- お役立ち記事
- Feeder System Optimization Know-How: Improving Efficiency in Press Processing
Feeder System Optimization Know-How: Improving Efficiency in Press Processing
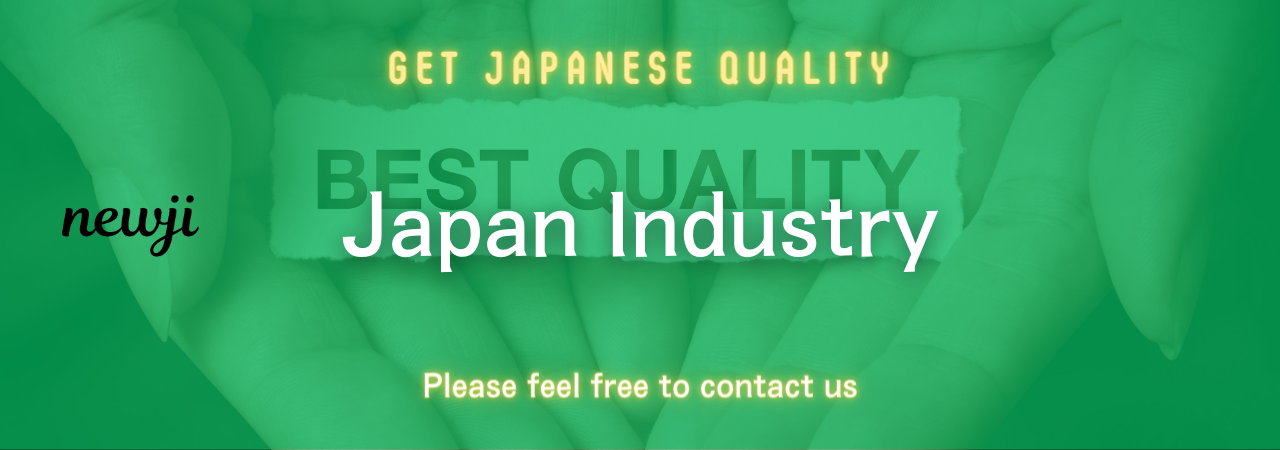
目次
Understanding Feeder Systems in Press Processing
Feeder systems are integral components of press processing, ensuring materials are delivered in an orderly and efficient manner.
Without a well-optimized feeder system, productivity can suffer, leading to delays and increased operational costs.
Understanding the basics of feeder systems helps in recognizing the areas that need improvement.
What is a Feeder System?
A feeder system in press processing refers to the automated mechanism that supplies raw material into the press machine.
It ensures continuous production by maintaining a steady flow of material.
Feeder systems come in various designs depending on the type of press and material being used, such as roll feeders, bowl feeders, and vibratory feeders.
The Importance of Optimizing Feeder Systems
Optimizing feeder systems is crucial for several reasons.
Firstly, it maximizes production efficiency by minimizing downtime and material waste.
Well-optimized systems ensure materials are fed at the right pace and quantity, preventing bottlenecks in the production line.
Secondly, optimized feeders reduce wear and tear on machinery.
When material is supplied consistently and correctly, the press operates smoothly, reducing the likelihood of jams and mechanical failures.
Lastly, a well-optimized feeder system can significantly lower production costs.
It minimizes energy consumption and material waste, leading to a more cost-effective production process.
Key Factors in Feeder System Optimization
Several factors contribute to the optimization of feeder systems in press processing.
Material Type and Properties
Understanding the type and properties of the material being processed is fundamental.
Different materials require different handling methods.
For instance, metals need sturdy systems that can manage their weight and rigidity, while plastics may require gentler handling to prevent damage.
Feeder System Design
The design of the feeder system should match the specific requirements of the production line.
Roll feeders are ideal for continuous feed applications, while bowl feeders are perfect for sorting and feeding small components.
Choosing the right feeder design ensures smooth material flow and minimizes interruptions.
Feeder Speed and Timing
Feeder speed and timing are crucial elements.
The feeder must deliver material at a pace that matches the press’s operational speed to avoid overloading or underfeeding.
Automated systems with precise control mechanisms can adjust the feed rate in real time, ensuring synchronization with the press.
Regular Maintenance and Upgrades
Regular maintenance of feeder systems prevents unexpected breakdowns and extends their lifespan.
Periodic checks and prompt repairs keep the system in optimal condition.
Upgrading to the latest technology can also enhance performance, with modern feeders offering improved efficiency and reliability.
Steps to Optimize Feeder Systems
Optimizing feeder systems involves several strategic steps.
Conducting a Thorough Analysis
The first step is a comprehensive analysis of the current feeder system.
Identify any bottlenecks or inefficiencies in the material flow.
Gather data on feeder performance, including feed rates, downtime incidents, and material waste.
Choosing the Right Feeder System
Based on the analysis, select a feeder system that suits your specific needs.
Consider factors like material type, production speed, and precision requirements.
Consulting with feeder system manufacturers can provide insights into the best options available.
Implementing Automation
Automating the feeder system can significantly enhance efficiency.
Automated feeders adjust the feed rate in real time, ensuring consistent material flow.
They can also detect and respond to issues faster than manual systems, reducing the risk of downtime.
Regular Monitoring and Adjustments
Continuous monitoring of the feeder system is essential for sustained optimization.
Implement sensors and feedback mechanisms to track performance metrics.
Use this data to make necessary adjustments, ensuring the system operates at peak efficiency.
Benefits of an Optimized Feeder System
An optimized feeder system brings numerous benefits to press processing operations.
Increased Productivity
With a steady and accurate flow of materials, the production line operates smoothly without interruptions.
This leads to higher output rates and increased overall productivity.
Reduced Operational Costs
Efficient feeder systems minimize material waste and energy consumption.
This translates into lower operational costs, saving money in the long run.
Improved Product Quality
Consistent and accurate material feeding ensures the press produces components with uniform quality.
This reduces the number of defective products and enhances overall quality control.
Conclusion
Feeder system optimization is a critical aspect of improving efficiency in press processing.
By understanding the fundamental principles, analyzing the current system, and implementing strategic improvements, manufacturers can achieve significant gains in productivity and cost savings.
Regular maintenance, the right feeder design, and automation are all essential components of a well-optimized feeder system.
資料ダウンロード
QCD調達購買管理クラウド「newji」は、調達購買部門で必要なQCD管理全てを備えた、現場特化型兼クラウド型の今世紀最高の購買管理システムとなります。
ユーザー登録
調達購買業務の効率化だけでなく、システムを導入することで、コスト削減や製品・資材のステータス可視化のほか、属人化していた購買情報の共有化による内部不正防止や統制にも役立ちます。
NEWJI DX
製造業に特化したデジタルトランスフォーメーション(DX)の実現を目指す請負開発型のコンサルティングサービスです。AI、iPaaS、および先端の技術を駆使して、製造プロセスの効率化、業務効率化、チームワーク強化、コスト削減、品質向上を実現します。このサービスは、製造業の課題を深く理解し、それに対する最適なデジタルソリューションを提供することで、企業が持続的な成長とイノベーションを達成できるようサポートします。
オンライン講座
製造業、主に購買・調達部門にお勤めの方々に向けた情報を配信しております。
新任の方やベテランの方、管理職を対象とした幅広いコンテンツをご用意しております。
お問い合わせ
コストダウンが利益に直結する術だと理解していても、なかなか前に進めることができない状況。そんな時は、newjiのコストダウン自動化機能で大きく利益貢献しよう!
(Β版非公開)