- お役立ち記事
- Five measures that purchasing departments should implement in supply chain crisis management
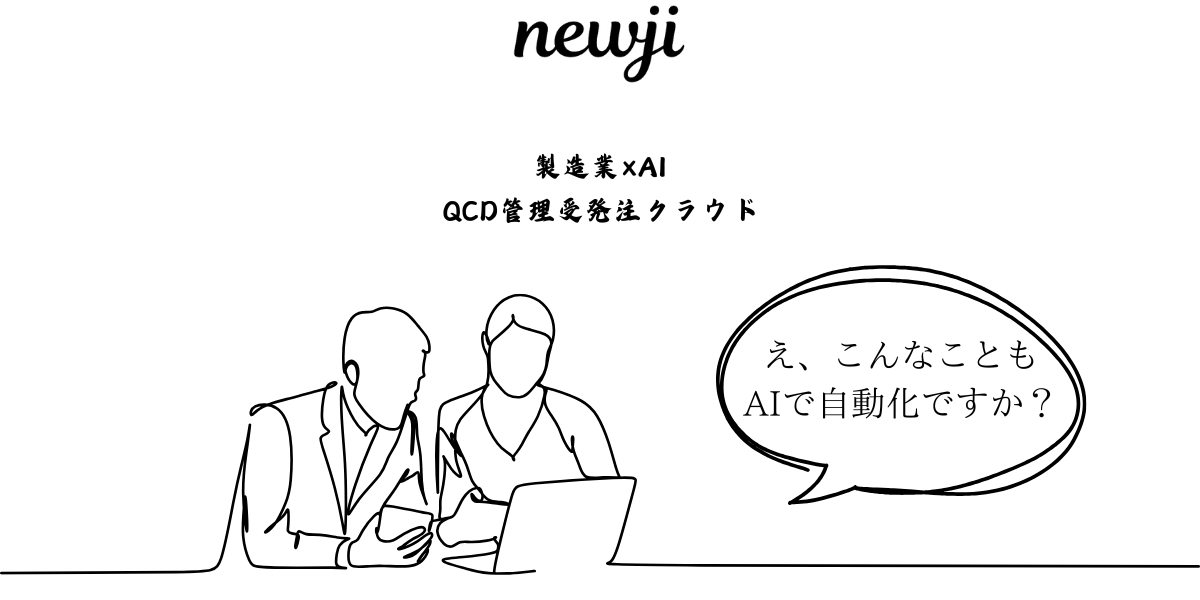
Five measures that purchasing departments should implement in supply chain crisis management
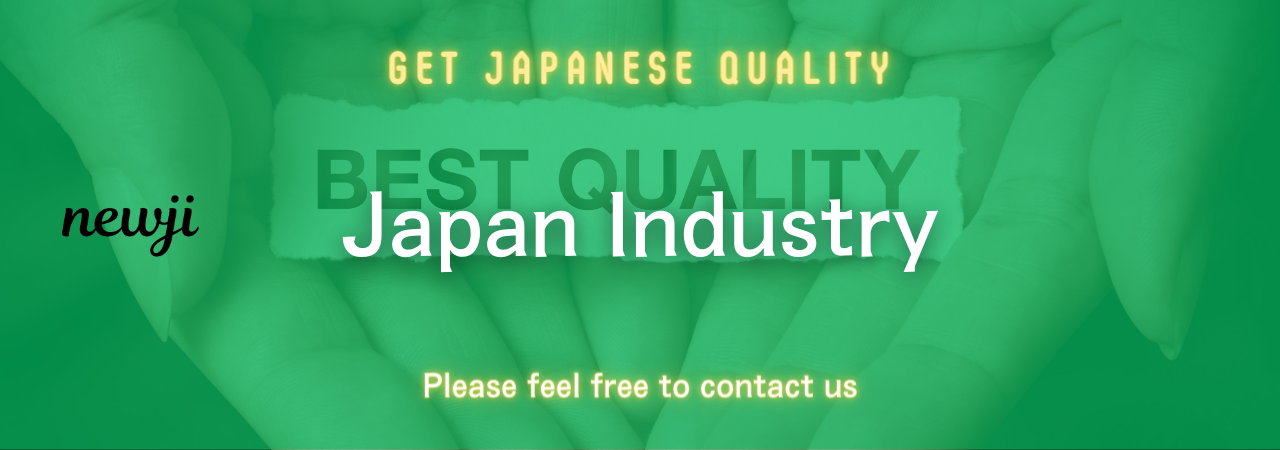
目次
Understanding Supply Chain Crisis Management
Supply chain crisis management refers to the various strategies and actions implemented by organizations, specifically purchasing departments, to handle disruptions within the supply chain effectively.
These disruptions can stem from several factors, including natural disasters, geopolitical tensions, financial instability, and sudden spikes in demand.
In today’s interconnected and globalized world, the importance of effective supply chain crisis management cannot be overstated.
An efficient approach ensures continuity of operations, minimizes financial losses, and maintains brand reputation.
Measure 1: Risk Assessment and Mitigation
Risk assessment is a crucial first step in managing supply chain crises.
Purchasing departments must assess potential risks associated with their supply chains, identifying vulnerabilities that could be exploited during a crisis.
By conducting detailed analysis and evaluations, departments can understand potential impacts on supply availability, cost, and delivery schedules.
Once risks are identified, it’s important to develop strategies for risk mitigation.
This includes diversifying suppliers, implementing contingency plans, and possibly investing in technology that provides real-time insights into supply chain operations.
Regularly updating risk assessments ensures that purchasing departments are well-prepared for potential disruptions.
Measure 2: Supplier Relationship Management
Building strong relationships with suppliers is a critical measure in effective crisis management.
Maintaining open and ongoing communication helps purchasing departments stay informed about potential issues suppliers may face and work collaboratively to find solutions.
This ensures that suppliers prioritize your needs, especially during high-demand periods or disruptions.
Furthermore, establishing long-term contracts with clear terms and expectations helps solidify these relationships.
Developing relationships with multiple vendors also provides flexibility and options should one supplier become unable to meet demands.
In cases of geopolitical or market changes, having alternative suppliers can mitigate risk significantly.
Measure 3: Inventory Management Strategies
Proper inventory management is essential during a supply chain crisis.
Purchasing departments need to balance having enough stock to meet demand while avoiding excess that could lead to increased costs or waste.
Adopting strategies like just-in-time inventory can reduce holding costs and ensure that products are received only as needed.
However, in anticipation of potential supply chain disruptions, implementing a buffer or safety stock strategy might be wise, providing extra inventory to cushion against shortages.
Inventory management software can also help track stock levels, predict demand, and optimize inventory across multiple locations, offering the purchasing department better control and insight.
Measure 4: Technology and Data Utilization
Utilizing technology and data analytics can significantly enhance a purchasing department’s ability to manage supply chain crises.
Advanced software and data-driven insights help predict potential disruptions by analyzing market trends, weather patterns, political climates, and financial fluctuations.
This predictive capability allows departments to act proactively, making informed decisions to circumvent potential issues.
Technological solutions such as blockchain can enhance transparency and traceability across the supply chain, ensuring accountability and reliability.
Automation tools can expedite processes, reducing the time needed to address emerging crises.
Integrating technology provides a more resilient and responsive supply chain management approach.
Measure 5: Continuous Improvement and Training
Continuous improvement is vital for a purchasing department to remain agile and resilient in the face of supply chain crises.
By regularly reviewing and refining crisis management strategies, departments can stay ahead of industry trends and adapt to changing circumstances.
Investing in training programs ensures that the team understands the latest tools, technologies, and methodologies in supply chain management.
Cross-training staff members allows for flexibility in roles during times of crisis, ensuring that operations continue smoothly despite personnel changes or increased demand.
Encouraging a culture of learning and adaptation not only prepares the department for crises but also fosters innovation and efficiency.
Conclusion
An effective supply chain crisis management strategy is essential for any purchasing department.
By implementing the five measures discussed—risk assessment and mitigation, supplier relationship management, inventory management strategies, technology and data utilization, and continuous improvement and training—departments can minimize disruptions and maintain business continuity.
The ever-evolving nature of the global economy makes it imperative for organizations to stay vigilant and prepared for any scenario.
By anticipating potential challenges and implementing robust strategies, purchasing departments can protect their supply chains and ensure their organization’s long-term success.
資料ダウンロード
QCD調達購買管理クラウド「newji」は、調達購買部門で必要なQCD管理全てを備えた、現場特化型兼クラウド型の今世紀最高の購買管理システムとなります。
ユーザー登録
調達購買業務の効率化だけでなく、システムを導入することで、コスト削減や製品・資材のステータス可視化のほか、属人化していた購買情報の共有化による内部不正防止や統制にも役立ちます。
NEWJI DX
製造業に特化したデジタルトランスフォーメーション(DX)の実現を目指す請負開発型のコンサルティングサービスです。AI、iPaaS、および先端の技術を駆使して、製造プロセスの効率化、業務効率化、チームワーク強化、コスト削減、品質向上を実現します。このサービスは、製造業の課題を深く理解し、それに対する最適なデジタルソリューションを提供することで、企業が持続的な成長とイノベーションを達成できるようサポートします。
オンライン講座
製造業、主に購買・調達部門にお勤めの方々に向けた情報を配信しております。
新任の方やベテランの方、管理職を対象とした幅広いコンテンツをご用意しております。
お問い合わせ
コストダウンが利益に直結する術だと理解していても、なかなか前に進めることができない状況。そんな時は、newjiのコストダウン自動化機能で大きく利益貢献しよう!
(Β版非公開)