- お役立ち記事
- Foldable Compact Bed Manufacturing Process and Durability Strengthening
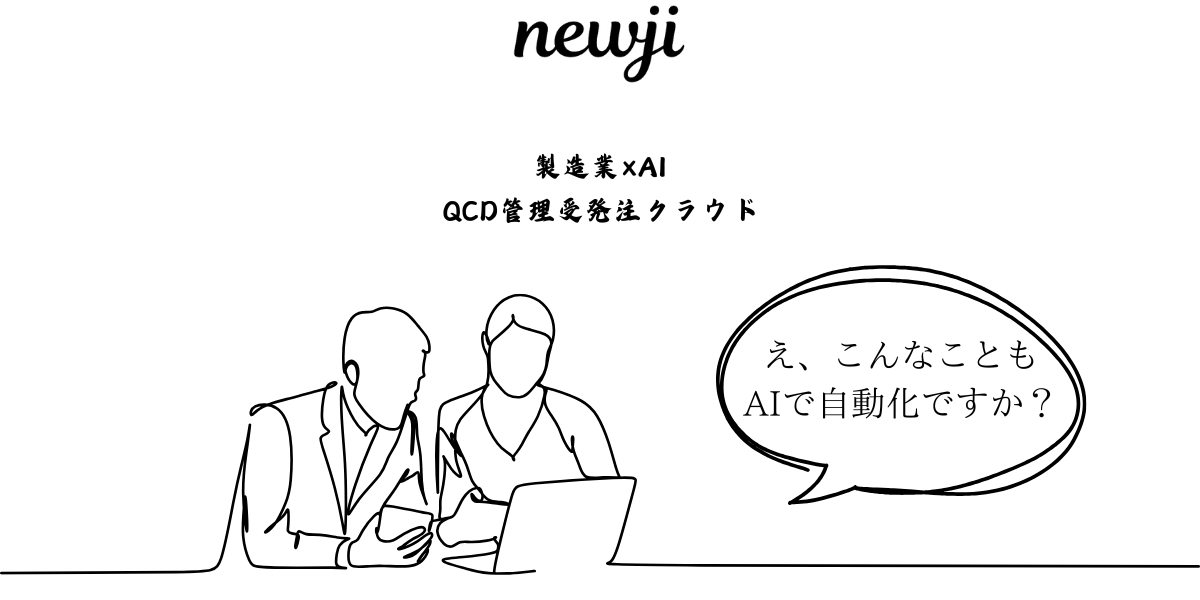
Foldable Compact Bed Manufacturing Process and Durability Strengthening
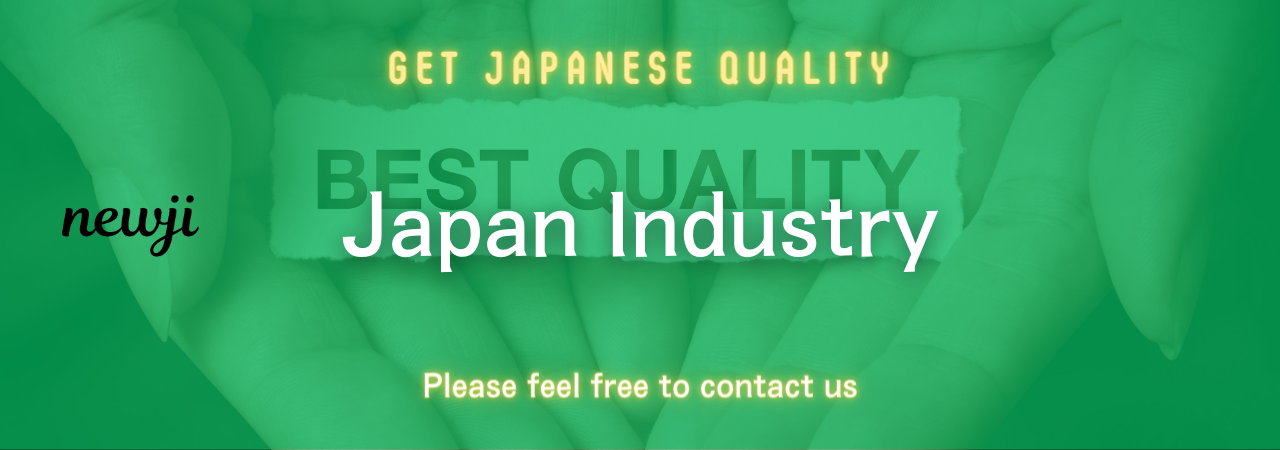
目次
Understanding the Manufacturing Process of Foldable Compact Beds
Foldable compact beds are a fantastic solution for those who need space-saving furniture options in their homes or when traveling.
To better appreciate these incredible products, let’s walk through the detailed manufacturing process that ensures their practicality and reliability.
Material Selection
The manufacturing journey starts with selecting the right materials.
The materials chosen for foldable compact beds must be both lightweight and durable to support weight and frequent folding.
High-quality metals, such as aluminum or steel, are commonly used for the frame due to their strength and ability to endure repeated use.
For the bed’s surface, manufacturers often opt for robust fabrics or sturdy wood slats.
These materials need to support the weight comfortably while providing adequate comfort for the user.
Design and Engineering
Once the materials are selected, the next phase is design and engineering.
This stage involves creating a blueprint that maximizes space efficiency without sacrificing user comfort.
Engineers work to balance the ease of folding mechanisms with structural integrity, ensuring that the bed not only folds easily but remains stable when in use.
Computer-aided design (CAD) software is frequently used to create detailed 3D models of the bed.
These models help in visualizing the final product, making any necessary adjustments before moving on to the next stage.
Prototyping and Testing
Prototyping is an essential step in the manufacturing process.
It involves creating a functional model of the foldable bed to test its design and functionality.
This prototype undergoes rigorous testing to identify any weaknesses or potential points of failure.
Testing involves simulating repeated folding and unfolding to assess the longevity and durability of the bed.
It also includes weight testing to ensure it can handle the intended load.
Manufacturers may conduct these tests in controlled environments and simulate extended use to predict product lifespan.
Based on the test results, the design is often tweaked to address any issues discovered, ensuring that the final product meets quality standards.
Production and Assembly
Once the design is finalized, production begins.
The first step in production is cutting and shaping the materials according to the design specifications.
Advanced machinery and precision tools are used to ensure each component is made to exact measurements.
Next, these components are assembled to form the frame and structure of the bed.
The assembly process must maintain high standards to ensure the bed’s stability and functionality.
Special attention is paid to the folding mechanism, where hinges and joints are carefully installed to facilitate easy operation.
Strengthening Durability in Foldable Compact Beds
Ensuring durability is a critical goal in the manufacturing of foldable compact beds.
Given their frequent use and the stress put on joints and materials, manufacturers employ several strategies to enhance durability.
Quality Control
Quality control is an integral part of the manufacturing process.
It involves thorough inspections at every stage, from material selection to the final assembly.
Inspectors look for defects or inconsistencies that could compromise the bed’s performance.
Advanced quality control technologies, such as 3D scanning and automated testing equipment, ensure all specifications are met.
This stage is crucial in catching issues early before large-scale production begins.
Advanced Folding Mechanisms
Innovative folding mechanisms are a key focus area to improve durability.
Manufacturers use high-grade hinges and joints that are designed to withstand constant motion without wear and tear.
Often, these components are made from corrosion-resistant materials to prolong their lifespan.
Additionally, incorporating locking systems that secure the bed when opened or closed adds another layer of safety and durability.
Finishing Touches and Protective Coatings
To extend the life of foldable compact beds, manufacturers apply protective coatings.
These coatings help resist scratches, moisture, and other environmental factors that could degrade materials over time.
For metal frames, powder coating or anodizing could be used to prevent rust and corrosion.
For wooden parts or fabric surfaces, special sealants or treatments enhance durability and appearance.
User Education and Maintenance
Durability also depends on how well users maintain their foldable beds.
Manufacturers often include guidelines for proper use and maintenance to ensure longevity.
Instructions may advise on correct folding techniques, weight limits, and cleaning procedures.
By educating users on these aspects, the beds can remain in optimal condition for extended periods.
Conclusion
The manufacturing of foldable compact beds is a complex process that requires careful consideration of materials, design, and engineering.
Through rigorous testing and quality control, manufacturers ensure these beds are not only functional but highly durable.
By focusing on innovative design strategies and educating users, foldable compact beds continue to be an excellent solution for anyone seeking space-saving furniture without compromising on strength and reliability.
資料ダウンロード
QCD調達購買管理クラウド「newji」は、調達購買部門で必要なQCD管理全てを備えた、現場特化型兼クラウド型の今世紀最高の購買管理システムとなります。
ユーザー登録
調達購買業務の効率化だけでなく、システムを導入することで、コスト削減や製品・資材のステータス可視化のほか、属人化していた購買情報の共有化による内部不正防止や統制にも役立ちます。
NEWJI DX
製造業に特化したデジタルトランスフォーメーション(DX)の実現を目指す請負開発型のコンサルティングサービスです。AI、iPaaS、および先端の技術を駆使して、製造プロセスの効率化、業務効率化、チームワーク強化、コスト削減、品質向上を実現します。このサービスは、製造業の課題を深く理解し、それに対する最適なデジタルソリューションを提供することで、企業が持続的な成長とイノベーションを達成できるようサポートします。
オンライン講座
製造業、主に購買・調達部門にお勤めの方々に向けた情報を配信しております。
新任の方やベテランの方、管理職を対象とした幅広いコンテンツをご用意しております。
お問い合わせ
コストダウンが利益に直結する術だと理解していても、なかなか前に進めることができない状況。そんな時は、newjiのコストダウン自動化機能で大きく利益貢献しよう!
(Β版非公開)