- お役立ち記事
- Features and Applications of Wire EDM: Machining Techniques for Precision Machining and Complex Shape Parts
Features and Applications of Wire EDM: Machining Techniques for Precision Machining and Complex Shape Parts
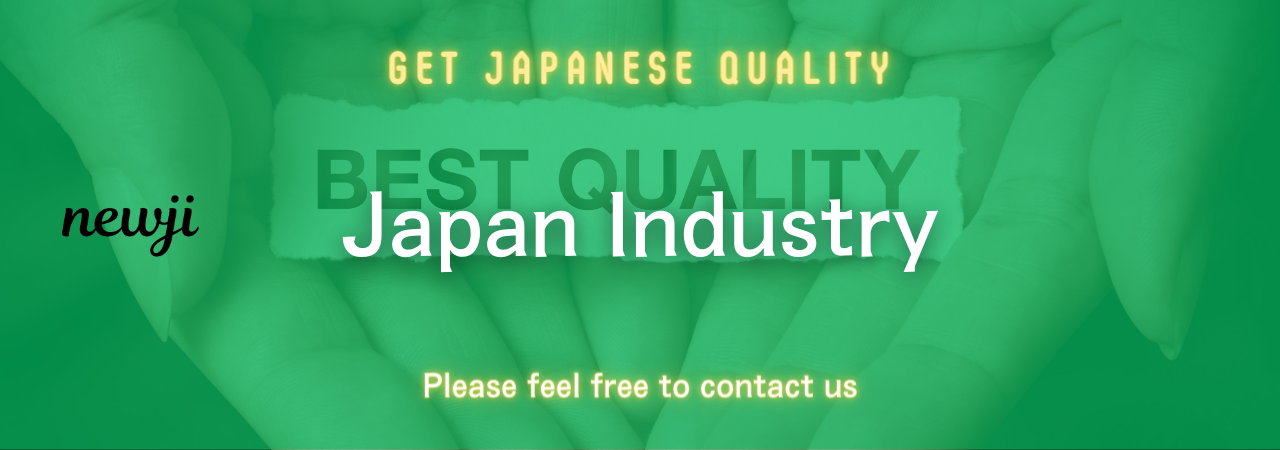
目次
Introduction to Wire EDM
Wire Electrical Discharge Machining, commonly known as Wire EDM, is a specialized machining process that uses an electrically charged wire to cut intricate shapes and precision components from various materials.
The process utilizes the phenomenon of electrical discharge to erode material.
Wire EDM is capable of producing highly accurate and complex parts that traditional machining methods cannot achieve.
In this article, we will explore the features, benefits, and applications of Wire EDM in the realm of precision machining.
What is Wire EDM?
Wire EDM is a non-traditional machining technique.
It employs a thin, electrically charged wire as an electrode to cut materials.
The wire does not make direct contact with the material being cut; instead, it releases electrical discharges or sparks between the wire and the material, which erodes the workpiece.
The eroded material is then flushed away by a dielectric fluid, ensuring a clean and efficient cut.
The Mechanics of Wire EDM
The primary components of a Wire EDM machine include a worktable, wire guide system, power supply, dielectric fluid system, and a control unit.
The electrically charged wire moves in a controlled path to cut the desired shape from the workpiece.
The wire is continuously fed from a spool, ensuring a fresh cutting edge.
The dielectric fluid, often deionized water, acts as an insulator and coolant, preventing overheating and removing eroded particles.
Precise movements are governed by CNC (Computer Numerical Control) units, ensuring accuracy up to micrometer levels.
Basic Steps in Wire EDM
1. **Setup:**
The workpiece is mounted on the worktable, and the wire is threaded through the wire guides.
2. **Programming:**
CNC programming is used to define the cutting path and parameters.
3. **Machining:**
The process begins with the wire generating sparks to erode material along the programmed path.
4. **Flushing:**
The dielectric fluid continuously flushes away eroded material and cools the work area.
5. **Completion:**
The cut part is removed and inspected for precision and accuracy.
Features of Wire EDM
Precision and Accuracy
Wire EDM is renowned for its exceptional precision and accuracy.
Capable of producing parts with tolerances as tight as ±0.001 mm, it is ideal for intricate and complex components.
The CNC control allows for consistent and repeatable cuts, ensuring high-quality results.
Complex Shapes and Geometries
One of the standout features of Wire EDM is its ability to machine complex shapes and geometries.
Traditional machining methods struggle with intricate designs, but Wire EDM can easily handle sharp corners, thin walls, and intricate contours.
This makes it ideal for industries requiring complex components, such as aerospace, medical device manufacturing, and mold making.
Material Versatility
Wire EDM can cut a wide range of conductive materials, including hard metals like titanium, stainless steel, and tungsten, as well as softer metals like aluminum and copper.
It is also effective on materials that are difficult to machine using conventional methods, such as ceramics and composites.
Applications of Wire EDM
Aerospace Industry
In the aerospace industry, precision and reliability are paramount.
Wire EDM is used to manufacture critical components such as turbine blades, engine parts, and landing gear components.
The ability to produce complex shapes with high accuracy ensures the performance and safety of aerospace equipment.
Medical Device Manufacturing
The medical field requires components with exceptional precision and intricate details.
Wire EDM is utilized to produce surgical instruments, implants, and medical devices.
Its accuracy and ability to handle biocompatible materials make it an indispensable tool in medical manufacturing.
Tool and Die Making
Wire EDM is a cornerstone of tool and die making.
It is used to create molds, dies, and punches with intricate features.
The accuracy and repeatability of Wire EDM ensure that the produced tools are of the highest quality, leading to better end products.
Automotive Industry
In the automotive sector, Wire EDM is employed to manufacture parts such as fuel injectors, transmission components, and engine parts.
The process allows for the production of high-precision parts that contribute to the performance and efficiency of vehicles.
Electronics Industry
The miniaturization trend in electronics demands precise and intricate components.
Wire EDM is used to produce connectors, microelectronic components, and intricate circuit board features.
Its ability to handle fine details makes it a valuable asset in electronics manufacturing.
Advantages of Wire EDM
Non-Contact Machining
Since Wire EDM is a non-contact process, it eliminates mechanical stress and deformation on the workpiece.
This is particularly beneficial when working with delicate or thin materials.
High Precision
Wire EDM offers unparalleled precision, making it suitable for applications requiring tight tolerances.
The CNC-controlled wire path ensures consistent and repeatable results, enhancing overall quality.
Complex Shapes
The ability to machine complex shapes and intricate details is one of the key advantages of Wire EDM.
It opens up possibilities for innovative designs and advanced engineering solutions.
Conclusion
Wire EDM stands as a versatile and precise machining method with applications across various industries.
Its ability to produce high-precision and complex parts makes it an invaluable tool for modern manufacturing.
Whether in aerospace, medical device manufacturing, or electronics, Wire EDM offers significant advantages in terms of accuracy, versatility, and efficiency.
As technology advances, Wire EDM continues to evolve, further expanding its capabilities and applications in precision machining.
資料ダウンロード
QCD調達購買管理クラウド「newji」は、調達購買部門で必要なQCD管理全てを備えた、現場特化型兼クラウド型の今世紀最高の購買管理システムとなります。
ユーザー登録
調達購買業務の効率化だけでなく、システムを導入することで、コスト削減や製品・資材のステータス可視化のほか、属人化していた購買情報の共有化による内部不正防止や統制にも役立ちます。
NEWJI DX
製造業に特化したデジタルトランスフォーメーション(DX)の実現を目指す請負開発型のコンサルティングサービスです。AI、iPaaS、および先端の技術を駆使して、製造プロセスの効率化、業務効率化、チームワーク強化、コスト削減、品質向上を実現します。このサービスは、製造業の課題を深く理解し、それに対する最適なデジタルソリューションを提供することで、企業が持続的な成長とイノベーションを達成できるようサポートします。
オンライン講座
製造業、主に購買・調達部門にお勤めの方々に向けた情報を配信しております。
新任の方やベテランの方、管理職を対象とした幅広いコンテンツをご用意しております。
お問い合わせ
コストダウンが利益に直結する術だと理解していても、なかなか前に進めることができない状況。そんな時は、newjiのコストダウン自動化機能で大きく利益貢献しよう!
(Β版非公開)