- お役立ち記事
- Features and advantages of wire EDM in manufacturing
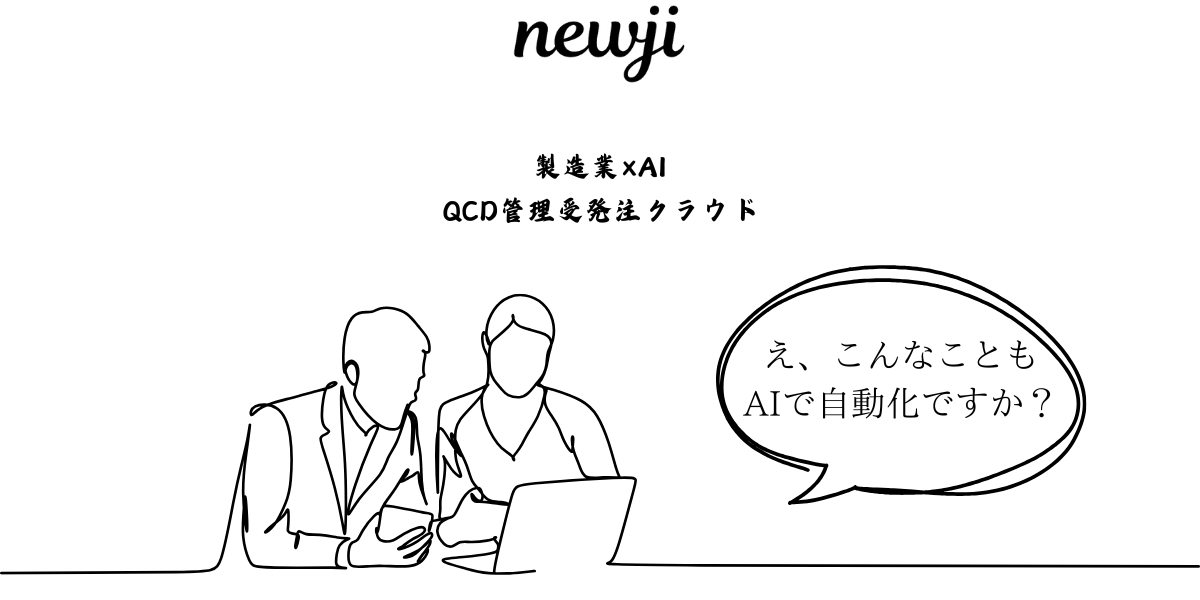
Features and advantages of wire EDM in manufacturing
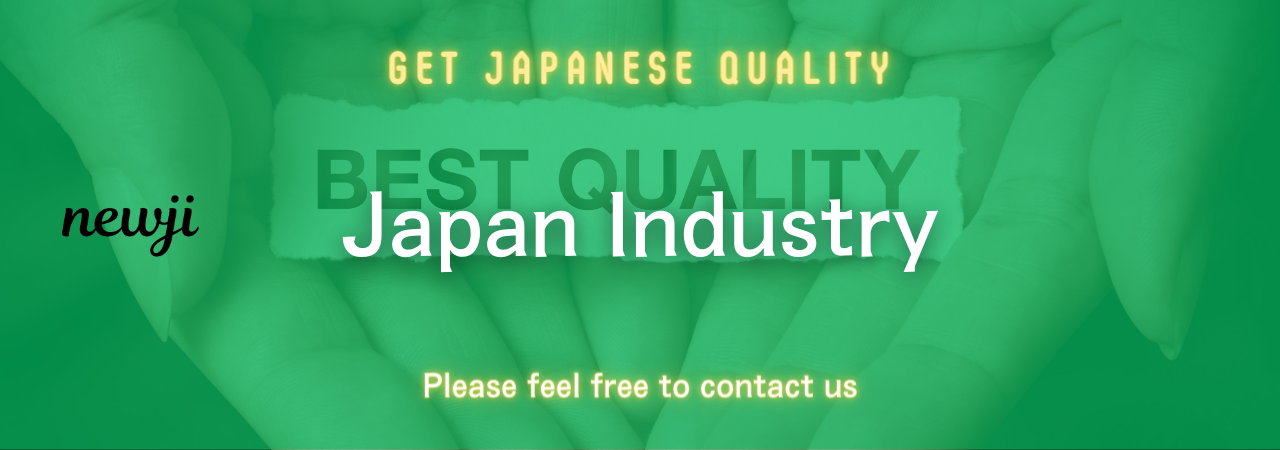
目次
Introduction to Wire EDM
In the manufacturing world, precision is paramount.
Whether creating small intricate parts or large impressive structures, the accuracy of the machining process can make all the difference.
One technology that has stood out for its exceptional precision and versatility is Wire Electrical Discharge Machining, commonly known as Wire EDM.
Wire EDM uses a thin wire, usually made of brass, to cut through metal.
The process relies on electrical discharges, or sparks, between the wire and the material, producing high-precision cuts without ever touching the workpiece.
This technique offers several advantages over traditional machining methods, making it a popular choice in various industries.
Precision and Accuracy
Wire EDM is synonymous with precision.
Engineers and manufacturers often turn to this technology when they need to create parts with tight tolerances.
Traditional machining methods can struggle to achieve the same level of detail, especially on small or complex components.
The precision of Wire EDM comes from its ability to make very fine cuts, sometimes just a few microns wide.
The wire itself is incredibly thin, often less than the diameter of a human hair.
This allows for extremely accurate and delicate cuts, meaning that even the most intricate patterns can be reproduced with high fidelity.
Versatility of Materials
One of the standout features of Wire EDM is its versatility when it comes to materials.
Unlike some machining methods that only work effectively with specific types of metal, Wire EDM can be used with a wide range of materials.
This includes harder metals like titanium and tungsten, as well as softer metals such as aluminum and brass.
Wire EDM can even cut through electrically conductive ceramics and graphite.
This makes it an invaluable tool in sectors like aerospace, automotive, and medical device manufacturing, where the materials used can vary greatly but precision remains consistently critical.
Complex Geometries
The ability to create complex geometries is another advantage of Wire EDM.
Traditional machining techniques often face limitations when dealing with intricate shapes and designs.
However, Wire EDM can easily produce complicated forms that would be difficult or impossible to achieve with other methods.
Whether it’s tight corners, sharp edges, or intricate internal features, Wire EDM can handle it all.
This flexibility is particularly beneficial for industries that require high customization, such as prototyping and small production runs.
Minimal Material Waste
In manufacturing, reducing waste is not just about saving money; it’s also about efficiency and sustainability.
Wire EDM is known for its ability to minimize material waste during the cutting process.
The thinness of the wire means that very little material is removed, resulting in minimal scrap.
Additionally, because Wire EDM doesn’t require physical contact between the tool and the workpiece, there’s less wear and tear on equipment.
This translates to longer tool life and less frequent replacements, further reducing waste and saving costs in the long run.
Surface Finish and Quality
The quality of the surface finish is crucial in many manufacturing processes, particularly those involving high-precision components.
Wire EDM is renowned for producing excellent surface finishes straight out of the machine.
The electrical discharges create smooth cuts without the need for further polishing or finishing.
This high-quality surface finish is especially important in industries like mold making, where the final product’s appearance and functionality depend heavily on the initial machining process.
Being able to achieve such results right off the bat is a significant time and cost saver.
Automation and Efficiency
Modern Wire EDM machines come equipped with advanced automation capabilities.
This allows for unattended machining, which is a substantial benefit in terms of efficiency and productivity.
With automated wire threading and program-controlled operations, manufacturers can run their machines overnight or during weekends, maximizing output without increasing labor costs.
Automation also minimizes the chance of human error, ensuring consistent quality across all parts produced.
This level of efficiency is essential for meeting tight deadlines and maintaining a competitive edge in the market.
Conclusion
Wire EDM offers numerous features and advantages that make it a powerful tool in manufacturing.
From its unmatched precision and versatility in handling various materials, to its ability to produce complex geometries and minimize waste, Wire EDM is a game-changer.
The technique’s excellent surface finish and advanced automation further enhance its appeal, making it an invaluable technology in modern machining.
As industries continue to evolve and demand higher precision and efficiency, the role of Wire EDM will only become more significant.
Whether for prototyping, specialized production, or large-scale manufacturing, Wire EDM’s capabilities ensure it remains at the forefront of machining technologies.
Manufacturers looking to stay ahead in a competitive market would do well to consider the features and advantages offered by Wire EDM, leveraging this technology to achieve their production goals with precision and cost-effectiveness.
資料ダウンロード
QCD調達購買管理クラウド「newji」は、調達購買部門で必要なQCD管理全てを備えた、現場特化型兼クラウド型の今世紀最高の購買管理システムとなります。
ユーザー登録
調達購買業務の効率化だけでなく、システムを導入することで、コスト削減や製品・資材のステータス可視化のほか、属人化していた購買情報の共有化による内部不正防止や統制にも役立ちます。
NEWJI DX
製造業に特化したデジタルトランスフォーメーション(DX)の実現を目指す請負開発型のコンサルティングサービスです。AI、iPaaS、および先端の技術を駆使して、製造プロセスの効率化、業務効率化、チームワーク強化、コスト削減、品質向上を実現します。このサービスは、製造業の課題を深く理解し、それに対する最適なデジタルソリューションを提供することで、企業が持続的な成長とイノベーションを達成できるようサポートします。
オンライン講座
製造業、主に購買・調達部門にお勤めの方々に向けた情報を配信しております。
新任の方やベテランの方、管理職を対象とした幅広いコンテンツをご用意しております。
お問い合わせ
コストダウンが利益に直結する術だと理解していても、なかなか前に進めることができない状況。そんな時は、newjiのコストダウン自動化機能で大きく利益貢献しよう!
(Β版非公開)