- お役立ち記事
- Fatigue testing and durability evaluation methods for composite materials that leaders of quality control departments in the aircraft parts manufacturing industry should know
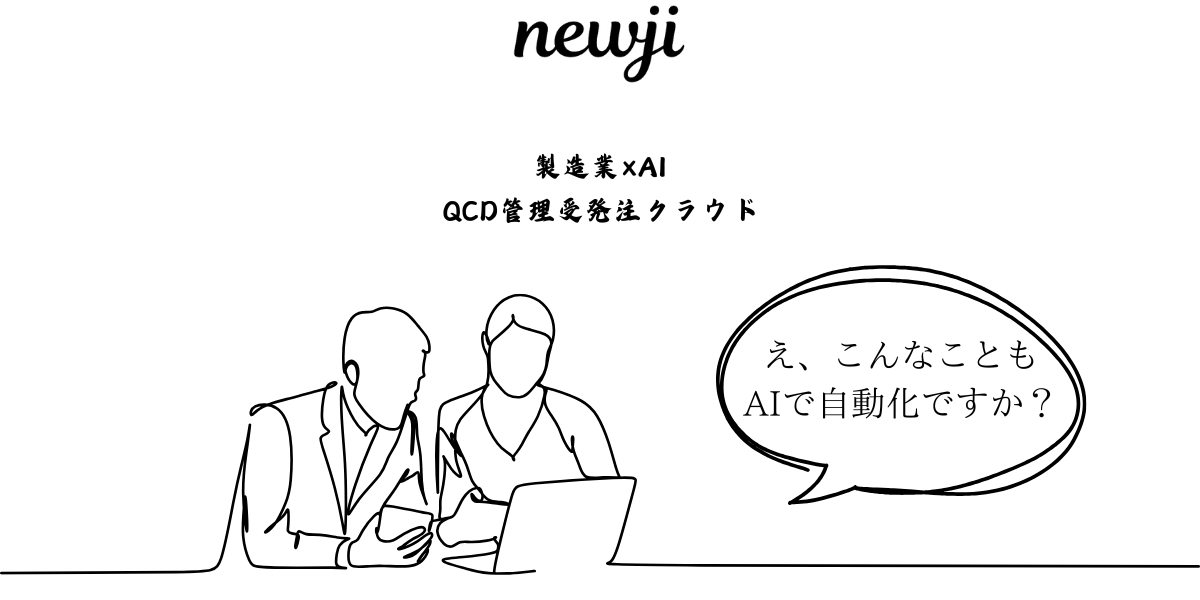
Fatigue testing and durability evaluation methods for composite materials that leaders of quality control departments in the aircraft parts manufacturing industry should know
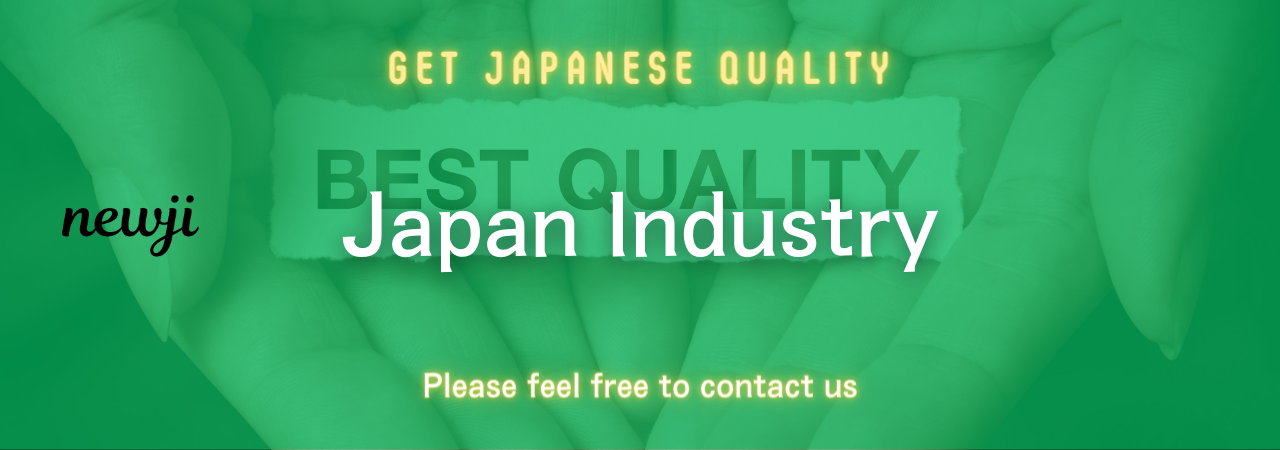
目次
Introduction to Composite Materials in Aircraft Manufacturing
Composite materials are an essential component in the modern aircraft industry.
They are favored for their light weight and high strength, allowing for more efficient and safe aircraft designs.
However, to ensure their reliability and safety, rigorous testing and evaluation methods are required, especially concerning fatigue and durability.
Understanding the various testing methods for these materials is crucial for leaders in quality control departments.
Having this knowledge ensures that components meet industry standards and function appropriately during their lifecycle.
What is Fatigue Testing?
Fatigue testing is a method used to determine how materials can withstand repeated stress over time.
It simulates real-world conditions where materials undergo repeated loading and unloading.
In aircraft parts, fatigue could arise from engines running, take-offs, landings, and turbulence.
To conduct fatigue testing, samples of the composite material are subjected to cyclic loads until failure occurs.
The aim is to generate a fatigue life curve or S-N curve, which represents the relationship between the stress range (S) and the number of cycles to failure (N).
The Importance of Fatigue Testing for Aircraft Components
Fatigue testing is crucial for aircraft components due to safety requirements.
Composite materials may not show visible signs of damage until they fail.
Therefore, understanding their fatigue life helps predict potential failure and improve design.
Furthermore, fatigue testing identifies weaknesses in manufacturing processes.
By analyzing test results, manufacturers can make adjustments to ensure consistent quality and safety.
Durability Evaluation Methods
Durability evaluation involves testing the lifespan and service conditions of composite materials.
It assesses how long a material can perform its intended function without degradation.
Common Durability Tests
1. **Environmental Exposure Tests**: These tests examine how composite materials withstand environmental conditions such as humidity, temperature changes, UV exposure, and chemical exposure.
2. **Mechanical Property Tests**: These tests evaluate the material’s resistance to deformation under mechanical stresses.
It includes tensile, compression, and shear tests.
3. **Impact Testing**: This assesses a material’s ability to absorb energy during an impact, which is crucial for safety in case of collisions or unexpected impacts.
Advanced Testing Methods
With advancements in technology, testing methods for composite materials continue to evolve.
These advanced methods enhance accuracy and provide deeper insights into material behavior.
Non-Destructive Testing (NDT)
NDT methods allow the evaluation of composites without causing damage.
These include ultrasonic testing, radiography, and thermography.
NDT enables continuous monitoring of materials over their service life, ensuring ongoing reliability and safety.
Acoustic Emission Testing
This method involves listening for sound waves emitted by a material under stress.
It’s used to detect the initiation and growth of cracks within composite structures, offering early warning signs of potential failures.
Implementing Testing and Evaluation in Quality Control
For leaders of quality control departments, integrating fatigue testing and durability evaluation into processes is essential.
This involves selecting appropriate testing methods based on the specific material and intended application.
Moreover, training and skilled personnel are vital for conducting tests and interpreting results.
Continuous investment in new testing technologies will enhance capabilities and ensure compliance with international standards.
Key Benefits of Comprehensive Testing
1. **Safety Assurance**: Comprehensive testing ensures components perform safely throughout their lifecycle.
2. **Cost Efficiency**: Identifying potential failures early reduces maintenance and repair costs.
3. **Increased Lifespan**: Understanding durability leads to better maintenance protocols and longer component life.
Conclusion
As the aviation industry continues to innovate, the role of composite materials becomes increasingly significant.
By mastering fatigue testing and durability evaluation, quality control leaders play a vital role in maintaining safety and efficiency in aircraft manufacturing.
Keeping abreast of the latest testing methods and technologies is crucial.
It ensures that composite materials meet the stringent requirements of modern aviation, contributing to the industry’s growth and success.
資料ダウンロード
QCD調達購買管理クラウド「newji」は、調達購買部門で必要なQCD管理全てを備えた、現場特化型兼クラウド型の今世紀最高の購買管理システムとなります。
ユーザー登録
調達購買業務の効率化だけでなく、システムを導入することで、コスト削減や製品・資材のステータス可視化のほか、属人化していた購買情報の共有化による内部不正防止や統制にも役立ちます。
NEWJI DX
製造業に特化したデジタルトランスフォーメーション(DX)の実現を目指す請負開発型のコンサルティングサービスです。AI、iPaaS、および先端の技術を駆使して、製造プロセスの効率化、業務効率化、チームワーク強化、コスト削減、品質向上を実現します。このサービスは、製造業の課題を深く理解し、それに対する最適なデジタルソリューションを提供することで、企業が持続的な成長とイノベーションを達成できるようサポートします。
オンライン講座
製造業、主に購買・調達部門にお勤めの方々に向けた情報を配信しております。
新任の方やベテランの方、管理職を対象とした幅広いコンテンツをご用意しております。
お問い合わせ
コストダウンが利益に直結する術だと理解していても、なかなか前に進めることができない状況。そんな時は、newjiのコストダウン自動化機能で大きく利益貢献しよう!
(Β版非公開)