- お役立ち記事
- Foam basics/generation mechanism and defoaming/defoaming technology
月間77,185名の
製造業ご担当者様が閲覧しています*
*2025年2月28日現在のGoogle Analyticsのデータより
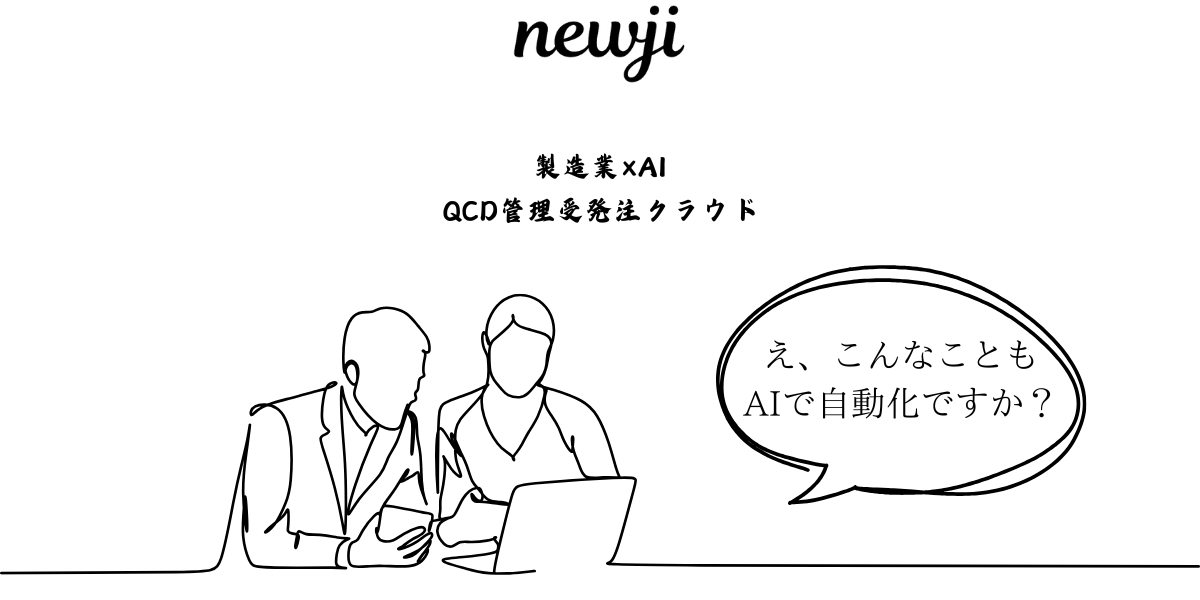
Foam basics/generation mechanism and defoaming/defoaming technology
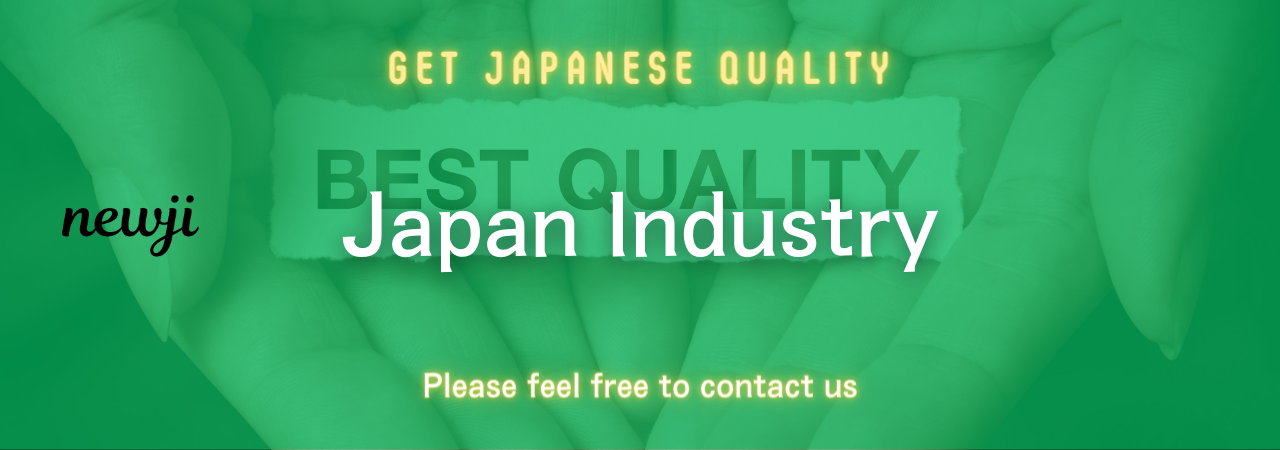
Foam is a common occurrence in many industrial processes, household activities, and natural phenomena.
This article delves into the basics of foam, the mechanism by which it is generated, and the technology used in defoaming and foam prevention.
目次
Understanding Foam
Foam is a type of colloidal system that consists of gas bubbles dispersed in a liquid or solid matrix.
It is characterized by a bubbly appearance and can vary in terms of stability and density depending on its composition and environmental conditions.
Foam formation typically occurs when air or another gas is mixed into a liquid, creating bubbles that are stabilized by surfactants, which are surface-active agents.
Surfactants reduce the surface tension between liquid and gas, allowing bubbles to remain intact for a longer period.
This process is vital in creating a stable foam structure.
Foam Generation Mechanism
Foam generation involves three main steps: bubble formation, bubble stabilization, and bubble coalescence.
Understanding these steps provides insight into controlling foam formation across various applications.
Bubble Formation
Bubbles form when a gas is introduced into a liquid.
This can occur through mechanical agitation, chemical reactions, or by varying the pressure and temperature conditions within the liquid.
At this stage, the number and size of bubbles depend on the amount of gas present and the intensity of agitation applied.
Bubble Stabilization
Once bubbles are formed, their stability depends on the presence of surfactants.
Surfactants accumulate at the gas-liquid interface, reducing surface tension and preventing bubbles from bursting.
These molecules have hydrophilic (water-attracting) and hydrophobic (water-repelling) ends that create a stable film around the bubble, allowing it to persist over time.
Bubble Coalescence
Bubble coalescence refers to the merging of smaller bubbles into larger ones, which eventually leads to the breakdown of the foam structure.
The rate of coalescence is affected by factors such as the concentration of surfactants, viscosity of the liquid, and external forces applied to the system.
Reducing coalescence rate is critical in maintaining foam stability.
Defoaming Technology
Defoaming, or antifoaming, technology is used to control unwanted foam in industrial processes, enhancing efficiency and product quality.
Defoamers are chemical additives used to eliminate or suppress foam.
There are several approaches to defoaming, each targeting different aspects of foam formation.
Chemical Defoamers
Chemical defoamers work by altering the physical properties of foam to encourage bubble rupture.
They often contain oils, hydrophobic particles, or surfactants that destabilize the foam structure.
Common types include silicone-based defoamers, which are versatile across various applications, and mineral oil-based defoamers, often used in food processing and fermentation industries.
Mechanical Defoamers
Mechanical defoamers are devices or systems that physically break down foam.
These include vacuum systems, centrifuges, and air compressors that reduce foam by altering pressure and temperature conditions.
Mechanical methods are often employed in large-scale operations where chemical additives may not be appropriate.
Biological Defoamers
Biological defoamers utilize enzymes or microorganisms that naturally break down foam-producing agents.
They are environmentally friendly and ideal for applications that require minimal chemical interference, such as wastewater treatment or food production.
Applications of Foam and Defoaming Technology
Foam has advantageous uses, yet understanding its control is critical across diverse industries.
Food and Beverage
In the food and beverage industry, foam is used in products like beer, carbonated drinks, and whipped cream to improve texture and appearance.
However, excessive foam can disrupt production processes or alter product quality, making defoaming technology essential.
Pharmaceuticals
In pharmaceutical manufacturing, foaming can interfere with batch consistency, leading to inefficiencies.
Defoamers ensure consistent product quality and effective manufacturing processes.
Paints and Coatings
Foam control in paints and coatings is vital to prevent defects in the final product, such as reduced gloss and uneven application.
Defoamers are key in maintaining the desired aesthetic and functional properties of coatings.
Conclusion
Foam plays a significant role in various natural and industrial processes.
Understanding the fundamentals of foam formation and employing effective defoaming technologies can optimize the efficiency and quality of numerous products and applications.
As technology advances, new methods of foam control continue to arise, offering innovative solutions to manage foam across a broad spectrum of fields.
資料ダウンロード
QCD管理受発注クラウド「newji」は、受発注部門で必要なQCD管理全てを備えた、現場特化型兼クラウド型の今世紀最高の受発注管理システムとなります。
ユーザー登録
受発注業務の効率化だけでなく、システムを導入することで、コスト削減や製品・資材のステータス可視化のほか、属人化していた受発注情報の共有化による内部不正防止や統制にも役立ちます。
NEWJI DX
製造業に特化したデジタルトランスフォーメーション(DX)の実現を目指す請負開発型のコンサルティングサービスです。AI、iPaaS、および先端の技術を駆使して、製造プロセスの効率化、業務効率化、チームワーク強化、コスト削減、品質向上を実現します。このサービスは、製造業の課題を深く理解し、それに対する最適なデジタルソリューションを提供することで、企業が持続的な成長とイノベーションを達成できるようサポートします。
製造業ニュース解説
製造業、主に購買・調達部門にお勤めの方々に向けた情報を配信しております。
新任の方やベテランの方、管理職を対象とした幅広いコンテンツをご用意しております。
お問い合わせ
コストダウンが利益に直結する術だと理解していても、なかなか前に進めることができない状況。そんな時は、newjiのコストダウン自動化機能で大きく利益貢献しよう!
(β版非公開)