんな時は、newjiのコストダウン自動化機能で大きく利益貢献しよう!
(β版非公開)