- お役立ち記事
- Fatigue/strength design and failure analysis of metal materials
月間77,185名の
製造業ご担当者様が閲覧しています*
*2025年2月28日現在のGoogle Analyticsのデータより
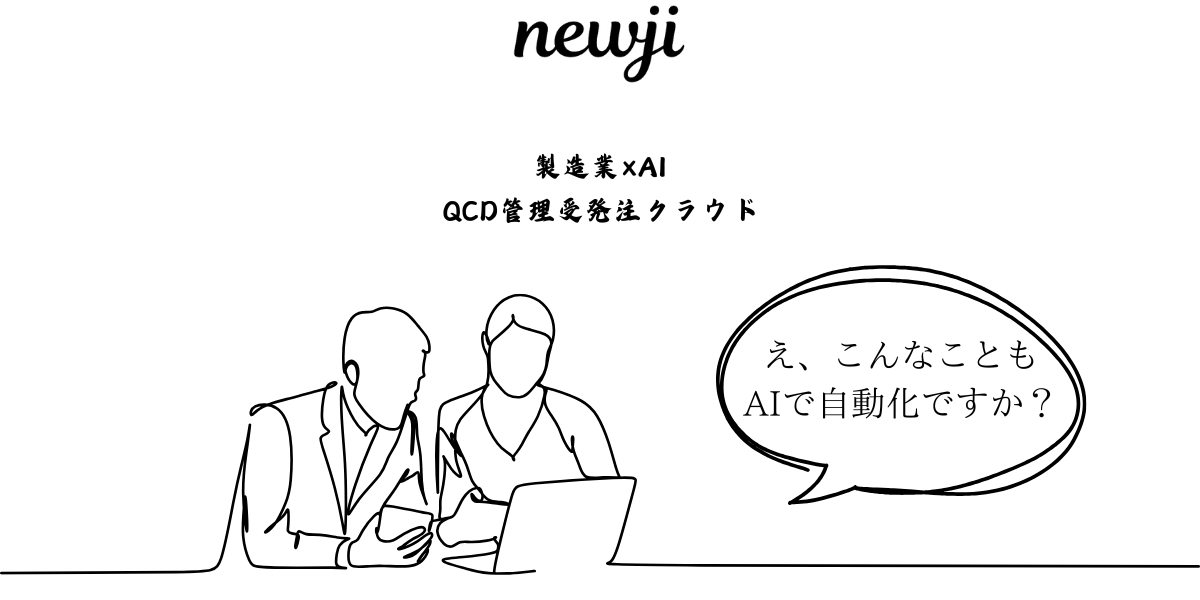
Fatigue/strength design and failure analysis of metal materials
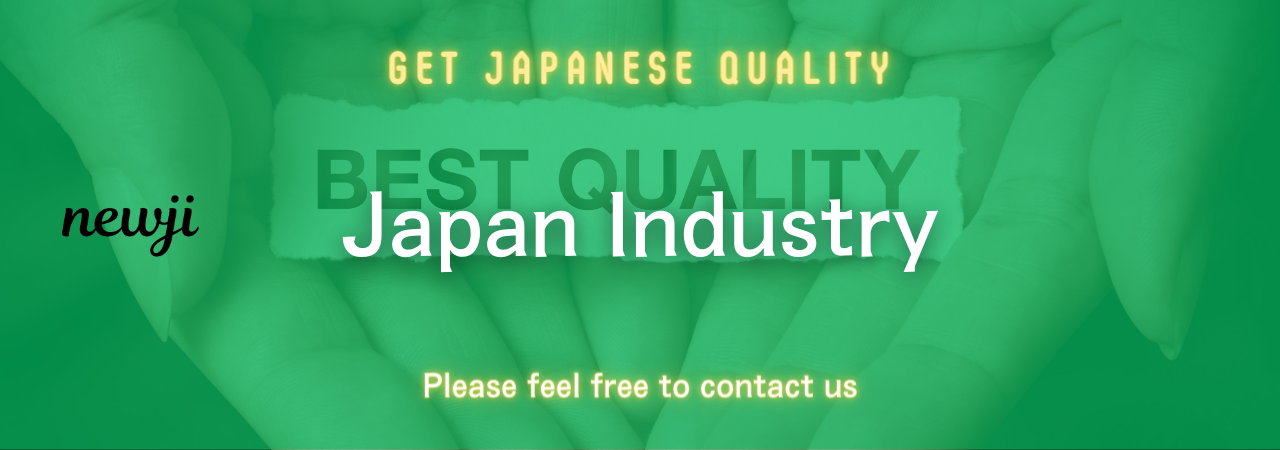
目次
Understanding Fatigue and Strength in Metal Materials
When dealing with metal materials, it is essential to understand both fatigue and strength to ensure that they perform well in their applications.
Metal fatigue refers to the weakening of a material caused by cyclic loading, which can eventually lead to failure.
On the other hand, strength is the ability of the material to withstand an applied force without breaking or deforming.
Metals used in various industries, including aerospace, automotive, and construction, need to be carefully designed and tested to prevent failure in critical applications.
Understanding the balance between fatigue and strength is crucial for engineers and designers to ensure the longevity and safety of metal components.
What is Fatigue in Metal Materials?
Fatigue in metal materials occurs when they are subjected to repeated stress or strain cycles.
Over time, this cycling can cause the material to crack and eventually fail.
Fatigue is a significant concern because it can occur even when the stresses are below the material’s ultimate tensile strength.
The fatigue process typically progresses through three stages: initiation, propagation, and final rupture. During initiation, microscopic cracks develop at stress concentrators, such as surface imperfections or internal defects.
Propagation is when these cracks grow with each stress cycle, eventually leading to a final rupture where the material breaks completely.
The Importance of Fatigue Testing
Engineers perform fatigue testing to predict how a metal will behave under cyclic loading conditions.
This involves subjecting a sample to repeated forces and observing when and how it fails.
By understanding the fatigue life of a material, engineers can determine its suitability for specific applications and make necessary design adjustments.
Fatigue testing also helps in creating S-N curves, which plot the number of cycles a material can endure before failure against the applied stress level.
This curve is a valuable tool for predicting how long a metal component can last under specific conditions and is critical for designers when selecting materials for long-term performance.
Strength Considerations in Metal Materials
The strength of metal materials is defined by their ability to withstand applied forces without failure or excessive deformation.
There are several types of strength parameters to consider, including tensile strength, compressive strength, and shear strength.
1. **Tensile Strength**: This is the maximum stress that a material can withstand while being stretched or pulled before necking or breaking.
2. **Compressive Strength**: This is the ability of a material to withstand loads that would reduce size.
3. **Shear Strength**: This is the ability of a material to withstand forces that can cause the internal structure of the material to slide against itself.
Understanding these strength properties helps engineers choose the appropriate metal for their application, ensuring that it can perform under the expected loads and conditions.
Designing for Strength and Fatigue
Designing metal components with fatigue and strength in mind requires a comprehensive approach.
Engineers consider several factors during the design process to prevent premature failure.
1. **Material Selection**: Choosing the right metal alloy is crucial.
Alloys with high fatigue resistance are often selected for applications involving cyclic loading.
The composition of the metal can greatly affect its fatigue and strength characteristics.
2. **Surface Treatment**: Techniques such as polishing, coating, or shot peening are used to improve the surface finish and reduce stress concentrators, which can be origins for crack initiation.
3. **Load Management**: Proper design includes distributing loads evenly to minimize stress concentrations.
This could involve design changes such as altering shapes or adding fillets to reduce sharp transitions that can increase local stresses.
4. **Regular Inspection and Maintenance**: Even with the best designs, regular inspection and maintenance are key to detecting early signs of fatigue.
This proactive approach can prevent catastrophic failures by addressing issues before they escalate.
Failure Analysis of Metal Components
Failure analysis is performed when metal components fail to determine the cause of the failure.
This process often involves a thorough examination of the failed component, including visual inspections, microscopic examinations, and various tests to understand the causes.
Some common methods used in failure analysis include:
– **Fractography**: This involves examining the fracture surfaces to identify characteristics that provide clues about the failure mode.
– **Metallography**: This method examines the microstructure of the metal to identify any defects or inconsistencies that may have led to failure.
– **Mechanical Testing**: Tests such as hardness tests, tensile tests, and impact tests can provide valuable information about the metal’s properties and the conditions that led to failure.
By conducting these analyses, engineers can gain insight into why a component failed and use this information to improve future designs, materials, or processes.
Conclusion
Understanding fatigue and strength in metal materials is essential for designing durable and reliable components.
By considering factors such as material selection, surface treatments, load management, and regular maintenance, engineers can extend the life of metal components and prevent unexpected failures.
Moreover, failure analysis plays an important role in learning from past failures and enhancing the performance of future designs.
Through a combination of knowledge, analysis, and design considerations, metal components can achieve the desired balance of fatigue resistance and strength necessary for their specific applications.
資料ダウンロード
QCD管理受発注クラウド「newji」は、受発注部門で必要なQCD管理全てを備えた、現場特化型兼クラウド型の今世紀最高の受発注管理システムとなります。
ユーザー登録
受発注業務の効率化だけでなく、システムを導入することで、コスト削減や製品・資材のステータス可視化のほか、属人化していた受発注情報の共有化による内部不正防止や統制にも役立ちます。
NEWJI DX
製造業に特化したデジタルトランスフォーメーション(DX)の実現を目指す請負開発型のコンサルティングサービスです。AI、iPaaS、および先端の技術を駆使して、製造プロセスの効率化、業務効率化、チームワーク強化、コスト削減、品質向上を実現します。このサービスは、製造業の課題を深く理解し、それに対する最適なデジタルソリューションを提供することで、企業が持続的な成長とイノベーションを達成できるようサポートします。
製造業ニュース解説
製造業、主に購買・調達部門にお勤めの方々に向けた情報を配信しております。
新任の方やベテランの方、管理職を対象とした幅広いコンテンツをご用意しております。
お問い合わせ
コストダウンが利益に直結する術だと理解していても、なかなか前に進めることができない状況。そんな時は、newjiのコストダウン自動化機能で大きく利益貢献しよう!
(β版非公開)