- お役立ち記事
- FMEA practical points
FMEA practical points
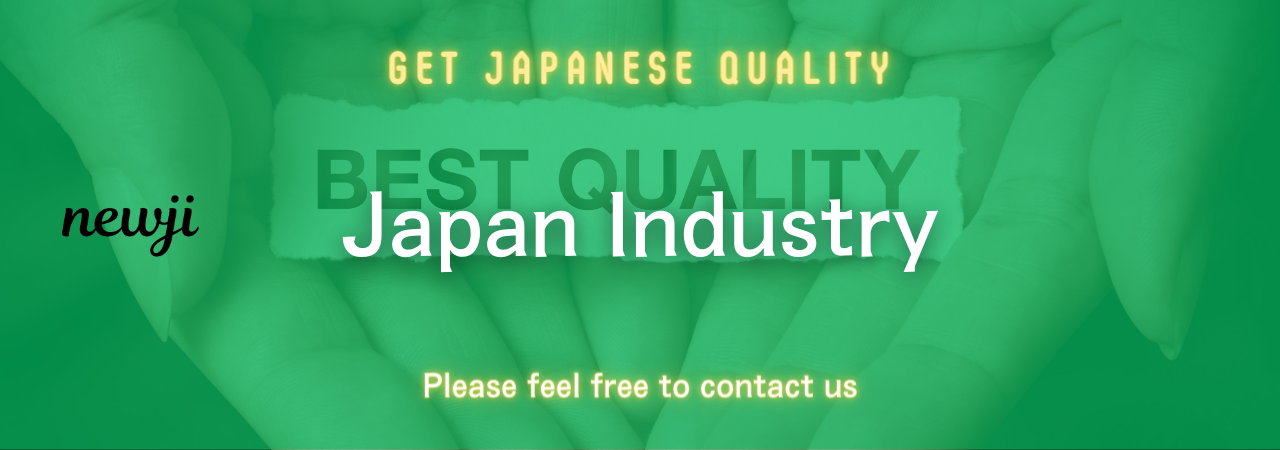
FMEA, or Failure Mode and Effects Analysis, is a critical method used in various industries to anticipate and address potential problems before they occur.
By systematically examining possible failure modes, FMEA helps organizations identify and prioritize risks, thereby enhancing the safety, reliability, and performance of products and processes.
目次
Understanding the Basics of FMEA
FMEA is a structured approach used to analyze potential failures and their effects.
It helps in determining the severity of consequences, the likelihood of occurrence, and the ability to detect failures in time.
By doing so, companies can develop action plans to reduce or eliminate risks.
There are two main types of FMEA: Design FMEA (DFMEA) and Process FMEA (PFMEA).
DFMEA focuses on potential failures in product design, while PFMEA examines possible failures in manufacturing and production processes.
Both types aim to ensure that products meet quality standards and function as intended.
The Importance of FMEA in Industries
FMEA is invaluable for industries such as automotive, aerospace, healthcare, and manufacturing, where the reliability and safety of products are paramount.
By proactively identifying potential problems and developing strategies to mitigate them, organizations can save significant time and resources.
This not only helps in avoiding product recalls and warranty claims but also improves customer satisfaction and brand reputation.
Steps in Conducting an Effective FMEA
Conducting an FMEA involves a step-by-step process to systematically analyze potential failure modes.
Here’s a closer look at the key steps involved:
Step 1: Assemble a Team
Form a cross-functional team that includes individuals with diverse expertise related to the product or process.
This ensures a comprehensive understanding of potential risks and helps in generating effective solutions.
Step 2: Define the Scope
Clearly define the scope of the FMEA by identifying the process, product, or system to be analyzed.
Understanding the scope helps in maintaining focus and avoids unnecessary complexity.
Step 3: Identify Potential Failure Modes
Examine each component or step in the process to identify possible failure modes.
Consider what could go wrong at each stage and list all potential failures.
Step 4: Analyze Effects and Causes
For each identified failure mode, assess its potential effects on the system, end-users, or stakeholders.
Determine the potential causes of each failure mode and analyze how it might occur.
Step 5: Assign Severity, Occurrence, and Detection Ratings
Each failure mode is rated based on three factors: severity (impact of the failure), occurrence (likelihood of the failure happening), and detection (ability to detect the failure before it occurs).
These ratings help in prioritizing risks.
Step 6: Calculate Risk Priority Number (RPN)
Multiply the severity, occurrence, and detection ratings to calculate the Risk Priority Number (RPN) for each failure mode.
The RPN helps prioritize which risks require immediate attention.
Step 7: Develop and Implement Actions
For failure modes with high RPNs, develop and implement action plans to reduce or eliminate risks.
These actions may involve design changes, process modifications, or enhanced testing.
Step 8: Review and Monitor
Regularly review the FMEA to ensure its effectiveness and update it as necessary.
Monitoring helps in adapting to changes and new information that may impact the risk assessment.
Practical Tips for Effective FMEA
While following the structured process of FMEA, there are several practical points to keep in mind:
Involve the Right People
Ensure that your FMEA team includes individuals with relevant expertise and experience.
Their diverse perspectives will enhance the thoroughness and accuracy of the analysis.
Be Thorough Yet Focused
While it’s important to be thorough, avoid analyzing every detail unnecessarily.
Focus on critical components and processes that have the most significant impact on performance and safety.
Use Data Effectively
Leverage historical data, testing results, and previous FMEAs to inform your analysis.
This data can provide valuable insights into potential risks and effective mitigation strategies.
Communicate Clearly
Ensuring clear communication throughout the process is crucial.
Document findings effectively and share them with relevant stakeholders to facilitate informed decision-making.
Continuous Improvement
FMEA should be an ongoing process rather than a one-time activity.
Regularly assess and update your analysis to accommodate changes in technology, regulations, and market conditions.
The Benefits of Implementing FMEA
Implementing FMEA provides numerous benefits, making it an essential tool for organizations:
Improved Product Reliability
By identifying and addressing potential problems early, FMEA enhances the reliability and performance of products, reducing the likelihood of failures.
Reduced Costs
Proactively addressing risks helps organizations avoid expensive recalls, rework, and warranty claims, ultimately saving costs.
Customer Satisfaction
Delivering high-quality, reliable products improves customer satisfaction and strengthens brand loyalty.
Enhanced Safety
FMEA contributes to enhanced safety by identifying and mitigating risks associated with product or process failures.
Conclusion
Failure Mode and Effects Analysis (FMEA) is a powerful tool for identifying and addressing potential risks in products and processes.
By following a structured approach and implementing practical strategies, organizations can enhance product quality, safety, and reliability while reducing costs and ensuring customer satisfaction.
Incorporating FMEA into your quality management practices is a proactive step that fosters continuous improvement and long-term success.
資料ダウンロード
QCD調達購買管理クラウド「newji」は、調達購買部門で必要なQCD管理全てを備えた、現場特化型兼クラウド型の今世紀最高の購買管理システムとなります。
ユーザー登録
調達購買業務の効率化だけでなく、システムを導入することで、コスト削減や製品・資材のステータス可視化のほか、属人化していた購買情報の共有化による内部不正防止や統制にも役立ちます。
NEWJI DX
製造業に特化したデジタルトランスフォーメーション(DX)の実現を目指す請負開発型のコンサルティングサービスです。AI、iPaaS、および先端の技術を駆使して、製造プロセスの効率化、業務効率化、チームワーク強化、コスト削減、品質向上を実現します。このサービスは、製造業の課題を深く理解し、それに対する最適なデジタルソリューションを提供することで、企業が持続的な成長とイノベーションを達成できるようサポートします。
オンライン講座
製造業、主に購買・調達部門にお勤めの方々に向けた情報を配信しております。
新任の方やベテランの方、管理職を対象とした幅広いコンテンツをご用意しております。
お問い合わせ
コストダウンが利益に直結する術だと理解していても、なかなか前に進めることができない状況。そんな時は、newjiのコストダウン自動化機能で大きく利益貢献しよう!
(Β版非公開)