- お役立ち記事
- Fatigue Mechanics Basics and Applications for Design and Life Prediction
月間76,176名の
製造業ご担当者様が閲覧しています*
*2025年3月31日現在のGoogle Analyticsのデータより
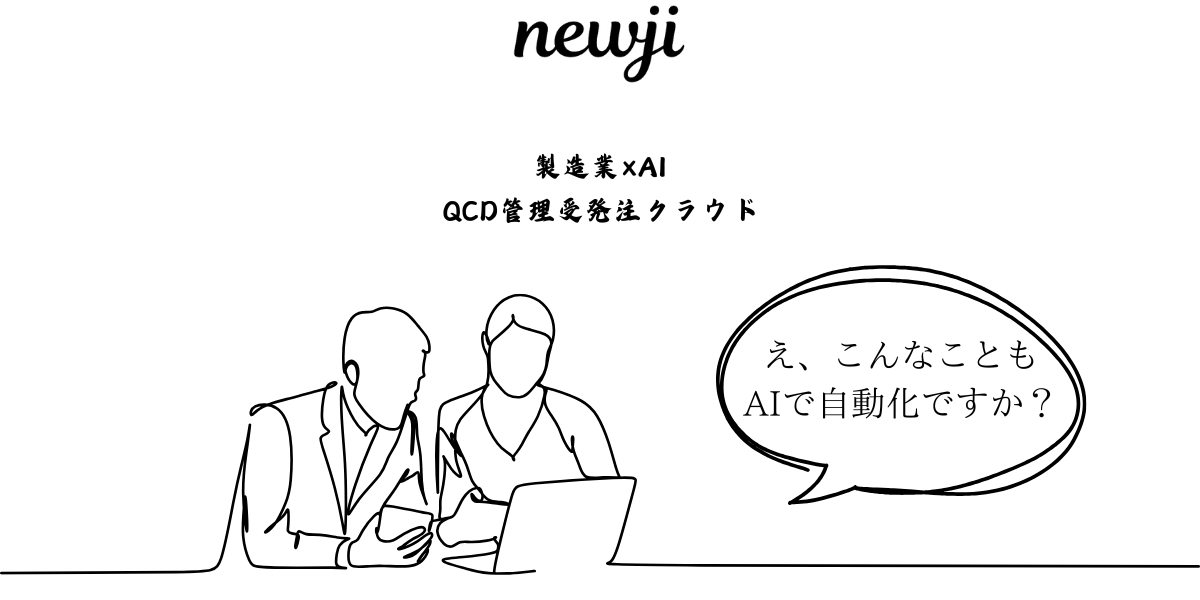
Fatigue Mechanics Basics and Applications for Design and Life Prediction
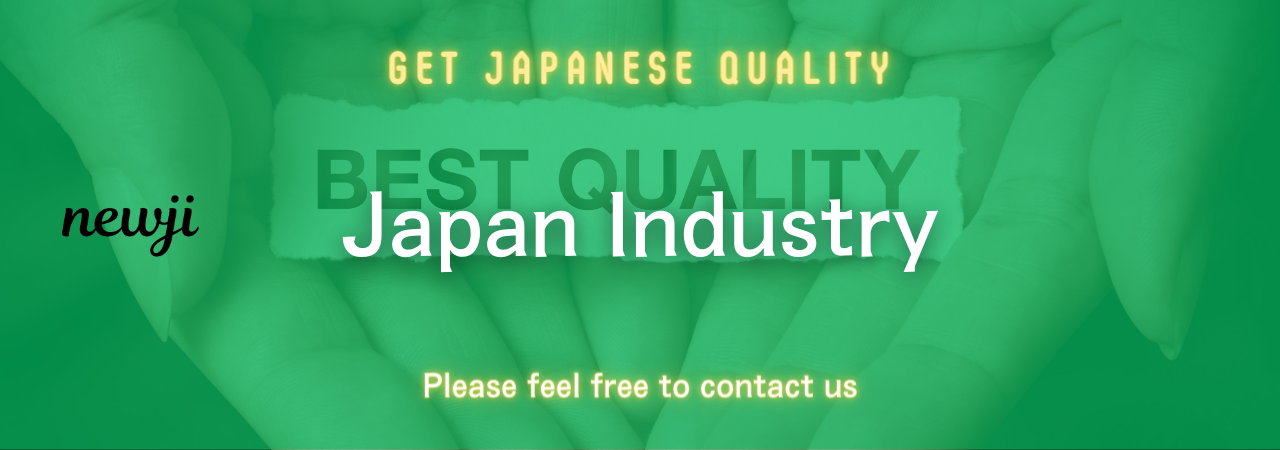
目次
Understanding Fatigue Mechanics
Fatigue mechanics is a crucial concept in the field of material science and engineering.
It refers to the study of materials under cyclic loading conditions, which often leads to the initiation and propagation of cracks, ultimately resulting in failure.
Understanding this concept is vital for engineers and designers to ensure the longevity and durability of various structures and components.
Fatigue is progressive and localized structural damage that occurs when a material is subjected to repeated loading and unloading.
This repetitive stress can cause small cracks to form, which grow over time and can eventually lead to catastrophic failure if not properly managed.
The phenomenon is particularly concerning because it can occur at stress levels significantly lower than the material’s ultimate tensile strength.
Importance of Fatigue in Design
Incorporating fatigue mechanics into design processes is essential for developing products and structures that can withstand cyclic stresses over time.
Engineers need to consider fatigue life during the initial design phase to predict how long a material or component can function safely under expected usage conditions.
Ensuring safety and reliability is paramount, especially in industries such as automotive, aerospace, and civil engineering.
For instance, aircraft components are subject to rigorous fatigue testing because their failure could result in catastrophic outcomes.
Similarly, bridges and other infrastructure are designed to endure frequent loads from traffic and environmental conditions.
Methods for Fatigue Life Prediction
Several methods are employed to predict the fatigue life of materials and components.
S-N Curves
One common approach is the use of S-N curves, which represent the relationship between the cyclic stress amplitude (S) and the number of cycles to failure (N).
These curves help engineers estimate the lifespan of a material when subjected to certain stress levels.
Standardized tests, such as the ASTM E466, are used to generate S-N curves for various materials.
Fracture Mechanics
Fracture mechanics is another method used for predicting fatigue life by focusing on the crack growth rate as a function of cyclic stress intensity.
This approach is beneficial for components that already have cracks or defects, allowing engineers to estimate the remaining life of the component.
Paris’ Law is a well-known equation in fracture mechanics that describes the rate of crack growth.
Factors Affecting Fatigue Life
Several factors can impact the fatigue life of a material or component.
Material Properties
Different materials exhibit varying fatigue characteristics.
Metals, for example, are typically more prone to fatigue than plastics, and within metals, the type of alloy can significantly affect fatigue behavior.
Heat treatment and surface finish also play crucial roles in a material’s susceptibility to fatigue.
Load Conditions
The nature of the applied load, including its magnitude, frequency, and direction, can greatly influence the fatigue life of a material.
Components subjected to high-frequency or high-amplitude loads tend to have a shorter fatigue life.
Additionally, varying load directions can complicate the stress states, possibly accelerating fatigue failure.
Environmental Factors
Environmental conditions such as temperature, humidity, and corrosive environments can exacerbate fatigue.
Corrosion, in particular, can significantly reduce fatigue life by facilitating crack initiation and growth.
Special consideration is required for components exposed to harsh environmental conditions to ensure longevity.
Applications in Engineering
Fatigue mechanics principles are applied across various fields of engineering to enhance product reliability and safety.
Aerospace Engineering
In aerospace engineering, fatigue analysis is critical for the design and maintenance of aircraft components like wings, fuselages, and landing gears.
These components undergo rigorous testing to identify potential fatigue issues and are subject to regular inspections throughout their service life to ensure safety.
Automotive Industry
The automotive industry relies heavily on fatigue analysis for developing and testing vehicle components such as engines, suspensions, and tires.
Fatigue-resistant materials and designs help manufacturers create cars that are both safe and durable.
Fatigue tests ensure that components can withstand the stresses of daily driving and environmental variations.
Civil Engineering
Civil structures like bridges, buildings, and tunnels require careful consideration of fatigue in their design.
Civil engineers use fatigue analysis to ensure that these structures can endure the load cycles from traffic and natural forces, such as wind and seismic activity, over their expected lifespans.
Advancements in Fatigue Mechanics
Recent advancements in technology and materials science have improved fatigue mechanics and life prediction methods.
Computational tools like finite element analysis (FEA) allow engineers to simulate fatigue behavior under various scenarios, identifying potential failure points more accurately.
Additionally, the development of new materials, including composites and advanced alloys, offers improved fatigue resistance.
These materials provide engineers with more options in designing components that perform better under cyclic loading.
In conclusion, a deep understanding of fatigue mechanics is essential in modern engineering to design safe, reliable, and long-lasting structures and components.
By considering factors such as material properties, load conditions, and environmental influences, engineers can predict fatigue life and mitigate potential failures.
As technology continues to advance, fatigue analysis methods will become even more refined, leading to more robust and resilient designs across various industries.
資料ダウンロード
QCD管理受発注クラウド「newji」は、受発注部門で必要なQCD管理全てを備えた、現場特化型兼クラウド型の今世紀最高の受発注管理システムとなります。
ユーザー登録
受発注業務の効率化だけでなく、システムを導入することで、コスト削減や製品・資材のステータス可視化のほか、属人化していた受発注情報の共有化による内部不正防止や統制にも役立ちます。
NEWJI DX
製造業に特化したデジタルトランスフォーメーション(DX)の実現を目指す請負開発型のコンサルティングサービスです。AI、iPaaS、および先端の技術を駆使して、製造プロセスの効率化、業務効率化、チームワーク強化、コスト削減、品質向上を実現します。このサービスは、製造業の課題を深く理解し、それに対する最適なデジタルソリューションを提供することで、企業が持続的な成長とイノベーションを達成できるようサポートします。
製造業ニュース解説
製造業、主に購買・調達部門にお勤めの方々に向けた情報を配信しております。
新任の方やベテランの方、管理職を対象とした幅広いコンテンツをご用意しております。
お問い合わせ
コストダウンが利益に直結する術だと理解していても、なかなか前に進めることができない状況。そんな時は、newjiのコストダウン自動化機能で大きく利益貢献しよう!
(β版非公開)