- お役立ち記事
- Feeder System Optimization Know-How: Improved Efficiency in Press Forming
Feeder System Optimization Know-How: Improved Efficiency in Press Forming
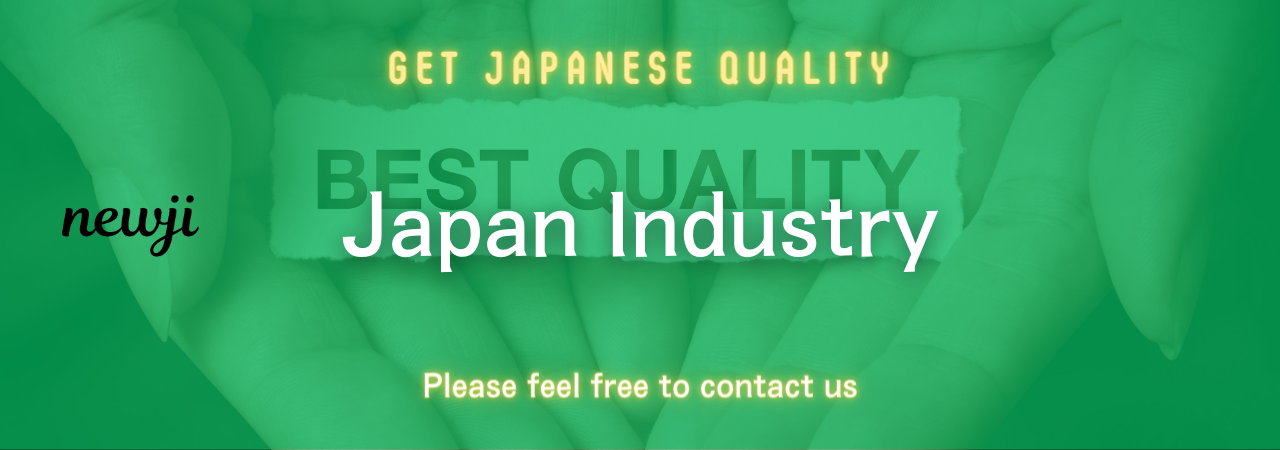
Press forming is a critical process in manufacturing, transforming raw materials into well-defined shapes.
The efficiency of this process can significantly influence production output and quality.
One often overlooked aspect is the feeder system, which ensures a smooth supply of materials into the press.
By optimizing the feeder system, manufacturers can achieve improved efficiency, reduce waste, and enhance overall productivity.
目次
What is a Feeder System?
A feeder system is a mechanism that delivers raw materials into the press forming machine.
It controls the speed, timing, and precision with which the material is fed.
A well-optimized feeder system ensures that the exact amount of material is ready for the press head to form.
Types of Feeder Systems
There are various types of feeder systems, each designed to meet specific needs:
– **Mechanical Feeders**: These utilize mechanical components like gears and cams to feed materials.
– **Servo Feeders**: Relying on servo motors, these offer precise control over feeding speed and position.
– **Air Feeders**: Utilize compressed air to move the material.
– **Roll Feeders**: Use rollers to pull and push material through the system.
Each type has its strengths and weaknesses, and the choice of feeder can greatly impact the press forming process.
Why Optimize the Feeder System?
Enhanced Precision
An optimized feeder system ensures that the material is fed consistently and accurately.
This precision reduces errors in the press forming process, which can lead to a higher quality of the final product.
Increased Speed
By improving the feeder system, you can increase the speed at which materials are delivered to the press.
This can lead to faster production times, allowing for more units to be manufactured in a given period.
Reduced Waste
When the feeder system is optimized, there is less chance of material wastage.
Accurate feeding ensures that only the necessary amount of material is used, reducing scrap and raw material costs.
Improved Safety
A well-maintained and optimized feeder system can also reduce the risk of accidents.
When the system operates smoothly, it minimizes the chances of malfunctions that could pose hazards to operators.
Steps to Optimize the Feeder System
Evaluate Current System Performance
Begin by assessing the current performance of your feeder system.
Identify any bottlenecks or areas where the system may be failing to deliver materials effectively.
Gather data on feed rates, accuracy, and downtime to understand where improvements are needed.
Upgrade Technology
Consider upgrading to more advanced feeder systems.
Servo feeders, for instance, offer superior precision and control compared to mechanical or air feeders.
Investing in new technology can have significant long-term benefits.
Regular Maintenance
Regular maintenance is crucial for keeping the feeder system running smoothly.
Perform routine checks to ensure all components are in good working condition.
Address any wear and tear promptly to avoid disruptions in the feeding process.
Train Staff
Ensure that your staff is well-trained to operate and maintain the feeder system.
Proper training can prevent operator errors and enhance the overall efficiency of the system.
Implement Automation
Automation can greatly enhance the efficiency of feeder systems.
Automated systems can precisely control feed rates and timings, reducing the need for manual intervention.
This can lead to more consistent production outcomes.
Benefits of Feeder System Optimization
Cost Savings
By reducing material waste and increasing production speed, optimizing the feeder system can lead to significant cost savings.
You’ll use less raw material and produce more units in less time, enhancing your bottom line.
Quality Improvement
An optimized feeder system ensures precision in the press forming process, resulting in higher quality products.
This can lead to better customer satisfaction and fewer returns or complaints.
Boosted Productivity
Increased efficiency means that your production line can handle more tasks in a shorter amount of time.
This boost in productivity can help you meet higher demand and expand your market reach.
Energy Efficiency
Optimizing the feeder system can also contribute to energy efficiency.
More efficient feeding means that the press forming machine operates smoothly, consuming less power and reducing operating costs.
Challenges in Feeder System Optimization
Initial Investment
Upgrading or optimizing a feeder system may require a significant initial investment.
While the long-term benefits are substantial, the upfront costs can be a barrier for some manufacturers.
Complexity in Retrofit
If you’re integrating a new feeder system into an existing press, retrofitting can be complex.
It may require modifications to ensure compatibility, which can be time-consuming and costly.
Training Requirements
Staff will need to be trained on new feeder technologies or optimized systems.
Training can take time and may temporarily slow down production until employees are fully proficient.
Conclusion
Optimizing the feeder system in press forming is a strategic move that can lead to improved efficiency, reduced waste, and enhanced overall productivity.
By evaluating current system performance, investing in upgrades, maintaining equipment, training staff, and implementing automation, manufacturers can overcome challenges and reap substantial benefits.
While the process may require an initial investment and some complexity in execution, the long-term gains in cost savings, quality improvement, and increased productivity make it a worthwhile endeavor.
In the competitive manufacturing landscape, a fine-tuned feeder system can be a decisive factor in achieving operational excellence.
資料ダウンロード
QCD調達購買管理クラウド「newji」は、調達購買部門で必要なQCD管理全てを備えた、現場特化型兼クラウド型の今世紀最高の購買管理システムとなります。
ユーザー登録
調達購買業務の効率化だけでなく、システムを導入することで、コスト削減や製品・資材のステータス可視化のほか、属人化していた購買情報の共有化による内部不正防止や統制にも役立ちます。
NEWJI DX
製造業に特化したデジタルトランスフォーメーション(DX)の実現を目指す請負開発型のコンサルティングサービスです。AI、iPaaS、および先端の技術を駆使して、製造プロセスの効率化、業務効率化、チームワーク強化、コスト削減、品質向上を実現します。このサービスは、製造業の課題を深く理解し、それに対する最適なデジタルソリューションを提供することで、企業が持続的な成長とイノベーションを達成できるようサポートします。
オンライン講座
製造業、主に購買・調達部門にお勤めの方々に向けた情報を配信しております。
新任の方やベテランの方、管理職を対象とした幅広いコンテンツをご用意しております。
お問い合わせ
コストダウンが利益に直結する術だと理解していても、なかなか前に進めることができない状況。そんな時は、newjiのコストダウン自動化機能で大きく利益貢献しよう!
(Β版非公開)